Timothy Sullivan
Disabled Veterans Outreach Program (DVOP) Specialists at American Job Center- Claim this Profile
Click to upgrade to our gold package
for the full feature experience.
-
English Native or bilingual proficiency
Topline Score
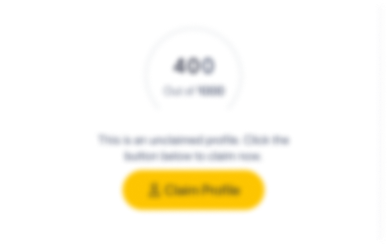
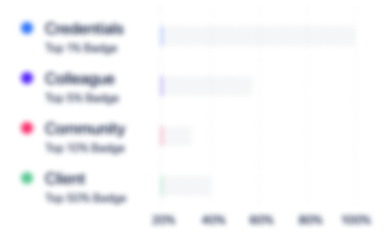
Bio
0
/5.0 / Based on 0 ratingsFilter reviews by:
Experience
-
American Job Center
-
Government Administration
-
1 - 100 Employee
-
Disabled Veterans Outreach Program (DVOP) Specialists
-
Jun 2023 - Present
The Disabled Veterans Outreach Program (DVOP) Specialist works directly with veterans and other eligible persons by providing individualized career services to help them reach their employment goals. Provide services which include, but are not limited to, comprehensive assessment interviews, career guidance, individual employment plans, labor market information, and staff-assisted job search activities. Develop, coordinate, and/or facilitate workshops and presentations to applicants on job readiness or the most current job search techniques, as well as demonstrates the use of job listings to assist clients with exploring available training and employment opportunities. Identify and evaluate barriers, exploring solutions to assist in removing such barriers, while facilitating and referring customers to appropriate supportive services to promote self-sufficiency and employment. Perform job counseling with applicants to identify their abilities, needs, interests, and values in relation to job opportunities and career goals by utilizing a variety of assessments and evaluation tools. Render career development and assessment services to clients for the purpose of matching their application skill sets to vacancies, in order to job match or provide job referrals. Conduct outreach with local veteran and community-based organizations, and educational institutions to ensure maximum assistance is available to veterans served; which will also require travel to remote locations to provide direct assistance to veteran customers. Responsible for consulting and coordinating with various representatives from federal, state, and local programs and employers to promote the development of entry-level and career job opportunities, job training, apprenticeships, and vocational counseling services for veterans Show less
-
-
-
Denso Manufacturing Athens Tennessee, Inc.
-
United States
-
Automotive
-
1 - 100 Employee
-
Senior Maintenance Technician
-
Jul 2017 - Feb 2023
Production Maintenance Multi-skilled professionals who troubleshoot and repair complex industrial machines. Repair both electrical and mechanical systems including robotics, testers, hydraulics, and pneumatics on highly automated production equipment. Troubleshoot and program PLC’s and robots. Extensive Electronics and PLC troubleshooting / programming as well as mechanical overhaul and adjustment of machinery. Daily and preventative maintenance on automated equipment. Knowledgeable in control wiring, strong computer skills and project management skills. Show less
-
-
-
The Woodbridge Group
-
United States
-
Hospitals and Health Care
-
Maintenance Technician
-
Oct 2016 - Jul 2017
This position is 50% mechanical work and 50% electrical work. Repairs machines or equipment, dismantling as necessary to gain access to defective parts. making the necessary adjustments to ensure efficient or proper operation. Operate and repair plant support machinery, boilers, softener, compressors etc. Handle major repairs and liaison with contractors as required. Develop and implement preventative/ predictive maintenance on all machinery and equipment. General industrial maintenance duties. All other related duties as assigned. Show less
-
-
-
SugarCreek
-
United States
-
Food and Beverage Manufacturing
-
300 - 400 Employee
-
Maintenance Technician
-
Apr 2015 - Oct 2016
DESCRIPTION SUMMARY Perform routine maintenance and repairs as needed to keep machines and mechanical equipment operating efficiently and in a safe manner. Coordinate with Plant Management to establish maintenance schedules on various machines so as to minimize downtime on production. PRINCIPAL DUTIES AND RESPONSIBILITIES • Review and complete work orders timely, conducting necessary maintenance or repairs as needed. • Follow Lockout/Tagout procedures at all times and ensure all Maintenance Personnel are following Lockout/Tagout procedures at all times. •Inspect, operate or test machinery or equipment to diagnose machine malfunctions. • Dismantle machines, equipment or devices to access and remove defective parts, using hoists, cranes, hand tools or power tools. • Perform routine maintenance, such as inspecting drives, motors or belts, checking fluid levels, replacing filters or doing other preventive maintenance actions. • Diagnose mechanical problems and determine how to correct them, checking blueprints, repair manuals or parts catalogs as necessary. •Repair machines, equipment or structures, using tools such as hammers, hoists, saws, drills, wrenches or equipment such as precision measuring instruments or electronic testing devices. • Maintain constant communication with Plant Management regarding any maintenance issues that may arise. • Complete daily reports outlining maintenance or repairs conducted over the course of the shift. • Complete setup and teardown of machines and equipment at beginning and end of shifts. •Comply with federal, state, and company policies, procedures and regulations. • Support all safety, food quality and sanitation initiatives and policies. • Follow safety rules and procedures. • Perform other duties and tasks as assigned. Show less
-
-
-
Cardinal Health
-
United States
-
Hospitals and Health Care
-
700 & Above Employee
-
Maintenance Technician
-
Apr 2010 - Feb 2015
Training and experience in multiple PME’s (forklift, reach truck, boom(bucket) lifts, etc.), hand and large powered tool usage, meters and electrical test equipment, use and red-lining blueprints, fall equipment and restraints, electrical hazards, dock safety and maintenance, extreme cold environments, environmental hazards. Servicing high voltage electrical supply and monitoring equipment and facility wiring, including VFD power supplies, cabling, high voltage chargers & battery maintenance. Troubleshooting ladder and control logic PLC’s and reprogramming process controllers or replacing faulty modules and system boards. Performing Maintenance and Monitoring with varied metering equipment on electric conveyor systems. Replacing industrial motors, belts, speed controls, conveyor runs, chain controls, braking, diverting and merging systems, scanners and monitors and dock levelers. Recalibrating automation sensors and controllers to ensure safe, routine operation of Input / Output devices. Installing, inspecting, maintaining critical plumbed fluid (hydraulic, water), electrical and pneumatics in safety and operational systems in accordance with applicable Fire codes and Building Blueprints. Responsible for OHSA compliance while performing inspections and maintenance in hot, cold and mechanized environments. Primarily supervisory and independent duty to maintain facility operation on nights and weekends. Show less
-
-
-
Pole Position Raceway
-
United States
-
Entertainment Providers
-
1 - 100 Employee
-
Site Operations Manager
-
Oct 2007 - Apr 2010
Provided Customer Service and Supervised personnel, motorized operations, safety and security, and accident response for customer ranging from 6yr and up. Trained employees in daily operation, data entry / recall for immediate operational management, recall archived information, company polices, and customer relations. Managed consumables / merchandising and equipment / parts / inventories, manpower usage and facility utilizations. Provided Customer Service and Supervised personnel, motorized operations, safety and security, and accident response for customer ranging from 6yr and up. Trained employees in daily operation, data entry / recall for immediate operational management, recall archived information, company polices, and customer relations. Managed consumables / merchandising and equipment / parts / inventories, manpower usage and facility utilizations.
-
-
-
-
Hazardous Material Technician
-
Sep 2007 - Jun 2009
Ensured compliance with all federal, state and local laws and regulations, including multi-level EPA reporting. Performed inspections of materials packaging, transport and storage facilities. Packaged hazardous chemical, radiological, and biological waste for disposal at external facility. Ensured compliance with all federal, state and local laws and regulations, including multi-level EPA reporting. Performed inspections of materials packaging, transport and storage facilities. Packaged hazardous chemical, radiological, and biological waste for disposal at external facility.
-
-
-
United States Air Force
-
United States
-
Defense and Space Manufacturing
-
700 & Above Employee
-
Aircraft Armement System Technician
-
Nov 2001 - Aug 2007
USAF 7-level maintenance qualification to load and maintain weapon systems on all USAF aerial delivery platforms, including supporting electronic circuits and arming mechanisms. Assigned responsibility for personal and crew understanding and compliance with applicable DOD regulations, including local facility and command policies as well as USAF general regulations. Detailed training in assembling and maintaining complex electrical and mechanical equipment and accessories, including troubleshooting, use of schematics, blueprints and test equipment, wire repair and maintenance documentation. Maintained network-based time- and mission-critical data, secure classified information and reported schedule to management. Trained in and responsible for USAF IMDS. Completed certification courses in Microsoft Office, Windows and Local Area Networks. Operated light and heavy fork and scissor lifts, heavy trucks, 15-60 passenger buses, hydraulic and electrical support equipment, towed vehicles carrying conventional and highly sensitive materials. Held responsibility for equipment, operations, safety (operations, HAZMAT) and 50 department personnel. Trained and supervised troops to support operational flight and payload delivery requirements in critical strategic wartime assignments. Performed written staff evaluations and verbal management of personnel. Supervised and performed weapons loading on operational strike aircraft during prolonged operations. Trained, participated in, supervised aircraft and aircraft environment safety, including FOD detection, damage and hangar/ramp/runway hazard inspections, safety reporting procedures, and flight safety requirements. Extended deployments to CONUS / theater facilities in support of operation under adverse conditions. Demonstrated ability to adapt plans to changing conditions and requirements on a day-to-day basis and the ability to accomplish extended operational tasks regardless of hours and level of effort required. Show less
-
-
Education
-
Norco College
Associate of Science (A.S.), Industrial Electronics Technology/Technician -
Community College of the Air Force
Associate of Science (AS), Aircraft Armament Systems Technology -
Community College of the Air Force
Associate's degree, Aircraft Armament Systems Technology
Community
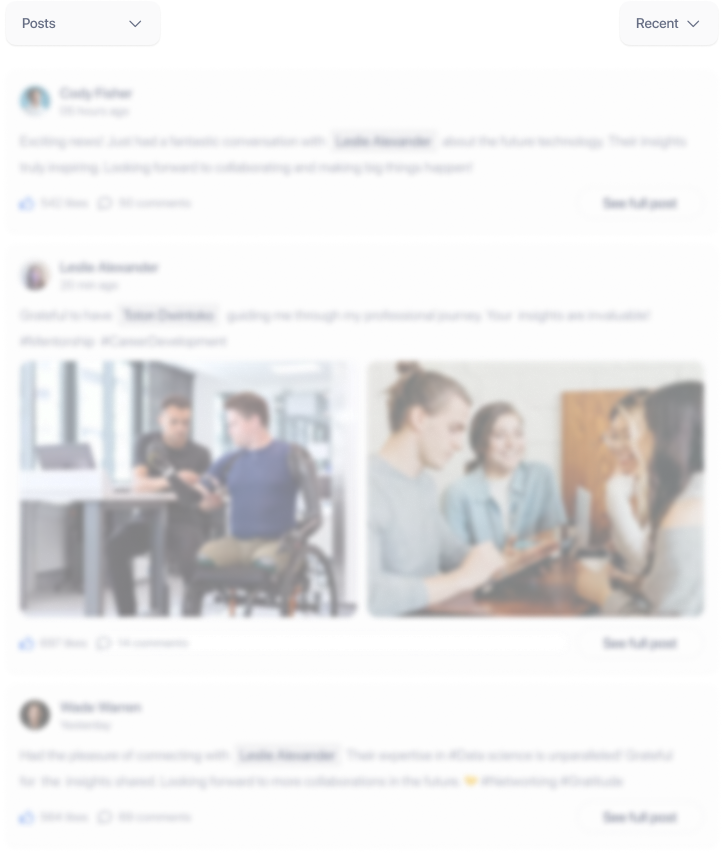