Timothy House
Director of Operations at Cornwell Quality Tools- Claim this Profile
Click to upgrade to our gold package
for the full feature experience.
Topline Score
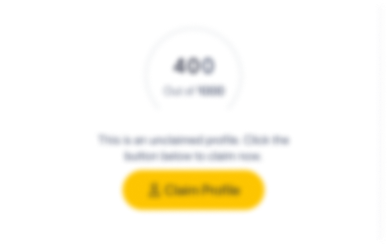
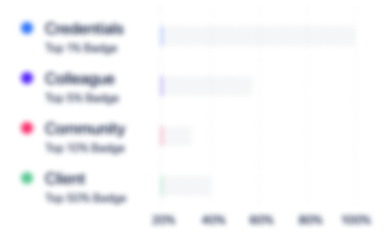
Bio


Credentials
-
Leadership Developement Program
Center for Creative LeadershipNov, 2016- Nov, 2024
Experience
-
Cornwell Quality Tools
-
United States
-
Motor Vehicle Manufacturing
-
100 - 200 Employee
-
Director of Operations
-
Oct 2020 - Present
• Responsibility of all operations at three production plants and warehouses. • Manage the purchasing plans necessary to maintain production schedules and stock levels. • Responsible for on time delivery, inventory turns, and inventory accuracy of each site. • Manage and promote quality and continuous improvement of all plant operations. • Manage capital expenditures and related projects, • Responsible for the hiring, training, and safety of staff in multiple locations. • Manage new product development and act as liaison between marketing and operations. • Responsible for engineering, quality, and customer interactions related to manufactured product. Show less
-
-
-
Columbus McKinnon
-
United States
-
Machinery Manufacturing
-
700 & Above Employee
-
Materials and Production Manager
-
Apr 2014 - Present
• Manage the daily operations; including scheduling, procurement, manufacturing, warehousing, and shipping. • Responsible for the two plants performance of on time delivery, inventory turns, inventory accuracy, shipments, customer satisfaction, and financials. • Responsible for continuous improvement and plant lean initiatives. • Experienced, trained, and practice Lean Manufacturing and the Toyota KATA processes. • Responsibility for the environmental and safety performance of the two plants and employees. • Manage the budgets of direct and indirect departments and the operating income of the two plants. • Oversee 15 salary and 104 hourly employees - United Steel Workers. • Responsible for the hiring, training, and continuous education of staff. Show less
-
-
-
Helios C
-
Canton, Ohio Area
-
Operations Manager
-
Jun 2009 - Apr 2014
• Manage the daily operations of a TS16949 Tier 1 Automotive wheel coatings business. • Responsible for the company’s profits and costs to supply Ford, Chrysler, and GM with $120,000 worth of product daily. • Responsible for continuous improvement and plant lean initiatives. • Control inventories for multiple wheel types including forged wheels and process materials used in daily production. • Oversee 41 staff members including production managers, shipping / receiving managers, lab technicians, maintenance manager, and warehouse manager. • Facilitate staffing and training of new employees. Show less
-
-
-
The Timken Company
-
United States
-
Industrial Machinery Manufacturing
-
700 & Above Employee
-
Senior Supply Chain Systems Analyst
-
Jul 2005 - May 2009
•Project Manager responsible for cost, schedules, and design of, Supply Chain and Production Management modules within Timken’s SAP Operating System. •Sarbanes-Oxley Specialist for the Supply Chain and Inventory Control portions of Timken’s SOX Compliance Guidelines. Responsible for control and documentation integrity, system testing, and user system security access. •Design Supply Chain Operating ERP System to fit the needs of a constantly changing business. •Develop purchasing and stocking strategies to minimize working capital expense and maximize cash flow. •Analyze the Supply Chain to continuously improve the product flow from raw to the customer. •Create reports that are used to effectively operate the daily supply chain. Show less
-
-
-
State Industrial Products
-
United States
-
Chemical Manufacturing
-
400 - 500 Employee
-
Operations Materials Manager
-
Nov 2000 - Jun 2005
•Manage three department managers, and oversee the operations of purchasing, inventory planning, the distribution center operations, the quotations, and sourcing department. •Implemented a lean manufacturing environment reducing backlog and warehouse operation costs. •Effectively re-structured a quotation department of five individuals servicing 140 outside sales representatives. •Reduced customer order backlog by 58% through forecasting, inventory planning and effective purchasing tactics. •Managed a department of five individuals. A team of purchasing specialist, distribution center planners and production planners, which produce daily production plans, focusing on customer requirements and forecasted inventory levels. •Created and managed sales forecast, demand planning, and associated materials for production/inventory. •Managed and maintained the inventory for seven different distribution centers across North America. •Increased customer order fill rates from 78% to 96% while reducing total inventory value by 28%. •Re-designed the layout of and data for, manufacturing and planning in SAP at State Industrial Products. Show less
-
-
-
KYOCERA SGS Precision Tools
-
United States
-
Industrial Machinery Manufacturing
-
100 - 200 Employee
-
Master Production Scheduler
-
Jun 1987 - Oct 2000
•Scoped, designed, developed, and set up PeopleSoft manufacturing software for SGS Tool Company. •Managed a team of four production schedulers, each being responsible for different product lines produced in different locations. •Managed and maintained Demand Solutions Forecasting and Distribution Requirements Plan for over 20,000 items. •Produced and maintained economic production lot sizes and inventory stocking levels for four different product lines. •Managed raw material, work in process and finished goods inventories for a product line of over 8,000 items. •Created and maintained quotes, prints, and drawings for non-standard products. •Used MRP/MPS to create finished goods plan and order raw material. •Acted as liaison between customer service representatives and manufacturing, expediting product through shop floor as well as providing delivery dates. •Journeyman Machinist - Tool Maker. Show less
-
-
Community
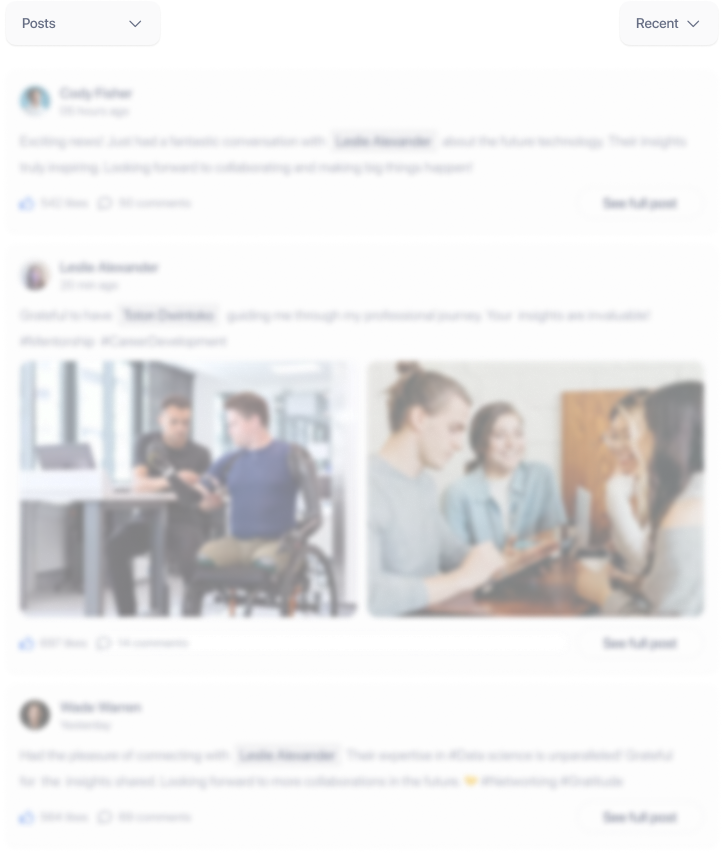