Timothy Bassett, CRL, LSSGB
Vice President - Converting Operations at Marcal Manufacturing, LLC- Claim this Profile
Click to upgrade to our gold package
for the full feature experience.
Topline Score
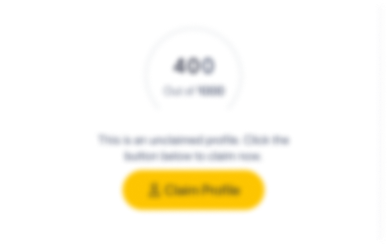
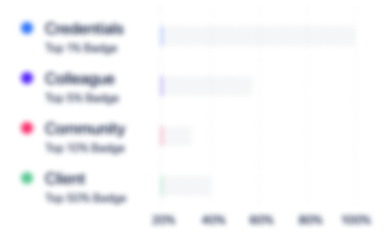
Bio

John DeCorte
Tim and I worked together for many years at the Kimberly-Clark tissue manufacturing facility in New Milford, CT. What stood out about Tim immediately was his intelligence, paired with a fierce ambition and a sense of purpose. It was no question Tim had all of the makings of a highly-capable business leader, and his hard-fought and well-earned ascension through the ranks at KC, and beyond, is a testament to that. Tim has made a career of transcending barriers, and his skill as a leader was earned through the experience he has collected working (and succeeding) in many different roles, from the factory floor on up to running entire departments. Of one thing I am certain, Tim’s potential is limitless. He is a uniquely valuable asset; a true competitive advantage within any organization.

David Frye, CMRP, CRL
Tim has been a real asset to the effort of implementing TPM and OPEX. Tools and processes he created for use in his facility have been adopted and adapted for use across the corporation. He is always looking for new challenges and has proven to be up to all he has found. Tim is a great team player, comfortable interfacing at all levels, and would be an asset to any organization.

John DeCorte
Tim and I worked together for many years at the Kimberly-Clark tissue manufacturing facility in New Milford, CT. What stood out about Tim immediately was his intelligence, paired with a fierce ambition and a sense of purpose. It was no question Tim had all of the makings of a highly-capable business leader, and his hard-fought and well-earned ascension through the ranks at KC, and beyond, is a testament to that. Tim has made a career of transcending barriers, and his skill as a leader was earned through the experience he has collected working (and succeeding) in many different roles, from the factory floor on up to running entire departments. Of one thing I am certain, Tim’s potential is limitless. He is a uniquely valuable asset; a true competitive advantage within any organization.

David Frye, CMRP, CRL
Tim has been a real asset to the effort of implementing TPM and OPEX. Tools and processes he created for use in his facility have been adopted and adapted for use across the corporation. He is always looking for new challenges and has proven to be up to all he has found. Tim is a great team player, comfortable interfacing at all levels, and would be an asset to any organization.

John DeCorte
Tim and I worked together for many years at the Kimberly-Clark tissue manufacturing facility in New Milford, CT. What stood out about Tim immediately was his intelligence, paired with a fierce ambition and a sense of purpose. It was no question Tim had all of the makings of a highly-capable business leader, and his hard-fought and well-earned ascension through the ranks at KC, and beyond, is a testament to that. Tim has made a career of transcending barriers, and his skill as a leader was earned through the experience he has collected working (and succeeding) in many different roles, from the factory floor on up to running entire departments. Of one thing I am certain, Tim’s potential is limitless. He is a uniquely valuable asset; a true competitive advantage within any organization.

David Frye, CMRP, CRL
Tim has been a real asset to the effort of implementing TPM and OPEX. Tools and processes he created for use in his facility have been adopted and adapted for use across the corporation. He is always looking for new challenges and has proven to be up to all he has found. Tim is a great team player, comfortable interfacing at all levels, and would be an asset to any organization.

John DeCorte
Tim and I worked together for many years at the Kimberly-Clark tissue manufacturing facility in New Milford, CT. What stood out about Tim immediately was his intelligence, paired with a fierce ambition and a sense of purpose. It was no question Tim had all of the makings of a highly-capable business leader, and his hard-fought and well-earned ascension through the ranks at KC, and beyond, is a testament to that. Tim has made a career of transcending barriers, and his skill as a leader was earned through the experience he has collected working (and succeeding) in many different roles, from the factory floor on up to running entire departments. Of one thing I am certain, Tim’s potential is limitless. He is a uniquely valuable asset; a true competitive advantage within any organization.

David Frye, CMRP, CRL
Tim has been a real asset to the effort of implementing TPM and OPEX. Tools and processes he created for use in his facility have been adopted and adapted for use across the corporation. He is always looking for new challenges and has proven to be up to all he has found. Tim is a great team player, comfortable interfacing at all levels, and would be an asset to any organization.

Credentials
-
Atlas Leadership Academy - Class of 2022
Atlas Holdings LLCJan, 2023- Nov, 2024 -
Certified Reliability Leader
Association of Asset Management ProfessionalsMay, 2019- Nov, 2024 -
Problem Solving & Decision Making
Kepner-TregoeMar, 2016- Nov, 2024 -
Project Management
ESI InternationalOct, 2015- Nov, 2024 -
Lean Six Sigma Green Belt
Kimberly-ClarkMay, 2015- Nov, 2024 -
Continuous Improvement Professional
Kimberly-ClarkApr, 2015- Nov, 2024 -
Lean Blue Belt Certification
Kimberly-ClarkMar, 2015- Nov, 2024 -
SMED Certified Instructor
Kimberly-ClarkFeb, 2015- Nov, 2024 -
Equipment Improvement Certified Instructor
Kimberly-ClarkAug, 2014- Nov, 2024 -
Autonomous Care Certified Instructor
Kimberly-ClarkMar, 2014- Nov, 2024 -
5S Certified Instructor
Kimberly-ClarkFeb, 2013- Nov, 2024 -
OSHA 40 hour General Industries Certificate
Keene State CollegeJul, 2009- Nov, 2024 -
State of Connecticut Emergency Medical Responder - Department of Publich Health
State of ConnecticutJul, 2012- Nov, 2024
Experience
-
Marcal Paper
-
United States
-
Paper and Forest Product Manufacturing
-
1 - 100 Employee
-
Vice President - Converting Operations
-
Feb 2023 - Present
- Accountability for all converting products - Reporting responsibilities for SC, PA, NV, & TN
-
-
Mill Manager (Director of New Jersey Operations)
-
Nov 2021 - Feb 2023
Responsible for all operations of the New Jersey plant.
-
-
Director Of Operations (Manufacturing & Converting)
-
Mar 2021 - Nov 2021
Director of Operations for all on site manufacturing and converting assets
-
-
Director of Converting Operations
-
Oct 2020 - Mar 2021
-
-
-
Kimberly-Clark
-
United States
-
Manufacturing
-
700 & Above Employee
-
Senior Manufacturing Operations Consultant - OPEX & Reliability (North America)
-
Oct 2018 - Oct 2020
o Facilitate, promote and support OPEX/Lean cultural developmento Execute focused transformations and operational excellence deployment utilizing an extensive playbook of lean tools and methodologyo Coach and develop teams to use lean techniques and thinking (leader as teacher)o Use MBC, MS and OS diagnostic tools to identify full potential opportunities and gap closure planso Facilitate the development, introduction and tracking of standard work for leaders within focus areao Teach others to create and use OPEX and lean standardso Implement standards and processes to build One Best Way thinking and practices across North Americao Provide coaching and SME through problem solving activities to address ongoing barriers to deliveryo Identify capability gaps and prioritize activities to address these gapso Provide training to close the lean capability gaps within teamso Advocate value stream thinking through teaching and coaching teams in subject mattero Develop and manage systems and processes to ensure compliance with Plan, Do, Check, and Adjust processeso Provide mechanism to track and report scorecard of Operational Excellence transformation measures through weekly/month accountabilityo Ensure all barriers to the Strategy Deployment plan are identified and problem solved to achieve delivery of the resultso Support the internal governance / PDCA processeso Assist in prioritization and standardization of workload across KCNAo Supports the introduction of management processes to ensure sustainability Show less
-
-
Site Quality Manager
-
Apr 2018 - Oct 2018
• Worked with all mill assets (2 manufacturing, 5 converting, and distribution center) to ensure all product leaving the mill remained within specifications and exceeds customer requirements• Maintained and improved systems that support the assets continuous improvement and variability • reduction• Led mill through customer audits including a perfect score in private label customer quality audit• Led Mill biological testing program and worked with staff to bring up to ISO standards• Maintained legal required FDA documentation for codes as applicable• Led lab team as well as scheduling, maintenance, calibration, and documentation for all mill quality testing equipment per STM Show less
-
-
Manufacturing Operations Consultant
-
Apr 2017 - Apr 2018
• Led team of 85+ hourly and salaried team members over 2 tissue manufacturing lines through focused improvement efforts to meet equipment effectiveness Glidepath targets (OEE). • Delivered 1.5% improvement versus 2016 and 2% improvement versus projected output. • Led operating work area in full compliance with local EHS legislation and codes including reduction of machine risk by greater than 5% year over year.• Implemented several waste reduction processes leading to a reduction of 1% in waste.• Introduced an hourly performance feedback system helping hourly crew leaders to provide annual coaching and feedback to their teams. • Participated in periodic team reviews covering status versus objectives, strategies, action plans, maintenance activities and resource needs Show less
-
-
Tissue Converting Operations Consultant
-
Jun 2016 - Apr 2017
• Operating work area in full compliance with local EHS legislation and codes. • Understanding the EHS aspects and hazards of their work area and managing them to acceptable levels of risk or impact. • Reporting, investigating and promptly addressing substandard acts and conditions. • Ensuring that business activities support the facility EHS policy and the K-C Corporate OS&H and Environmental policies. • Identifying EHS aspects and hazards and managing them to acceptable levels of risk or impact. • Reporting, investigating and promptly addressing substandard acts and conditions. • Driving the setting of EHS objectives and evaluating the effectiveness of the facility EHS Management System. • Coordinating resource support for 4 converting lines. This involves coordinating engineering support (mechanical, electrical, process), coordinating maintenance/operator support as well as providing operations expertise. • Identify improvement areas and use Lean and OPEX tools to improve converting lines’ operation in order to support key business objectives. • Participate in periodic team reviews covering status versus objectives, strategies, action plans, maintenance activities and resource needs. • Develop and/or implement visual management, standard work, and leader standard work and other department programs/procedures such as centerline projects, training programs, housekeeping policies, etc. to deliver our Safety, Quality, Delivery, Cost and People Results. • Provide leadership to improve department housekeeping • Manage several of the Converting Department administrative tasks such as yellow material runs, Qhold disposition of wadding and finishing supplies, validate and correct Pims and MIDAS data, ensure visual management is up to date and that trigger points enable problem solving. • Work within and coach less experienced team members on internal control policies and procedures, OPEX and Lean tools. Show less
-
-
Site TPM Leader/Operational Excellence (OPEX) Change Agent
-
Sep 2014 - Jun 2016
• Integrated a focused Lean Improvement approach alongside the Kimberly-Clark and McKinsey & Company change teams at six manufacturing facilities (Jenks OK, Chester PA, Mobile AL, Huntsville, ON, CA, Fullerton, CA and New Milford CT).• Introduce autonomous care principles and the tie between Total Productive Manufacturing, Operational Excellence, and Lean manufacturing. • Support the roll out of Opex to multiple assets within the New Milford Mill throughout the diagnostic, design, and implementation phases. • Provide feedback and coaching to asset leaders in order to build a group capable of operational excellence without change team guidance.• Lead through influence by providing coaching to Mill leadership of all levels.• Lead complex Problem Solving Kaizen events at the site and various business functions (e.g. Research and Engineering) using advanced tools and thinking such as Kepner-Tregoe and Lean Six Sigma to help the sites address variability. Show less
-
-
Site Total Productive Maintenance (TPM) Leader
-
Feb 2013 - Jun 2016
• Trained large and small groups on Lean and TPM principles including 5S, Autonomous Care, Equipment Improvement, Simple Problem Solving, Strategy Deployment, Standard Work, Leader Standard Work, and Lean Basics. • Facilitated multi-day educational workshops including autonomous care, EIT, and Opex. • Established 3 new Equipment Improvement Teams which combined all 4 crews, maintenance and engineering into one team focused on continuous improvement, problem solving and breaking down barriers. • Coached 5 Equipment Improvement Teams through standardization, organization, and engagement in problem solving yielding $450,000/yr. savings. -The OLP team achieved a 2% production improvement year over year.- Multipack experienced a 9% reduction in delay and 14% OEE improvement.- Tissue manufacturing rewinder team achieved a sustained 5% improvement in quality. Show less
-
-
Health and Safety Coordinator
-
Jan 2009 - Feb 2013
• Managed 2,700 environmental, health and safety events.• Led Tissue Manufacturing team to 900+ injury free days. •Mill EH&S steering committee member setting strategy for the team to achieve first ever injury free year. •Coordinated various safety improvement solutions and prioritized the highest return solutions at ~$500,000/yr.
-
-
Manufacturing
-
Jul 2006 - Jan 2009
Held rolls with increasing responsibilities including work with powered industrial vehicles and overhead cranes.
-
-
Education
-
Liberty University
Bachelor’s Degree, Bachelor of Science in Business Management
Community
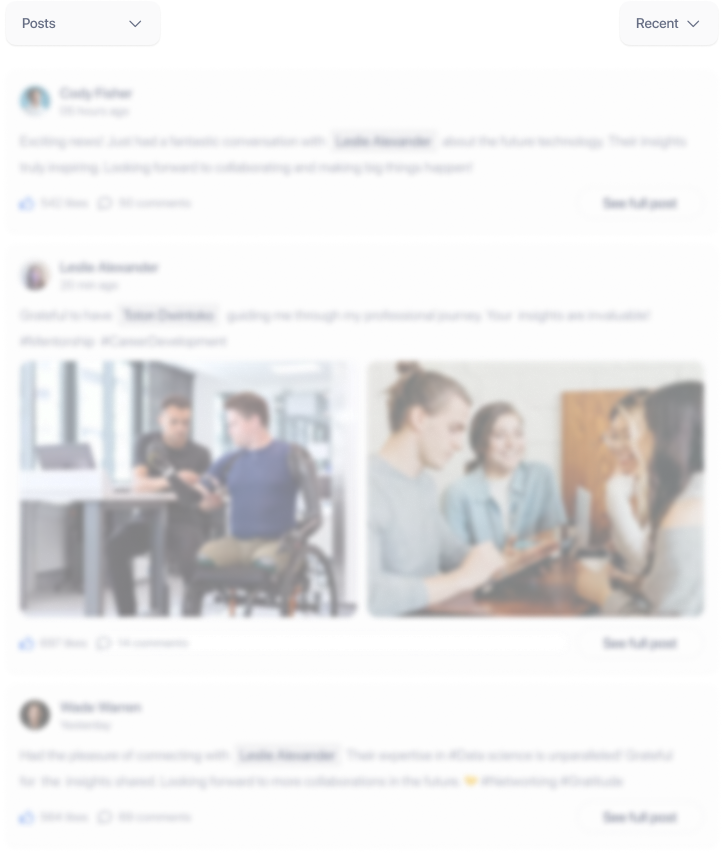