Tim Mann
Production & Compounding Manager at The Visual Pak Companies- Claim this Profile
Click to upgrade to our gold package
for the full feature experience.
Topline Score
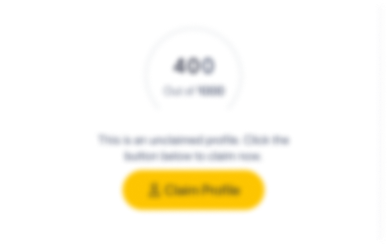
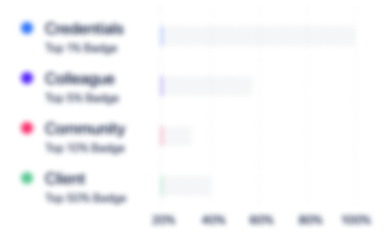
Bio
0
/5.0 / Based on 0 ratingsFilter reviews by:
Experience
-
The Visual Pak Companies
-
United States
-
Packaging and Containers Manufacturing
-
100 - 200 Employee
-
Production & Compounding Manager
-
Mar 2023 - Present
-
-
-
-
Production Manager
-
Apr 2014 - Present
-
-
-
-
Supervisor
-
Oct 2012 - Apr 2014
Supervised a staff of 60-80 employees with a mix of full time and temporary workers across 2 lines of production. Each line producing between 50,000 and 70,000 pizzas within a 10hr shift. Enforced all safety, quality, and company rules and guidelines. Reduced or increased head count based on work demand on a daily basis. Tracked and evaluated scrap on a daily basis, along with insuring that our efficiency with regards to machine run time and throughput were within target. Confirmed and balanced all production with regards to cases produced and machine run times for the shift. Maintained and confirmed hourly SPC charts for ingredient usage and weights to insure we were running within specifications and label weight. Approved all hours and established weekly schedules based on work load and rotation due to 6 day work week. Show less
-
-
-
Central Aquatics
-
United States
-
Health, Wellness & Fitness
-
1 - 100 Employee
-
Team Lead / Manager
-
Jan 2007 - Oct 2012
Managed up to 20 associates in a piece work environment over two shifts including, machine operators, frame builders, glass cutters and forklift operators. The facility produces 10-12 thousand fish tanks daily with all of the components for these tanks going through my department. Accountable for all manufacturing activities for 250 SKUs prior to the assembly process. Responsibilities included: Cost Management, Quality, Safety, Production, Sanitation and Maintenance in accordance with all corporate and regulatory guidelines. COST REDUCTION Increased productivity by 20% by reducing hours and running fluid schedules for production. Increased profitability by 40% for the department by doing bill of material reviews to insure that the proper labor was allocated to the proper components. In addition reduced overhead by cutting staff and cross training to avoid overtime. Successfully assisted with the start of implementation of SAP, which will help with reducing raw material and finished good inventory and increased the turns. Interacted with receiving, warehouse, traffic and production scheduling on a daily basis, ensuring the needs of the customer would be met while maintaining plant efficiency and reducing chance of downtime. Show less
-
-
-
Pactiv
-
Plastics Manufacturing
-
1 - 100 Employee
-
Production Supervisor
-
Mar 2005 - Dec 2006
Staffed Operators and Packers for 10-14 lines based on availability. Supervised over 50 associates across 5 departments. Prioritized work for Set Up, Extrusion, Shipping and Maintenance. Enforced all safety, quality, and company rules and guidelines. Reduced or increased head count based on work demand on a daily basis. Tracked and evaluated scrap on a daily basis, along with insuring that our efficiency with regards to machine run time and throughput were within target. Confirmed and balanced all production with regards to cases produced and machine run times for the shift within SAP Aided in the hiring, evaluating, promoting, transferring and training of employees during a period of growth where work force almost doubled. Trained down all necessary training with regards to new policies or procedures and also any required training.Evaluated production and efficiencies against both daily and monthly goals. Show less
-
-
-
Thistle Molded Group
-
United States
-
Plastics Manufacturing
-
1 - 100 Employee
-
Production Supervisor
-
Mar 2004 - Mar 2005
Created checklists for start up and shutdown to insure the highest quality products could be made.Developed and implemented changeover procedures, which reduced downtime and led to an increase in productivity.Tracked and evaluated scrap on a daily basis. Maintained overtime and attendance records daily.Enforced all safety, quality and company rules and guidelines. Staffed Operators and Packers for 10-14 press stations based on availability. Prioritized work for Set Up, Extrusion, Shipping and Maintenance. Show less
-
-
-
Rich Products Corporation
-
United States
-
Food and Beverage Manufacturing
-
700 & Above Employee
-
Production Manager
-
Sep 1989 - Jan 2004
Industry-leading $1.7 billion frozen food company and leading suppler/solutions provider to the Food Service and In-Store Bakery industries. Production Manager (2001 - 2004) Managed 23 hourly associates over two shifts with an operating budget of $2 million. Facility sales were $65 million with $30 million of this being from dry mix. Accountable for all manufacturing activities for 250 SKUs. Responsibilities included: Cost Management, Quality, Safety, Production, Sanitation, and Maintenance in accordance with all corporate and regulatory guidelines. COST REDUCTION Increased productivity by 20% and reduced labor and overhead by $100,000 by reducing hours and running fluid schedules for production and people. Reduced waste from 1% to 0.5% with process improvements, which saved over $160,000.Successfully assisted with implementation of SAP and MRP (QAD), which helped with reducing finished case inventory by 15% and increased the turns. Interacted with receiving, warehouse, traffic and production scheduling on a daily basis, ensuring the needs of the customer would be met while maintaining plant efficiency and reducing chance of downtime. ASSOCIATE PROGRAMS Conducted weekly Safety Meetings to discuss concerns or issues. This contributed to 600 days without a work related injury.Coached production associates to take ownership of assigned areas. Rebuilt an unorganized team in the mist of reoccurring turnover, limited experience and reluctant team members by setting clear expectations, coaching and stressing individual accountability. PRODUCTION Participated on team that developed and implemented HACCP program for plant. Assisted with several yield and quality improvement projects. In addition, aided with development and start up of all new products. Played a significant part in achieving 14 “Superior“ratings for plant sanitation and food safety inspections by the American Institute of Baking. Show less
-
-
Education
-
Maddison University
Bachelor of Science (B.S.), Business Administration and Management, General -
Leadership Skills Academy Buffalo NY
Bachelor of Science (BS), Business Administration and Management, General
Community
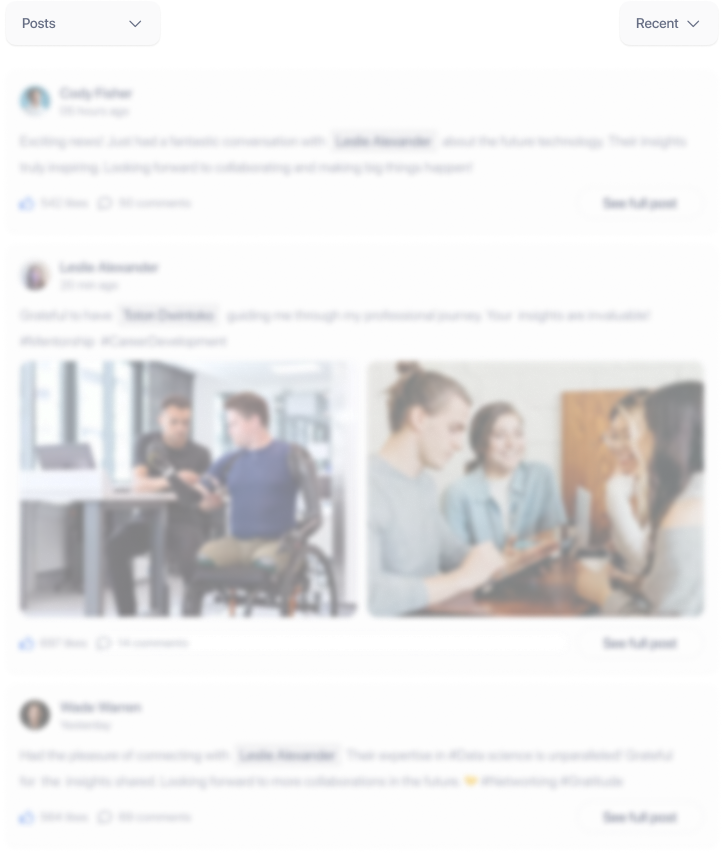