Tim Giles
Principal Specialist Engineer at Advisian- Claim this Profile
Click to upgrade to our gold package
for the full feature experience.
Topline Score
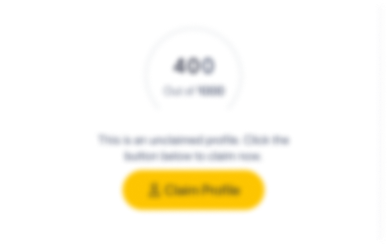
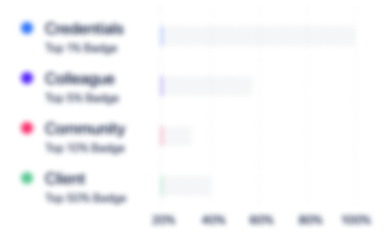
Bio


Experience
-
Advisian
-
Australia
-
Business Consulting and Services
-
700 & Above Employee
-
Principal Specialist Engineer
-
Jun 2015 - Present
Primary focus was on project management and process design development leadership for a new solution phase polymer process, with focus on development of Basis of Design and execution strategy for a pilot facility, integrated simulation of the polymerization and recovery process for pilot and commercial design, and process definition, equipment sizing and costing for pilot and commercial design. Also provided technical input into the following projects: - Concept phase evaluation of a SABIC petrochemical project, with focus on assessing utility requirements. - Front End Engineering Support for Enviro Innovate and Enviro Ambient CO2 capture technology. - Government of Alberta 2018 Petrochemical Diversification program applicant review process.
-
-
-
Worley
-
Australia
-
Professional Services
-
700 & Above Employee
-
Principal Specialist Engineer
-
Jan 2014 - Jun 2015
Shell Sarnia Advantaged Feedstock Expansion project - Aug 2014 to Apr 2015– Currently providing study leadership for assessing 15,000 bpd expansion of existing Crude Unit #2 facilities, with focus on heat integration, pre-fractionation and atmospheric distillation.Manager MEG Systems – Jan 2014 to July 2015 – Held responsibility for development of Monoethylene Glycol (MEG) recovery technology, and associated studies. Studies completed included a revamp study for a MEG Reclaimer stationed at the Burullus Gas Idku site near Alexandria Egypt, and conceptual design of a MEG Recovery Unit Pilot Plant that was ultimately cancelled due to a change in program focus.
-
-
Principal Specialist Engineer
-
Jun 2005 - Dec 2013
Chief Process Engineer – Apr to Dec 2013. Administration of Calgary Process Team.Director, Process Engineering – Jan to Apr 2013. Administration of the Calgary Process Engineering Team.Manager Process Engineering for Mineable Oil Sands July 2010 – Dec 2012. Include Lead role for Total’s JNM Basic Engineering update, and contribution to non-aqueous mineable oil sands bitumen extraction technology.Expander Energy, Edmonton Alberta – Wood Gasification. Pre-FEED using CHOREN Carbo-V® gasification tech, Syngas cleanup, Water Shift Reaction technology, CO2 removal via Selexol, FT synthesis, SMR, autothermal reactors, hydrocracking, PSA and CO2 liquefaction.Total Canada, Fort McMurray – Deer Creek. 100,000 BBLPSD Oil Sands Production. Responsible for development of Paraffinic Froth Treatment process.Enbridge Canada, Edmonton – Alberta Saline Aquifer. Responsible for evaluation of CO2 compression and pipeline options for CO2 Capture.Syncrude Canada, Fort McMurray – CO2 Capture Study. Led feasibility study for capture of CO2 from SMR and Benfield Hydrogen plants, FGD exhaust, and CO Boilers.Shell Canada, Fort McMurray – Albian Sands Expansion 1. Lead development of Functional Description, C&E and SD Keys, and process audit.Korea National Oil Company, Fort McMurray – SAGD Study. Pre-FEED study using diluent enhanced separation. Quadrise, Calgary Alberta – CO2 Sequestration. Pre-Feed evaluation of gasification facilities.Nexen Canada Ltd., Fort McMurray – CO2 Sequestration Study with retrofit of OSTG and GTG-HRSG for oxyburn. Husky Energy, Fort McMurray – Heavy Oil Recovery. Screening study assessing enhancement to SAGD operations utilizing high temperature solvent treater technology.CCR Technologies Inc., Egypt – Burullus Gas Debottlenecking of Mobile Reclaiming Units. Petro-Canada, Fort McMurray – Fort Hills Oil Sands. Conceptual design building upon TrueNorth Oil Sands Ltd (2000 - 2002). Lead responsible for overseeing 15 process engineers.
-
-
-
Colt Engineering
-
Oil and Gas
-
1 - 100 Employee
-
Sr Process Engineer
-
Nov 2002 - May 2005
CCR Technologies Inc., Norway – Hammerfest LNG (~$200 M). Installation of a 16 m3/h MEG reclaimer facility designed to recover MEG from produced water recovered from the sub-sea well tieback line. Facilities design excluded the pressure letdown and primary oil-gas-water separation, but included the detailing of facilities to separate water from MEG and recover a salt rich waste sludge stream. Process Lead for initial FEED efforts, then Technology Advisor responsible for overseeing the technical detailing of the facility on behalf of the licensor, CCR Technologies Inc.CCR Technologies Inc., Russia – Sakhalin II LNG (~$20 M). Installation of a small MEG reclaimer facility designed to recover MEG from produced water recovered from the sub-sea well tieback line. Facilities provided were similar to those for the Hammerfest project with the exception that a salt brine waste product was produced in place of a sludge. Process Lead for initial FEED efforts and Technology Advisor responsible for overseeing the technical detailing of the facility on behalf of the licensor, CCR Technologies Inc.CCR Technologies Inc., Gulf of Mexico – Kerr-McGee Red Hawk project (~$20 M). Provision of technical auditing on behalf of CCR Technologies, of engineering completed by another engineering contractor who was detailing the design of an ~ 500 BBLPD MEG reclaimer, processing the aqueous stream recovery from platform separation facilities. Process Engineering Manager responsible for leading a team of 25-30 process engineers, establishing work practices and design guidelines, while also providing lead level support to other projects as noted over this period.Petro-Canada, Mississauga Ontario – Low Sulfur Gasoline (~$200 M). Feed level development of facilities upgrade to reduce sulfur to less than 15 ppm. Sr. Process Engineer, on short term assignment, responsible for mass balance development and modeling of complex multiphase heater recovery circuits.
-
-
Sr Process Engineer
-
May 1998 - Oct 2002
Nexen Canada Ltd., Fort McMurray – Long Lake Commercial SAGD (~$250 M). Greenfield installation of steam assisted gravity drainage (SAGD) facilities designed to recover and separate bitumen from the produced water using FWKO, treater technology with electrostatic coalescing, lime softening based water treatment, glycol cooling circuits, and assorted utilities and infrastructure. TrueNorth Oil Sands Ltd., Fort McMurray – TrueNorth Oil Sands (~$3.0 B). Engineering ranging from Pre-Feed to near completion of an EDS for facilities including aspects of warm water and solvent extraction, solvent flash and distillation recovery, electrical cogeneration, and all required general utilities. Alberta Energy Corporation (AEC), Fort McMurray – Foster Creek SAGD Pilot Plant. Develop proposals for upgrading the water purification system to incorporate Aqua Pure mechanical recompression water distillation for recovery of boiler feed water and heat recovery from high pressure steam condensate blowdown. Canadian Chemical Reclaiming Inc. – Mobile Units 4/5 (~$5.0 M). The mobile facilities utilized proprietary flash desalting technology coupled with vacuum distillation, water cooling towers, rotary vacuum pumps, refrigeration utilities, and PLC control, all mounted on mobile trailers Canadian Chemical Reclaiming Inc. – Shell Mensa WD143 facilities Gulf of Mexico (~$10 to 15 M). The facilities utilized proprietary flash desalting technology similar to that noted for Units 4/5 above, with the exception that these facilities were larger and were installed offshore in compliance with API-14C and related offshore standards. Canadian Chemical Reclaiming Inc. – Mobile Units 3 (~$3.0 M). The mobile facility utilized proprietary flash desalting technology similar to that noted for Units 4 and 5 above.
-
-
-
-
Lead Process Development Engineer
-
Apr 1996 - Apr 1998
Lead Process Development Engineer for the development of a 350 KTA Advanced SCLAIRTECH solution based polyethylene synthesis process. This process involved aspects of ethylene, octene and butene purification (with alumina, mole sieves and silica gel), reaction utilizing tubular and stirred reactors processing supercritical fluids at up to 4500 psig, distillation utilizing structured packing and trayed towers with thermosyphon and forced circulation reboilers, polymer handling including extrusion, antioxidants and UV stabilizers, 600 psig steam generation, hot oil heating, refrigeration, tempered water cooling, and general utilities such as nitrogen, instrument air, steam tracing and cooling water. Responsibilities also included specification of piping materials utilizing nickel plating and overlay, inconel and monel, as well as specification of sizing of control valves operating in two-phase polymer service.This process utilized a Zieglar-Natta catalysis in a high pressure supercritical solvent, synthesis of molten linear low density polymer, and facilities to recover/cycle and purify the solvent and un-reacted monomers as well as to pelletize and suitably process the pellets for delivery to the customer. The completion of this project required the coordination of a research team in Sarnia and Calgary as well as direct interface with internal and contract Engineering personnel. Efforts started in 1993 with the preparation of a basic data package that justified the construction of a pilot/demonstration plant in Sarnia, Ontario, where-in he held lead process responsibility, followed by the approval of a World scale Advanced SCLAIRTECH facility for Joffre, Alberta, where-in he was the principal contact between the project team and the Research and Development Team. Further details of this project are considered confidential.
-
-
Lead Process Development Engineer
-
Sep 1994 - Mar 1996
-
-
Process Operations Contact Engineer
-
Jul 1991 - Aug 1994
Process Operations Engineer with accountability for daily operation of catalyst removal and solvent recovery operations as well as various environmental concerns such as flares, effluent decanting, and Dowtherm-A operations. Responsibility included daily coordination with the operations team, supplier contracts, participation in non-conformance investigations, and participation in upgrades required to achieve ISO9002 certification.
-
-
-
DuPont Canada
-
Kingston, Ontario
-
Lead Development Engineer
-
Feb 1988 - Jun 1991
Lead Development Engineer for the preparation of a basic design package for a 25 kg/h polyethylene pilot plant planned for Kingston, Ontario. Completed key documents such as conceptual and detailed PFDs, mass and energy balance data, and equipment data sheets, prior to transferring to the production facility in Sarnia, Ontario. This design effort focused on small scale tubing, reactors, diaphragm compressors, ground flares, catalytic oxidation and alkane purification. Due to market conditions, this pilot facility was never built. Process Development Engineer responsible for the conceptual design of 2000 kg/h facilities for the synthesis (5000 psig hydrogenation with ammonia cooling) and recovery via vacuum distillation (10 Torr) of a diamine intermediate required for synthesis of Nylon 12,12. The job entailed completion of plant trails to collect required design data, development of process flow diagrams and mass and energy balance data, detailed design with Research responsibility for P&IDs and plans for tie-in into existing facilities. Involvement included co-leadership during commissioning and startup of the facilities.
-
-
Education
-
University of Toronto
Master's Degree, Chemical Engineering -
University of Toronto
Bachelor's Degree, Chemical Engineering
Community
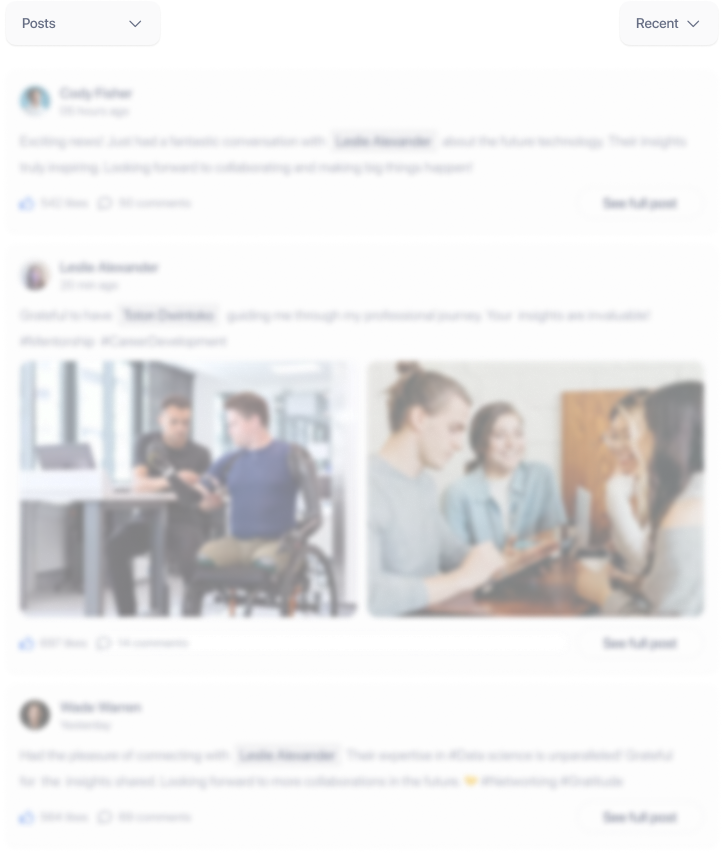