Tim Cook
Director of Thermatech Product Solutions at Bassett Mechanical- Claim this Profile
Click to upgrade to our gold package
for the full feature experience.
Topline Score
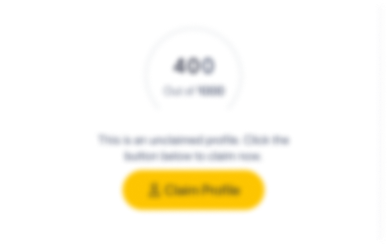
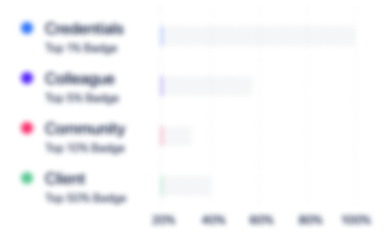
Bio
0
/5.0 / Based on 0 ratingsFilter reviews by:
Experience
-
Bassett Mechanical
-
United States
-
Industrial Machinery Manufacturing
-
100 - 200 Employee
-
Director of Thermatech Product Solutions
-
Oct 2022 - Present
Kaukauna, Wisconsin, United States
-
-
Senior Manager of Thermatech Product Solutions
-
Oct 2021 - Oct 2022
Kaukauna, Wisconsin, United States
-
-
Engineering & Quality Manager - Metal Fabrication Division
-
Dec 2020 - Sep 2021
Kaukauna, Wisconsin, United States
-
-
Engineering Manager - Metal Fabrication Division
-
Nov 2019 - Dec 2020
Kaukauna, WI
-
-
-
-
Project Engineer 1 - Product Manager/Project Manager
-
May 2018 - Nov 2019
De Pere, Wi Global Product Manager for Durr MEGTEC's Particulate Control - Pulse Jet Fabric Filter offering. Responsible for both the engineering and management of emission control projects. Involved with any or all of the following emission control equipment: Wet Electrostatic Precipitators, Fabric Filters, Wet and Dry Flue Gas Desulfurization, Selective Catalytic and Non-Catalytic Reduction Systems, Evaporative Coolers, and Thermal and Catalytic Oxidizers. Requires interaction with… Show more Global Product Manager for Durr MEGTEC's Particulate Control - Pulse Jet Fabric Filter offering. Responsible for both the engineering and management of emission control projects. Involved with any or all of the following emission control equipment: Wet Electrostatic Precipitators, Fabric Filters, Wet and Dry Flue Gas Desulfurization, Selective Catalytic and Non-Catalytic Reduction Systems, Evaporative Coolers, and Thermal and Catalytic Oxidizers. Requires interaction with customer base, design team, manufacturing personnel and service technicians to execute projects on schedule and within the approved budget. Work with process engineers and drafting/design team to develop reliable, cost effective pollution control systems. Size and specify key system components, including fans, pumps, heat exchangers, valves, burners, etc… Coordinate equipment installation and commissioning. Maintain complete and accurate project documentation, including engineering calculations and customer approvals. Track project costs and identify opportunities for cost reduction. Develop and maintain project schedule. Frequent communication with customer to provide status updates and address open issues. Occasional travel required for site meetings with customers, HAZOP meetings, equipment start-up and optimization. Timely and thorough internal project reporting (progress reports, trip reports, change orders, etc...).
-
-
Engineer 3 - Mechanical Project Engineer
-
Aug 2015 - May 2018
De Pere, Wisconsin Responsible for both the engineering and management of emission control projects. Involved with any or all of the following emission control equipment: Wet Electrostatic Precipitators, Fabric Filters, Wet and Dry Flue Gas Desulfurization, Selective Catalytic and Non-Catalytic Reduction Systems, Evaporative Coolers, and Thermal and Catalytic Oxidizers. Requires interaction with customer base, design team, manufacturing personnel and service technicians to execute projects on… Show more Responsible for both the engineering and management of emission control projects. Involved with any or all of the following emission control equipment: Wet Electrostatic Precipitators, Fabric Filters, Wet and Dry Flue Gas Desulfurization, Selective Catalytic and Non-Catalytic Reduction Systems, Evaporative Coolers, and Thermal and Catalytic Oxidizers. Requires interaction with customer base, design team, manufacturing personnel and service technicians to execute projects on schedule and within the approved budget. Work with process engineers and drafting/design team to develop reliable, cost effective pollution control systems. Size and specify key system components, including fans, pumps, heat exchangers, valves, burners, etc… Coordinate equipment installation and commissioning. Maintain complete and accurate project documentation, including engineering calculations and customer approvals. Track project costs and identify opportunities for cost reduction. Develop and maintain project schedule. Frequent communication with customer to provide status updates and address open issues. Occasional travel required for site meetings with customers, HAZOP meetings, equipment start-up and optimization. Timely and thorough internal project reporting (progress reports, trip reports, change orders, etc...).
-
-
-
UW-Green Bay
-
United States
-
Transportation/Trucking/Railroad
-
Men's and Women's Nordic Ski Team Associate Head Coach
-
Jun 2012 - Jun 2018
Green Bay, Wisconsin Area Create year-round individualized training plans. Conduct training sessions. Race day support and wax technician.
-
-
-
Fincantieri Marine Group
-
United States
-
Shipbuilding
-
500 - 600 Employee
-
Engineer II: Lead Structural Engineer
-
Mar 2014 - Aug 2015
Marinette, Wi • Develop functional designs for structural systems on project • Assist the Project Lead in determining the technical requirements for the project • Cost Account Manager for Dept – Labor (5.4 mil) • Manage structural design/drafting group (Up to 30 resources) • Determine the most cost effective solutions to several assembly, design and/or construction methods.
-
-
Engineer I: Structural Engineer
-
Aug 2011 - Mar 2014
Marinette, Wi • Review functional products for all structural systems on project • Cost Account Manager for Dept – Labor ($5.4 mil). • Manage all customer directed changes affecting Dept for 6 projects. • Verified the functional design through calculations and validated the design. • Worked many cost savings initiatives for production. • Completed project on reducing construction costs by approximately $500,000.
-
-
Associate Structural Engineer
-
Jan 2011 - Aug 2011
Marinette, Wi • Cost Account Manager for Dept - labor and material ($28.2 Mil). 6 projects. • Reviewed design producibility requests from production for applicability and implementation. • Worked with production as liaison for resolution of Trial Cards prior to delivery of LCS-3.
-
-
-
-
Production Supervisor/Manufacturing Engineer
-
Sep 2010 - Jan 2011
Wausau, WI Responsible for meeting production goals for assigned departments · Planning for 3rd shift of assigned departments · Coordination of raw materials, machines, and manpower resources · Responsible for meeting ship dates
-
-
-
Wausau Paper
-
Paper & Forest Products
-
100 - 200 Employee
-
Production Planning- Summer Intern
-
May 2010 - Sep 2010
Rhinelander, Wi Scheduled and trimmed orders to No. 6 and No. 9 Paper Machines Worked with Paper Machine Superintendents and Technical Service employees to create and document new grades of paper Researched and documented roll condition after rewinding such as roll size, roll weight and lineal footage to reduce waste Researched and documented trimming and scheduling process and presented ways to improve process as a Lean Manufacturing effort
-
-
-
Verso Paper Corp.
-
United States
-
Paper and Forest Product Manufacturing
-
300 - 400 Employee
-
Preventive Maintenance Program Development Engineer- Summer Intern
-
May 2008 - Aug 2008
Escanaba, Mi Research and document the Tank/Pressure Vessel/Pressure Relief Device Risk management essential care strategy tasks Research and document preventive and predictive maintenance, and Condition Monitoring Inspection specifications for critical assets Enter/update the PM02 records and history information into the SAP database Preventive Maintenance risk management plan for E3 Jet Heads, E3 Headbox, and Wrapper. Researched and Documented the details of equipment and process… Show more Research and document the Tank/Pressure Vessel/Pressure Relief Device Risk management essential care strategy tasks Research and document preventive and predictive maintenance, and Condition Monitoring Inspection specifications for critical assets Enter/update the PM02 records and history information into the SAP database Preventive Maintenance risk management plan for E3 Jet Heads, E3 Headbox, and Wrapper. Researched and Documented the details of equipment and process components Defined the lubrication, preventive & predictive maintenance, and Condition Monitoring Inspection specifications for each asset ntered the information into the DMSI MAINTelligence databases(or SAP as appropriate) Produced the DMSI bar-coded equipment labels and installed the labels at the equipment locations Worked with maintenance & operations personnel assigned to perform routes to establish the sequential order of points in the routes Served as a point of contact for technical assistance and training for the operations of the DMSI software and hardware Show less
-
-
-
-
Preventive Maintenance & Condition Monitoring Program Development Engineer-Summer Intern
-
May 2007 - Aug 2007
Escanaba, Mi Researched and Documented the details of equipment and process components Defined the lubrication, preventive & predictive maintenance, and Condition Monitoring Inspection specifications for each asset Entered the information into the DMSI MAINTelligence databases(or SAP as appropriate) Produced the DMSI bar-coded equipment labels and installed the labels at the equipment locations Worked with maintenance & operations personnel assigned to perform routes to establish the sequential… Show more Researched and Documented the details of equipment and process components Defined the lubrication, preventive & predictive maintenance, and Condition Monitoring Inspection specifications for each asset Entered the information into the DMSI MAINTelligence databases(or SAP as appropriate) Produced the DMSI bar-coded equipment labels and installed the labels at the equipment locations Worked with maintenance & operations personnel assigned to perform routes to establish the sequential order of points in the routes Served as a point of contact for technical assistance and training for the operations of the DMSI software and hardware Show less
-
-
Education
-
University of Wisconsin-Platteville
Master of Science in Engineering, Engineering Management & Structural Engineering -
Northern Michigan University
Bachelor's degree, Mechanical Engineering Related Technologies/Technicians & Mathematics
Community
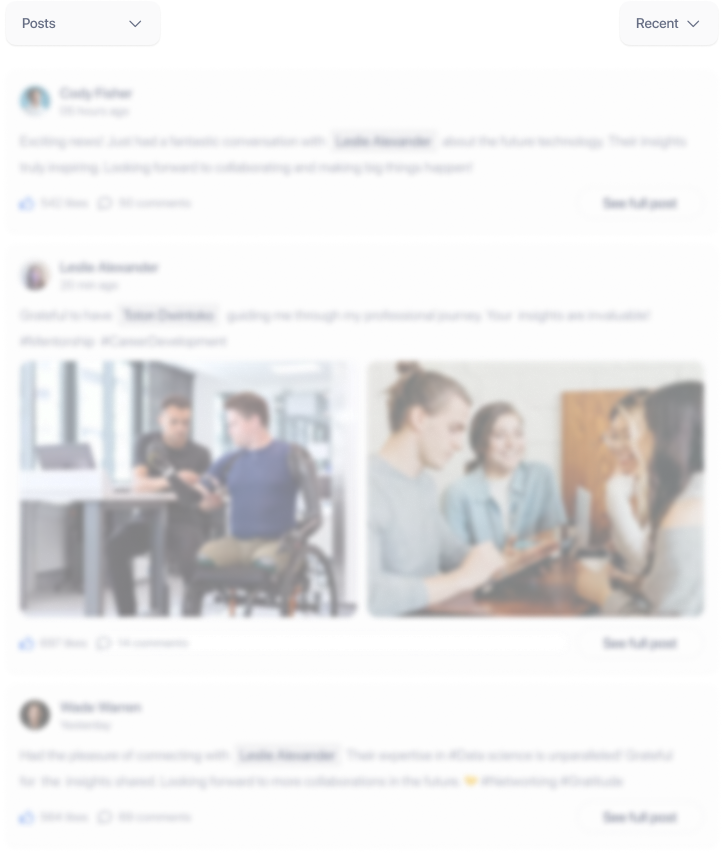