Tibor Tamas
Corporate Quality Manager at Cablcon- Claim this Profile
Click to upgrade to our gold package
for the full feature experience.
-
English Full professional proficiency
-
Hungarian Native or bilingual proficiency
-
Romanian Professional working proficiency
Topline Score
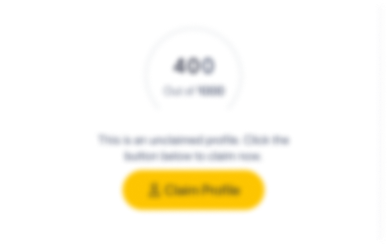
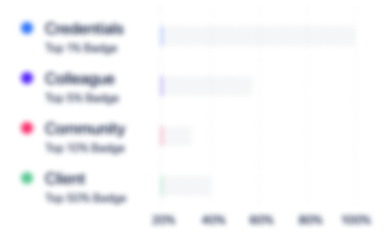
Bio

Kevin Yoon
I had the greatest pleasure of working with Tibor at Alcatel. He is definitely all-around individual with extensive industry experience in telecommunication. With deep knowledge in quality and productengineering, he was a great asset to the team. Looking forward to working with him in the future.

Raluca Vlasea, MBA, PMP
I had the pleasure of working with Tibor while at RIM. He is an intelligent, resourceful and dynamic individual with extensive industry experience. He is very skilled at creating and maintaining customer relationships and I got to experience that first hand during a business trip to one of the AT&T distribution centers. He is highly viewed and appreciated among his peers and leadership across all functional groups at RIM, for his can do attitude, proven aptitude to drive results and his knowledge. Tibor will have a benefic impact in any organization and be a key member in any team.

Kevin Yoon
I had the greatest pleasure of working with Tibor at Alcatel. He is definitely all-around individual with extensive industry experience in telecommunication. With deep knowledge in quality and productengineering, he was a great asset to the team. Looking forward to working with him in the future.

Raluca Vlasea, MBA, PMP
I had the pleasure of working with Tibor while at RIM. He is an intelligent, resourceful and dynamic individual with extensive industry experience. He is very skilled at creating and maintaining customer relationships and I got to experience that first hand during a business trip to one of the AT&T distribution centers. He is highly viewed and appreciated among his peers and leadership across all functional groups at RIM, for his can do attitude, proven aptitude to drive results and his knowledge. Tibor will have a benefic impact in any organization and be a key member in any team.

Kevin Yoon
I had the greatest pleasure of working with Tibor at Alcatel. He is definitely all-around individual with extensive industry experience in telecommunication. With deep knowledge in quality and productengineering, he was a great asset to the team. Looking forward to working with him in the future.

Raluca Vlasea, MBA, PMP
I had the pleasure of working with Tibor while at RIM. He is an intelligent, resourceful and dynamic individual with extensive industry experience. He is very skilled at creating and maintaining customer relationships and I got to experience that first hand during a business trip to one of the AT&T distribution centers. He is highly viewed and appreciated among his peers and leadership across all functional groups at RIM, for his can do attitude, proven aptitude to drive results and his knowledge. Tibor will have a benefic impact in any organization and be a key member in any team.

Kevin Yoon
I had the greatest pleasure of working with Tibor at Alcatel. He is definitely all-around individual with extensive industry experience in telecommunication. With deep knowledge in quality and productengineering, he was a great asset to the team. Looking forward to working with him in the future.

Raluca Vlasea, MBA, PMP
I had the pleasure of working with Tibor while at RIM. He is an intelligent, resourceful and dynamic individual with extensive industry experience. He is very skilled at creating and maintaining customer relationships and I got to experience that first hand during a business trip to one of the AT&T distribution centers. He is highly viewed and appreciated among his peers and leadership across all functional groups at RIM, for his can do attitude, proven aptitude to drive results and his knowledge. Tibor will have a benefic impact in any organization and be a key member in any team.

Credentials
-
Certified Engineering Technologist
OACETT - Ontario Association of Engineering Technicians and TechnologistsJan, 1997- Oct, 2024 -
ASQ Certified Quality Auditor
ASQ - World HeadquartersJun, 2022- Oct, 2024
Experience
-
Cablcon
-
United States
-
Telecommunications
-
1 - 100 Employee
-
Corporate Quality Manager
-
May 2021 - Present
Directing and implementing strategies to strengthen and improve quality within the organization Leading the focus in reducing the Cost of Poor Quality Maintaining corporate TL9000 & ISO certification Responsible for safety Directing and implementing strategies to strengthen and improve quality within the organization Leading the focus in reducing the Cost of Poor Quality Maintaining corporate TL9000 & ISO certification Responsible for safety
-
-
-
Emblem Solutions
-
United States
-
Telecommunications
-
1 - 100 Employee
-
Sr. Quality & Reverse Logistics Manager
-
Jan 2019 - Jan 2021
Overall management of the operations for carrier customer relations, sourcing and procurement, device quality, warranty repair, field quality, call center, service parts & technical support and managing 3rd party service vendors. Overall management of the operations for carrier customer relations, sourcing and procurement, device quality, warranty repair, field quality, call center, service parts & technical support and managing 3rd party service vendors.
-
-
-
ZTE Corporation
-
China
-
Telecommunications
-
700 & Above Employee
-
Quality Manager
-
Sep 2016 - Dec 2018
Formulates and maintains quality objectives complementary to corporate goals and objectives Reviews all data obtained from customer to ensure quality consistency and compliance Prepares and presents quality findings to management through weekly reports Designs and implements quality best practices based on customer feedback Investigates and prepares corrective actions plans based on customer feedback Coordinate and facilitate internal and external quality audits as necessary Identify and develop new quality activities which enhance the account team quality program Organize and maintain all quality related records for the account team Provide customer support for quality issues as required Process and review Early Warning Process (EWP) data provided by customer after launch Process and review Field Performance Reports (FPR's) and provide official responses Lead quality section of SPR (Supplier Performance Review) and provide official responses Show less
-
-
-
Alcatel mobile
-
China
-
Telecommunications
-
300 - 400 Employee
-
Quality Manager
-
Mar 2015 - Feb 2016
Manage product quality specifications and requirements for North America Prepare and manage pre-FAI, FAI and all other product related inspections Act as a representative of the quality team towards customers and internal teams Participate in all DR (Decision Reviews) through project lifecycle as quality representative; Design Concept to End of Life. Be main point of contact for all product quality related topics Maintain and improve internal processes and procedures related to product quality Communicate significant issues or developments identified during quality activities and provide recommended design changes or process improvements to management Prepare reports to communicate involvement and outcomes of quality activities Develop, maintain and apply quality requirements and standards for the development of new products Work closely with production to design, implement and improve methods for process control, process improvement, testing and inspection prior to product launch to mitigate mass production risks Organize, Define, Manage and Execute EWP activities for carriers Provide and review EWP reports with customers and manage all action items to closure Work closely with reverse logistics on field return data & RCA Drive local FLFA, root cause analysis, corrective action and 8D report generation for all customer quality issues. Communicate preliminary findings and 8D report to customer for agreed closure. Ensure lessons learned are integrated into new projects NPI activities Show less
-
-
-
Pantech Wireless, Inc.
-
Telecommunications
-
200 - 300 Employee
-
Quality Manager
-
Jul 2012 - Mar 2015
Maintain all Discrepancy Reports (RQIL) from customers in the customer data base system by organizing updated developing information of open issues Respond to Discrepancy reports from the distribution centers – working closely with the Logistics team to resolve issues. Participate in all Quality related meetings with customers Collaborate with HQ team as it relates to PCN (Product Change Notification) submissions Follow up on all Logistics related Corrective Actions until all issues are closed Collaborate with HQ and RL teams as it relates to receiving all FAI deliverables by customer deadline responsible for First Article Inspection (FAI) and successful product launches Receive and Respond to Customer Quality Issues as single point of contact Facilitate responses to Periodic SPR Submit monthly reports to Customer per MPA requirements Manage Corrective Action responses Create documentation based on ISO/TL guidelines for key processes/procedures Facilitation of production readiness activities Facilitation of Infrastructure testing/pre launch testing Management Representative for TL 9000 Quality Program Manage TL9000 certification & registration Internal auditor for Pantech Show less
-
-
-
BlackBerry
-
Canada
-
Software Development
-
700 & Above Employee
-
Customer Quality Manager
-
Mar 2008 - Jun 2011
Contributed to quality and reliability roadmapsMaintained customer-facing, closed loop corrective action process program that accelerated the defect detection, correction and preventative activitiesMaintained all Discrepancy Reports from customers in the customer data base system by organizing updated developing information of open issuesResponded to discrepancy reports from MDC and FDCProject management for in depth analysis and extensive corrective actionLead customer call back sessions and Early Warning Process activitiesResponsible for First Article Inspection (FAI)/Source Audit activities at the customer levelIdentified quality characteristics that are important for achieving customer satisfaction - updated and published these characteristicsCollaborated with head quarter team as it relates to PCN (Product Change Notification) submission to CustomerMonitored quality of service and productsManaged projects for in depth analysis and extensive corrective actionCorrective and preventive processes coordinationCarrier scorecards - helped in collecting relevant information for quality and reliabilityContinuous improvement and customer satisfaction, understanding the trends related to quality and reliability for major customersSubmitted monthly reports to customer per MPA/requirementsManaged corrective action responses to internal organization issues as well as administrative ownership of CAPA databaseMaintained Product and Delivery Quality dashboard/metrics on monthly basis.Regular visits to the carriers (AT&T, Sprint, T-Mobile, US Cellular, Brightstar and Celistics), including quarterly business reviews (QBR) and supplier performance reviews (SPR)Acted as customer representative during audits of consigned materials and related processes inside RIM and outsourcing partnersServed as the single main contact point for all quality and reliability questions and inquiries Show less
-
-
Process Development Engineering Specialist
-
May 2006 - Mar 2008
Generated product time standards & performed capacity studiesEvaluated and implemented new equipment platforms and concepts in the areas of assembly automation and material handlingEvaluated new assembly line conceptsInvestigated and recommended improvements to existing processesWritten a white paper and implemented some aspectsOrdered & commissioned new automated equipmentDefined, analyzed and implemented processes to improve quality, yield and customer satisfactionFamiliar with Point of Sale packaging and packaging materialsResponsible for process improvements, new product introduction and also supporting with new process implementation Show less
-
-
-
Accutech EMS
-
Kitchener, ON
-
Project Manager
-
Dec 2005 - Feb 2006
Provided guidance and direction to team members Ensured that programs are on track & identified risks and delays Aided in developing new manufacturing & assembly processes Responsible for new product introduction (NPI) and engineering changes (EC) Responsible for enhancing the organizations reputation through analysis & organization of multiple projects Accepted ownership for accomplishing new & different request & explored opportunities to add value to customer needs Provided guidance and direction to team members Ensured that programs are on track & identified risks and delays Aided in developing new manufacturing & assembly processes Responsible for new product introduction (NPI) and engineering changes (EC) Responsible for enhancing the organizations reputation through analysis & organization of multiple projects Accepted ownership for accomplishing new & different request & explored opportunities to add value to customer needs
-
-
-
Linamar Corporation
-
Canada
-
Motor Vehicle Manufacturing
-
700 & Above Employee
-
Project Engineer
-
Feb 2005 - Oct 2005
Responsible for the manufacturing aspects of two automated assembly lines Develop & implement manufacturing documentation Ensured successful new product launches on time and on budget, by leading and coordinating cross-functional teams Developed and maintained project budgets, program checklists, project timing charts, and technical records Continuous improvement activities, including feasibility studies for installation of new equipment Prepared capital equipment justifications, vendor selection, design review/approval, buy-off and equipment commissioning of $1,000,000 to 3.4 million highly automated lines Planed cell layout, process flows and estimate line balance Participated in APQP, PPAP, PFMEA, Control Plan, Process Flow and DFMEA meetings Manufacturing support with a “hands-on” approach Show less
-
-
-
Omron Industrial Automation Europe
-
Netherlands
-
Automation Machinery Manufacturing
-
700 & Above Employee
-
Manufacturing Technologist
-
Dec 2001 - Feb 2005
Responsible for final approval and turnover of projects to manufacturing Develop & implement manufacturing documentation Developed and maintained project budgets, program checklists, project timing charts, and technical records Worked with Product Engineering on product development and specification development Continuous improvement activities, including feasibility studies for installation of new equipment Prepared capital equipment justifications, vendor selection, design review/approval, buy-off and equipment commissioning of $25,000 to 2.4 million manual and highly automated lines (5 sec. cycle time) Participated in APQP, PPAP, PFMEA, Control Plan, Process Flow and DFMEA meetings Assisted in determining capital equipment/tooling necessary to provide manufacturing capacity and develop short and long term budgets accordingly Traveled to various supplier sites as necessary to achieve plant objectives and to evaluate their proposed equipment Selected and supervised suppliers for subcontracted operations Show less
-
-
-
BBi Inc.
-
Guelph, ON
-
Program Manager
-
May 2001 - Oct 2001
Managed and co-ordinate programs from award of order through design, tool fabrication, validation, to successful production (Cradle to grave project management) Launched, maintained and completed programs on time and below budget, including GMT 610, GMT 8* series Ensured that each functional area understands its own responsibilities and the impact of their work on the program Kept abreast on all work performed on the program and ensure that all outputs required by the contract are performed within the defined schedule Monitored the costs incurred and schedule achieved to determine if the program is on time and within budget, and work with other functions to ensure the program remains on target Interfaced with sales, plants and customers on design, materials and process issues as well as co-ordinating all new projects, engineering changes, following PPAP procedures and other QS 9000 documentation Provided engineering, tooling and design support to both customers and manufacturing plants Influenced technical product specifications from internal/external customer’s needs Provided product update and distributed technical information to external/internal customers Actively pursued new business through increased content, new program acquisition and the development of new material and processes Served as central owner of the product providing day to day decisions that affect the product as issues arise Initiated research to ensure that new and existing products are aligned with market needs Show less
-
-
-
Dana Incorporated
-
United States
-
Motor Vehicle Manufacturing
-
700 & Above Employee
-
Manufacturing Technologist
-
Mar 1999 - May 2001
Responsible for the manufacturing aspects of three automated manufacturing cells of aluminum brazed oil coolers and a E-coat paint line Ensured successful new product launches, on time and on budget, by leading and coordinating cross-functional teams Develop and maintain project budgets, program checklists, project timing charts, and technical records Reviewed customer drawings and supplied Sales with updated pricing for re-quote of engineering revisions Worked with Product Engineering on product development and specification development Continuous improvement activities, including feasibility studies for installation of new equipment, including a semi-automated 4-head riveter, an automated burst tester, a semi-automated hose assembly machine, an automatic torque machine and a semi-automated production cell (Multicell) Prepared capital equipment justifications Plan cell layout, process flows and estimate line balance Participated in APQP, PPAP, PFMEA, Control Plan and Process Flow meetings Championed process improvement, corrective action, cost reduction and error-proofing activities Recommended PM procedures and frequencies Assisted in determining capital equipment/tooling necessary to provide manufacturing capacity and developed short and long term budgets accordingly Traveled to various suppliers and manufacturers sites as necessary to achieve plant objectives and to evaluate their proposed equipment Supervised as many as 30 production associates on a fill in basis Show less
-
-
Education
-
Lansbridge University
MBA -
Athabasca University
B. Admin, Business Administration and Management, General -
Sheridan College
Technologist, Mechanical Engineering
Community
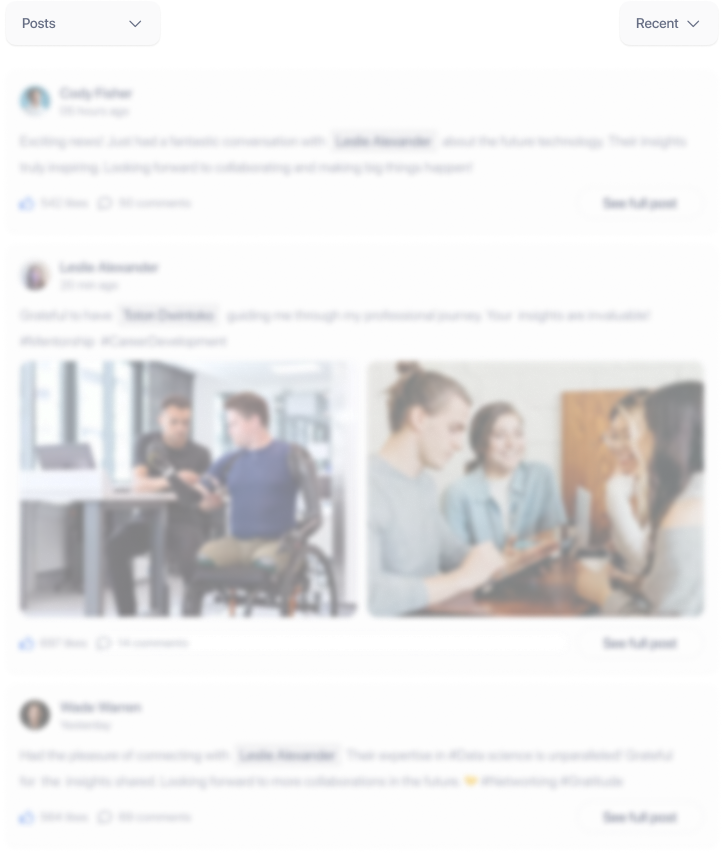