Thuy Ngo
Product Engineer at EPM Global Services- Claim this Profile
Click to upgrade to our gold package
for the full feature experience.
Topline Score
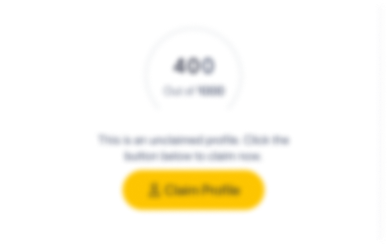
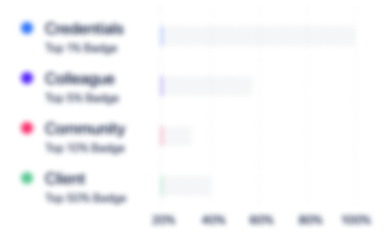
Bio


Experience
-
Vexos Markham
-
Canada
-
Appliances, Electrical, and Electronics Manufacturing
-
1 - 100 Employee
-
Product Engineer
-
Feb 2011 - Present
.Product Engineer for prototype and production build. •Prepared manufacturing work instructions, completed build reports and communicated with suppliers and customers to solve technical issues . •Worked with manufacturing operation team to drive continues improvement activities. .Product Engineer for prototype and production build. •Prepared manufacturing work instructions, completed build reports and communicated with suppliers and customers to solve technical issues . •Worked with manufacturing operation team to drive continues improvement activities.
-
-
-
Celestica
-
Canada
-
Manufacturing
-
700 & Above Employee
-
Manufacturing and Process Engineer
-
Oct 2005 - Mar 2010
Manufacturing and process engineer for prototype and production builds. • Defined strategic plans for managing product data. • Performed diagnosis and troubleshooting on SMT machines such as Siemens X-series, Siemens S-25, GSM and Camalot XyflexPro. • Prepared manufacturing work instructions, completed build reports and communicated with suppliers and customers to solve technical issues. • Identified and implemented solutions to address product defects. • Implemented technical changes or enhancements to existing equipment processes, products or continuous improvement initiatives. • Achieved 20% reduction in downtime and 50% reduction in knocked-off component defects. • Improved process control for Stomper product using PFMEA. 50% improvement for tester error defects and 50% improvement to production cycle time. • Reduced SMT Product Changeover with different Chemistry from 110min to 40min for SMED. • Reduced Quick SMT Changeover from 60min to 15min for Juniper. • Increased throughput 240% from 2500 to 6000/week by applying lean concepts to cell design. • Setup new process flow, manufacturing work instruction and labels for RMA. • Reduced programming and debug time with processes to check the orientation of parts offline. • Developed thermal shield oven fixture resulting in $345,000 savings on 20,000 cards.
-
-
Education
-
University of Toronto
Bsc, Mathematic
Community
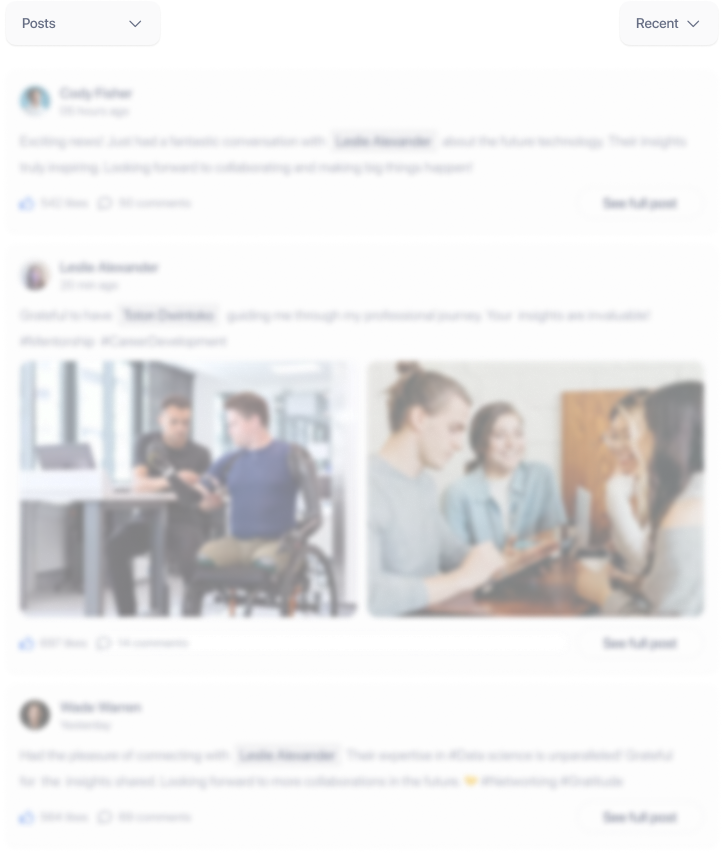