Thomas Milam
Manufacturing Engineer / Supervisor at Boehringer Laboratories, LLC- Claim this Profile
Click to upgrade to our gold package
for the full feature experience.
Topline Score
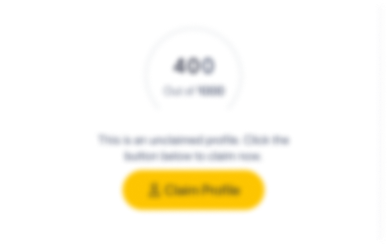
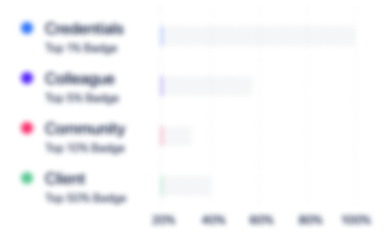
Bio

Christopher Loman
Thomas "TJ" Milam is an accomplished leader who helped me adapt to the Swagelok culture. He is a leader in work ethic, Lean manufacturing principals, communication at all levels, and collaboration. His always positive attitude brings a great atmosphere to everyone he leads. TJ is also very accomplished at balancing culture, associate understanding, and business capabilities. His ability to develop associates and other leaders is second to none as well. He is always willing to take on any challenge and take ownership of his performance whether good or underperforming.

Christopher Loman
Thomas "TJ" Milam is an accomplished leader who helped me adapt to the Swagelok culture. He is a leader in work ethic, Lean manufacturing principals, communication at all levels, and collaboration. His always positive attitude brings a great atmosphere to everyone he leads. TJ is also very accomplished at balancing culture, associate understanding, and business capabilities. His ability to develop associates and other leaders is second to none as well. He is always willing to take on any challenge and take ownership of his performance whether good or underperforming.

Christopher Loman
Thomas "TJ" Milam is an accomplished leader who helped me adapt to the Swagelok culture. He is a leader in work ethic, Lean manufacturing principals, communication at all levels, and collaboration. His always positive attitude brings a great atmosphere to everyone he leads. TJ is also very accomplished at balancing culture, associate understanding, and business capabilities. His ability to develop associates and other leaders is second to none as well. He is always willing to take on any challenge and take ownership of his performance whether good or underperforming.

Christopher Loman
Thomas "TJ" Milam is an accomplished leader who helped me adapt to the Swagelok culture. He is a leader in work ethic, Lean manufacturing principals, communication at all levels, and collaboration. His always positive attitude brings a great atmosphere to everyone he leads. TJ is also very accomplished at balancing culture, associate understanding, and business capabilities. His ability to develop associates and other leaders is second to none as well. He is always willing to take on any challenge and take ownership of his performance whether good or underperforming.

Experience
-
Boehringer Laboratories, LLC
-
United States
-
Medical Equipment Manufacturing
-
1 - 100 Employee
-
Manufacturing Engineer / Supervisor
-
May 2023 - Present
I began leading a team of 12 associates manufacturing medical devices through a period of significant growth of the organization. During my tenure, the company has never placed a product on backorder. My primary focus has been improving the department's training curriculum to enable rapid strategic scaling as market demand makes necessary. Through minor retooling of standard operating procedure documents and an emphasis on the first day experience, our team has welcomed four new associates aboard, with a 75% retention rate. Show less
-
-
-
Swagelok
-
United States
-
Industrial Machinery Manufacturing
-
700 & Above Employee
-
Production Supervisor
-
Sep 2021 - Aug 2023
I led a team of 40+ CNC machinists through the busiest year in company history. Through significant effort, my team's average monthly production increased by 15% from the beginning of my tenure to present operating conditions. This was achieved through several means:- Onboarded 13 CNC operators into a department with a high skill requirement, producing an retention rate of 70%. Intentional and strategic training curricula were developed to help new associates accelerate their development.- Extreme engagement with the shop floor. I relocated my work station from an office to a mobile desk on wheels so that I could be a consistent presence on the shop floor, and spend my time ensuring my team has what it needs to succeed. I held myself accountable to touch base with every member of my team once per hour, every hour, each shift.- People-focused servant leadership. I made morale a focal point of my leadership cadence, hosting cookouts, potlucks, gift exchanges, super bowl parties, etc. I found that breaking bread and enjoying togetherness was an important ingredient to my team's teamliness.- Driving accountability. I reviewed individual's performance each day to identify gaps in performance and prioritized crucial conversations with struggling associates, identifying early where we needed to "right the ship".- Analysis of department-level data. I reviewed big-picture trends in departmental performance on a weekly cadence. Through this practice, I identified and pursued a few machine-related issues that significantly impacted performance, and identified and amplified best practices from areas of the department where we were consistently winning.- Created a supplemental scheduling tool to identify where pieces of equipment were relative to their schedule, and implemented it department-wide so the most critical machines were run as necessary. This allowed us to avoid disappointing customers by shipping orders later than promised. Show less
-
-
Manufacturing Engineer
-
Jan 2021 - Sep 2021
I aggressively pursued improvements in operational efficiency, attempting to improve the bottom line of business financials through process improvements. Through strategic implementation of a cold saw to create part blanks, and a few tweaks to the sequence with which parts are manufactured, my efforts drove a $100,000 reduction in cost of goods sold per annum. Additionally, I helped facilitate the manufacture of a new valve component, creating the associated quality documents and overseeing the manufacture of validation manufacturing runs, creating a future value stream for the company. Show less
-
-
Quality Assurance Engineer
-
Feb 2020 - Jan 2021
I created tools to enable the organization to quickly identify quality concerns or weaknesses, and improve upon them. Utilizing Microsoft Power BI and Excel, I created a Quality Notifications dashboard that made vital metrics visible to anyone in the organization in a few seconds. With a few clicks, anyone could view historical performance, current status, and future targets vs. projected performance. In less than one year, the frequency of Quality Notifications decreased by more than 10%. This reduced the total cost of quality of this facility by $120,000 per year. Show less
-
-
-
Swagelok
-
United States
-
Industrial Machinery Manufacturing
-
700 & Above Employee
-
Mechanical Engineering Intern
-
May 2018 - Aug 2018
I worked among Manufacturing Engineers within Swagelok's Valve Service Group on several continuous improvement projects. The focus of my experience was on decreasing internal costs, and drastically shortening lead times. My contributions included: -Designing reamers for common needle valve bodies. Machining cycle time was reduced by 3 minutes, resulting in an annual savings of $30,000 per year at current volume. Additionally, the reamers enable the company to uphold a higher standard of quality than it was previously capable of. -Laying out component maps of parts that are Made To Order to customer specification. I designed several component maps so that every component that could possibly go into these customizable parts was represented on a single sheet of paper. After populating it with supply chain data, we were able to identify weaknesses in our supply chain, and shorten lead times from an average of 20 weeks to 8 weeks. Show less
-
-
-
ALACRIANT, INC.
-
United States
-
Mechanical Or Industrial Engineering
-
1 - 100 Employee
-
Project Manager
-
May 2017 - Aug 2017
I organized the new product launch team within the engineering department of Alacriant, a precision metal fabricator that specializes in laser cutting, forming and robotic welding. I modeled timelines for all product launch projects, and set our team up for success by prioritizing tasks in a manner that lead to a successful and punctual product launch. My contributions included: -Building an interface within Microsoft Project using Visual Basics to create and track the status of the launch, manufacture, and delivery or all new parts -Interacting with top level management, the engineering team, and machine operators to prevent failure modes rather than react to them -Improved and documented the flow of information on new product launch process to eliminate wasted time, increasing the internal lead time of the company by an average of two days, and eliminating several hundred hours of engineering resources by eliminating the double handling of information -Coordinated the design, build, and modification of forming tools between the primary manufacturing plant and the affiliated tool room in Cuyahoga Heights in order to best suit business demands -Engineered a work cell to create a brush guard, and created fixturing to increase precision and decrease cycle time for assembly of parts Show less
-
-
-
GE Aerospace
-
United States
-
Aviation and Aerospace Component Manufacturing
-
700 & Above Employee
-
Co-op
-
Aug 2016 - Dec 2016
I worked among a team of financial analysts to properly monitor the services and invoicing of the services division of GE Aviation. My primary assignment was to design a tool to find holes in our billing system to that we could properly invoice the customer. The resulting system identified $150 million in services that were not documented as having been invoiced during the 2015 calendar year. This system is capable of being populated with fresh data each year new financial information is released, and will serve GE Aviation Services for several years. Show less
-
-
-
Medina Heating and Air Conditioning Co.
-
United States
-
Installer/Serviceman
-
May 2015 - Aug 2015
I was a member of a dynamic team of technicians who installed and serviced air conditioners and heat pumps in both residential and commercial settings. I was a member of a dynamic team of technicians who installed and serviced air conditioners and heat pumps in both residential and commercial settings.
-
-
Education
-
The Ohio State University
Mechanical Engineering -
Medina High School
Diploma
Community
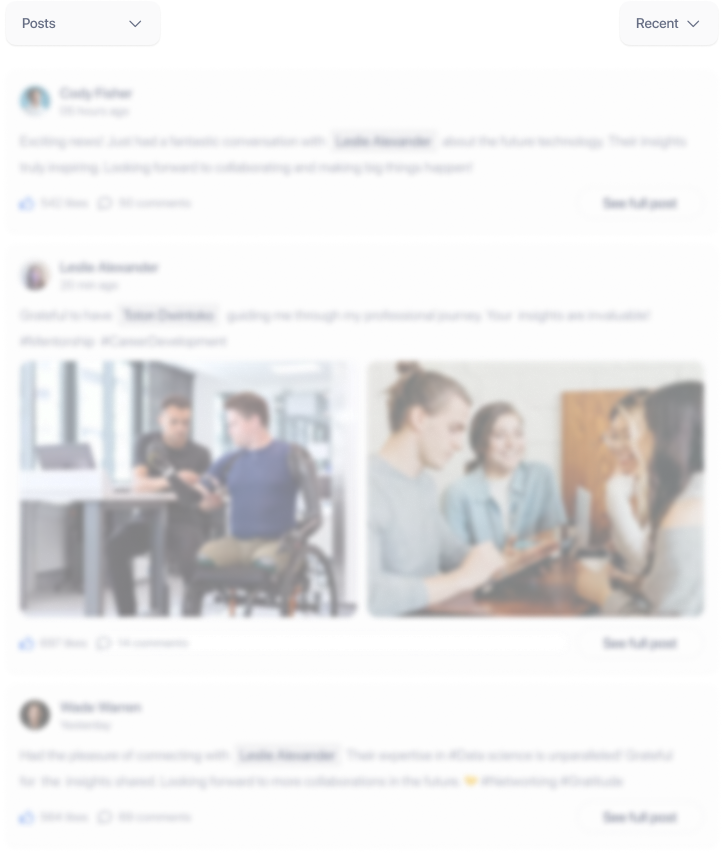