Thomas Dorris
GM and Operational Controller Northport Operations at Eberspächer North America, Inc.- Claim this Profile
Click to upgrade to our gold package
for the full feature experience.
Topline Score
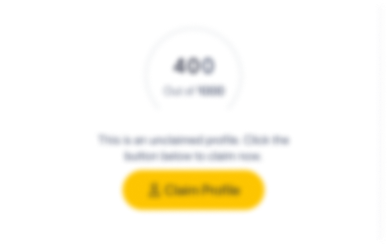
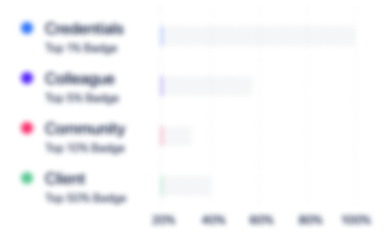
Bio


Experience
-
Eberspächer North America, Inc.
-
United States
-
Motor Vehicle Manufacturing
-
1 - 100 Employee
-
GM and Operational Controller Northport Operations
-
Nov 2020 - Present
-
-
GM and Operational Controller - Spartanburg & Northport
-
Jan 2020 - Oct 2020
-
-
Plant Manager and Operational Controller
-
Nov 2017 - Dec 2019
Responsible for managing Tier I Northport Sequencing Plant (IATF 16949 ISO 9001 Certified) Operations and Financial activities with 400 plus employees including Engineering, Production, Logistics, & IT during MB Series Production.• Orchestrated the full recovery (ENA’s Flag Ship Operation for the last four years) by improving operational profitability (~150%) with significantly improving operational communications (Daily Top Leadership & PC&L meetings, Scrap walks, etc.), revised & creating new KPIs, while coaching an highly talented & result driven leadership team.• Successfully managed the plant wide ramp up from 85% to 150% production capacity for six consecutive months (24/7) during MB New Model Changeover. • Zero Recordable Accidents in the last four years• Improved OEE from 50% to 95% within one year• Reduced scrap costs from 6% plus to 1/2% • Reduced Perpetual inventory by ~$6M (~45%) while significantly improving inventory accuracy Show less
-
-
Operational Controller
-
Oct 2016 - Nov 2017
-
-
-
Tarkett NA
-
Florence, Alabama Area
-
Director of Finance
-
Oct 2015 - Oct 2016
Responsible for overseeing the accounting operations at two plant operations, with total ten employees, on monitoring and maintaining financial, inventory, and cost accounting systems. Prepared weekly & monthly forecasts and annual profit plans. Daily interacted with all levels of management on financial decision-making issues, new product developments, cost improvements (Toyota Production/Six SIGMA) and major capital expenditure projections while being liaison for internal & external audits. • Orchestrated the resolution of $2.6M Inventory Accountability issue at Florence West • Orchestrated the development and implementation of new automated inventory scanning and consolidation processes which significantly reduced transactional errors and plant wide physical inventories from 4 plus days to 1 day. • Orchestrated the reduction of monthly closing cycle from 5 days to 3 days while improving timely EBITDA reporting Show less
-
-
-
Carl Star Group (Formerly Carlisle Corporation - CTP Division)
-
Jackson, Tennessee Area
-
Plant Controller
-
Aug 2012 - Oct 2015
Responsible for supervising three staff members with monthly closings and briefing management on monthly financial results (e.g. pricing & profit margins, production variances, etc.). Supervised the monitoring, maintaining, and revising financial, inventory and cost accounting systems. Prepared weekly & monthly forecasts and annual profit plans. Supervised cost accounting and inventory activities coupled with being liaison for internal & external audits. Daily interacting with all levels of management on financial decision-making issues, new product developments, cost improvements (Lean/Six SIGMA), and major capital expenditure projections. • Orchestrated the one-year EBIT improvement (~110%) by significantly reducing Material, Scrap and Operational Overhead costs. • Orchestrated the analysis and resolution of $8.6M Inventory Accountability • Initiated the financial justification for backward integration of outsourced production materials into the Carlisle Transportation Division Operations (~$5.5M Annual Cost Savings) • Initiated the development and implementation of new automated inventory scanning process which significantly reduced transactional errors and plant wide physical inventories completion times from 2 plus days to less than 8 hours. • Supervised the seamless implementation of the financial models for a new JDE E1 ERP production system • Orchestrated the reduction of monthly closing cycle from 4 1/2 to 2 days while improving timely EBITDA reporting • Directly worked with the Jackson Leadership on receiving in the largest TVA cash incentive ~$225k from Jackson Energy Authority Show less
-
-
-
Rheem Manufacturing
-
United States
-
Consumer Goods
-
700 & Above Employee
-
Controller
-
Aug 2007 - Aug 2012
Directly responsible for supervising the successful financial recovery of Montgomery Operations. Supervised ten employees with monthly closings and summarizing/briefing management on monthly financial results (e.g. pricing & profit margins, production variances, etc.). Supervised the monitoring, maintaining, and revising financial, inventory, and cost accounting systems. Prepared monthly forecasts and annual & five-year profit plans. • Orchestrated significantly improved contribution margins by $25M within five years • Orchestrated the reduction of monthly closing cycle from ten to four days, coupled with preparing flash EBITDA results on the second closing day, while implementing new Oracle ERP Financial system. • Orchestrated the successful implementation of new Oracle ERP financial system which significantly improved financial visibility and operational efficiencies. • Orchestrated the development and implementation of improved inventory controls which significantly reduced transactional errors and eliminated the necessity for costly quarterly physical inventories ($300k plus cost savings) Show less
-
-
Education
-
Rider University
Bachelor of Science, Accounting
Community
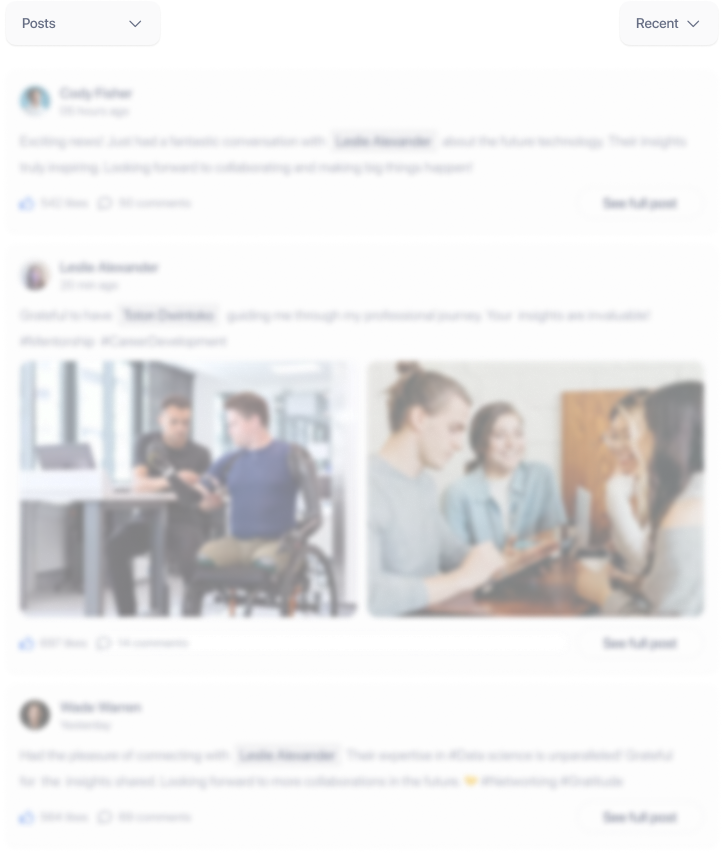