Therapon Pongpiachan
Regional Continuous Improvement Manager at Darigold- Claim this Profile
Click to upgrade to our gold package
for the full feature experience.
Topline Score
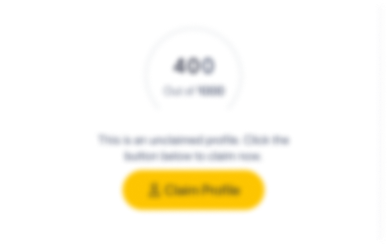
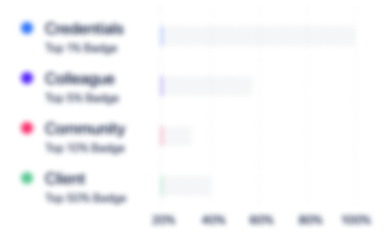
Bio


Credentials
-
ISO 22000 Foundation - Food Safety Certification
LRQAAug, 2022- Nov, 2024 -
Lean Six Sigma Black Belt (ICBB)
Lean Six Sigma Institute LATAMJul, 2022- Nov, 2024 -
Six Sigma Green Belt (CSSGB)
SimplilearnJan, 2015- Nov, 2024 -
Statistical Quality Control
Northwest AnalyticsJan, 2014- Nov, 2024 -
Certified HACCP Auditor (CHA)
ASQ - World HeadquartersJan, 2011- Nov, 2024 -
Certified Trainer
TWI Institute HeadquartersJan, 2010- Nov, 2024
Experience
-
Darigold
-
United States
-
Food & Beverages
-
700 & Above Employee
-
Regional Continuous Improvement Manager
-
2022 - Present
• Multi-plant support as a subject matter expert (SME) to build TPM/WCM/ Lean capability. • Leads and facilitates in Lean adoption and methodology effectiveness. • Leads improvement project teams for Supply Chain and Operations strategic loss reduction/value enhancement projects. • Responsible for evaluating and coaching supply chain and multi-site TPM/WCM/ Lean adoption and the monitoring key performance indicators. • Trains and mentors local CI managers and staff as well as select corporate functional groups. Show less
-
-
-
Ajinomoto Foods North America, Inc.
-
United States
-
Food and Beverage Manufacturing
-
300 - 400 Employee
-
Continuous Improvement Manager
-
2020 - 2022
• Standardizes measurement metrics for the plant to include KPI's, OEE, Maintenance, Sanitation, Warehouse, Material management, and other operational functions. • Delivers measurable cost savings, tangible quality/safety/environmental/sustainable improvements to the plant. • Develop and manage an operating plan to meet or exceed business unit objectives. Determine strategies and tactics for achieving financial objectives, presenting assumptions and recommending objectives. Make sound business projections, identify the impact of budgetary assumption changes, and make appropriate adjustments. • Direct operational efforts in the most efficient manner possible for our sustainable resources and by appropriate utilization of equipment and personnel. • Strive to continuously improve operations with respect to best practices for productivity, food quality, worker safety, inventory levels and management of operating expenses. Show less
-
-
-
USAA
-
United States
-
Financial Services
-
700 & Above Employee
-
Process Engineer
-
2017 - 2019
• Acquires and applies proficient knowledge of the process engineering discipline. • Leads and facilitates cross-functional, collaborative teams in business improvement and development initiatives using PP&E standards and guidelines to optimize the overall efficiency and effectiveness of the process. • Utilizes board knowledge of customers, products, processes to support business problem analysis and determine the best methodology to resolve defect or issue. • Conducts basic statistical analysis and drives improvement efforts based on analysis. • Analyzes processes to identify areas of improvement and provide appropriate analytics to facilitate business effort prioritization. • Serves as resources to less experienced team members on escalated issues of routine nature. Resolves issues and navigates obstacles to deliver work product. Show less
-
-
-
C.H. Guenther & Son
-
United States
-
Food and Beverage Manufacturing
-
400 - 500 Employee
-
Continuous Improvement Leader (CIL)
-
2012 - 2017
• Monitors productivity by obtaining hourly updates from production team members and mix technicians; walking the floor, attended operator meetings, and review operator and Modicon summary report. • Conducted ongoing audits of packaging lines’ status versus manufacturer recommended baselines, leading to revision of Standard Operating Procedures. • Lead special project teams using DMAIC to analyze current processes, recommend improvements, prepare Capital Expense Requests, coordinate implementation, and measure and track success. • Lead cross-functional team to determine root cause of SAP errors, change production processes to match SAP needs, prepare documentation, and train employees to eliminate error. • Compiled data for tracking of KPI’s, capacity planning, OSCOT and other performance metrics. Show less
-
-
-
H-E-B
-
United States
-
Retail
-
700 & Above Employee
-
Continuous Improvement Coordinator
-
2004 - 2012
• Collected, complied, analyzed, and prepared documentations/presentations to leaderships in order to brief the overall status of facility’s program. • Monitored TWI process and advised Plant Leadership on course of action. • Evaluated results and obstacles and created work tools to support improvement plan execution. Worked with Manufacturing Management to plan and deliver changes to KPI targets. • Created standard work as basis for continuous improvement. Tracked and reported team progress – taught teams how to use the metrics. • Developed processes and systems to ensure sustainability. Improved job methods by teaching employees to see waste. Show less
-
-
Education
-
Kettering University
Master of Science - MS, Lean Manufacturing -
University of Phoenix
Bachelor of Science - BS, Business Administration, Management and Operations
Community
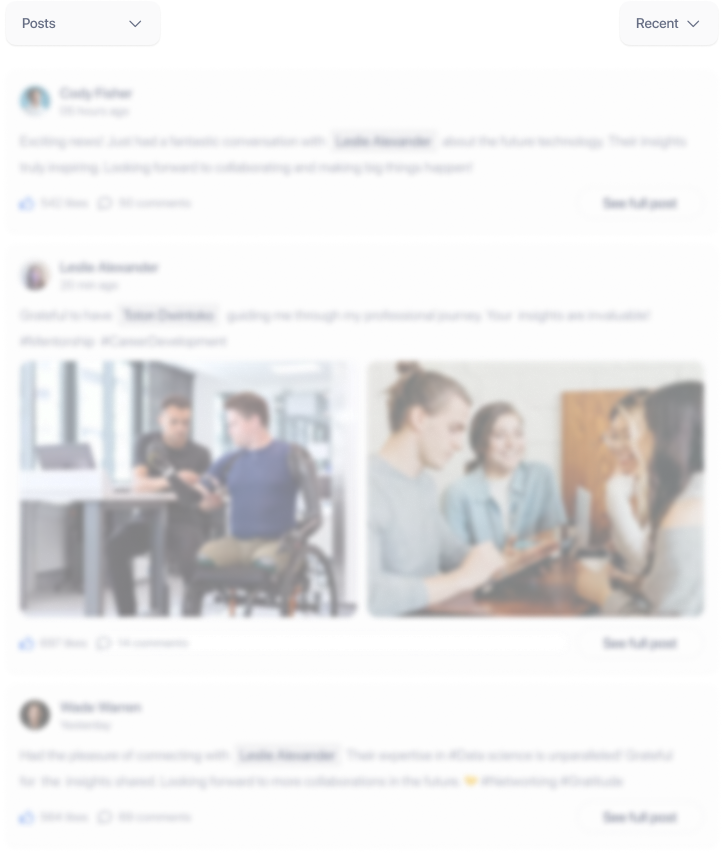