Thanakarn Buamas
Director Of Quality Dept. at T3 Technology Co.,Ltd- Claim this Profile
Click to upgrade to our gold package
for the full feature experience.
-
English Professional working proficiency
Topline Score
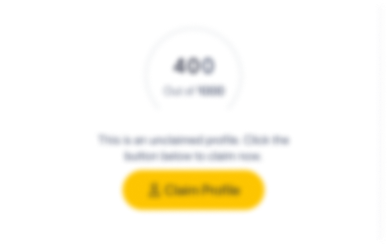
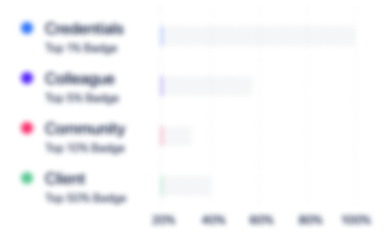
Bio

Duangkamol Jettanataikul
I had a chance to work with Thanakarn as a CQE and SQE in Electronics Company during 2009-2012. He is dependable, and incredibly hard-working. Beyond that, his knowledge of SQE, Six Sigma, Quality assurance, 8D were advantaged for both companies. Along with his undeniable talent, Thanakarn has always been an absolute joy to work with. He always manages to foster positive discussions in order to acheive the target of each project or able to solve all the problems.

Duangkamol Jettanataikul
I had a chance to work with Thanakarn as a CQE and SQE in Electronics Company during 2009-2012. He is dependable, and incredibly hard-working. Beyond that, his knowledge of SQE, Six Sigma, Quality assurance, 8D were advantaged for both companies. Along with his undeniable talent, Thanakarn has always been an absolute joy to work with. He always manages to foster positive discussions in order to acheive the target of each project or able to solve all the problems.

Duangkamol Jettanataikul
I had a chance to work with Thanakarn as a CQE and SQE in Electronics Company during 2009-2012. He is dependable, and incredibly hard-working. Beyond that, his knowledge of SQE, Six Sigma, Quality assurance, 8D were advantaged for both companies. Along with his undeniable talent, Thanakarn has always been an absolute joy to work with. He always manages to foster positive discussions in order to acheive the target of each project or able to solve all the problems.

Duangkamol Jettanataikul
I had a chance to work with Thanakarn as a CQE and SQE in Electronics Company during 2009-2012. He is dependable, and incredibly hard-working. Beyond that, his knowledge of SQE, Six Sigma, Quality assurance, 8D were advantaged for both companies. Along with his undeniable talent, Thanakarn has always been an absolute joy to work with. He always manages to foster positive discussions in order to acheive the target of each project or able to solve all the problems.

Credentials
-
Coaching Skills for Leaders and Managers
Linkin InSep, 2020- Oct, 2024 -
Building Trust
Lynda.comJun, 2019- Oct, 2024 -
Creative Thinking
Lynda.comJun, 2019- Oct, 2024 -
Disrupting Yourself
Lynda.comJun, 2019- Oct, 2024 -
Leading and Working in Teams
Lynda.comJun, 2019- Oct, 2024 -
Take a More Creative Approach to Problem-Solving
Lynda.comJun, 2019- Oct, 2024 -
Cultivating Mental Agility
Lynda.comJan, 2019- Oct, 2024 -
Leading without Formal Authority
Lynda.comMar, 2018- Oct, 2024 -
ISO9000
-
Experience
-
T3 Technology Co.,Ltd
-
Thailand
-
Telecommunications
-
1 - 100 Employee
-
Director Of Quality Dept.
-
Sep 2021 - Present
• Conduct Responsible for quality, repair and after sales & Service support of product from Customer feedback. • Conduct comprehensive reviews and audits to ensure all products exiting the NPI phase adhere to a stringent production release criterion prior to the ramp to sustaining production, including design for manufacturability input, BOM reviews, process/test development, and other activities to ensure supplier readiness to produce defect free products• Manage suppliers to comply with T3 and Customer quality management procedures, requirements and specifications• Use of excellent interpersonal skills to develop strong relationships with suppliers and internal stakeholders to influence proactive quality & improvements in the suppliers• Enforces the implementation QMS to compliance with all ISO standard, Customer requirements and regulatory standards.• Manages, prepares and coordinates for certification audit , MP audit ,customer audit, customer visit activities, supplier audit and ensures the appropriate corrective & preventive actions are taken effectively and timely manner.• Leads customer complaints investigation processes, identifies the root causes and ensures the appropriated corrective & preventive actions are taken effectively and timely manner. • Analyses trend of complaints based on root cause categories and leads team to minimize complaints. Ownership of all failure related RMAs back to the supplier, ensuring timely failure analysis (8D), true root cause, and permanent corrections actions are completed to contractual schedules• Conduct comprehensive reviews and audits to ensure Repair center based quality management systems enable timely problem resolution and proactive analysis of issues• Follow up the output from performance review meeting and ensures that evidence of improvement activities and corrective & preventive actions taken.• Generate quality metrics on supplier performance and establish measures to monitor quality risk & avoidance Show less
-
-
Operation/Quality Control Manager
-
Dec 2020 - Sep 2021
• Responsible for quality, repair and after sales & Service support of product from Customer feedback. • Conduct comprehensive reviews and audits to ensure all products exiting the NPI phase adhere to a stringent production release criterion prior to the ramp to sustaining production, including design for manufacturability input, BOM reviews, process/test development, and other activities to ensure supplier readiness to produce defect free products• Ensure suppliers to comply with T3 and Customer quality management procedures, requirements and specifications• Use of excellent interpersonal skills to develop strong relationships with suppliers and internal stakeholders to influence proactive quality & improvements in the suppliers• Enforces the implementation QMS to compliance with all ISO standard, Customer requirements and regulatory standards.• Manages, prepares and coordinates for certification audit , MP audit ,customer audit, customer visit activities, supplier audit and ensures the appropriate corrective & preventive actions are taken effectively and timely manner.• Leads customer complaints investigation processes, identifies the root causes and ensures the appropriated corrective & preventive actions are taken effectively and timely manner. • Analyses trend of complaints based on root cause categories and leads team to minimize complaints. Ownership of all failure related RMAs back to the supplier, ensuring timely failure analysis (8D), true root cause, and permanent corrections actions are completed to contractual schedules• Conduct comprehensive reviews and audits to ensure Repair center based quality management systems enable timely problem resolution and proactive analysis of issues• Follow up the output from performance review meeting and ensures that evidence of improvement activities and corrective & preventive actions taken.• Generate quality metrics on supplier performance and establish measures to monitor quality risk & avoidance Show less
-
-
-
Oracle
-
United States
-
Warehousing
-
1 - 100 Employee
-
Principal Supplier Engineer
-
Jan 2017 - Sep 2020
Responsible for technical, quality, and manufacturing/test process engineering support of outsourced embedded Power Supplies Conduct comprehensive reviews and audits to ensure all products exiting the NPI phase adhere to a stringent production release criteria prior to the ramp to sustaining production, including design for manufacturability input, BOM reviews, process/test development, and other activities to ensure supplier readiness to produce defect free products Ensure suppliers to comply with Oracle quality management procedures, requirements and specifications Provide product and component level technical leadership within the supply chain including quality and manufacturing related issues, problem analysis and resolution Use of excellent interpersonal skills to develop strong relationships with suppliers and internal stakeholders to influence proactive quality & process improvements in the suppliers Set, monitor, and proactively manage process and product quality goals and associated supplier compliance to those goals Define, analyze and present to management detailed quality performance metric reports throughout the supply chain and utilize the results to drive improvement initiatives Ownership of all failure related RMAs back to the supplier, ensuring timely failure analysis, root cause, and permanent corrections actions are completed to contractual schedules Conduct comprehensive reviews and audits to ensure supplier based quality management systems enable timely problem resolution and proactive analysis of issues Plan and execute regular supplier audits covering the entire manufacturing/test process and use results to drive continuous improvement Manage and drive increased supplier performance through regular supplier scorecards and participation in quarterly management reviews Collaborate with the Manufacturing and Quality engineers worldwide, in assessing and addressing supplier quality issues Show less
-
-
-
Seagate Technology
-
United States
-
Computer Hardware Manufacturing
-
700 & Above Employee
-
Sr.Supplier Quality Engineering
-
Jul 2007 - Oct 2016
• Lead Responsibility on Semi Asics component (Flip chip Preamp), PCC, PCCA both Thailand supplier and over sea supplier (China, Vietnam, Singapore) • Set up, maintain and monitor the effective Supplier and Receiving quality system. • Member QPM team for monitoring real time data SPC and feed back to supplier for improvement. • Responsible for documentation of supplier (PMP etc), First Article coordinator and process qualifications. • Provide inspection criteria to inspection group • Ensure the supplier corrective action & quality improvement program are implemented effectively on timely basis. • Follow up, Track all assignments and issues until satisfactory closure • Work with the HSA process team to establish component’s factory quality control methods and ensure on time delivery of quality parts. • Monitor and develop supplier quality performance, Component Process Development, Qualification and periodic \ Audits. • Evaluate supplier’s technical expertise and manufacturing process and capabilities. • Interface across functional groups, coordinating prototype and production build activities from product Staging through development, in preparation for high volume mass production. • In depth knowledge of supplier processes and cleanliness capabilities • Capable to perform Component and Assembly Failure Analysis. • Work internally with cross functional members in design, SQE, process, NPI, IQA, purchasing, commodity and externally with HSA material suppliers • Follow up CA and PA under 8D concept with member OSB for implement quality performance • Lead QQR, BPDC (Best Practice Deployment Checklist) activity working with Supplier for review board and closing Gap which potential concern quality issue. • QSR SS9 for ESD auditor compliance to ANSI/ESD S20.20 & IEC 61340-5-1 Show less
-
-
-
-
Sr.Quality Engineering
-
Jan 2006 - Jul 2007
• Head of Improvement Process and control Process under Quality manual • Reduce Lot reject and reply CAR from customer • DPPM from Customer by improvement under target 1000 DPPM • Improvement quality of products under six-sigma tool • Analysis root-cause and action for quality of product • Reduce complaint from our customer • Reduce waste of product not over 0.35% and control part scrap not over 2.8% • Analysis data from NPI at FA phase by follow up from customer requirement • Analysis part cleanliness and LPC (liquid particle count) for FA part • Evaluation part for reduce scrap and improvement • Control and observe part by use statistics tool for analysis • Control part by follow up SPC data • Design jig & Fixture for use to measurement part at IQA • Contact and support customer for customer audit to satisfied • Action and follow up issue complaint from customer • Owner Six-Sigma Project improvement Show less
-
-
-
Nidec Electronics
-
Germany
-
Software Development
-
Process Engineer
-
Jan 2004 - Jan 2006
• Improvement Process and control Process • Modify and analysis tear down process • Design Jig and fixture for support in line process • Control yield for productivity and Scarp for rework • Design Teardown Process for Evaluation • Design Quality Control Flow Chart for REWORK • Design Work Instruction for REWORK • Design, setup and maintenance machine for support rework process • Improvement Process Teardown for reuse part scrap • Control WIP scrap and amount All models • Improvement and consignment to supplier and Design process by under QCFC • Produce process diagram and procedure for Engineering Evaluation • Receive 8th from NETS Awards competition about EE reduce Scrap • Control yield washing parts before input to assembly in process • Maintenance machine washing for support parts • Computer support Group (CSG) by finding data skip and analysis data tracking before sent to customer Show less
-
-
-
Delta Electronics
-
Taiwan
-
Appliances, Electrical, and Electronics Manufacturing
-
700 & Above Employee
-
Design Engineer
-
May 2003 - Jan 2004
• Design and develop magnetic component for standard power supply, adaptor, monitor and television, which related to safety and UL's insulation system. • Select material and define cost analysis • Member in Advance Product Quality Planning team (APQP) to evaluate design and product feasibilities in pilot run stage. • Member in Problem Solving Team (PST) to analyze and improve production efficiency and capacity. • Contact customer to clarify customer spec or quality issue of prototype phase, confirms the prototype sample schedule and follows up the customer approval. • Prepare the engineering document for customer (PPAP, FMEA, control plan, design review) and document for mass production (production specification, Bill of Material) • Responsibility design Electronics part of Panasonic, Sharp, Sony and all Europe devices. Show less
-
-
Education
-
มหาวิทยาลัยรังสิต
Bachelor's Degree, Electrical, Electronic and Communications Engineering Technology/Technician -
มหาวิทยาลัยรามคำแหง
Master Degree, Engineering&inspection law
Community
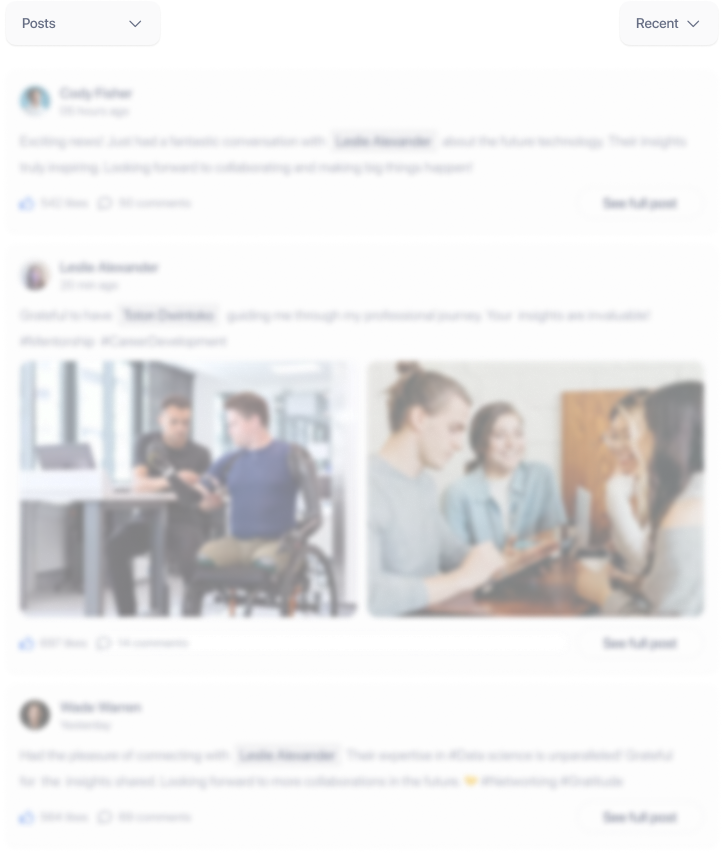