Thamsanqa Vincent Dube
Managing Director at Talic Investments Group (Pty) Ltd- Claim this Profile
Click to upgrade to our gold package
for the full feature experience.
-
Sotho, Southern Professional working proficiency
-
English Full professional proficiency
-
Zulu Native or bilingual proficiency
-
Portuguese Elementary proficiency
Topline Score
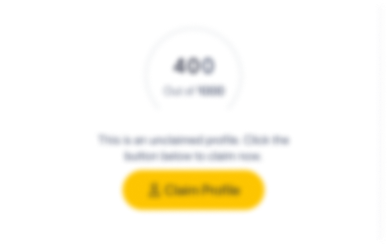
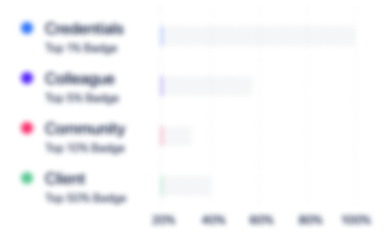
Bio

Prosper Rugube
Vincent is a great professional with good interpersonal skills. He is able to work in adhoc schedules and will do everything in his power to deliver results even with limited resources. I worked with Vincent on the Moatize Coal Project and he was able to provide quality assurance services on time and is a highly reliable individual.

Prosper Rugube
Vincent is a great professional with good interpersonal skills. He is able to work in adhoc schedules and will do everything in his power to deliver results even with limited resources. I worked with Vincent on the Moatize Coal Project and he was able to provide quality assurance services on time and is a highly reliable individual.

Prosper Rugube
Vincent is a great professional with good interpersonal skills. He is able to work in adhoc schedules and will do everything in his power to deliver results even with limited resources. I worked with Vincent on the Moatize Coal Project and he was able to provide quality assurance services on time and is a highly reliable individual.

Prosper Rugube
Vincent is a great professional with good interpersonal skills. He is able to work in adhoc schedules and will do everything in his power to deliver results even with limited resources. I worked with Vincent on the Moatize Coal Project and he was able to provide quality assurance services on time and is a highly reliable individual.

Experience
-
Talic Investments Group (Pty) Ltd
-
South Africa
-
Mining
-
1 - 100 Employee
-
Managing Director
-
Aug 2014 - Present
Responsible for development of high-quality business strategies and plans that will align with our business objectives including; Preparation of proposals and other business development initiatives. Actively engaging with clients to understand their requirements. Designing of mineral processing plants and developing solutions in all areas of the mineral processing across various systems, unit operations and process equipment. Identifying, scoping and managing process test work (on site or laboratory based). Execution of all design calculations, design criteria, in the compilation and execution of equipment lists and calculations. Compiling operating cost estimates including estimation of consumables, labor, maintenance materials and power. Providing input to capital cost estimates. Preparing written project reports. Developing of integrated process and quality management methodology across all studies and executing projects, including commissioning and start up. Lead role in on site commissioning of new plant, equipment and process systems.
-
-
-
South African Bureau of Standards
-
South Africa
-
Government Administration
-
400 - 500 Employee
-
Technical Liaison Officer
-
Apr 2015 - Dec 2019
-
-
-
Intertek
-
United Kingdom
-
International Trade and Development
-
700 & Above Employee
-
Operations Manager
-
Jun 2013 - Oct 2013
Operations & Project Management - ensuring the smooth operation of any sampling and processing projects mainly within Vale and Tete region of Mozambique, project planning, Establishing of policies and procedures that align with the organization’s overall goals and objectives. Implementation of standards of performance, safety policies and procedures and review production and activity reports. SHEQ management – managing an integrated SHEQ policy and ensuring that our people, processes and procedures comply with all relevant legislatures including ISO 9001, ISO 17025, ISO 1400, ISO 18001. Management of quality systems such as LEAN, 5S and six sigma.Financial management - Development of financial budgets, compile financial statements and other information to ensure financial goals are achieved as well as reduction of operational costs and increase revenues. Client invoicing and accounts management.Process Management & control - improving processes efficiency and availability, design and implementation of sampling and sample preparation systems, continuous improvements. Ensuring availability of resources to perform all necessary work which also included inventory management, staff rooster and stock control.Maintenance Planning – Assist maintenance team in scheduling planned preventative maintenance for all equipment, machinery and vehicles, reduction of downtime within the processes. Ensuring that all necessary spares are adequate to prevent downtime of equipment. Logistics management - Ensuring that samples were freighted safely from Mozambique to other labs in South Africa and Australia, including sample packaging, packing & tracking.Coaching and training – Accessing staff competence and skills needs, development of training material and coaching.Human resource management - people management, select and hire new employees (senior/skilled employees) and assign responsibilities to the entire staff, conflict resolutions, payroll etc
-
-
Assistant Laboratory Manager
-
Jan 2011 - Jun 2013
Laboratory Management - To assist with the establishment of a Coal Laboratories in line with procedures and guidelines established by Intertek Quality Control - Apply international standards in establishment of laboratory practices and ongoing quality control procedures both analytical and administrative and obtain ISO accreditation. Carry out laboratory audits and produce audit reports with recommendationsProcess Management - Reviewing and implementing test methods, implementing new technology, investigating and resolving technical problems. Prioritizing the laboratory (sampling and process) workload. Sample and data management. Carry out laboratory audits and produce audit reports with recommendations. Maintain current knowledge of advances in laboratory technology.SHEQ management – managing an integrated SHEQ policy and ensuring that our people, processes and procedures comply with all relevant legislatures including ISO 9001, ISO 17025, ISO 1400, and ISO 18001. Management of quality systems such as LEAN, 5S and six sigma. Ensures proper safety precautions and procedures are followed for storage, use and disposal of chemicals, ensure compliance with current safety and environmental requirementsHuman Resource Management - Recruitment, training and evaluation of staff and provide technical expertise as required.Inventory Management - Maintain inventory of consumables and spare parts and ensures that adequate supplies and appropriate equipment are in stock to minimize production disruptions. Maintenance Planning – Assist maintenance team in scheduling planned preventative maintenance for all equipment, machinery and vehicles, reduction of downtime within the processes. Ensuring that all necessary spares are adequate to prevent downtime of equipment
-
-
-
Bureau Veritas Group
-
France
-
Environmental Services
-
700 & Above Employee
-
Process Superintendant
-
Jun 2010 - Jan 2011
Process Management - Planning, coordinating and managing day to day activities of a 70 personnel commercial coal laboratory (sample preparation section), Managing all the sample preparation processes and making sure the procedures are followed promptly. Developing, improvement and maintenance of SOPs Projects Analysis - Daily scoping of work and making sure instructions requirements are correctly understood throughout the process. Inventory management - Equipment, stock and consumables management Quality Control - Implementing quality control strategy for sample preparation department in line with overall laboratory strategy. Assisting SHEQ Manager in strategic accreditation processes, Assisting supervisors with the implementation of ISO 17025 and Providing training on quality and technical related matters and creating quality awareness at all staff levels
-
-
-
Mashala Resources Pty Ltd
-
Ermelo
-
Junior Engineer - Quality and Logistics
-
Jan 2010 - Jun 2010
SHEQ management - Comply with the relevant Legislation ( Mine Health and Safety Act, Labor Legislation and Company Policies and Procedures) Logistics – ROM: Controlling day to day logistic activities from Run-of mine stockpile to siding, coordinating and liaising with external stakeholders – Transnet, Eskom and other relevant stakeholders• Supervising the loading and dispatch of coal cargoes’ to our customers• Distributing daily work instructions and supervise the material handling team, Siding qualities control. Contractor Management - coordinating and liaising with the coal processing plant contractor and laboratory contractor to optimize yields and qualities• Logistics • coordinating and advising in disciplinary hearings Compiling and submitting required reports Process Control – Operation of a coal processing plant (DMS), control room monitoring, sampling, medium corrections. Yield monitoring, process optimization Process Management – data analysis and interpretation, process improvement, continuous improvement projects (organic efficiency, plant efficiency), ROM analysis, Washability curves, equipment performance monitoring, reagents management, water processing (thickener operation)
-
-
-
-
Trainee operator
-
Aug 2008 - Jan 2010
Effluent plant Operation and water treatment Day to day operation and optimization of the effluent plant Sampling and sample analysis Chemicals preparation Chemical Dosage control and usage to limit budget strains Data analysis and reports compilation, SCD maintenance and data analysis Management of a team of plant operators and planning of shifts Daily, weekly and monthly reports for the Operations manager Ordering of chemicals and consumables Team coaching (enabling teamwork) Treating water in the boilers
-
-
-
-
trainee Metallurgist
-
Jun 2007 - Aug 2008
• Day to day planning of plant operation and maintenance (two separate plants) • Plant operation • Plant/Process optimization (particle size distribution analysis on ROM, discard and product material, flow rate analysis, close monitoring of spiral, DMS cyclone, sieve bends, D&R screens etc.) • Resources management (water, coal, magnetite) • Management of the water purification system (thickener i.e. ensuring correct dosage of flocculants and lime) • Sampling as per lab schedules and sample analysis at the laboratory. • Product Quality control • Assessing plant performance and weekly reporting to the plant Manager • Ordering & management of consumable within budget limits • People management • Monitoring SHE integrated policies (indirectly) • Stockpile planning • Research works for the company on continual process (coal processing and handling) improvement
-
-
Education
-
University of Cape Town
Certificate, Operations Management -
Tsoelopele Leadership Academy
NQF Level 4, Finance for Non-Financial Managers -
Tsoelopele Leadership Academy
NQF Level 4, Fundamentals of Project Management -
Tshwane University of Technology
Bachelor of Technology (BTech), Metallurgy -
Tshwane University of Technology
National Diploma, Engineering: Metallurgy -
SABS Training Academy
Certificate, ISO 9001:2015 - Implementation & Auditing
Community
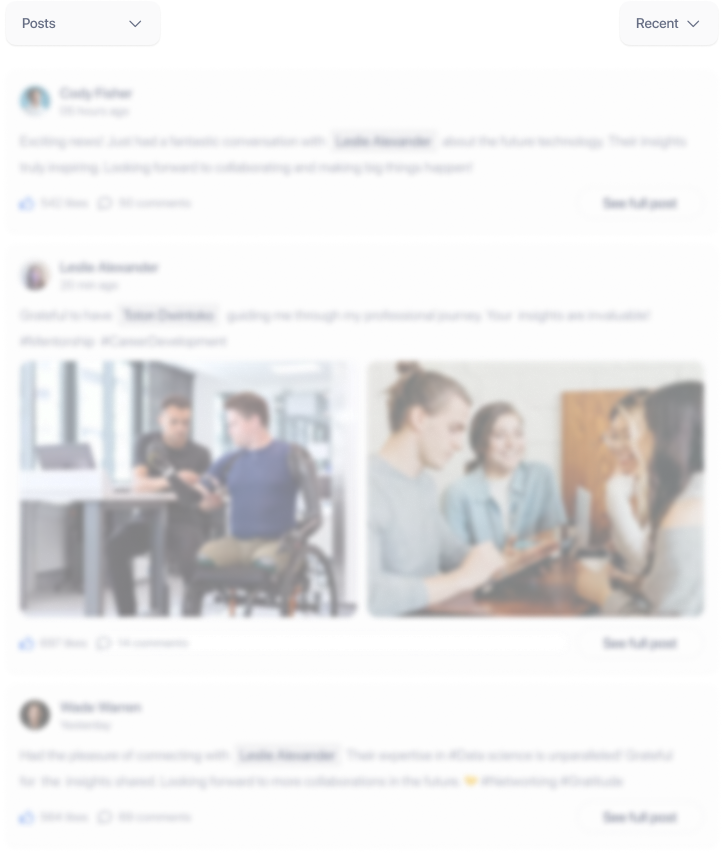