Thabisile Mathumbu
Systems Auditor at Nando's South Africa- Claim this Profile
Click to upgrade to our gold package
for the full feature experience.
Topline Score
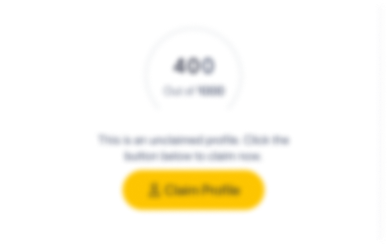
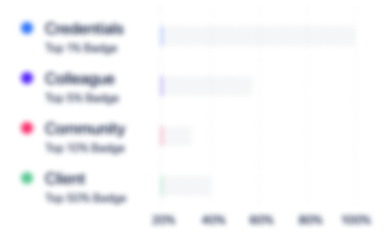
Bio


Experience
-
Nando's South Africa
-
South Africa
-
Restaurants
-
700 & Above Employee
-
Systems Auditor
-
Apr 2016 - Present
: Conduct Escudo Audits in all South Africa and applicable African casas. Ensure that audit reports are sent to casas within the stipulated time frame. Accurately report non-conformances and recommended corrective actions. Communicate audit scores that are below 60% and all high risk food safety conformances to relevant department heads. Participate and provide inputs to the continuous improvement of the Escudo Protocol. Conduct audit protocol trainings to relevant stakeholders. Provide support to the Supplier Quality Assurance by conducting product quality evaluation in the casas and provide reports Show less
-
-
-
Megga Candy
-
Johannesburg Area, South Africa
-
QA Manager
-
Jan 2014 - Oct 2014
Update/ implement/ Manage the Quality Management Systems HACCP/ISO22000 Manage 4 quality controllers and 8 hygienists Manage Cleaners, Hygiene and upkeep of the facility External Audits (PnP, Spar, Intertek/FSA) Conduct Internal Audits, Corrective Actions, Root Cause Analysis Conduct Supplier Audits/ Visits Investigate Customer Complaints Update Halaal Certificates/ Handle Halaal visits Trend Analysis on Production, Micro Training and Communicate Policies and procedures to Staff Updating or drawing up Product Specs/ MSDS/ COA’s Maintaining Raw material Specifications Maintaining/ updating documentation System according to Legislation Management Review Show less
-
-
-
Charlton Vos College
-
Pretoria Area, South Africa
-
Educator
-
Mar 2013 - Jan 2014
Lesson preparation and teaching Social Science and Technology Lead, administer, assess and manage learners. Lesson preparation and teaching Social Science and Technology Lead, administer, assess and manage learners.
-
-
-
QK Meats South Africa
-
Food and Beverage Manufacturing
-
1 - 100 Employee
-
Quality Manager
-
Sep 2012 - Feb 2013
Support, manage, coach Quality Assurance team and monitor performance goals. Ensure that product and processes meet customer specifications. Provide support for manufacturing operations to improve quality and productivity Conduct monthly audits to ensure hygienic engineering design on production equipments. Monitor GMP, Food Safety and Hygiene compliance through internal audits Conduct customer complaint investigations and give feedback to customers. Conduct organoleptic and shelflife product projects and compile product specifications. Prepare and participate in external audits, IBL, BRC, Pick n Pay and monthly Woolworths KPI’s Oversee projects and tasks in the Quality department related to production. Ensure Quality Assurance and Food Safety related training, work place competency and admin. Identify areas of improvement and participate in problem solving. Conduct R&D factory trials and compile and finalize product specifications. Show less
-
-
-
LSG Sky Chefs
-
Germany
-
Food and Beverage Manufacturing
-
700 & Above Employee
-
Supplier Auditor
-
Oct 2011 - Mar 2012
Supervise the hygiene and quality activities throughout the supply chain such that quality, hygiene and food safety services via the supply chain are rendered effectively and compliant with LSG Standards to the business. Maintain a Vendor Audit schedule that complies with LSG policy and procedures Ensure that the correct follow up procedures, including corrective actions are followed pertaining to audit failures. Ensure the availability and maintenance of specifications relevant to vendors Ensure high standard of advice and guidance to vendors to support the meeting of LSG required quality standards Ensure induction process to any new vendors supplying LSG Ensure correct recording of all vendor audits, action plans and corrective actions conformances Show less
-
-
-
Nestlé Professional ESAR
-
South Africa
-
Food and Beverage Services
-
1 - 100 Employee
-
Food Safety Specialist
-
Oct 2009 - Sep 2011
Consult Factory Supply Chain, Production, Engineering and QA in implementing and maintaining GMP, prerequisite program requirements (GMP – PRP) and Food Safety. Develop and implement training materials for use at site for improving the Food Safety Awareness on shop-floor level. Coordinate activities with Pest Control agency and ensure compliance of practices and continuous improvement. Preparation and follow up during the plant maintenance repair and upgrades Advise Factory Management on Food Safety Management issues. Audit and assess the level of implementation of the Food Safety Management System in factory. Assist selected suppliers in the implementation and assurance of Food Safety requirements. Investigate and raise CAR on Food Safety related Consumer Complaints Train and develop Operators and Team Leaders with respect to food safety Team Leader to the Food Safety and 5S Champion teams Show less
-
-
-
RCL FOODS
-
South Africa
-
Food and Beverage Manufacturing
-
700 & Above Employee
-
Quality Assurannce Technologist
-
Jan 2005 - Feb 2008
Managed Quality Controllers. Plant monitoring-maintaining good manufacturing practices (GMP’s), good hygiene practices (GHP) Analyzing production process and advising or recommending action Identifying training needs and development /executing relevant training programme as well as maintaining the Non Conformance programme Liaison with production management to ensure smooth processing flow and with maintenance team in terms of process breakdowns and preventative maintenance Demonstrate People Management Skills and discipline within the department Maintain company image, manage performance and involved in decision making within the department Maintain workmanship and product quality Sampling product for chemical and Microbiological analysis Plant, personnel hygiene survey (micro swab sampling) and report writing which includes compliance evaluation Quality analysis on all products – from received goods which includes raw meat, powders, spices and packaging material to finished frozen and ready to eat (RTE) products Monitoring and reporting on raw material and new product development trials Trouble shooting for Research and Development team via QA Manager Comply weekly KFC reports with Head Office Verifying the validity of the HACCP studies Identifying short comings with regards to procedure, work instructions and records CCP identification and awareness training to all staff in relevant areas Ensures a high standard of security measurements, practices and procedures with regards to HACCP- ISO 22 000-2005 (CCP monitoring throughout the plant) and Star Audits. Show less
-
-
-
Bromor Foods
-
Durban Area, South Africa
-
Quality Control Technician
-
Aug 2002 - Dec 2004
Microbiology – media preparation, sampling analysis and Quality analysis (acid, brix, sulphur dioxide, stability taste) Conformance on packaging and incoming raw Materials (liaison with different suppliers) Online quality checks (fill heights, packaging), Microbiological and quality auditing (address Non-conformances assist in HACCP implementation and maintain good laboratory practices) Capturing data (SAP, MS Word, MS Excel, MS Power point) Consumer complains (investigate and provide feedback to consumer services Process operations (manufacture of syrup and halls juices, conduct sanitation on water system and manufacturing tanks) Show less
-
-
Education
-
Durban University of Technology
National Diploma, Food Tchnology
Community
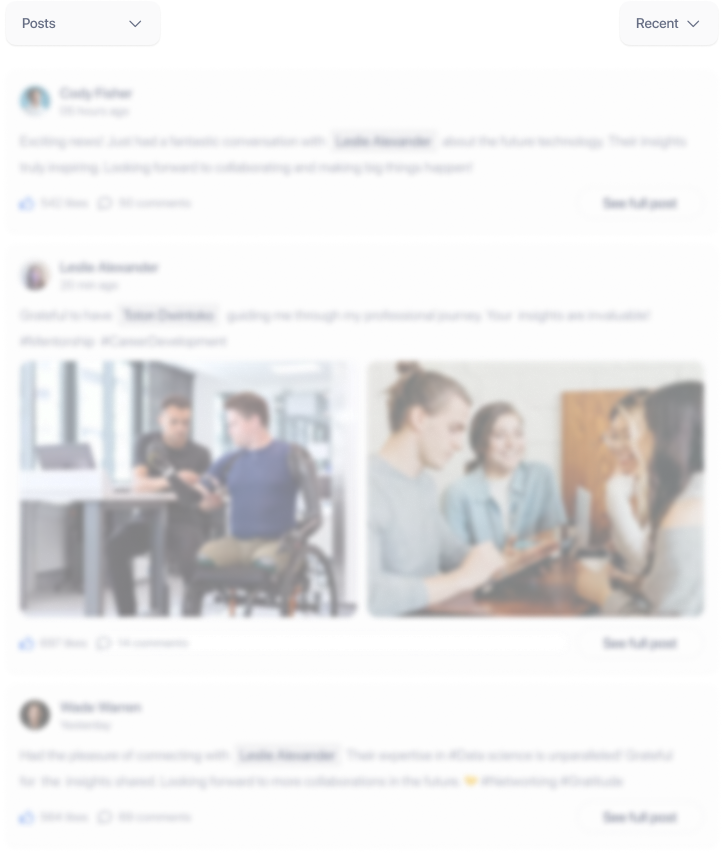