Terry Miller CHST
Corporate EHS Manager at Construction Solutions Group- Claim this Profile
Click to upgrade to our gold package
for the full feature experience.
Topline Score
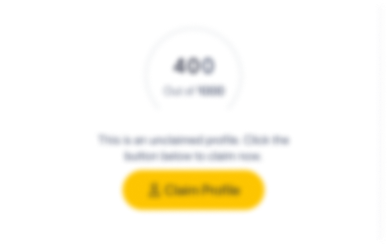
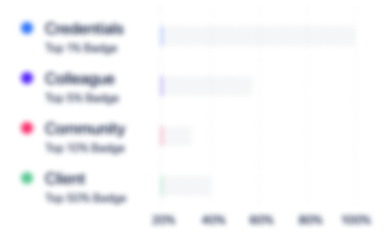
Bio
0
/5.0 / Based on 0 ratingsFilter reviews by:
Credentials
-
Certified Safety Manager (CSM)
National Association Of Safety ProfessionalsMay, 2019- Sep, 2024 -
Current TWIC
TWIC Transportation Worker Identification CredentialFeb, 2019- Sep, 2024 -
Certified Safety Director CSD
National Association Of Safety ProfessionalsJan, 2020- Sep, 2024 -
Licensed Safety Professional LSP
National Association Of Safety ProfessionalsJan, 2020- Sep, 2024 -
Safety Auditor Certification
NASPwebFeb, 2019- Sep, 2024 -
Construction Health and Safety Technician (CHST)
Board of Certified Safety ProfessionalsJun, 1999- Sep, 2024 -
CSST
Associated Builders and Contractors
Experience
-
Construction Solutions Group
-
United States
-
Construction
-
1 - 100 Employee
-
Corporate EHS Manager
-
Apr 2022 - Present
-
-
-
Covanta
-
United States
-
Environmental Services
-
700 & Above Employee
-
Regional Safety Manager, Covanta Field Services Group
-
Nov 2021 - Apr 2022
-
-
Tulsa Facility Program Safety Manger
-
Oct 2020 - Apr 2022
Facilitate the implementation of comprehensive safety improvement process (policies, procedures, processes) for the facility Provide safety guidance and direction to facility employees and Contractors Serve as a subject matter expert and technical adviser for safety functions at the facility Identify the needs, then lead the development and delivery of appropriate safety education/training programs and other services for Covanta Energy employees. Monitor, evaluate, analyze, track, and publicize the facility's safety performance; lead the safety continuous improvement efforts Provide safety leadership to plant safety teams Perform facility safety self-assessment/audits Complete and document Process Maps Near Misses and run reports for Management. Show less
-
-
-
Matrix Service Company
-
United States
-
Construction
-
400 - 500 Employee
-
HSE Due Diligence Advisor
-
Jan 2019 - Apr 2020
The HSE Due Diligence Advisor position is primarily responsible for coordinating and leading all Corporate SAFE/Score Assessments as well as follow-up assessments as needed in support of the company. This includes the revision and maintenance of the assessment process for all subsidiaries and Corporate, developing a corporate annual assessment schedule, coordinating participants as well as analyzing the results from the assessments and developing process improvements based on the trends of findings. Reports to the Corporate HSE Manager Essential Functions • Actively supports the Company’s commitment to safety and its “Core Values.” • Represents the Company at all times with high moral standards while adhering to the Company’s “Code of Business Conduct and Ethics.” • Perform assessments and follow-up assessments; this includes traveling to project sites away from the corporate office. • Analyze findings from assessments to assess frequencies of non-conformances, trends and root causes. • Ensure all findings and corrective actions are tracked. This includes identifying the responsible person(s) for completing the corrective action(s), the estimated completion date and close out dates. • Develop SAFE/SCORE assessments specific to the product line and business units as well as updating, revising and maintaining the corporate assessment process. • Assess and analyze all assessments by subsidiary companies in order to look for commonalities as well as the development of recommendations and action plans based on the totality of the data that has been collated. • Coordinate with each subsidiary company in assisting with their SAFE/Score assessment by coordinating schedules, collating information, and sharing findings throughout the Company. • Develop annual assessment schedule and coordinate with management and operations with regards to participants. Show less
-
-
-
-
Senior Safety Specialist
-
Jun 2018 - Jan 2019
Job responsibilities include, but are not limited to: - Develop and facilitate the implementation of comprehensive safety improvement process (policies, procedures, processes) for the facility - Provide safety guidance and direction to facility employees - Serve as a subject matter expert and technical adviser for safety functions at the facility - Identify the needs, then lead the development and delivery of appropriate safety education/training programs and other services for APCo employees at Gorgas - Monitor, evaluate, analyze, track, and publicize the facility's safety performance; lead the safety continuous improvement efforts - Provide safety leadership to plant safety teams - Perform facility safety self-assessment/audits - Occasionally support night and weekend safety related activities - Occasionally serve as an on-call person for the compliance department Show less
-
-
-
-
Project Safety Manager
-
Jun 2017 - Mar 2018
-
-
-
Sparstane LLC
-
Environmental Services
-
Environmental Health and Safety Manager
-
Jun 2016 - Apr 2017
• Identifying, managing, directing, developing, and auditing for continuous improvement the EH&S systems, procedures, and policies • Developing and implement training for all personnel to assure understanding of environmental, health, and safety programs • Establishing a culture that focuses on EH&S compliance as an overriding expectation for which everyone will be held accountable • Serving as a team leader to investigate and resolve complex EH&S issues and concerns • Managing regulatory agency inspections, inquiries, contacts, reporting in accordance with corporate and regulatory requirements • Communicating effectively to all levels from floor to corporate executives the progress and trends towards achieving excellence in EH&S compliance • Zero past due action items for all audits, investigations and action plans • Ensure facility is in compliance with EPA and OSHA regulations, Sparstane Corporate EH&S Standards and Guidelines • Establish and maintain site-specific Environmental, Safety, & Health procedures • Conduct an annual, internal Safety & Health assessment / audit • Maintain schedules of all safety and health activities including; inspections, reports, audits, etc. • Maintain monthly safety statistics and incidents • Maintain and provide PPE supplies for employees, contractors, vendors/visitors • Schedule or Conduct applicable safety and health training for all employees in a timely fashion • Maintain safety and health documentation Show less
-
-
-
FDR Safety
-
United States
-
Business Consulting and Services
-
1 - 100 Employee
-
Senior Site Safety Manager- Rep For Big River Steel
-
Nov 2015 - Jun 2016
Provide onsite safety consultation in accordance with all applicable policies and guidelines (OSHA, MSHA, Client, FDR Safety and Site Specific) throughout all phases of the project. KEY RESPONSIBILITIES: · Consulting and advising, safety in compliance with the Client’s requirements, OSHA regulations or MSHA regulations · Participate in meetings as directed by the client construction coordination meetings as mandated by the client instead · Provide consultation as they pertain to the customer, OSHA, MSHA and other applicable requirements. We will Advise and consult on JSA’s (job safety analysis) in detail at the task location · Attain detailed knowledge of all ES&H Guidelines and other contractual documents including the Pre-Bid Meeting Minutes · Assist in the delivery of any contract qualification process at the site level and confer with the customer corporate safety director as necessary to ensure that all contractors entering the site are qualified or otherwise approved · Prepare monthly injury illness and injury reports and maintain the same for auditing purposes as requested by the client · Review for compliance any and all permits as required · Monitor field activities at a very high frequency identifying high risk tasks and advise on violations to complete task safely · Complete Safety Audits at a frequency consistent with job hazards · Prepare documented safety data as directed by the client. · Coordinate and participate in incident investigation and analysis as directed by the client · Maintain a proactive approach to safety fostering a positive relationship with other site safety managers, craft workers and team members · Conduct and document routine safety observations, provide feedback (Positive and Negative alike) or coaching to all workers, based on observation findings Show less
-
-
-
Georgia-Pacific
-
United States
-
Paper and Forest Product Manufacturing
-
300 - 400 Employee
-
EHS Manager
-
Feb 2014 - Nov 2015
Provided leadership, coordination, and technical expertise to achieve excellence in the areas of environmental and health and safety. A vital part of the plant’s management team. Identifying, managing, directing, developing, and auditing for continuous improvement the EHS systems, procedures, and policies Developing and implement training for all personnel to assure understanding of environmental health and safety programs Establishing a culture that focuses on EHS compliance as an overriding expectation for which everyone will be held accountable Serving as a team leader to investigate and resolve complex EHS issues and concerns Managing regulatory agency inspections, inquiries, contacts, reporting in accordance with corporate and regulatory requirements Directing outside contractors / internal resources to obtain appropriate and timely permits Communicating effectively to all levels from floor to corporate executives the progress and trends towards achieving excellence in EHS compliance Assure all required testing is performed, reported and documented for POTW and storm water discharges, drinking water, waste characterization, etc. Perform compliance audits and resolve identified issues Perform “New Substance Review” on any new chemical brought on-site Maintain required and voluntary Plans including; SPCC (Spill Prevention & Counter Control), SWP3 (Storm water Pollution Prevention, Pollution Controls O&M (Operating and Maintenance) Coordinate disposal of all non-hazardous liquid and solid waste and universal and hazardous waste Respond to spills and releases Provide all required training to applicable personnel including; Oil and Hazardous Substance Spill Prevention, Control and Response, Storm Water Pollution Prevention, hazardous waste handling, and DOT. Report investigate and develop corrective actions to any identified issues and incidents Conduct a root cause analysis for all reportable environmental incidents Show less
-
-
-
Bluewater Energy Services
-
Netherlands
-
Oil and Gas
-
500 - 600 Employee
-
Safety Manager Rep for Dominion Energy
-
Sep 2013 - Nov 2013
Hopewell, VAReview and verification subcontractor safety plans and procedure to meet Dominion policy and OSHA standards including training of personnel and certification of operators Hold contractors and tier subcontractors accountable to the safety action plan and contractual requirements for safety.Coal Biomass Conversion Startup and Commissioning
-
-
Safety Manager Rep for Dominion Energy
-
Dec 2012 - Aug 2013
Review and verification subcontractor safety plans and procedure to meet Dominion policy and OSHA standards including training of personnel and certification of operators Hold contractors and tier subcontractors accountable to the safety action plan and contractual requirements for safety.DSI System to reduce sulfur dioxide (SO2) emissions at the Facility, utilizing Dry Sorbent Injection technology that includes dry sorbent unloading, storage, handling, and milling Systems, as well as dry sorbent feeding and injection systems (the “DSI System”) Existing precipitator hopper conveyance piping are required to upgrade the system’s capacity to handle additional particulate loading collected from the existing electrostatic precipitators with the additional loading of the dry sorbent(sodium bicarbonate)fly ash system modification will also include installation of new vacuum Blowers to account for the additional redundancy and capacity necessary to support the conveying pipe Modification. Show less
-
-
-
-
Safety Manager Rep Marsulex
-
May 2011 - Apr 2012
Review and verification subcontractor safety plans and procedure to meet MET and Owners policy and OSHA standards including training of personnel and certification of operators Hold contractors and tier subcontractors accountable to the safety action plan and contractual requirements for safety. Coal Fire Plant Fuel Gas Desulfurization (FDG) & Reagent Prep. System (RPS) Lime Prep for Absorbers Projects. Managed all contractors during construction activities all craft including silo erectors Union and Non-union Show less
-
-
-
Matrix
-
Wholesale Import and Export
-
1 - 100 Employee
-
Safety Manager
-
May 2010 - May 2011
Review and verification subcontractor safety plans and procedure to meet Matrix and Owners policy and OSHA standards including training of personnel and certification of operators Hold contractors and tier subcontractors accountable to the safety action plan and contractual requirements for safety. New construction of 5 Oil Storage Tanks from civil to testing with Matrix employees and contractors Review and verification subcontractor safety plans and procedure to meet Matrix and Owners policy and OSHA standards including training of personnel and certification of operators Hold contractors and tier subcontractors accountable to the safety action plan and contractual requirements for safety. New construction of 5 Oil Storage Tanks from civil to testing with Matrix employees and contractors
-
-
-
-
Safety Manager
-
Oct 2009 - Feb 2010
Multitrade Rabun Gap, GA and Telogia, FL ; Multitrade, LLC Safety Manager Reconstruction (Update) of Biomass Power Plant had been shut down for several years. Review and verification subcontractor safety plans and procedure to meet Multitrade policy and OSHA standards including training of personnel and certification of operators Hold contractors and tier subcontractors accountable to the safety action plan and contractual requirements for safety. Oversaw contractor safety, assist Multitrade in training of Multitrade Personnel and Bringing the Plant up to standards and code from ground up. Made safety assessments and recommendations, wrote safety manual and developed safety training. Show less
-
-
Education
-
National Association of Safety Professionals | NASP
Community
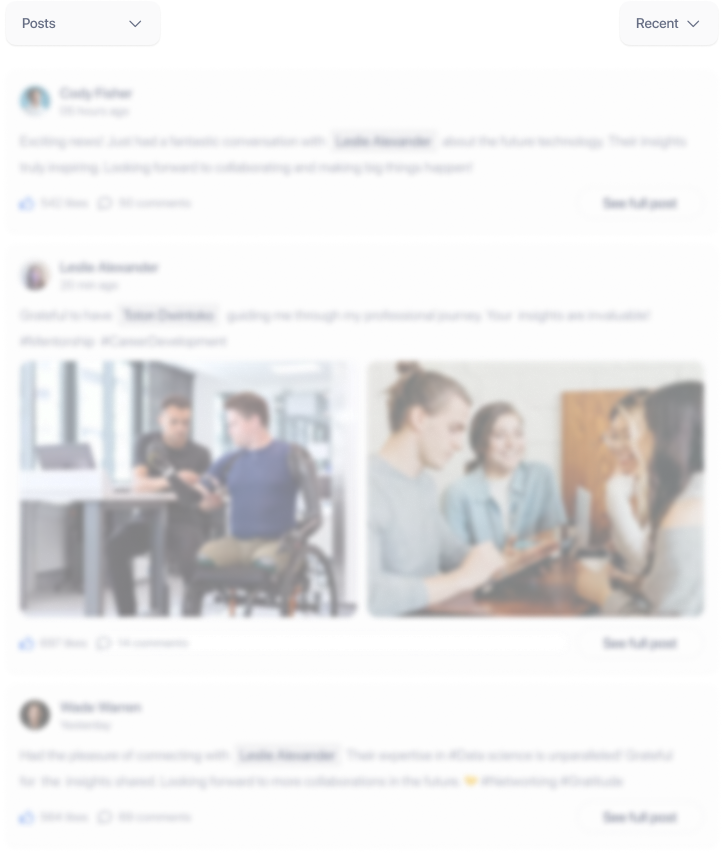