Ted Hajec
Plant General Manager at Salcomp Manufacturing USA- Claim this Profile
Click to upgrade to our gold package
for the full feature experience.
Topline Score
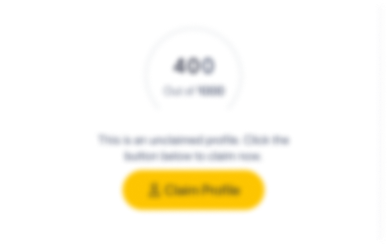
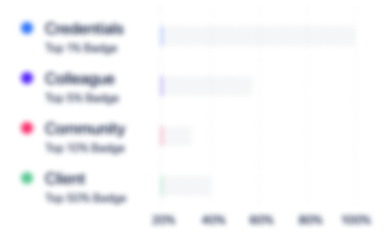
Bio


Experience
-
Salcomp Manufacturing USA
-
United States
-
Appliances, Electrical, and Electronics Manufacturing
-
1 - 100 Employee
-
Plant General Manager
-
Nov 2022 - Present
-
-
-
TT Electronics plc
-
United Kingdom
-
Appliances, Electrical, and Electronics Manufacturing
-
700 & Above Employee
-
Operations Director
-
Mar 2022 - Sep 2022
Managed Electronic Mfg, Engr and Facilities, to help complete the transfer from Corpus Christi to Plano, turning up production and producing qualification builds for all product families. Managed Electronic Mfg, Engr and Facilities, to help complete the transfer from Corpus Christi to Plano, turning up production and producing qualification builds for all product families.
-
-
-
Presto
-
Brazil
-
Graphic Design
-
Supply Chain Director
-
May 2021 - Oct 2021
Directed building a Repair facility in Carrollton, due to extensive product failures caused by COVID's excessive disinfecting of restaurant tablets. Directed building a Repair facility in Carrollton, due to extensive product failures caused by COVID's excessive disinfecting of restaurant tablets.
-
-
-
Motorola Solutions
-
Software Development
-
400 - 500 Employee
-
Director Business Operations ( Vice President Operations )
-
Jul 2019 - Aug 2020
Formerly WatchGuard Video - Executive Operations leadership and overall P&L profitability, S&OP planning, business goals and performance of the Production, Procurement, Quality engineering, Logistics, Shipping and Transportation, and all Manufacturing Operations, building the organization near the start-up beginnings. - Built business to annual revenue $100,000,000+, drive performance with expertise in Engineering and Lean and Continuous Improvements. - Oversaw construction and daily facility maintenance and OSHA compliance for 140,000 sq-ft complex. - Implemented GP (Great Plains) ERP planning software system, 6,000 part number system and forecasting to run the business, along with $13,000,000 inventory in warehouse and finished goods. - Defined KPI’s, weekly scorecards and metrics for the Supply chain and Operations departments. - Proficient using MS Office, with strong Excel skills.
-
-
-
WatchGuard Video
-
United States
-
Law Enforcement
-
1 - 100 Employee
-
Vice President Operations
-
May 2007 - Jul 2019
Motorola Solutions buyout in July 2019, therefore same roles and duties as above... - Built Manufacturing and Operations (Start-up) of In-Car Video Equipment and Body-worn cameras for Law Enforcement Agencies. Motorola Solutions buyout in July 2019, therefore same roles and duties as above... - Built Manufacturing and Operations (Start-up) of In-Car Video Equipment and Body-worn cameras for Law Enforcement Agencies.
-
-
-
Celestica
-
Canada
-
Manufacturing
-
700 & Above Employee
-
General Manager
-
Aug 2006 - Mar 2007
Responsible for the complete P&L and facility of a $100 million Fulfillment Contract Mfg business in Dallas, building and fulfilling every BlackBerry cell phone for the entire US market. • Responsible for Investment worth $6.5 million of inventory and finished goods in 88,000 sq ft warehouse/office. • Operations ranged from final assembly of annually 5 million Blackberries, reprocessing 100K Motorola phones, to hub RIM and SUN products via a 4 shift, 7-day operation, with over 260 production associates, and management. • Re-organized the entire facility from a Repair depot to a Fulfillment operation while doubling production capacity.
-
-
-
-
Director Operations
-
Nov 2005 - Aug 2006
Manufacturing of custom Servers - Responsible for the total manufacturing and logistics operations world-wide of a $100 million business. • Manage the Receiving and Warehousing departments of all incoming material and $14 million of inventory and $2 million in finished goods, and the Distribution and shipping of computer components worldwide. • Manage the manufacturing and production and worldwide shipping of over 10,000 computer servers annually. Manufacturing of custom Servers - Responsible for the total manufacturing and logistics operations world-wide of a $100 million business. • Manage the Receiving and Warehousing departments of all incoming material and $14 million of inventory and $2 million in finished goods, and the Distribution and shipping of computer components worldwide. • Manage the manufacturing and production and worldwide shipping of over 10,000 computer servers annually.
-
-
-
Tyco Electronics/Madison Cable, now TE Connectivity
-
Switzerland
-
Appliances, Electrical, and Electronics Manufacturing
-
1 - 100 Employee
-
Technical Consultant
-
Apr 2005 - Nov 2005
Consultant for Tyco Electronics Power Systems Manage product design information (PDI) process for Restriction of Hazardous Substances (RoHS) compliance on all old and new high tech power supply products being outsource manufactured in International facilities (Mexico, India, and China). Consultant for Tyco Electronics Power Systems Manage product design information (PDI) process for Restriction of Hazardous Substances (RoHS) compliance on all old and new high tech power supply products being outsource manufactured in International facilities (Mexico, India, and China).
-
-
-
-
Director Operations
-
Apr 2001 - Feb 2005
First employee hired (Start-up) to build the Operations department where our mission was to design and outsource manufacture a next generation optical transport system, targeting large telecommunications carriers and Fortune 100 enterprises. • Responsible for global supply chain strategy including the entire procurement of system hardware (circuit boards, electronic and optical components, mechanical assemblies) from outsourced CMs and vendors worldwide. • Implemented Oracle 11i Manufacturing, Inventory control, and Purchase Order ERP system, and installed and maintained Agile DBM tool • Hired and trained the entire highly effective cross-functional team for Operations Department (Engr/Purchasing Quality/Logistics/IT). • Managed New Product Introduction (NPI) process between designers and outsourced CMs and processed over 1300 Engr Change orders. • Managed Quality department and established initial ISO process, working towards ISO9000-2000 certification.
-
-
-
-
Engr and Mfg Technical Manager
-
Jun 1985 - Jan 2001
Performed many different engineering and Operations management manufacturing positions in high tech Telecommunications and electronic manufacturing and assembly facilities worldwide, Roles included - Engineering Technical Manager, Manufacturing Operations Manager, NPI Procurement/Material Engineer, Outsourcing Consultant for International Tech transfer mfg Assignment to Spain, Lead Project Process/Product Engineer/Shop Manager/Supervisor, Lead Product Engineer, Project Leader on NPI Flipchip / BGA Project, International Expatriate Engineer/Consultant - Korea, Lead SMT Process/Planning Engineer.
-
-
-
Boeing
-
United States
-
Aviation and Aerospace Component Manufacturing
-
1 - 100 Employee
-
Mechanical Engineering Intern
-
Sep 1982 - Sep 1984
Co-op Engr – Engineer for NPI product and process development and improvements in the re-production of Chinook Helicopters, converting from metal to polymer. Worked a total of 1 year over 2 terms (8 months, and then 4 months). Co-op Engr – Engineer for NPI product and process development and improvements in the re-production of Chinook Helicopters, converting from metal to polymer. Worked a total of 1 year over 2 terms (8 months, and then 4 months).
-
-
Education
-
Clarkson University
Master of Science - MS, Engineering and Global Operations Management -
Widener University
Bachelor of Science (BS), Mechanical Engineering
Community
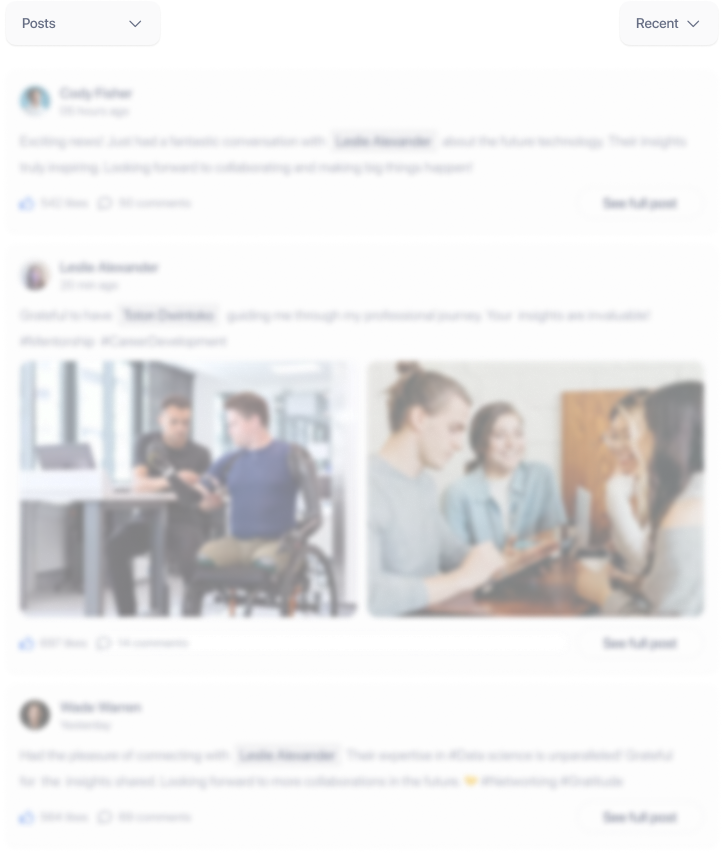