Tatiana Dahlstedt
Planner at Cox & Company- Claim this Profile
Click to upgrade to our gold package
for the full feature experience.
-
English Full professional proficiency
-
Spanish Native or bilingual proficiency
Topline Score
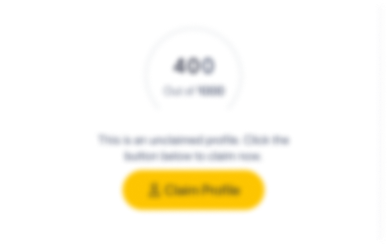
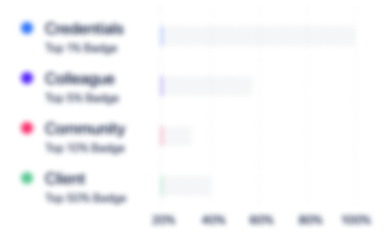
Bio

Stamatios Saridakis
Tatiana is a very energetic person and a pleasure to work with. See is very detailed oriented and a true professional on what see does best. I will recommend Tatiana for her professionalism and well rounded knowledge.

Orly Garrett
Tatiana is an intelligent woman very capable of accomplishing assigned tasks independently and showing initiative while doing so. Although she held a clerical position, she could clearly perform duties well beyond a clerical function. I would recommend her unhesitatingly.

Stamatios Saridakis
Tatiana is a very energetic person and a pleasure to work with. See is very detailed oriented and a true professional on what see does best. I will recommend Tatiana for her professionalism and well rounded knowledge.

Orly Garrett
Tatiana is an intelligent woman very capable of accomplishing assigned tasks independently and showing initiative while doing so. Although she held a clerical position, she could clearly perform duties well beyond a clerical function. I would recommend her unhesitatingly.

Stamatios Saridakis
Tatiana is a very energetic person and a pleasure to work with. See is very detailed oriented and a true professional on what see does best. I will recommend Tatiana for her professionalism and well rounded knowledge.

Orly Garrett
Tatiana is an intelligent woman very capable of accomplishing assigned tasks independently and showing initiative while doing so. Although she held a clerical position, she could clearly perform duties well beyond a clerical function. I would recommend her unhesitatingly.

Stamatios Saridakis
Tatiana is a very energetic person and a pleasure to work with. See is very detailed oriented and a true professional on what see does best. I will recommend Tatiana for her professionalism and well rounded knowledge.

Orly Garrett
Tatiana is an intelligent woman very capable of accomplishing assigned tasks independently and showing initiative while doing so. Although she held a clerical position, she could clearly perform duties well beyond a clerical function. I would recommend her unhesitatingly.

Experience
-
Cox & Company
-
United States
-
Aviation and Aerospace Component Manufacturing
-
100 - 200 Employee
-
Planner
-
Aug 2021 - Present
Summary:Coordinate and expedite flow of material, parts and assemblies between departments.Duties and Responsibilities:- Review of backlogs and related information to determine material requirements using Material Requirements Planning (MRP) to identify required materials.- Requisitions material and establishes delivery dates to Purchasing, according to customer requirements and material availability.- Generate shop orders based upon Engineering Masters, optimum lot sizes and material availability to support Master Production Schedule (MPS)- Monitor production schedules and reports status to contracts on weekly meetings.- Review computerized records such as material inventory, in process production reports for quantity and location of materials to insure accuracy.- Move or arrange transport of materials from one department to another as required.- Perform yearly physical inventory for all assigned programs. Show less
-
-
Stockroom Supervisor
-
Nov 2015 - Aug 2021
Summary-Collect work orders from the planning group and schedule the stockroom staff kitting activities to support work order release dates and the production department.-Oversee the inventory cycle count program, ensuring accuracy of inventory and performing root cause analysis for inaccurate inventory to continuously improve material management.-Manage and continuously improve the control and flow of material from supplier to customer.-Manage the shelf life program, monitoring expiration dates and performing positive recall of soon to expire material from the production floor.-Monitor the stockroom freezer and update out-time logs for temperature controlled material.-Manage and lead a group of 5 stockroom clerks, assigning their work day-to-day, approving their time and attendance, as well as personal time off. Performs year-end reviews, as well as provide meaningful feedback and coaching throughout the year to help employee’s grow and improve.-Creates purchase orders for Stockroom supply material.-Ensure compliance to all company standards and procedures. Show less
-
-
-
Frequency Electronics, Inc.
-
United States
-
Appliances, Electrical, and Electronics Manufacturing
-
1 - 100 Employee
-
Hybrid Stock Room Clerk - Junior Planner
-
Nov 2011 - Oct 2015
Kitting of parts for high reliability programs requiring traceability by using ESD pre cautions per FEI standards. Use of parts list to kit material. Verify information in kitted parts as: Date Code, Lot #'s, Quantities, Ref. Designations, Manufacturer, Project #, Part # and ATRs. Creation of reconciliation forms to be attached to the configuration log. Assure all documents are approved and are the latest revision. Assure each kit contains parts list, kitting log, shortage sheets and manufacturing bar coded travelers before releasing to the manufacturing floor. Issue parts after kit is pulled and when requested by manufacturing. Receive parts after inspected in QA and re-locate to adecuate warehouse by project number assigned Show less
-
-
-
U.S. Census Bureau
-
United States
-
Government Administration
-
700 & Above Employee
-
Enumerator NRFU RI Non Response Follow-Up Re-Interview
-
May 2010 - Aug 2010
Quality assurance on interviews by re-interviewing a percent of all households who did not mail in their forms, but were counted by a Census taker. Quality assurance on interviews by re-interviewing a percent of all households who did not mail in their forms, but were counted by a Census taker.
-
-
-
-
Translator
-
Dec 2009 - Feb 2010
Translation of Spec sheets for products sold by the company. Translation of Spec sheets for products sold by the company.
-
-
-
U.S. Census Bureau
-
United States
-
Government Administration
-
700 & Above Employee
-
Enumerator Address Canvassing
-
Apr 2009 - Jun 2009
Planned work by reviewing assignment area to determine organization of neighborhoods and locate households for conducting interviews. Conducted interviews with residents in assigned areas by following stringent guidelines and confidentiality laws. Explained the purpose of the census interview, answered resident's questions, elicited information following a script, and recorded census data on forms. Complied with accuracy standards while maintaining high production rates. Maintained records of hours worked, units produced, miles driven, quality control results, and expenses incurred in the performance of duties. Meet daily with supervisor to review and submit work, and receive additional instructions. Show less
-
-
-
JRS Architect, P.C.
-
United States
-
Architecture and Planning
-
1 - 100 Employee
-
Junior Project Manager
-
Aug 2007 - Oct 2008
Preparation of construction drawings; floor plans, elevations, sections and renderings (AutoCad 2009LT, some photoshop). Field measurements to verify existing conditions. Coordination between different trades. Interaction with Clients and Project Architecs to apply proposed layouts to spaces based on existing conditions. Responsible with a team of two designers for producing space plans and interior finishes for corporate offices and banks. Developed expertise in field measuring, architectural planning, inventory product specification, finish selection, renderings and presentation boards. Show less
-
-
-
Catapano Engineering and Architecture, P.C.
-
United States
-
Architecture and Planning
-
1 - 100 Employee
-
Architectural Designer
-
Feb 2007 - Aug 2007
Preparation of construction drawings; floor plans, elevations, sections and renderings (AutoCad 2007, some photoshop). Field measurements to verify existing conditions. Interaction with Project Architects to apply proposed layouts to spaces based on existing conditions. Worked creating construction Documents for McDonald’s restaurants and Starbucks coffee shops. Preparation of construction drawings; floor plans, elevations, sections and renderings (AutoCad 2007, some photoshop). Field measurements to verify existing conditions. Interaction with Project Architects to apply proposed layouts to spaces based on existing conditions. Worked creating construction Documents for McDonald’s restaurants and Starbucks coffee shops.
-
-
-
RexCorp Realty
-
Real Estate
-
1 - 100 Employee
-
Architectural Draftperson
-
Aug 2004 - Feb 2007
Preparation of construction drawings; floor plans, elevations and sections. (AutoCad 2005). Field measurements to verify existing conditions. Interaction with Regional Architects to apply proposed layouts to existing or new tenant spaces. Confirmation of finishes. Floor and wall finishes, window treatments and millwork finishes also. Supervision and scheduling for the Central Architecture Department. Management of Spaceman data files. Preparation of construction drawings; floor plans, elevations and sections. (AutoCad 2005). Field measurements to verify existing conditions. Interaction with Regional Architects to apply proposed layouts to existing or new tenant spaces. Confirmation of finishes. Floor and wall finishes, window treatments and millwork finishes also. Supervision and scheduling for the Central Architecture Department. Management of Spaceman data files.
-
-
-
-
Associate Architect
-
Feb 2004 - Jun 2004
Preparation of construction drawings; floor plans, elevations, sections and renderings (AutoCad 2004, some photoshop). Field measurements to verify existing conditions. Filing for permits at various Building Departments around the Long Island area. Worked with violations in NYC. Diazo (blue line) reproduction. Model making. Preparation of construction drawings; floor plans, elevations, sections and renderings (AutoCad 2004, some photoshop). Field measurements to verify existing conditions. Filing for permits at various Building Departments around the Long Island area. Worked with violations in NYC. Diazo (blue line) reproduction. Model making.
-
-
-
-
Designer Assistant
-
Feb 2002 - Feb 2004
Preparation of construction drawings; floor plans, elevations, sections and renderings (AutoCad 2000, some photoshop). Wall System Bill-of-Materials (BOM) and diagrams. Supervision and scheduling of designer assistant department. Sales Order entry and revision. Sales volume/performance dat Preparation of construction drawings; floor plans, elevations, sections and renderings (AutoCad 2000, some photoshop). Wall System Bill-of-Materials (BOM) and diagrams. Supervision and scheduling of designer assistant department. Sales Order entry and revision. Sales volume/performance dat
-
-
-
Frequency Electronics, Inc.
-
United States
-
Appliances, Electrical, and Electronics Manufacturing
-
1 - 100 Employee
-
Clerical
-
2000 - 2002
-
-
Education
-
Nassau Community College
AAS Design, Interior Design -
Universidad José María Vargas
Architecture, Architecture -
Colegio Francia
High School Diploma, Science -
Colegio Maria Auxiliadora
Community
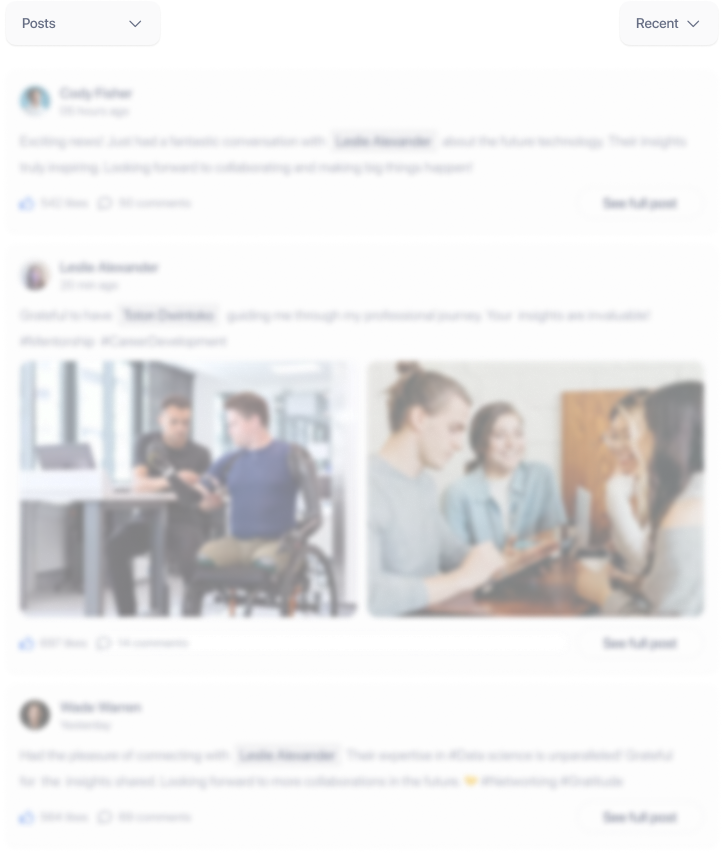