Tanya Dorn
Sr. Consultant at Spinnaker SCA- Claim this Profile
Click to upgrade to our gold package
for the full feature experience.
Topline Score
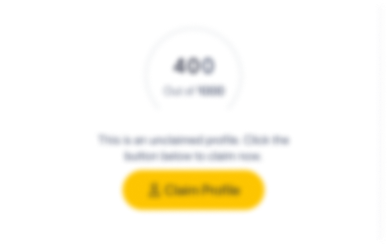
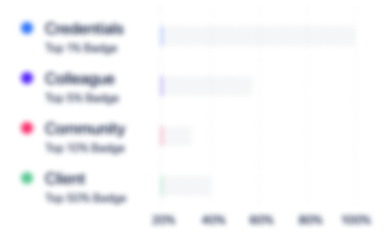
Bio


Experience
-
Spinnaker SCA
-
United States
-
Business Consulting and Services
-
1 - 100 Employee
-
Sr. Consultant
-
Jun 2022 - Present
Colorado, United States - Collaborated with client organizations to assess their supply chain operations, identify areas of improvement, and develop customized solutions to enhance efficiency and reduce costs. - Analyze supply chain processes, including demand planning, procurement, inventory management, and logistics, to identify bottlenecks, inefficiencies, and cost drivers. - Provided training and workshops to clients on Kinaxis RapidResponse best practices, supply planning, and demand forecasting… Show more - Collaborated with client organizations to assess their supply chain operations, identify areas of improvement, and develop customized solutions to enhance efficiency and reduce costs. - Analyze supply chain processes, including demand planning, procurement, inventory management, and logistics, to identify bottlenecks, inefficiencies, and cost drivers. - Provided training and workshops to clients on Kinaxis RapidResponse best practices, supply planning, and demand forecasting techniques - Collaborated with cross-functional teams including procurement, production, and logistics - Prepare and present training documents and reports for recommendations for further improvements - Assisted in the management of client relationships and resolving any issues or concerns. - Collaborated with cross-functional teams including procurement, production, and logistics, to develop and monitor production schedules, ensuring alignment with customer demand Show less
-
-
-
mSE Solutions
-
Germany
-
Business Consulting and Services
-
1 - 100 Employee
-
Sr. Production Consultant
-
Sep 2021 - Jun 2022
Germany - Functioned as interim planning activities for 5 plants globally - Conducted comprehensive assessments of production facilities, evaluated workflows, and recommended process enhancements to reduce waste, minimize downtime, and optimize resource utilization. - Supported daily manufacturing operations, ensuring adherence to production schedules, and quality standards - Developed and implemented production strategies, including lean manufacturing techniques, and improved… Show more - Functioned as interim planning activities for 5 plants globally - Conducted comprehensive assessments of production facilities, evaluated workflows, and recommended process enhancements to reduce waste, minimize downtime, and optimize resource utilization. - Supported daily manufacturing operations, ensuring adherence to production schedules, and quality standards - Developed and implemented production strategies, including lean manufacturing techniques, and improved productivity. - Conducted training and workshops for production teams, focusing on best practices, and quality control. - Improving manufacturing processes and optimizing operational efficiency Show less
-
-
-
Plexus Corp.
-
United States
-
Appliances, Electrical, and Electronics Manufacturing
-
700 & Above Employee
-
Master Scheduler II
-
Oct 2018 - Sep 2021
Neenah, Wisconsin, United States - Developed and maintained production forecasts, ensuring alignment with customer demands and optimizing resource utilization. - Collaborated with cross-functional teams including production, procurement, and logistics to identify capacity constraints and implement strategies for meeting production targets. - Planned and scheduled production activities considering lead times, material availability, and production capacity. - Conducted regular analysis of production data to identify… Show more - Developed and maintained production forecasts, ensuring alignment with customer demands and optimizing resource utilization. - Collaborated with cross-functional teams including production, procurement, and logistics to identify capacity constraints and implement strategies for meeting production targets. - Planned and scheduled production activities considering lead times, material availability, and production capacity. - Conducted regular analysis of production data to identify bottlenecks, implement corrective actions, and improve overall efficiency. - Monitored and tracked key performance indicators (KPIs) related to production schedules, such as on-time delivery, schedule adherence, and cycle time leveraging software tools and ERP systems - Coordinated with suppliers to ensure timely delivery of raw materials and components - Collaborate with program managers, customers, and stakeholders to identify key requirements and constraints · Manages material cost and schedule impact of proposed engineering changes in addition to taking necessary actions to ensure positive implementation and incorporation of approved engineering releases. · Mentor and trained new Production Planners and Master Schedulers on planning systems, procedures, and workflow
-
-
Production Planner
-
Sep 2010 - Oct 2018
Neenah, Wisconsin, United States - Develop and maintain project schedules, ensuring alignment with project objectives and deadlines - Conduct regular schedule reviews to identify potential risks and propose mitigation strategies - Monitor and track project progress, providing regular updates to stakeholders - Coordinate with cross-functional teams to resolve scheduling conflicts and optimize resource allocation - Implement and enforce scheduling standards and best practices across the organization - Actively… Show more - Develop and maintain project schedules, ensuring alignment with project objectives and deadlines - Conduct regular schedule reviews to identify potential risks and propose mitigation strategies - Monitor and track project progress, providing regular updates to stakeholders - Coordinate with cross-functional teams to resolve scheduling conflicts and optimize resource allocation - Implement and enforce scheduling standards and best practices across the organization - Actively participated in daily and weekly production meetings, providing updates on schedule adherence, and addressing any concerns or issues. - Collaborated with internal customer teams on monthly financial forecast
-
-
Production Team Lead
-
Apr 2004 - Sep 2010
United States Provided leadership for 10 to 15 direct reports. · Effectively communicated daily schedules, goals, quality issues/concerns between shifts to ensure customer expectations are met · Assigned work assignments based on daily department needs and achieved department metrics. · Conducted performance appraisals. · Coaching, disciplinary action and supported Lean/Sigma, continuous improvement activities while providing input for improvements
-
-
Education
-
Fox Valley Technical College
Business Management, General Sales, Merchandising and Related Marketing Operations -
Chilton High School
Community
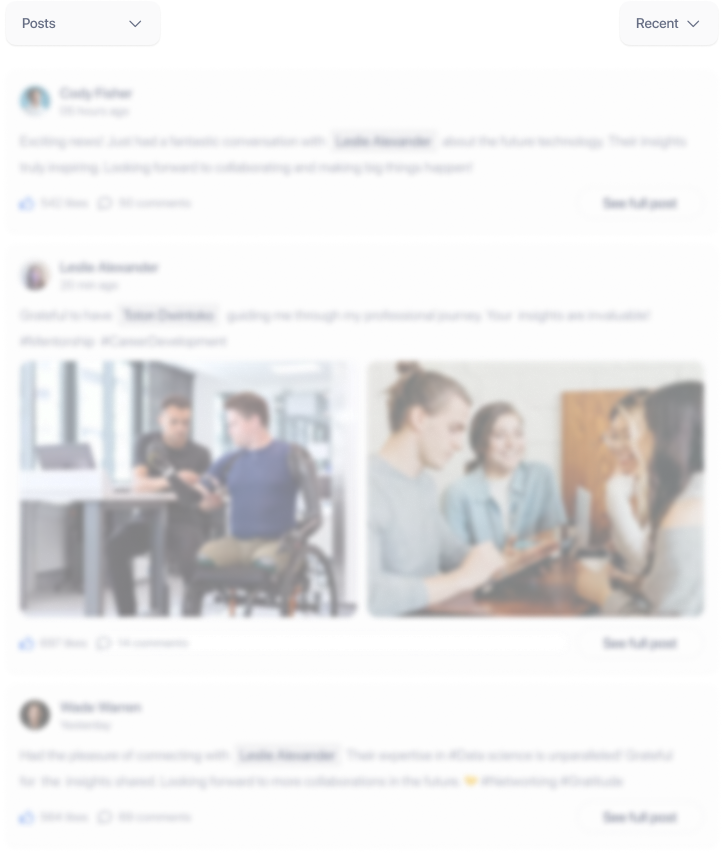