
Tammie McGowan, BSBA
CSR Performance Assessment and Assurance Manager at Coastal Logistics Group- Claim this Profile
Click to upgrade to our gold package
for the full feature experience.
Topline Score
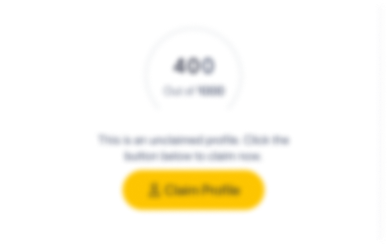
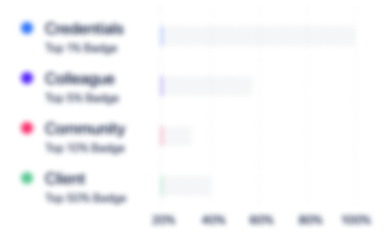
Bio


Credentials
-
Six Sigma Green Belt
Caterpillar Inc.
Experience
-
Coastal Logistics Group
-
United States
-
Transportation, Logistics, Supply Chain and Storage
-
1 - 100 Employee
-
CSR Performance Assessment and Assurance Manager
-
Sep 2015 - Present
Oversee work performance and accuracy of billing of a team of highly experienced customer service representatives. Provide support to CSRs throughout the month to ensure end of month invoicing is kept on track for reporting to Executive Leadership.Review and investigate past due accounts, including communication with customers for resolution.Set up new systems and processes and provide training as required.Assist as needed with all functions of Customer Service.Review quotes to ensure all aspects of work performed is captured and accurate.
-
-
Key Account Manager
-
Sep 2015 - Sep 2022
• Manage shipping, receiving and inventory control for major accounts. • Coordinate container movement from the Port of Charleston and Savannah to CLG.• Interact with customers and anticipate customer needs to initiate assistance beyond duties assigned.• Provide system support locally and to other CLG facilities.• Prepare estimates and invoices to customers using Microsoft CRM. • Process internal paperwork for all incoming and outgoing shipments.
-
-
-
Tex Cap Electric
-
United States
-
International Trade and Development
-
1 - 100 Employee
-
Office Administrator
-
Jun 2015 - Sep 2015
Responsibilities included placing ads for employment, calling potential candidates, verifying references, handing the paperwork for new hires (applications, submitting background checks, reviewing base access forms for accuracy), new hire orientation, performing drug and alcohol testing, coordinating DOT physicals, submitting payroll to corporate, reviewing safety procedures, and ensuring office supplies were available when needed & replenishing when necessary. Responsibilities included placing ads for employment, calling potential candidates, verifying references, handing the paperwork for new hires (applications, submitting background checks, reviewing base access forms for accuracy), new hire orientation, performing drug and alcohol testing, coordinating DOT physicals, submitting payroll to corporate, reviewing safety procedures, and ensuring office supplies were available when needed & replenishing when necessary.
-
-
-
Metalworx, Inc. - a Division of Jrlon, Inc.
-
United States
-
Machinery Manufacturing
-
1 - 100 Employee
-
Warehouse Technician
-
Aug 2014 - Mar 2015
Implemented and maintained Inventory Record Accuracy process and metrics resulting in substantial improvement in Inventory Accuracy. Ensured that all materials, whether work in process, raw materials, purchased items, customer supplied material, or finished goods, were properly received and stored in the warehouse for future disposition. Performed cycle counts and inventory management transactions in E2 shop system. Directed routing of all in-process production parts to next operation. Supported Materials Coordinator with all aspects of shipping. Assisted Materials Manager with continuous improvement efforts. Developed standard packaging requirements for finished goods and updated routing information in E2 Shop System.
-
-
-
Caterpillar Inc.
-
United States
-
Machinery Manufacturing
-
700 & Above Employee
-
Materials Technician
-
Sep 2009 - May 2014
Supervised teams of full time and contract workers to count, reconcile, and pack parts for shipment for the exit of twelve value streams due to facility closure. Managed teams of contract workers to successfully complete physical inventories in support of a warehouse consolidation project resulting in a $640k annual lease cost reduction. Assisted with managing and executing customer consigned inventory physical audits resulting in 99% accuracy for four consecutive years. Performed analysis and submitted proper documentation for approval to scrap excess material. Led discussions in daily team meetings reviewing goals and problem solving initiatives. Drove continuous improvement culture by involving employees in problem solving & decision making as well as recognizing them for exceptional work. Prepared charts and graphs to illustrate metrics, material handling, and machine utilization. Developed and/or revised work instructions for all aspects of warehouse operations. Assisted in planning work assignments in accordance with production, shipping, and auditing schedules.
-
-
Configuration Technician
-
May 2007 - Dec 2012
Developed and implemented Incoming Quality Audit and nonconforming parts processes to measure supplier performance. Collaborated with suppliers to implement corrective actions on nonconforming incoming material resulting in a 12% reduction in line down time. Received “best practice” recommendation for implementing plant wide Material Review process. Implemented plant wide “Stop to Fix” culture and trained over 300 associates on new process. Created clear, concise and accurate work instructions, including visual representation of steps, utilizing Caterpillar blueprints. Assisted Engineering department, researching and developing New Product Introductions for one automotive and seven hydraulic lines, including service part processes.
-
-
Education
-
Southern Wesleyan University
Bachelor's Degree, Business Administration and Management, General -
Trident Technical College
Associate's degree, Information Technology -
Berkeley High School
High School Diploma, College Prep
Community
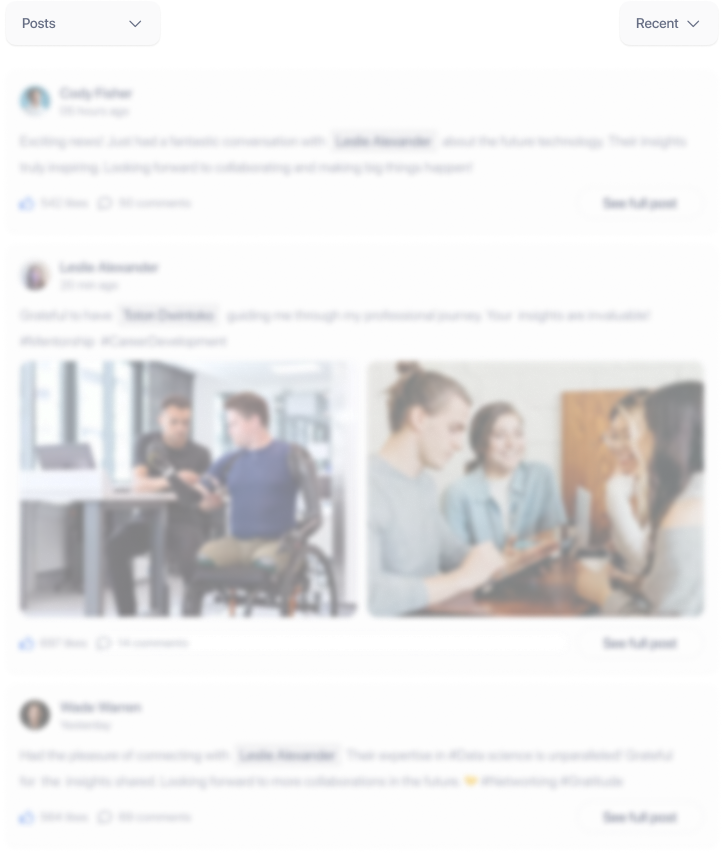