Syed Shoaib Raza
QA/QC Manager at DESCON ENGINEERING LIMITED- Claim this Profile
Click to upgrade to our gold package
for the full feature experience.
-
English -
Topline Score
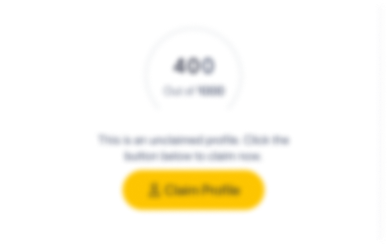
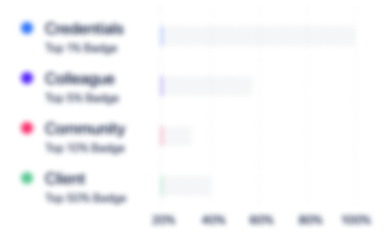
Bio
0
/5.0 / Based on 0 ratingsFilter reviews by:
Credentials
-
CSWIP 3.1
TWIOct, 2018- Sep, 2024 -
ASNT RT/UT/PT/MPI Level II
Real Time NDT ServicesSep, 2017- Sep, 2024 -
CSWIP 3.1
TWI Cambridge UKDec, 2013- Sep, 2024
Experience
-
DESCON ENGINEERING LIMITED
-
United Kingdom
-
Industrial Machinery Manufacturing
-
1 - 100 Employee
-
QA/QC Manager
-
Nov 2022 - Present
• Experienced Quality Management expertise in Mechanical Construction, spanning diverse sectors including Oil & Gas, Piping & Pipeline Projects (including Oil Flow lines, Cross country Pipelines, Central Processing Pipe lines, Refinery & Oil wells Piping), Pressure Vessels, Power Plants, Infrastructure, & Process Industries.• Proven track record in problem-solving & enhancing customer satisfaction, with a strong work ethic & a passion for excellence. I bring robust organizational skills & to secure a Quality Manager position, poised to contribute to our team's success in achieving company goals.• Proficient in reviewing & preparing Inspection & Test Plans (ITPs), Quality Inspection Plans (QIPs), Project Quality Plans (PQP), method statements, & Quality Procedures. Highly skilled in interpreting Isometric Drawings & ensuring alignment with relevant codes & st&ards.• Conducting internal audits in accordance with QMS ISO-9001 to ensure organizational compliance with quality management st&ards.• I have experience leading & participating in both internal & external audits & assessments, employing various tools like checklists, audit agendas, notifications, & preparing comprehensive audit reports. Additionally, I proactively collect best practices & insights from completed & ongoing projects, striving for continuous improvement in client quality assurance system documentation.• Efficiently manage & track approved & pending documents, procedures, & technical queries for EPC projects to ensure streamlined control & compliance.• Proficiently prepare, maintain, & update project welding control summaries while generating welding summaries for each system, oil well, or project to ensure accurate documentation & comprehensive project oversight.• Demonstrated expertise in coordinating with inter-discipline departments, clients, consultants, vendors, & inspection agencies to ensure seamless communication, collaboration, & project alignment. Show less
-
-
QA/QC Manager
-
Nov 2020 - Nov 2022
• Proven track record of delivering exceptional technical support & providing engineering clarifications to clients, fostering strong client relationships & project success.• I meticulously review project specifications & contract documents to ensure a clear understanding & identification of quality requirements in accordance with the relevant code/standard.• Act as a liaison between the Integrity Contractor(s) to ensure the completeness & currency of the asset register, inspection strategies, programs, plans of inspection, & condition monitoring, facilitating a comprehensive approach to asset management.• Provide independent assessment & feedback to Client on the effectiveness of contractors’ quality management processes & serve as the focal point for review/ approval of their quality plans. Prepare quality indicators & trends & develop necessary action plans to achieve quality objectives.• Assist the Employer / Client in identifying global quality requirements applicable to all contractors & establishing comprehensive cost-effective project quality systems including resources, project quality plans, project procedures, audit schedule.• Ensure compliance with company statutory procedures, quality, & safety st&ards, including reporting. Conduct technical audits, inspections, testing, & surveillance to ensure project quality requirements & to support front-end activities for material inspection & control systems.• Communicate with key project stakeholders to determine project requirements. I'm seeking a full-time position that presents professional challenges & allows me to apply my interpersonal skills, strong time management, & problem-solving abilities in alignment with project quality requirements.• to implement the PDCA (Deming Cycle) improvement process to enhance quality requirements in accordance with the standard. Additionally, to plan, coordinate, & lead quality programs to maintain alignment with established standards. Show less
-
-
-
Descon Engineering Limited
-
United Kingdom
-
Industrial Machinery Manufacturing
-
1 - 100 Employee
-
QA/QC Manager
-
Nov 2018 - Nov 2020
• Responsible for overseeing project quality planning, engineering and construction inspection activities. • Recorded, analyzed, and distributed quality statistical information. • Monitored staff organization and suggested improvements to daily functionality. • Reported production malfunctions to managers and production supervisors. • Implemented new quality assurance and customer service standards. • Assured consistent quality of production by implementing and enforcing automated practice systems. • Inspected products and worker progress throughout production. Evaluated interactions between associates and customers to assess personnel performance. • Collaborated with cross-functional teams to develop and implement process and system improvements. • Conducted process and system audits to identify areas of improvement and enforce compliance with industry standards. • Developed and implemented comprehensive quality assurance plans to monitor product quality and adherence to regulatory standards. • Investigated customer complaints and performed corrective actions to resolve quality issues. • Performed root cause analysis to identify and resolve quality issues and defects. • Created and maintained quality management systems to align with industry standards. • Assessed product quality by monitoring quality assurance metrics, reports and dashboards. • Conducted risk assessments to identify and mitigate potential quality issues. • Applied coaching techniques and tools to support managers and team members in improving performance. • Developed quality planning for multiple new product launches by verifying customer requirements and implementing in design and production. • Tracked quality issues with external customers, suppliers, and internal plant operations. Established and tracked quality department goals and objectives. • Determined quality department standards, practices, and procedures. Show less
-
-
-
Khaled Juffali Industrial Company
-
Oil and Gas
-
1 - 100 Employee
-
QA/QC Incharge
-
Apr 2017 - Jul 2018
• Developed and updated tracking spreadsheets for process monitoring and reporting. • Generated reports detailing findings and recommendations. • Conducted training and mentored team members to promote productivity and commitment to friendly service. • Conducted training and mentored team members to promote productivity, accuracy, and commitment to friendly service. • Established open and professional relationships with team members to achieve quick resolutions for various issues. • Mentored and guided employees to foster proper completion of assigned duties. • Built strong relationships with customers through positive attitude and attentive response. • Supervised team members to confirm compliance with set procedures and quality requirements. • Assisted in recruitment of new team members, hiring highest qualified to build team of top performers. • Promoted high standards through personal example to help each member understand expected behaviors and standards. • Communicated KPIs outlined in annual plan to inform employees of expectations and deliverables. • Reviewed, implemented and updated company records related to team activities for future reference. • Monitored team performance and provided constructive feedback to increase productivity and maintain quality standards. • Worked with team to identify areas of improvement and devised solutions based on findings. • Developed effective improvement plans in alignment with goals and specifications. • Educated staff on organizational mission and goals to help employees achieve success. • Devised and implemented processes and procedures to streamline operations. • Conducted regular reviews of operations and identified areas for improvement. • Provided reporting for forecast analysis and ad-hoc reporting in support of decision-making. • Evaluated customer needs and feedback to drive product and service improvements. Show less
-
-
-
Bulleh Shah Packaging Pvt. Ltd. (BSP)
-
Pakistan
-
Packaging and Containers Manufacturing
-
200 - 300 Employee
-
Plant Mechanical / Piping Inspection Engineer
-
Feb 2016 - Apr 2017
• Developed and implemented procedures to meet product quality standards. • Liaised between quality control and other departments and contractors, providing project updates and consultation. • Recorded and organized test data for report generation and analysis. • Conducted data review and followed standard practices to find solutions. • Created testing protocols to be used across product lines. • Performed routine maintenance and calibration on testing equipment. • Assessed products or services to evaluate conformance with quality standards. • Reviewed and validated quality requirements for manufacturing planning, supplier purchase orders, and engineering specifications to meet contract compliance regulations. • Completed supporting documentation for testing procedures, data capture forms, equipment logbooks and inventory forms. • Documented and executed detailed test plans and test cases and summarized and logged audit findings for reporting purposes. • Performed tests and inspections to conform to established standards. • Interpreted test results by comparing to established specifications and control limits, making recommendations on the appropriateness of data for release. • Reported problems and concerns to management. • Monitored testing procedures and verified performance of tests according to established item specifications and protocol. • Conducted investigations into questionable test results. • Reviewed production processes and identified potential quality issues. • Inspected raw materials and finished products to verify quality and disposed items that did not meet safety requirements. • Inspected items and compared against standards to meet regulatory requirements. • Drafted technical documents such as deviation reports, testing protocols and trend analyses. • Collected and analyzed data to measure the effectiveness of quality control processes. • Increased customer satisfaction and grew business by maintaining close relationships with customers. Show less
-
-
-
China Petroleum Engineering & Construction Corporation (CPECC)
-
Oil and Gas
-
700 & Above Employee
-
Site QA/QC Manager
-
Nov 2014 - Feb 2016
• Identified control gaps in processes, procedures and systems through in-depth research and assessment and suggested methods for improvement.• Developed and implemented corrective actions to bring business areas in line with standards.• Consulted clients on internal control systems development and audit program improvements.• Prepared working papers, reports and supporting documentation for audit findings.• Interviewed business owners to understand needs and explain audit scope.• Identified management control weaknesses and provided value added suggestions for remediation.• Developed audit policies, guiding administrative and technical functions.• Maintained professional knowledge by attending technical workshops annually.• Partnered with auditors to track errors and add contributions to maintain accuracy.• Collected and reported monthly expense variances and explanations.• Found tax solutions to complicated tax issues or errors from incorrect tax filings.• Identified legal tax savings and recommended ways to improve profits.• Used accounting software to issue tax returns and prepare consolidated reports.• Collaborated with accounting manager to comply with governing bodies and limit regulatory risks.• Cooperated with senior leaders to create operating budgets and initiate financial planning.• Trained new employees on accounting principles and company procedures.• Liaised with HR manager to organize and perform quality standard training for new and existing staff.• Managed and archived quality documentation and participated in internal and external quality audits.• Evaluated quality problems and performed assessments to identify and resolve issues.• Prepare and disseminate all required documentation records such as daily status reports, punch lists describing work items to be done, sketches of work already completed, material requirements, calculations, etc.• Integrate with and work alongside the quality team and perform all related tasks. Show less
-
-
QA/QC Engineer
-
Jun 2013 - Feb 2015
• Followed quality standards and procedures to minimize errors and maximize customer satisfaction.• Updated quality control standards, methods and procedures to meet compliance requirements.• Minimized costs of poor quality (COPQ) and maximized returns resulting in huge cost savings. Devised specifications for processes.• Calibrated instruments and scales in production area and quality lab.• Provided observations, took measurements and performed tests at various stages according to quality control plan.• Improved quality processes for increased efficiency and effectiveness.• Increased customer satisfaction through adherence to quality standards and customer requirements.• Inspected inbound and outbound products for compliance with established industry standards, company policies and procedures.• Collaborated with contract representatives and oversaw quality control implementations and reporting.• Sorted product and provided expertise on non-conforming product requirements.• Wrote and implemented new rework procedures to standardize processes and streamline workflow.• Developed and deployed execution control plans and created work instructions and procedures.• Led quality-assurance projects and enhanced productivity, realizing percentage repair increase in profits.• Coordination with inter-discipline departments, clients/consultants vendors & Inspection agencies. Provide technical support and engineering clarifications to clients.• To coordinate with NDT contractor & interpret the results with relevant code. Erection & Fabrication Inspection of Piping and Pipeline works.• Take lead in supervising the work of the EPC contractors, Act as Focal point for liaison & coordination with the external quality assessment provider.• Provide technical direction and implement the project Quality work processes, procedures, manuals and systems ensuring the contractors implement the best quality practices and fully comply with all Project specifications/standards. Show less
-
-
-
Excel Engineering (Pvt) Ltd
-
Civil Engineering
-
1 - 100 Employee
-
QA/QC Engineer
-
Sep 2009 - Apr 2013
• Take lead in supervising the work of the EPC contractors, Act as Focal point for liaison and coordination with the external quality assessment provider. • Provide technical direction and implement the project Quality work processes, procedures, manuals and systems ensuring the contractors implement the best quality practices and fully comply with all Project specifications/standards. • Ensure compliance with all company statutory procedures, quality & safety standards including any defined recording and reporting procedures. • Prepared working papers, reports and supporting documentation for audit findings. • Partnered with auditors to track errors and add contributions to maintain accuracy. • Trained new employees on accounting principles and company procedures. • Monitor and perform technical audits, in progress inspections, testing and surveillance activities to ensure that project quality requirements are being met. • Gather best practices and lessons learned from completed/on-going projects and ensure that client quality assurance system documents are continuously improved. • Implement Project inspection and test Plans, collate Inspection Results, coordinate field inspection activities of Petrofac and Third-Party Inspection agencies. • Identify specific requirements in the contract, which require to be addressed separately and need to be controlled through specific procedures. • Prepare accordingly documents relevant to data control, inspection reporting procedure, technical queries and procedures for concessionary reports. • Provide necessary recommendations that need to be forwarded to the client. Review procurement documents to ensure that quality requirement have been correctly translated into purchase requisitions and design documents. • Issue of non-conformance reports and track all non-conformance reports and undertake remedial action as required. • Prepare and issue Weekly QA/QC Reports/presentations to Client; as required. Show less
-
-
-
-
Graduate Trainee QA Engineer
-
Feb 2009 - Aug 2009
• Conducted audit inspections and independent checks to verify parts and materials. Designed and coordinated engineering tests and experiments. • Adhered to safety procedures and good housekeeping standards to comply with regulations. • Participated in failure analysis and debugging report activities. • Analyzed and planned workflow, equipment placement and space requirements to improve manufacturing efficiency. • Estimated materials costs and sourcing requirements for project feasibility. • Assessed scope and requirements to assist with project design determinations. • Generated cost estimates for inclusion in proposed capital and expense budgets. Shadowed designers and engineers to learn ways to implement methodologies. • Worked closely with engineers on assigned projects during manufacturing stages of Steam Boilers. • Collaborated with stakeholders to verify delivery of desired quality requirements to distributors. Prepared standard reports and documentation to communicate results to senior management. • Assisted with coordination of new equipment installation and implementation. • Evaluated sites to determine soil adequacy for handling building foundation loads. • Evaluated quality control processes and made recommendations for improvements in quality control. • Monitored projects to determine areas and processes needing improvement. • Delivered public presentations to provide plans and updates on projects. • Adhered to timelines to meet quality assurance targets. Provided repairs to avoid long maintenance wait times. • I prepare monthly QA/QC statistics and reports for timely submission to the head office. To update quality data, welding control summaries, welder qualification records, weld repair data, and maintain NDT records in accordance with relevant codes, such as ASME BPVC -VIII. Show less
-
-
Education
-
University of the Punjab
B.Sc. Engineering, Engineering
Community
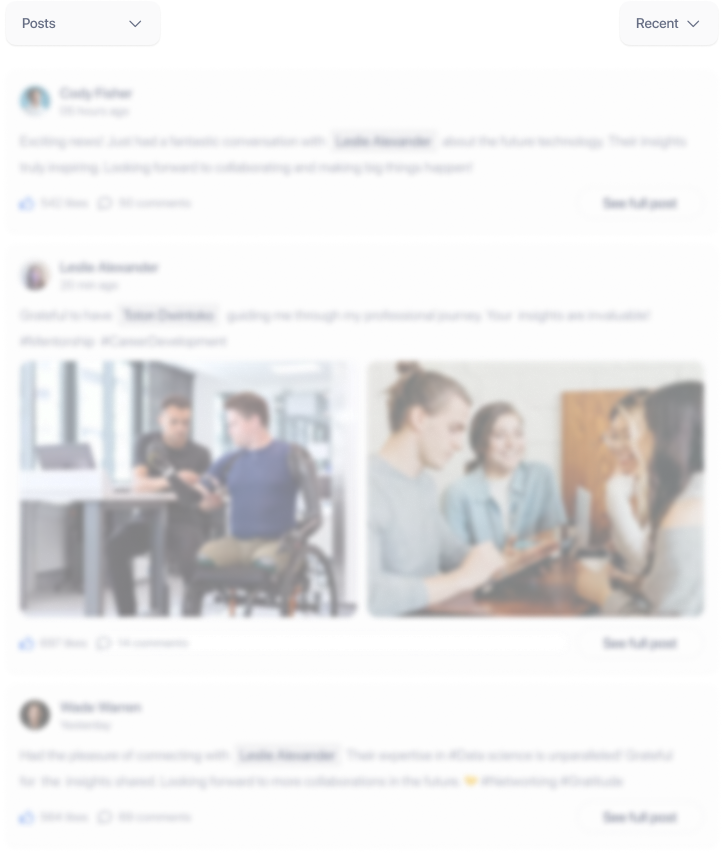