Suresh Devaraj
Service Coordinator at Accelleron- Claim this Profile
Click to upgrade to our gold package
for the full feature experience.
Topline Score
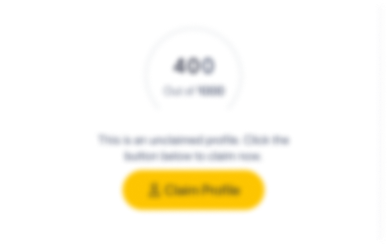
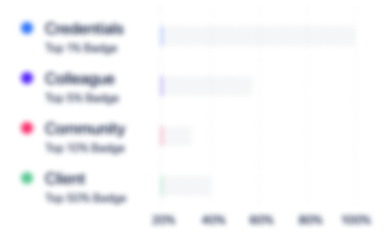
Bio


Experience
-
Accelleron
-
Switzerland
-
Industrial Machinery Manufacturing
-
700 & Above Employee
-
Service Coordinator
-
Mar 2022 - Present
Service operation lead-West region. Completely responsible for,1. Take care entire process RFQ level to Cash collection2. Service execution3. Ensure work standards according to ISO 9001:2015, throughout process. (as defined by company)4. Ensure 100% availability of equipment 5. Vendor management. Service operation lead-West region. Completely responsible for,1. Take care entire process RFQ level to Cash collection2. Service execution3. Ensure work standards according to ISO 9001:2015, throughout process. (as defined by company)4. Ensure 100% availability of equipment 5. Vendor management.
-
-
-
ABB India Ltd
-
500 - 600 Employee
-
Service Coordinator
-
Jun 2016 - Feb 2022
Service operation lead-West region. Completely responsible for,1. Take care entire process RFQ level to Cash collection2. Service execution3. Ensure work standards according to ISO 9001:2015, throughout process. (as defined by company)4. Ensure 100% availability of equipment 5. Vendor management. Service operation lead-West region. Completely responsible for,1. Take care entire process RFQ level to Cash collection2. Service execution3. Ensure work standards according to ISO 9001:2015, throughout process. (as defined by company)4. Ensure 100% availability of equipment 5. Vendor management.
-
-
-
ABB India Ltd
-
500 - 600 Employee
-
Senior Services Engineer
-
Sep 2005 - May 2015
Carrying out the activities of marketing, servicing, repairing & trouble shooting as well as generating spares order from customer. Managing failures & warranty claims through technical investigations and maintain coordination with Safety/Vendor co-coordinator Implementing quality systems in the organisation to reduce rejections & ensure zero defect products. Identifying areas of improvement and recommending process modifications and equipment calibrations to enhance operational efficiencies of the systems. Reviewing the operational practices, identify the areas of obstruction/ quality failures and work on system and process changes for qualitative improvement/ energy conservation. Assisting customer on operation of turbocharger and at the same time making records. Managing maintenance of workshop machineries as well as providing on the job training to new joiners.
-
-
-
Royal Enfield
-
India
-
Motor Vehicle Manufacturing
-
700 & Above Employee
-
Trainee
-
Oct 2004 - Aug 2005
Worked trainee on quality assurance department. Worked trainee on quality assurance department.
-
-
Education
-
RKDF UNIVERSITY
Bachelor of Engineering - BE, Mechanical Engineering -
Murugappa polytechnic college
Diploma, Mechanical Engineering
Community
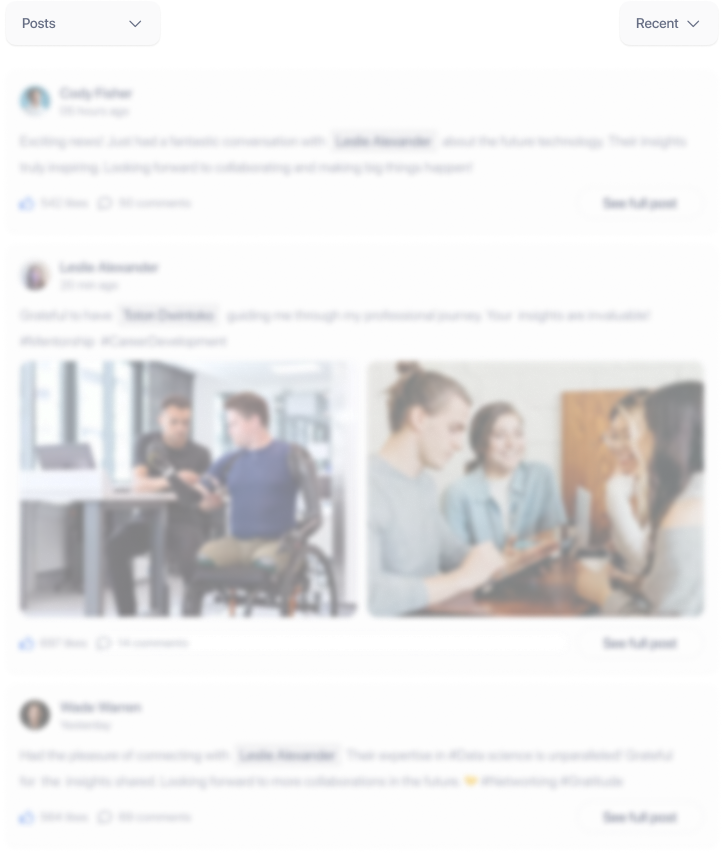