Sunny Garcha PCQI
QA Consultant at Paradigm Shift Consulting Limited- Claim this Profile
Click to upgrade to our gold package
for the full feature experience.
Topline Score
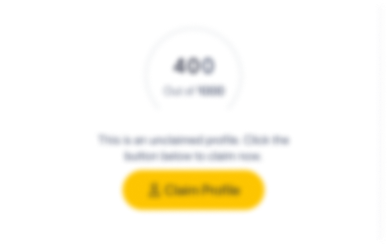
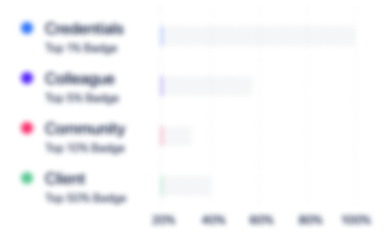
Bio


Experience
-
Paradigm Shift Consulting Limited
-
United Kingdom
-
Pharmaceutical Manufacturing
-
1 - 100 Employee
-
QA Consultant
-
Feb 2023 - Present
-
-
-
Medovate Limited
-
United Kingdom
-
Hospitals and Health Care
-
1 - 100 Employee
-
Senior Quality Engineer
-
Sep 2022 - Feb 2023
The Senior Quality Assurance Engineer I played a pivotal role in the enhancement and maintaining of the Medovate Quality Management System such that the system that is robust, efficient, compliant and meets the needs of the business. I also assumed leadership of some tasks including implementation of a new eQMS, MDSAP compliance, and non-conformance management, owning and controlling auditing systems and calibration and maintenance of equipment. Functions including: • Provide leadership in QA NC/CAPA root cause analysis and corrective actions • Lead gap analyses to ISO13485 and 21CFR part 820 • Lead eQMS implementation • Conduct process and design risk analyses where required and when they are required • Identify non-value adding steps in QMS processes and devise strategy to eliminate whilst maintaining compliance • Plan and conduct internal audits • Plan and conduct Supplier performance evaluation and auditing. • Facilitate audits of Medovate and partner facilities by external regulatory authorities. • Liaise with global regulatory authorities regarding the QMS and product certifications where required • Prepare and run Quality Management Review Meetings • Lead or participate in validation activities, risk management and design review • Management of post-market activities e.g. surveillance, customer feedback, failure analysis. • Contribute to strategic planning and implementation of Regulatory and Quality aspects of the business. • Keep abreast of new developments in QA/RA e.g. standards and regulations, assess impact, plan and complete mitigating actions. • Work closely with internal and external multi-disciplinary product development teams to ensure project success. • Liaise with other departments in achieving process optimisation • Conducting product related Quality Control activities where required • Deliver training on the QMS to existing and new staff.
-
-
-
AgPlus Diagnostics Ltd
-
United Kingdom
-
Medical Equipment Manufacturing
-
1 - 100 Employee
-
QA Manager
-
Mar 2021 - Sep 2022
As the QA Manager the position has me responsible for implementation and maintenance of the AG+ integrated Quality Management System and best practices across all elements of the business. Ensuring compliance with current legislation, approved policies and procedures. Maintaining adherence to service excellence and continuous improvement across the business As the QA Manager the position has me responsible for implementation and maintenance of the AG+ integrated Quality Management System and best practices across all elements of the business. Ensuring compliance with current legislation, approved policies and procedures. Maintaining adherence to service excellence and continuous improvement across the business
-
-
-
Smith+Nephew
-
United Kingdom
-
Medical Equipment Manufacturing
-
700 & Above Employee
-
Quality Specialist
-
Oct 2017 - Mar 2021
Smith & Nephew is a diversified advanced medical technology business that supports healthcare professionals in more than 100 countries to improve the quality of life for their patients. We have leadership positions in Orthopaedic Reconstruction, Advanced Wound Management, Sports Medicine and Trauma: • Orthopaedics Reconstruction - joint replacement systems for knees, hips and shoulders • Advanced Wound Management - wound care treatment and prevention products used to treat hard to heal wounds • Sports Medicine - minimally invasive surgery of the joint • Trauma & Extremities - products that help repair broken bones We have over 15,000 employees around the world. Annual sales in 2016 were more than $4.6 billion. We are a constituent of the UK's FTSE100 and our shares are traded on the London Stock Exchange and through American Depository Receipts on the New York Stock Exchange (LSE: SN, NYSE: SNN) . As a Quality Specialist the position helps determine disposition of final product and ensure compliance with Quality Assurance (QA) policies and procedures and SOPs. Multiple functions including: • Championing quality processes throughout the organisation to maintain standards to ISO 9001:2015 and 13485 • Responsible for implementation and maintenance of an adequate and effective internal audit program. • Organising CAPA consultations and helping to establish root cause and corrective and preventative actions. • Responsible for the maintenance of the QMS Document System. • Responsible for the update and issue of all site QA/RA documents. • Issuing Hold It Notices and coordinating as necessary product reconciliation and returns. • Management of the reconciliation of the quarantine area. • tracking & administering recall data. • compiling data for responses to competent authorities including MHRA, HPRA
-
-
-
Movianto
-
United Kingdom
-
Transportation, Logistics, Supply Chain and Storage
-
700 & Above Employee
-
Quality Coordinator
-
Mar 2013 - Oct 2017
Conduct extensive warehouse process and systems audits. Collate and execute a detailed examination of storage areas, deliver recommendations and solutions including corrective and preventative measures, enforce organisational, compliance and legislative requirements. Prepare comprehensive audit reports, formulate and communicate audit findings, evaluate feedback and offer advice on necessary and suggested improvements. Orchestrate and facilitate the training and coaching of staff members in all quality processes and procedures. Liaise directly with external auditors to host audits. Build strong relationships with customers during site visits. Act as a key interface for the company, handle and resolve complex customer complaints. Complete risk assessments to confirm safe working practices. Expertly investigate incidents, identify and mitigate ongoing issues to prevent reoccurrence.KEY ACCOMPLISHMENTS:• Achieved the overall compliance and auditing of all warehouses in accordance with MHRA and Home Office guidelines.• Performed effective non-conformance reporting and root cause analysis to resolve issues.• Championed quality processes throughout the organisation to secure an elevated level of compliance to GDP, ISO 9001:2008, and the MHRA.• Successfully established and integrated company Standards Operating Procedures (SOPs), devised and implemented Work Instructions (WIs) and supporting documents in accordance with all legislative requirements.• Effectively coordinated controlled drug import and export licence applications, accurately submitted the narcotic and psychotropic annual return to the Home Office.
-
-
Inventory controller
-
Oct 2006 - Mar 2013
-
-
Education
-
Lloyd's Register
QMS Auditor/Lead Auditor CQI & IRCA Certified -
Lloyds Register
Internal QMS Auditor -
Chartered Management Institute
First Line Management Level 3, Pass -
Hay Group
Hay Group Job Evaluation, Guide Chart Profile Methodology
Community
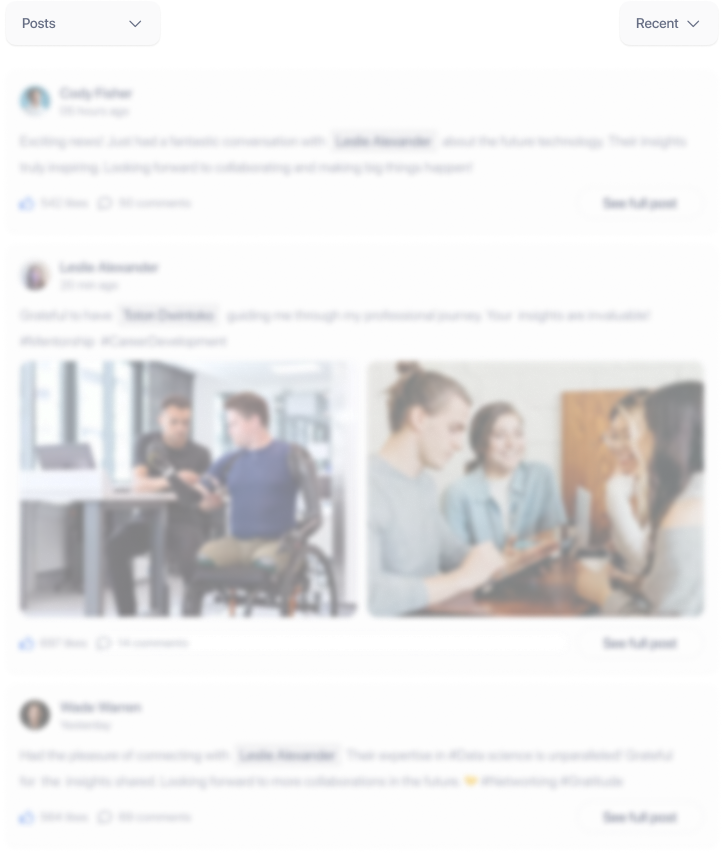