Sulay Parekh, P.Eng.
Maintenance Planner at Cenovus Energy- Claim this Profile
Click to upgrade to our gold package
for the full feature experience.
-
English Professional working proficiency
-
Gujarati Native or bilingual proficiency
-
Hindi -
Topline Score
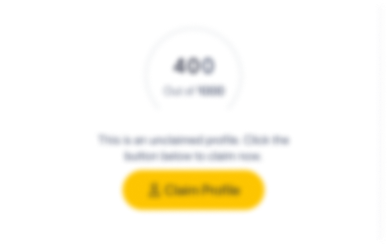
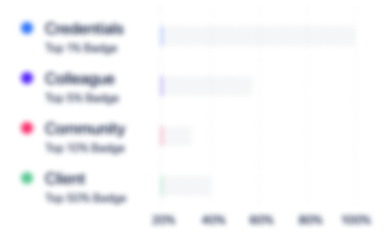
Bio

Josiah A. Oyiengo CFE,CISA,
A knowledgeable and experienced Engineer, meticulous in his work specifically scheduling and optimizing of resources, project management. A professional seeking to improve himself and his work mates/ peers.

Falit Goel
I know Sulay for over 10 years now. He is very hard working person and co-operative too. He does take his work seriously and believes in performing the work at right time along with positive attitude.

Josiah A. Oyiengo CFE,CISA,
A knowledgeable and experienced Engineer, meticulous in his work specifically scheduling and optimizing of resources, project management. A professional seeking to improve himself and his work mates/ peers.

Falit Goel
I know Sulay for over 10 years now. He is very hard working person and co-operative too. He does take his work seriously and believes in performing the work at right time along with positive attitude.

Josiah A. Oyiengo CFE,CISA,
A knowledgeable and experienced Engineer, meticulous in his work specifically scheduling and optimizing of resources, project management. A professional seeking to improve himself and his work mates/ peers.

Falit Goel
I know Sulay for over 10 years now. He is very hard working person and co-operative too. He does take his work seriously and believes in performing the work at right time along with positive attitude.

Josiah A. Oyiengo CFE,CISA,
A knowledgeable and experienced Engineer, meticulous in his work specifically scheduling and optimizing of resources, project management. A professional seeking to improve himself and his work mates/ peers.

Falit Goel
I know Sulay for over 10 years now. He is very hard working person and co-operative too. He does take his work seriously and believes in performing the work at right time along with positive attitude.

Credentials
-
Professional Mechanical Engineer
Association of Professional Engineers & Geoscientists of Saskatchewan (APEGS)May, 2021- Nov, 2024
Experience
-
Cenovus Energy
-
Canada
-
Oil and Gas
-
700 & Above Employee
-
Maintenance Planner
-
Oct 2015 - Present
• Reduction in 12% of duplicate and obsolete inventories and material by merging the spare codes enhancing the database with reduced number of inventory items • Completed BOMs and 150+ Tasklist on 100+ equipments for annual and regulatory inspections and frequent job activities and repetitive jobs for efficient and quicker package turn out for future jobs. • Created 18 strategy controlled Maintenance plans from single cycle to multiple cycle with various Maintenance schedule • Plan for regulatory inspection for equipment ( 30 Filter / Strainers, 20 API Tanks, 50 pumps, 7 Recip. Compressors, 21 Heat exchangers and many other rotary and static equipments) • Plan out all the Tank inspection internal and external and create a repair scope and modification needed as per API 650 standard. • Plan and support maintenance activities for pressure retaining components and piping systems; ensuring that repairs and/or modification conform to the requirements the ASME Boiler and ABSA and TSASK Pressure Vessel Code • Work with Procurement, Engineering and outside suppliers as required to order all non-stock parts and materials required to complete any given task; • Maintain complete contractor records, such as Bills of Material and specification sheets, within the electronic maintenance management system • Coordinate with the NACE inspector to inspect the Tank internal coating to see if it needs repair/ replacement. • Participate in appropriate Process Safety related evaluations/analysis (Process Hazard Analysis (PHA)/HAZOP, MOC checklists, etc.) • Provide inspection test plans (ITP) for maintenance activities including correct maintenance procedures, approved materials, code required non-destructive examination procedures/requirements and post maintenance testing procedures/requirements • Develop and maintain more than 45 generic Task list most commonly used in daily planning and use in the job package for work order
-
-
-
Dow
-
United States
-
Chemical Manufacturing
-
700 & Above Employee
-
Mechanical Maintenance Planner
-
Jan 2015 - Sep 2015
-Planning all routine maintenance work orders, covering full scope of operations & maintenance, accommodating safety requirements. -Develop comprehensive maintenance package as per Dow's site Safe Work Practices & Health, Safety and Environmental guidelines which includes manpower requirements, work sequencing, tool requirements, material requirements and entering requisitions for materials and services. -Ensure plans are updated based on field input via the planner feedback process. -Use equipment history and other technical information to include in current job plans. -Place completed work order packages to file cabinets in work area. -Review back log of new work orders that are waiting to be planned. -Maintain and manage the correct status of the work order in the planning process.
-
-
-
Loblaws Supermarkets Limited
-
Canada
-
Software Development
-
100 - 200 Employee
-
Frontend Member / Inventory Replenishment
-
Sep 2014 - Jan 2015
-Involve in Frontend jobs as Cashier and Merchandiser and also provided assistance to Counter Sales Representatives and Inside Sales Representatives as needed -Provide excellent Customer Service by assisting Customers in finding merchandise -Operate the register when needed and being knowledgeable about register operations -Provide assistance to the front end Associates with price checks -Ensure the merchandise is properly signed and priced and ensured stable stacking of merchandise. -Working closely with each respective division supervisor to further ensure their compliance with associated inventories -Maintain accuracy of inventory balances and made alternate arrangements in the event of shortages or delayed deliveries to minimize impact on the organization. -Inform and update non-stock orders in a timely fashion to purchaser, expediting all purchase orders,maintaining delivery information
-
-
-
Reliance Industries Limited
-
India
-
Oil and Gas
-
700 & Above Employee
-
Maintenance & Turnaround Planning Engineer
-
Aug 2010 - May 2014
-Achieved zero equipment failure for the Sulphur unit for the year 2013 by implementing preventive maintenance practices, condition monitoring techniques and by adhering to accurate equipment change over schedules-Reduction in 8% of duplicate and obsolete inventories by merging the spares enhancing the database with reduced number of inventory items-Attained 100% linking on unlinked Spares of all the equipments with its respective BOMs for Sulphur unit-Led and supervised all the subordinates from technicians, assistants and contractors for daily maintenance activities and shutdowns-Successfully completed planning and execution of the turnarounds for Sulphur and Crude units with responsibility of estimating, billing, coordination worth of $ 10 million -Prepared and managed annual budget for the plant of $2.5 million annually for plant maintenance-Published Maintenance and planning report on Weekly & Monthly Basis which included major activities done, shutdown jobs highlights and forward path for upcoming week and month to Vice president-Tracked Maintenance KPI’s like spares, Budget, Manpower utilization and Preventive maintenance activities.-Generated and executed work orders for Preventive maintenance, Breakdown maintenance & Condition Monitoring of rotary and static equipments.-Maintained equipment BOMs in SAP PM Module and equipment parts inventory to ensure parts availability for approximately 600 rotary and static equipments-Conducted safety audits with respect to equipment and work place abnormalities-Obtained and reviewed historical records of previously executed Turnaround jobs-Reviewed work scope change requests prior to their introduction into the proposed schedule and monitored the impact of it upon the Turnaround Plan-Monitored and maintained a continual update of the work requirements and requests and identified potentially problematic factors which can affect the turnaround schedule with regard to execution and progress
-
-
Graduate Mechanical Engineer
-
Sep 2008 - Jul 2010
-Maintained equipment BOMs in SAP PM Module and equipment parts inventory (in partnership with Stores) to ensure parts availability for approximately 600 rotary and static equipments.-Assessed and managed Spares codification, Material Procurement, Material Resources Planning (MRP) controlling, Insurance spares classification and monitoring.-Reduction in 8% of duplicate and obsolete inventories my merging the spares enhancing the database with reduced number of inventory items.-Achieved 100% linking on unlinked Spares with the respective BOMs for Sulphur and Crude Units-Created new Master data from Equipment strategy datasheet with BOM and cover all the spares maintained based on the hierarchy of the Superior equipment.-Issued purchase orders to suppliers to ensure 100% complete and on-time inbound delivery of quality finish products and raw materials-Reviewed inventory reports including excess and idle stock, inventory turnover, customer service rate, stock out, suppliers’ performance and critical stock items status-Monitored the ageing of stocks and follows through the disposition of condemned items to concerned departments.-Coordinated with customers on phase-in/out of items, product specifications, pricing and other related matters.-Extracted, validated and cleansed master data by comparing with actual data from warehouse audits to ensure accuracy
-
-
Education
-
UVPCE,Ganpat university
Bachelor of Technology (B.Tech.), Mechatronics, Robotics, and Automation Engineering -
Shree Narayana Guru Vidhyalaya
-
Calgary Immigrant Educational Society (CIES)
Project Management
Community
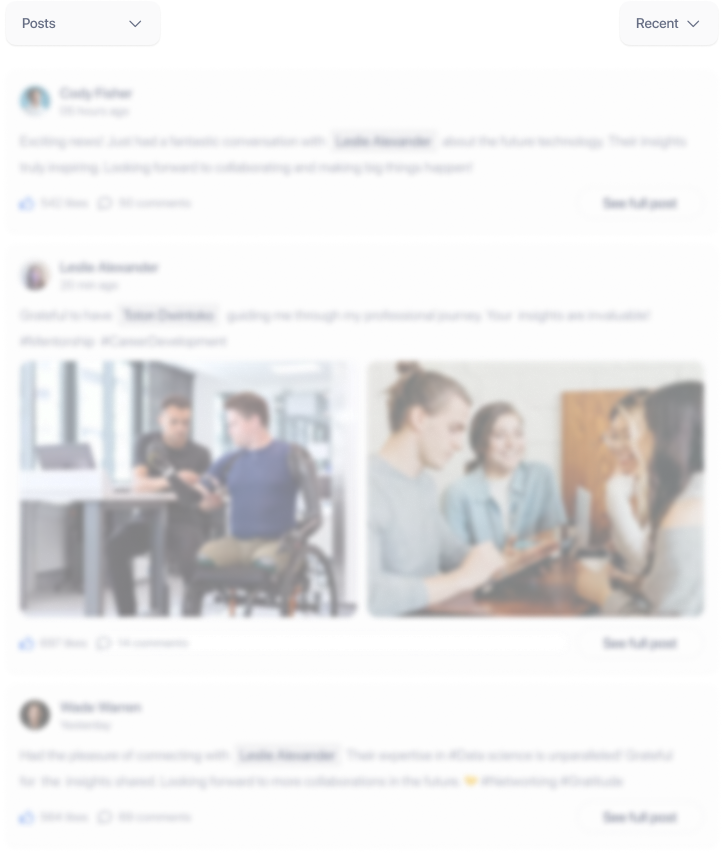