Sukhjinder Singh B. Eng, CSSBB
Quality Assurance Technician at National Engineered Fasteners Inc.- Claim this Profile
Click to upgrade to our gold package
for the full feature experience.
-
English -
-
Hindi -
-
Punjabi -
Topline Score
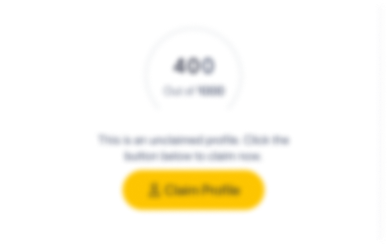
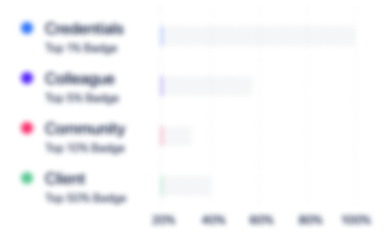
Bio
0
/5.0 / Based on 0 ratingsFilter reviews by:
Credentials
-
Lean Six Sigma Black Belt (ICBB)
The Council for Six Sigma Certification (CSSC)Dec, 2020- Sep, 2024 -
Solidworks
School of Business - Continuing Education at Conestoga CollegeDec, 2018- Sep, 2024 -
Process Quality Engineering
Conestoga CollegeDec, 2016- Sep, 2024 -
Project management
Conestoga CollegeApr, 2016- Sep, 2024
Experience
-
National Engineered Fasteners Inc.
-
Canada
-
Automotive
-
1 - 100 Employee
-
Quality Assurance Technician
-
Mar 2018 - Present
• Worked with suppliers to disposition the quarantined inventory and saved more than $50,000 • Taking lead role and supporting as necessary, the internal teams on issues related to internal, customer and supplier non-conformances and Corrective Action Requests• Facilitating and promoting problem-solving tools (the seven quality control tools, the seven management and planning tools, root cause analysis, Plan-Do-Check-Act (PDCA), 8D.• To write quality assurance reports that… • Worked with suppliers to disposition the quarantined inventory and saved more than $50,000 • Taking lead role and supporting as necessary, the internal teams on issues related to internal, customer and supplier non-conformances and Corrective Action Requests• Facilitating and promoting problem-solving tools (the seven quality control tools, the seven management and planning tools, root cause analysis, Plan-Do-Check-Act (PDCA), 8D.• To write quality assurance reports that describe manufacturing problems, corrective actions taken and preventative measures needed.• Lead the incoming quality inspection process, in-process quality control, internal audit program, gage and calibration process, and material tractability activities to assure effectiveness of the Quality System.• Read blueprints & Interpret GD&T on drawings.• Assisting Quality Manager in establishing, implementing and maintaining the Quality management system• To Create and maintain company quality documentation, such as quality manuals, quality procedures, etc.• To conduct audits-product, process, system or vendor etc. including closing out audit findings, create audits finding reports and determine proper corrective and preventive actions.• Respond to and address all customer concerns associated with the assigned programs with in the customer specified time frame and in the customer specific corrective action format. Follow up with the customer until closure is achieved.• Update and maintain the CAR log for customer issues making sure all required information are entered in a timely manner.• Participation in cross-functional teams, working with Design, Suppliers, in-house shops, sales, and planning.• To manage and maintain customer scorecards to meet and exceed the customers’ expectations; Show more Show less
-
-
-
Linamar Corporation
-
Canada
-
Motor Vehicle Manufacturing
-
700 & Above Employee
-
Quality Assurance Inspector
-
Jul 2017 - Mar 2018
• Assisted with Annual Layouts, capability studies, Internal and External audits, GR&R.• Assisted with Statistical Process Control (SPC) Analysis.• Operated CMM and worked/helped with CMM programming.• Performed various inspection using Vernier, Caliper, Tracer, Height Gauge, Pin Gauge, Optical comparator etc. to accomplish testing requirements.• Managed records of In-Process, First Off and Final Inspections. • Actively participated in Kaizen activities and provided… • Assisted with Annual Layouts, capability studies, Internal and External audits, GR&R.• Assisted with Statistical Process Control (SPC) Analysis.• Operated CMM and worked/helped with CMM programming.• Performed various inspection using Vernier, Caliper, Tracer, Height Gauge, Pin Gauge, Optical comparator etc. to accomplish testing requirements.• Managed records of In-Process, First Off and Final Inspections. • Actively participated in Kaizen activities and provided continuous improvement suggestions to QA Manager.• Supported with Layered Process Audit (LPA).• Issued Nonconforming Material Tags while adhering to TS 16949 processes including nonconforming material, identification, and inspection processes.• Performed destructive testing and evaluation.• Assisted with GP-12 and Safe Launch Programs.• Helped Quality Engineers with corrective actions analysis.• Helped Quality Manager with TS16949 support work. Show more Show less
-
-
-
Larsen & Toubro
-
India
-
Construction
-
700 & Above Employee
-
Project Quality Engineer
-
Jun 2012 - May 2015
• Worked with Suppliers to address the Quality Issues and to upload the 8D response on Customer specific formats, customer portals. • Conducted meetings with suppliers, Cross functional teams to resolve the issues on timely manner.• Effectively participated and performed Quality Planning and prepared APQP, FMEA, PPAP, Control Plans, MSA, SPC etc.• Initiated and participated in Root cause and 8 D analysis and implemented corrective actions.• Prepared PPAP packages and obtained… • Worked with Suppliers to address the Quality Issues and to upload the 8D response on Customer specific formats, customer portals. • Conducted meetings with suppliers, Cross functional teams to resolve the issues on timely manner.• Effectively participated and performed Quality Planning and prepared APQP, FMEA, PPAP, Control Plans, MSA, SPC etc.• Initiated and participated in Root cause and 8 D analysis and implemented corrective actions.• Prepared PPAP packages and obtained customer approval to meet deadlines. Performed capability studies, layouts, and CMM data analysis.• Effectively managed suppliers through direct communication, performance evaluation, audits and APQP.• Worked on safe launches and controlled shipping for new programs. • Helped QA Manager to define, develop, and implement quality assurance practices and procedures, test plans and other QA assessments to adhere compliance with ISO 9001 BQMS. • Tracked supplier performances and issued scorecards.• Conducted Audits- Process and Product, helped QA manager with closing out the findings. • Facilitated the external Audit, worked on the findings to obtain closure on timely manner. • Reviewed accuracy of process documentation and made updates as and when required.• Check and approve quality checklist reports to include the audit findings.• Generates statistical reports on monthly basis for key measurement indicators.• Reviewed technical drawings for completeness and accuracy.• Operated AutoCAD to work on 2D/3D models and created prints. Show more Show less
-
-
Education
-
Conestoga College
-
Conestoga College
-
Maharishi Markandeshwar University, Mullana
-
Government Polytechnic Nilokheri, India
-
H. B.S.E
Community
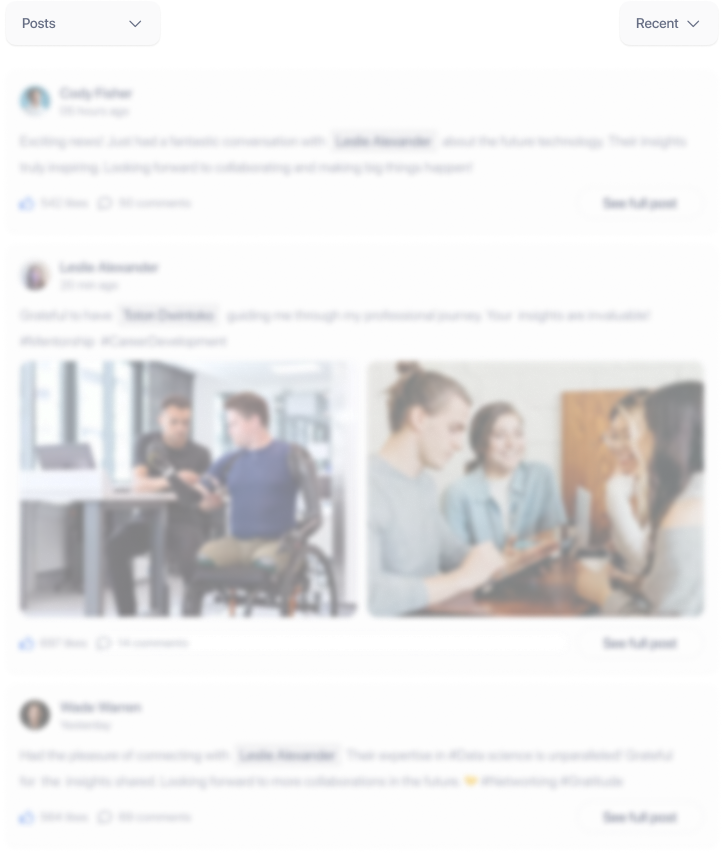