Subash R
Shift Manager at BLG Parekh Logistics- Claim this Profile
Click to upgrade to our gold package
for the full feature experience.
Topline Score
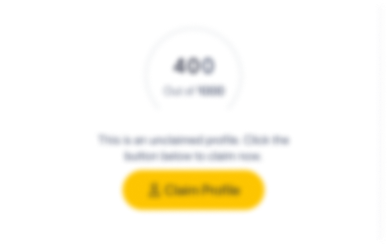
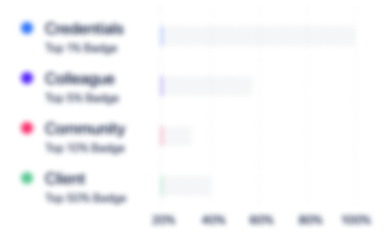
Bio


Experience
-
BLG Parekh Logistics
-
Transportation, Logistics, Supply Chain and Storage
-
1 - 100 Employee
-
Shift Manager
-
Jul 2019 - Present
To manage and drive the team, who involved in Warehouse Operations for better results in Productivity, Quality,On time Delivery, Inventory Management, Maintain 5S and material handling, and to co-ordinate with workforce to improve the Operations,Quality &meet company objectives. Manage the Overall CKD Operations with headcount of 150 Employees Responsible to report end to end Operations to Key account Manager on daily KPI’s . Reporting to the Pan India operations head on overall performance. Responsible to control Quality PPM within the stipulated norms. Responsibe to ensure achieving monthly target with in production cut-off time. Show less
-
-
-
Foxconn
-
Appliances, Electrical, and Electronics Manufacturing
-
700 & Above Employee
-
Senior Engineer
-
Feb 2018 - Jul 2019
Handling of 3000 SKUs with 45,000 Sq. ft. area of SMT, RM-Warehouse Managing the Overall WH Op’s through third party Customer& Support directly to Production -Kitting Ensure KPI or Meet on daily basis& review on Production meeting on daily basis Ensure No Orders delay should leads to Line Stop Evaluate the Op’s flow on Weekly basis and assign the Locations based on FSM data &Plan with respective of Projects & Models Manage the Mails / Phone calls from the supporting team &support to excute the urgentorders in on time Handled 800 Crores Inventory with through put value of 1200 crores per month Analysis the Transactions in SAP on Weekly basis with Respective of Plant & Storage Location Conduct the Training Programs inside the facilities Show less
-
-
-
UTi Worldwide (DSV A/S)
-
Denmark
-
Transportation, Logistics, Supply Chain and Storage
-
700 & Above Employee
-
Assistant Manager
-
Mar 2014 - Oct 2017
Managing the Inbound and Outbound Operation processes such as unloading, Receiving, Put away, Order placing, Picking, Palletizing, Vanning, Loading, Documentation and Dispatch. Maintaining optimal stock level to ensure timely availability of products. Ensure Customers KPI’s are met on day to day basis and reviewing with client on weekly, monthly and quarterly basis. Ensure Incoming Orders are dispatched in a FIFO basis, quarantine parts are dispatched in agreed ageing hours, pallets are stacked as per standards (BMH rule, Color Coding’s), In-house transactions and entries are charted as per SOP. Analyze the Orders andexecute the shipments according with Priority, Truck Utilization and Logistics Data. Coordinating the stock audits, cycle counts, Put away audit, Pick audit, Binface audit and Replenishment activities. Handling Customer Complaints, Transportaion Damage Losses(TDL)and involving in implementing Corrective and Preventive actions as required. Show less
-
-
-
Yusen Logistics (SAO Region) Co., Ltd.
-
Thailand
-
Transportation, Logistics, Supply Chain and Storage
-
700 & Above Employee
-
Executive
-
Mar 2012 - Feb 2014
Handling of 12,000 SKUs with 4,00,000 Sq. ft. of area(Renault Nissan PDC) Managing the Quality Inspection activities for Incoming Parts, Handling customer Complaints, Warehouse Operations, Maintain 3C/5S activities at Shop floor and Team Leader for Cross Functional Team. Preparing the Daily Quality report, Quality issue tracker, Claim Tracker, 5S activities report for Warehouse operation, Weekly audit Report, Weekly analysis report and Monthly Trend analysis for Incoming inspection and Customer Complaints. Co-ordinate with Operation team and involving in reduction of Customer Complaints and Control the level of PPM Submitting Corrective action and Preventive action Report to Customer for all claims related to Operation and Parts Quality through Problem solving method( 7 QC tools) Preparing One Point Lesson for new products, similar looking parts and display the image at in house area to avoid Wrong Picking Issues and wrong labeling issues Analyzing characteristics of product by studying the Drawing, Engineering specification of the product and explain the handling method of product to all workers- it helps to avoid claims and occurrence of part damage during operation at WH. Co-ordinate with Customer quality team and Involving in Supplier end visit. Coordinate with Packaging team and involve in Packaging developments. Show less
-
-
-
Khyungshin Industrial Motherson Ltd
-
Chennai Area, India
-
Graduate Engineering Trainee
-
Sep 2011 - Feb 2012
Leading the people to achieve the Dept. Objectives and Customer requirements. Implement manual inspection of circuit continuity Checker method (Buzzer Checking method) in Wiring Harness. Implement the Fuse Box Inspection method for Relay and Fuse Circuit Functions. Knowledge in Electric Circuit Routing. Co-ordinate with Production team involving in reduction of In- house PPM Preparation of Customer handling &Vendor handling Implementation of Kaizen for Non-conformance Maintaining of 3C&5S & Visual aids in shop Floor Preparation of Work standard and One Point Lesson for new product Analyzing of In-House and Customer PPM daily base Implementation of TQM activities Implementation of POKA YOKA for critical Parameters Handling of Customer audit and Internal Audit Verification of Finished Good Transfer Report (FGTR) and preparing PPM chart daily. Presenting Monthly Quality Status & Action plan to Top Management. Taking Corrective and preventive actions for customer complaints and In-House problems through the problem solving methods ( 7 QC Tools) Verification of Process Records. Implement continual improvement activities (KAIZEN) to make better result in productivity, quality, and safety, utilization of resources, detection system, and control of rejection. Show less
-
-
Education
-
Anna University
Bachelor of Engineering (BE), Electrical, Electronics and Communications Engineering -
NSVV Hr.Sec.School
HSC, Biology, Maths
Community
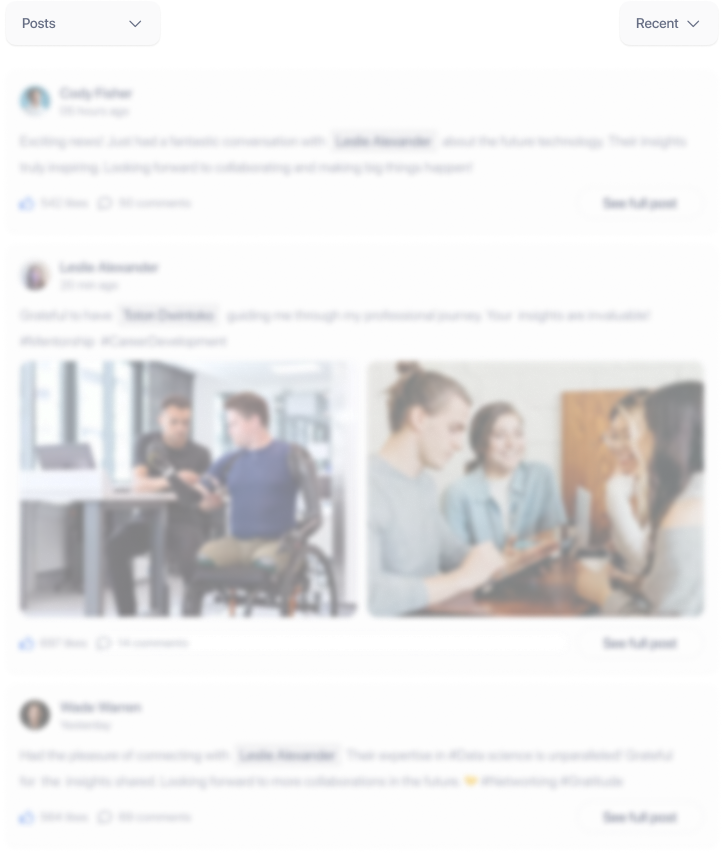