Stuart Unwin
Supplier Quality Engineer at ITM Power (LSE: ITM.L)- Claim this Profile
Click to upgrade to our gold package
for the full feature experience.
Topline Score
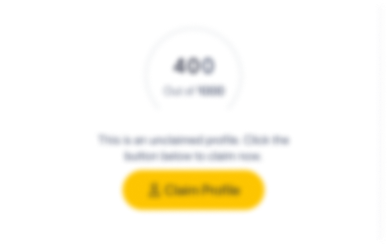
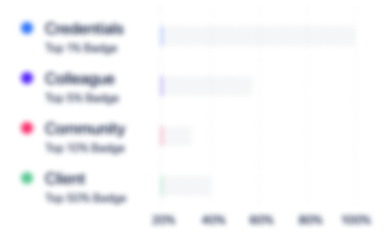
Bio


Credentials
-
Automotive Core Tools
Society of Motor Manufacturers and Traders (SMMT)Mar, 2018- Nov, 2024 -
IATF 16949:2016 Upgrade Training for 1st & 2nd Party Auditors
Society of Motor Manufacturers and Traders (SMMT)Nov, 2017- Nov, 2024 -
VDA 6.3:2016 Process Auditor
Society of Motor Manufacturers and Traders (SMMT)Sep, 2019- Nov, 2024 -
IRCA Certified ISO 14001:2015 Lead Auditor Training Course (A17903)
BSINov, 2016- Nov, 2024 -
VDA 6.3:2016 Process Auditor
Society of Motor Manufacturers and Traders (SMMT)Sep, 2016- Nov, 2024 -
ISO/TS 16949:2009 Lead Auditor Recertification Training for 1st & 2nd Party Auditors
Society of Motor Manufacturers and Traders (SMMT)Sep, 2014- Nov, 2024 -
VDA 6.3:2010 Process Auditor
Verband der Automobilindustrie (VDA) e.V.Sep, 2013- Nov, 2024 -
ISO/TS 16949:2009 Lead Auditor Training for 1st & 2nd Party Auditors
Society of Motor Manufacturers and Traders (SMMT)May, 2011- Nov, 2024 -
Internal Audit to ISO/TS 16949:2002
Total Quality Partnership LtdJun, 2008- Nov, 2024
Experience
-
ITM Power
-
United Kingdom
-
Services for Renewable Energy
-
200 - 300 Employee
-
Supplier Quality Engineer
-
Nov 2021 - Present
-
-
-
BAND-IT IDEX
-
United States
-
Industrial Machinery Manufacturing
-
1 - 100 Employee
-
Quality Engineer
-
Jan 2021 - Nov 2021
I joined the BAND-IT team to successfully help them attain accreditation to the automotive standard IATF 16949:2016 for their UK manufacturing site. Therefore; my main responsibility was to audit the Environmental/Quality Management System (EQMS) and all of the automotive products being manufactured on site to the following international standards: IATF 16949:2016, ISO 9001:2015 and ISO 14001:2015. From these audits; I generated my audit reports and discussed/reviewed my findings with the management team. Aiding with any root cause analysis and problem solving required for the audit findings. I completed a handful of annual revalidation PPAP submissions for current automotive customers. And I also aided the business in completing new initial PPAP submissions for new automotive customers. Show less
-
-
-
KOSTAL Group
-
Germany
-
Motor Vehicle Manufacturing
-
700 & Above Employee
-
Supplier Quality Engineer
-
Oct 2018 - Oct 2020
After a couple of years break from the supplier quality role, I decided to rejoin this team working with and helping develop our supply chain. I was responsible for ensuring our suppliers provide products that meet both our requirements and that of our customers.Driving improvements within our supply chain by utilising continuous improvement activities and my extensive experience planning and conducting audits. Working with our suppliers to highlight the benefits of implementing the opportunities for improvement found through my on-site auditing. Predominantly nearly all of the supplier audits I conducted was by using the VDA 6.3 process audit method. However there had been the odd occasion where I needed to incorporate IATF 16949 (includes ISO 9001) system audit approach into my audits at our suppliers.Through working with our suppliers I was able to highlight our high impact suppliers, especially for new project developments and support the PPAP in order to help guarantee a project flawless launch into production. With flawless launch in mind; this required me to review and approve all of our suppliers PPAP’s, calling upon APQP tools to support the project(s) where needed.As well as continuing to develop our suppliers through new project implementation, I also took the lead for the resolution of production quality concerns relating to our supply chain. This was achieved by working through 8D's and root cause analysis tools; Is-Is not method, Triple 5 Why, Ishikawa or Time Line Analysis.Even though I’d changed job roles from quality systems leader to supplier quality engineer, I was still responsible for conducting internal VDA 6.3 Process audits, IATF 16949 (includes ISO 9001) and ISO 14001 system audits along with supporting the team for our site IATF 16949 and ISO 14001 accreditation audits. Show less
-
-
Quality Systems Leader
-
May 2011 - Oct 2018
I was responsible for the Quality Management System "QMS" and to fulfil the company's requirement of achieving IATF 16949:2016 and ISO 14001:2015 accreditation. To help obtain the stated accreditations, I was a member of an international formed group by our headquarters for developing company audit requirements for accreditation transitions. I managed the internal audit management system along with the team of internal system and process auditors. I created our site audit schedules for IATF 16949 (includes ISO 9001), ISO 14001 and VDA 6.3 process or system based audits. I planned and conducted internal and external audits to the already stated standards including 5'S/process audits. This means I managed and reviewed all of the site audit findings (non-conformities and opportunities for improvement) and use problem solving methodology with the aid of root cause analysis tools to action the non-conformities. Each week I reported the status of our site audits and non-conformities to top management and held escalation meetings for audits or non-conformities should they go overdue.I was the site administrator for our core quality tool, which required me to coordinate with my colleagues both at our manufacturing plant and our headquarters for any updates or problems affecting the tool. Being the administrator of this core quality tool also required me to train our personnel on the use of tools such as Kostal 8D or Deviation Requests.To aid with the continual improvement of our manufacturing plant I developed and introduced Layer Process Audits "LPA" linked to the lean manufacturing principles of our site.I aided with customer on-site audits and conducted customer specific audit requirements such as Self Assessments when required. In the event of customer problems/escalations, I aided/visited Kostal sites around the world to audit the systems, processes or the implemented corrective actions. Show less
-
-
Supplier Quality Engineer
-
Jan 2008 - May 2011
I worked with our suppliers to ensure we received products that meet customer requirements. This would require visits to the suppliers to aid with problem solving using root cause analysis tools or review the implementation of the corrective actions. I presented the supplier 8D status during our morning production line meetings and created a cost recovery system for the non-conforming products received from our suppliers. I was responsible for the incoming inspection of our purchased parts whether this be functional, dimensional or visual checks. This meant I was also responsible for managing our supplier quarantine area, a location used for handling all non-conforming materials.My responsibilities also included to plan and conduct internal ISO/TS 16949 system audits (Includes ISO 9001) and 5'S lean manufacturing audits. This required me to review and close any system audit non-conformities or opportunities for improvement. Show less
-
-
-
Optare PLC
-
United Kingdom
-
Automotive
-
1 - 100 Employee
-
Student Engineer
-
2005 - 2006
This was my industrial placement, part of my university course. My job role was to aid the senior mechanical engineer on any issue within our manufacturing plant. I worked on the engine build assembly line all the way through to the engine installation to our vehicles. With this experience I was asked to produce two detailed engine build manuals for the Mercedes-Benz and MAN engines used within our vehicles. These manuals were used to aid with production operator training and help make the engine servicing and refit more efficient. I helped with problem solving any issues affecting our production assembly line (e.g. component failure) and also asked to redesign one of our vehicle chassis. Show less
-
-
-
Arrow Technical Services
-
United Kingdom
-
Appliances, Electrical, and Electronics Manufacturing
-
1 - 100 Employee
-
Production Technician
-
2001 - 2005
Worked within an electronic manufacturing area, assembling, programming and testing the Printed Circuit Board Assemblies "PCBA's"/ Products. Worked within an electronic manufacturing area, assembling, programming and testing the Printed Circuit Board Assemblies "PCBA's"/ Products.
-
-
Education
-
Sheffield Hallam University
Bachelor of Engineering with Honours, Mechanical and Automotive Engineering -
The Sheffield College
AVCE Engineering, Engineering Materials, Processes & Project, Design Development, Mechanical & Electronic Principles -
The Dronfield School
GCSE's, Design & Technology, Information Technology, Mathematics, Science, English Language, Geography
Community
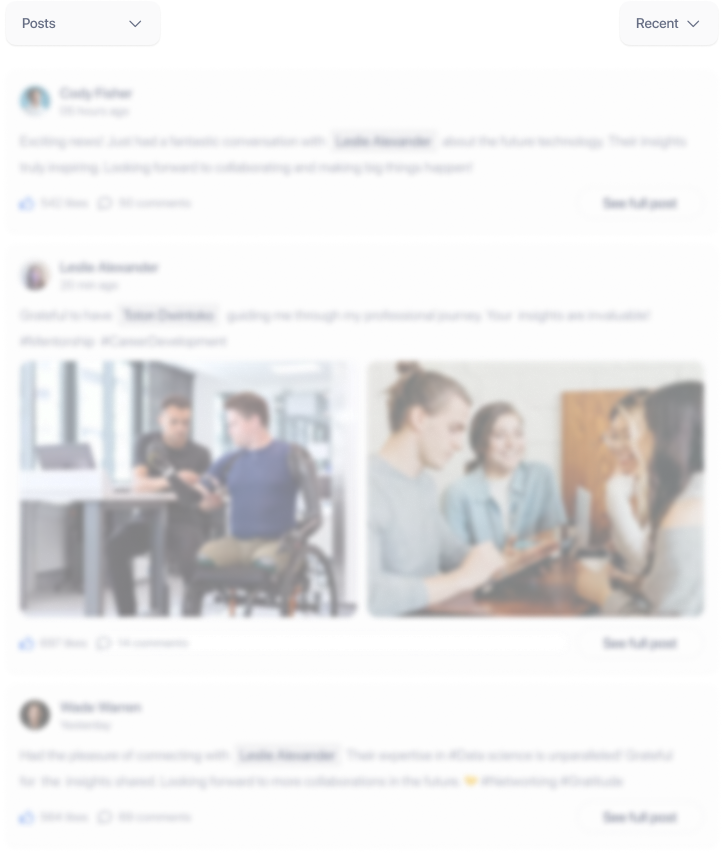