Stig-Gunnar Lundberg
Business Process Owner at mcare Sweden AB- Claim this Profile
Click to upgrade to our gold package
for the full feature experience.
-
English Professional working proficiency
-
Swedish Native or bilingual proficiency
-
German Elementary proficiency
Topline Score
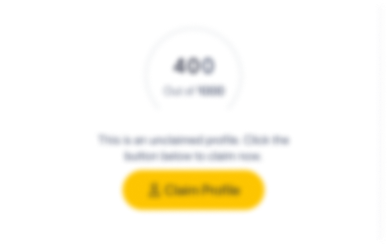
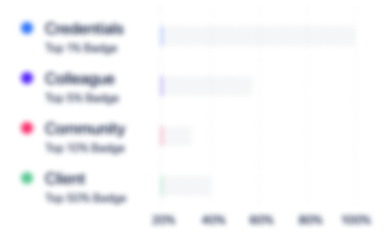
Bio


Experience
-
mcare Sweden AB
-
Sweden
-
IT Services and IT Consulting
-
1 - 100 Employee
-
Business Process Owner
-
Nov 2022 - Present
Responsible for developing and documenting processes linked to service delivery and related business systems (Fixably). Responsible for developing and documenting processes linked to service delivery and related business systems (Fixably).
-
-
-
-
Business Improvement Specialist
-
Nov 2020 - Dec 2022
Working on implementing a new data system and developing our processes. Responsible for our internal quality control and reporting.
-
-
Service Manager HHP
-
Jun 2019 - Nov 2020
Responsible for 4 workshops (two in Stockhom, one in Gothenburg and one in Malmö) that repairs mobilephones, tablets and laptops.
-
-
Quality Coordinator
-
Aug 2015 - Jun 2019
Responsible for back log management, including reporting of LTP (Long Time Pending) data to Samsung and analysis of repair data (Bounce and reporting quality). Follow-up of the spare parts and consumption an deliveries.
-
-
Team Manager
-
Feb 2015 - Aug 2015
Start and Operator of Samsung Walk in Service for mobile phones and tablets. Purchase and process planning, construction and deployment including operator for 6 months until new Team Manager was recruited.
-
-
-
Sony mobile
-
United States
-
Business Consulting and Services
-
Onsite Quality Manager
-
Oct 2013 - Oct 2014
Quality assurance of the repair process. Analyse final test data. Make your own quality checks. Reporting and collection of data on product quality in Excel. Time studies on the different stages of the repair process. Supported workshops remotely and on-site in other countries regarding improvement of their repair process. Quality assurance of the repair process. Analyse final test data. Make your own quality checks. Reporting and collection of data on product quality in Excel. Time studies on the different stages of the repair process. Supported workshops remotely and on-site in other countries regarding improvement of their repair process.
-
-
-
Mobilbyrån
-
Germany
-
Media Production
-
Service Engineer
-
Sep 2013 - Oct 2013
Repair Samsung phones Repair Samsung phones
-
-
-
-
Quality/ESD- Coordinator
-
Mar 2012 - Sep 2013
Assessment and Process Manager. Technical support for technicians. Mentors for production managers. Daily queue control and analysis of repair & final test data. Been driving quality assurance as per suppliers' requirements. Responsible for ESD and maintenance of measuring instruments. Assessment and Process Manager. Technical support for technicians. Mentors for production managers. Daily queue control and analysis of repair & final test data. Been driving quality assurance as per suppliers' requirements. Responsible for ESD and maintenance of measuring instruments.
-
-
-
-
Quality Coordinator
-
Dec 2010 - Mar 2012
Daily cue control and analysis of repair & final test data. Ensures that we are following the suppliers' requirements.Responsible for maintenance of measuring instruments.Technical support to technicians.
-
-
Supervisor
-
Sep 2006 - Dec 2010
Contact person for Nokia. Production KAM for Sony Ericsson. Assessments and process manager. Technical support to technicians. Daily cue control and analysis of repair & final test data. Ensures that we are following the suppliers' requirements.
-
-
-
-
Service Department Manager
-
Mar 2003 - Jul 2006
Responsible for Nokia department (including NCC). Had staff responsibility for 19 people. Responsible for supplier contacts. Been a driving force in quality assurance engineer. Nokia's requirements. Scheduled for spare parts. Responsible for technical equipment. Responsible for Nokia department (including NCC). Had staff responsibility for 19 people. Responsible for supplier contacts. Been a driving force in quality assurance engineer. Nokia's requirements. Scheduled for spare parts. Responsible for technical equipment.
-
-
-
-
Service Department Manager
-
2003 - 2006
Responsible for the Nokia department (incl. NCC). Had personnel responsibility for 22 people, including salary and development talks. Responsible for supplier contacts. Been driving quality assurance as per Nokia's requirements. Scheduled for spare parts stock. Responsible for technical equipment. Responsible for the Nokia department (incl. NCC). Had personnel responsibility for 22 people, including salary and development talks. Responsible for supplier contacts. Been driving quality assurance as per Nokia's requirements. Scheduled for spare parts stock. Responsible for technical equipment.
-
-
Education
-
Fyrisskolan, Uppsala
Gymnasieingenjör, El-Tele
Community
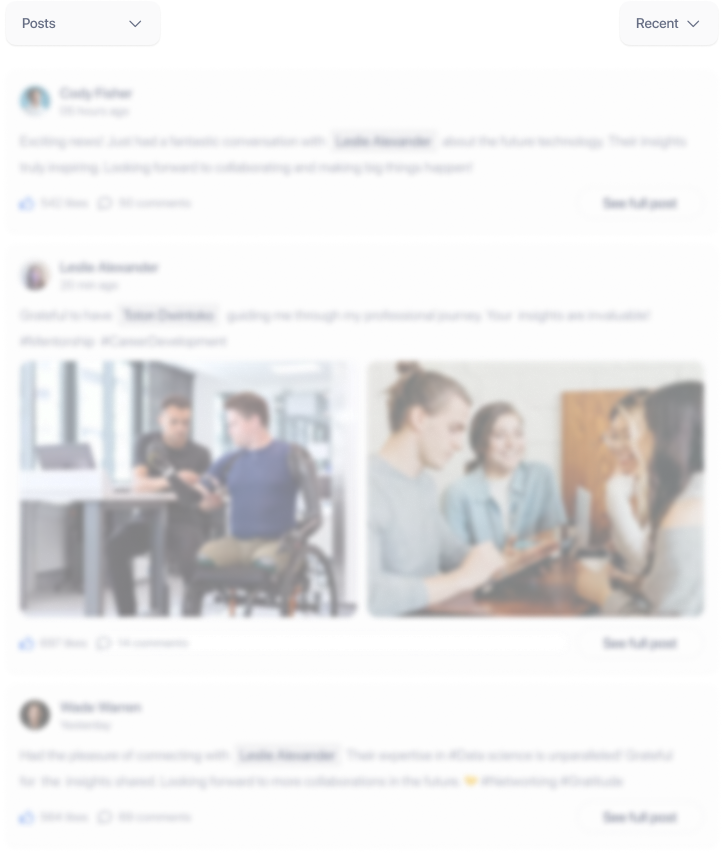