Steven Barrow
Director at Facet Manufacturing (UK)- Claim this Profile
Click to upgrade to our gold package
for the full feature experience.
Topline Score
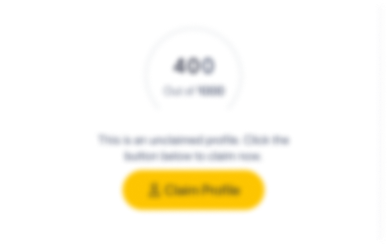
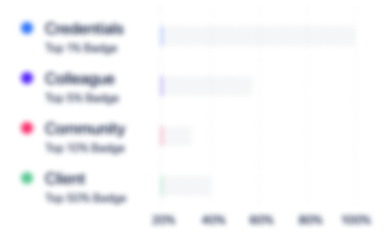
Bio

Joe Starkie
Steven,s forte is building really effective teams. He possesses great personal insight which enable him to play each team member to their strength,s. He is so good at this that he even uncovers skills in people that even they were unaware of. Coaching and coaxing them out of their comfort zones to achieve above previous expectations. To any company looking to grow and improve the capability of work teams and staff I cannot recommend Steve highly enough.

Robert Mahan
Steve worked for me for over 8 years starting as a production operator but was soon promoted through the business in a very short period of time to the position of line manager. During the time Steve worked for me his personality and ethic of work shone through becoming a great asset to any team i gave him to Manage. His professional manner of managing people and process has built him a great knowledge of manufacturing processes and procedures shone through on many of the projects he managed for me. His attention to detail and dogged approach at ensuring all i's were dotted and t's crossed meant that I was confident that no matter what issues he came across would be re solved in a timely manner to ensure that the process would run as smoothly as possible to ensure that all his production targets were met. during the time that steve worked for me he would always be looking for ways to improve the process , procedures, and his teams skills,during this time Steve was instrumental in changing our surface mount change over procedures to reduce Our change over times by 6 hrs which resulted in increasing are production output by of 45%. I would highly recommend Steve to any company

Joe Starkie
Steven,s forte is building really effective teams. He possesses great personal insight which enable him to play each team member to their strength,s. He is so good at this that he even uncovers skills in people that even they were unaware of. Coaching and coaxing them out of their comfort zones to achieve above previous expectations. To any company looking to grow and improve the capability of work teams and staff I cannot recommend Steve highly enough.

Robert Mahan
Steve worked for me for over 8 years starting as a production operator but was soon promoted through the business in a very short period of time to the position of line manager. During the time Steve worked for me his personality and ethic of work shone through becoming a great asset to any team i gave him to Manage. His professional manner of managing people and process has built him a great knowledge of manufacturing processes and procedures shone through on many of the projects he managed for me. His attention to detail and dogged approach at ensuring all i's were dotted and t's crossed meant that I was confident that no matter what issues he came across would be re solved in a timely manner to ensure that the process would run as smoothly as possible to ensure that all his production targets were met. during the time that steve worked for me he would always be looking for ways to improve the process , procedures, and his teams skills,during this time Steve was instrumental in changing our surface mount change over procedures to reduce Our change over times by 6 hrs which resulted in increasing are production output by of 45%. I would highly recommend Steve to any company

Joe Starkie
Steven,s forte is building really effective teams. He possesses great personal insight which enable him to play each team member to their strength,s. He is so good at this that he even uncovers skills in people that even they were unaware of. Coaching and coaxing them out of their comfort zones to achieve above previous expectations. To any company looking to grow and improve the capability of work teams and staff I cannot recommend Steve highly enough.

Robert Mahan
Steve worked for me for over 8 years starting as a production operator but was soon promoted through the business in a very short period of time to the position of line manager. During the time Steve worked for me his personality and ethic of work shone through becoming a great asset to any team i gave him to Manage. His professional manner of managing people and process has built him a great knowledge of manufacturing processes and procedures shone through on many of the projects he managed for me. His attention to detail and dogged approach at ensuring all i's were dotted and t's crossed meant that I was confident that no matter what issues he came across would be re solved in a timely manner to ensure that the process would run as smoothly as possible to ensure that all his production targets were met. during the time that steve worked for me he would always be looking for ways to improve the process , procedures, and his teams skills,during this time Steve was instrumental in changing our surface mount change over procedures to reduce Our change over times by 6 hrs which resulted in increasing are production output by of 45%. I would highly recommend Steve to any company

Joe Starkie
Steven,s forte is building really effective teams. He possesses great personal insight which enable him to play each team member to their strength,s. He is so good at this that he even uncovers skills in people that even they were unaware of. Coaching and coaxing them out of their comfort zones to achieve above previous expectations. To any company looking to grow and improve the capability of work teams and staff I cannot recommend Steve highly enough.

Robert Mahan
Steve worked for me for over 8 years starting as a production operator but was soon promoted through the business in a very short period of time to the position of line manager. During the time Steve worked for me his personality and ethic of work shone through becoming a great asset to any team i gave him to Manage. His professional manner of managing people and process has built him a great knowledge of manufacturing processes and procedures shone through on many of the projects he managed for me. His attention to detail and dogged approach at ensuring all i's were dotted and t's crossed meant that I was confident that no matter what issues he came across would be re solved in a timely manner to ensure that the process would run as smoothly as possible to ensure that all his production targets were met. during the time that steve worked for me he would always be looking for ways to improve the process , procedures, and his teams skills,during this time Steve was instrumental in changing our surface mount change over procedures to reduce Our change over times by 6 hrs which resulted in increasing are production output by of 45%. I would highly recommend Steve to any company

Credentials
-
NEBSM
National Education Board of Supervisory Management
Experience
-
Facet Manufacturing (UK)
-
United Kingdom
-
Appliances, Electrical, and Electronics Manufacturing
-
1 - 100 Employee
-
Director
-
Aug 2022 - Present
-
-
-
Diamond Electronics Ltd
-
United Kingdom
-
Appliances, Electrical, and Electronics Manufacturing
-
1 - 100 Employee
-
Group Quality Manager
-
Mar 2018 - Present
-
-
-
SciLabware Limited
-
United Kingdom
-
Computer Software
-
Production Supervisor
-
Feb 2017 - Jan 2018
-
-
-
Scholler Allibert
-
France
-
Investment Management
-
Production Manager
-
Dec 2012 - Oct 2016
• Implemented Lean manufacturing into a large, complex 24/7 moulding & assembly operation to enable continuous improvement (kaizen) and elimination of waste (muda). • Achieved a cost reduction of £37k in 12 months by reducing Kanban inventory • Improved tool change times by 85% through the implementation of a successful SMED (Single - Minute Exchange of Dies) programme. • Established daily risk assessment reporting resulting in a reduction by 10% of H&S incidents. • Set clear quality standards to achieve production plan OTIF performance targets. • Reviewed Standard Operating Procedures implementation improvement program to increase adherence. • Established continual review of staffing and capacity planning to achieve and maintain operational performance • Implemented register system reducing temporary staff costs. • Directly managed teams of permanent and agency staff (circa 40 direct reports) • Root Cause analysis and implementation of corrective action reduction of product rejection by 1% Show less
-
-
-
RSBP
-
United States
-
Defense and Space Manufacturing
-
1 - 100 Employee
-
Production manager
-
Sep 2008 - Aug 2012
• 26% reduction in direct labour costs by undertaking detailed review of through put timings. • Reduced on line inventory by 32% by undertaking Value Stream Mapping to improve process flow throughout the business. • Increased efficiency of edge banding activity by 25% by undertaking a Kaizen study of the process. • Established and led a 5Y problem solving team to resolve known historical defects resulting in a £20k saving on the previous year. • Established robust resource and capacity plans to manage employment of temporary labour at peak periods. Show less
-
-
-
Rieter Automotive
-
Switzerland
-
Motor Vehicle Manufacturing
-
1 - 100 Employee
-
Team Leader
-
Sep 2006 - Sep 2008
• Improved tool change times by 60% through the implementation of a successful SMED (Single – Minute Exchange of Dies) programme. • Implemented a QCDSM (Quality Cost Delivery Safety Morale) programme. • ISO 9001 quality standards maintained by consistent auditing. • Perpetual inventory system implemented to ensure traceability of all materials on line. • Leading, developing and motivating staff by challenging and supporting them. • Balanced equipment, lines and manage plant to meet production requirements. • Developed standardised operational procedures (SOPs) to improve individual and team performance. • Monitored and measure 5s performance by consistent auditing. • Organised effective and robust training for new and existing team members. • Fostered a culture of continuous improvement through 5 Y Problem solving and implementation of corrective action plans. Also researching best practice and adopting new ideas • Introduced daily audits to maintain good Health and Safety record Show less
-
-
-
-
Team Leader
-
May 2005 - Sep 2006
• Achieve all QCDSM targets. ISO 9001 ISO 1401. Through robust audits and regular quality training • Effective utilisation of plant and materials through daily preventative maintenance plan. • KPI s measured and maintained against agreed targets. • Supported to other teams to facilitate integration of activities. • Active member of a 5s team implementing standardisation across the factory. • Lead the identification, analysis and resolution of problems to ensure minimum interruption of the teams work. • Enable high standards of Health and Safety through audits. Show less
-
-
-
Celestica
-
Canada
-
Manufacturing
-
700 & Above Employee
-
Line Manager
-
Jan 1996 - Dec 2004
Celestica Limited.$10Bn Electronic manufacturing services. Providing end to end product life cycle solutions. Reporting to both Customer Operations Manager and Europe-North Division Technical Engineering Director. Key Responsibilities included: • Specifying and supporting strategies and new processes for New Product Introduction and volume builds. • Management of line operations, processes cycle times/ line utilisation. • Presentation operational information at management reviews. • Adherence to process and quality control systems. 99.9% achieved. • Quality management including corrective action plans. Housekeeping and visual management. • Control of materials and consumables. • Control of Operational Expenditure including headcount budget. • Seamless transfer of production to low cost geographies’. • People management. Including training development, health and safety, employment law compliance. Show less
-
-
Education
-
Blessed William Southern
Community
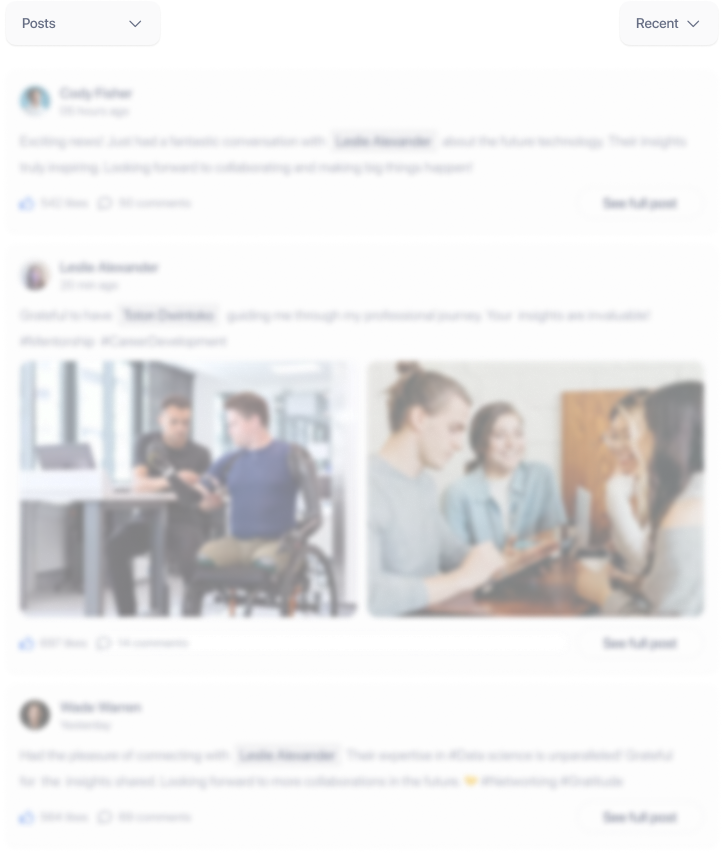