Steve Smith
Production Manager at Perigee Manufacturing Company, Inc.- Claim this Profile
Click to upgrade to our gold package
for the full feature experience.
-
English -
Topline Score
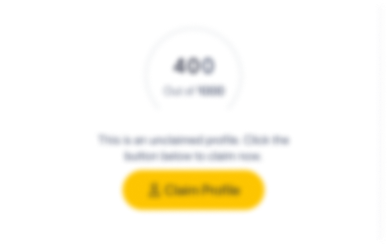
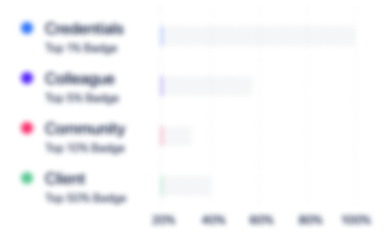
Bio


Experience
-
Perigee Manufacturing Company, Inc.
-
United States
-
Aviation and Aerospace Component Manufacturing
-
1 - 100 Employee
-
Production Manager
-
Oct 2018 - Present
-
-
-
-
Sales Consultant
-
Apr 2017 - Jun 2018
-
-
-
Ohio Screw Products, Inc.
-
United States
-
Manufacturing
-
1 - 100 Employee
-
Estimating Engineer
-
Aug 2015 - Jul 2016
• Quote all incoming jobs to determine best process and cycle times as well as pricing information• Troubleshoot production and machining problems on the floor • Quote all incoming jobs to determine best process and cycle times as well as pricing information• Troubleshoot production and machining problems on the floor
-
-
-
PTR Group; American Cap Company, ACCI Industries and PTR Tool & Plastics LLC
-
United States
-
Plastics Manufacturing
-
1 - 100 Employee
-
Coupler Project Manager
-
Jul 2011 - Jan 2015
• Managed all facets of a startup screw machine department manufacturing hydraulic fittings.• Purchased all necessary equipment for department, both primary and support.• Hired and trained all employees in production methods, quality procedures, machine safety and housekeeping. Disciplined if necessary up to and including dismissal.• Designed and manufactured all tooling, making what could be made in-house, outsourcing the balance.• Scheduled all production and personnel to meet customer delivery goals.• Final inspection of all out-going product as well as shipment of finished product and inventory control.In Early 2014, the company changed its business model, dissolving the screw machine department and beginning to produce couplers for the oil and gas industries. I assumed control of the project in April 2014 achieving several key goals.• Managed department growth from 8 to 65 employees covering three shifts.• Streamlined the entire process by purchasing equipment which enabled the company to bring several operations back in-house saving the company approximately 70% on manufacturing costs.• Improved overall production from 2100 pcs per month in April to over 21,000 pcs per month by December, raising monthly revenue from approximately $100K to nearly $1 million.• Controlled manufacturing and overhead costs by taking control of all purchasing for the department. • Scheduling of all personnel and production.• Documentation of all parts production, scrap, shipments to and from outside processes and final shipment of finished product to customer.
-
-
-
-
Director of Operations
-
Nov 2007 - Nov 2010
• Assumed control of the entire operation at our Osseo, MI facility in Nov. 2007 with goal of relocating the plant to our primary location in York, PA. by Sept 2008.• Accomplished goal of relocation of plant in May 2008, 4 months ahead of schedule.• Assumed control of York facility in June 2008 with responsibilities including purchasing, planning and scheduling of jobs and personnel, quoting, lay outs, quality, hiring and training of new personnel, shipping schedules, outside processing and inventory control.• Disciplinary actions if necessary up to and including discharge.• Implementation of Lean initiatives to control costs and quality. • Developed very good working relationships with and had direct contact with our customers.
-
-
-
-
Business Owner
-
Nov 2003 - Nov 2007
• Home improvement business concentrating on vinyl siding, roofing, porches and decks and small additions.• Interior work including drywall hanging and finishing, painting, flooring and copper plumbing. • Home improvement business concentrating on vinyl siding, roofing, porches and decks and small additions.• Interior work including drywall hanging and finishing, painting, flooring and copper plumbing.
-
-
-
Premier Hydraulics
-
United States
-
Machinery Manufacturing
-
1 - 100 Employee
-
Plant Manager
-
Jan 2000 - Mar 2003
• Managed a startup screw machine operation (Klaric Forge and Machine) a subsidiary of Premier. • Responsible for the inception and implementation of the screw machine operation including all primary and support equipment purchases.• Hiring and training of personnel in production and quality methods, safety and housekeeping.• Disciplinary responsibilities as necessary.• Quoting and layout of jobs.• Tool design and manufacture. Make in-house when possible, outsource the balance. • Set up, operation, maintenance and repair of machines.• Purchasing of raw materials and support materials.• Inventory and Quality control.
-
-
Education
-
Kent State University at Trumbull
Bachelor of Business Administration (BBA), Business Administration and Management, General -
Kent State University at Ashtabula
Associate Degree, Business Management
Community
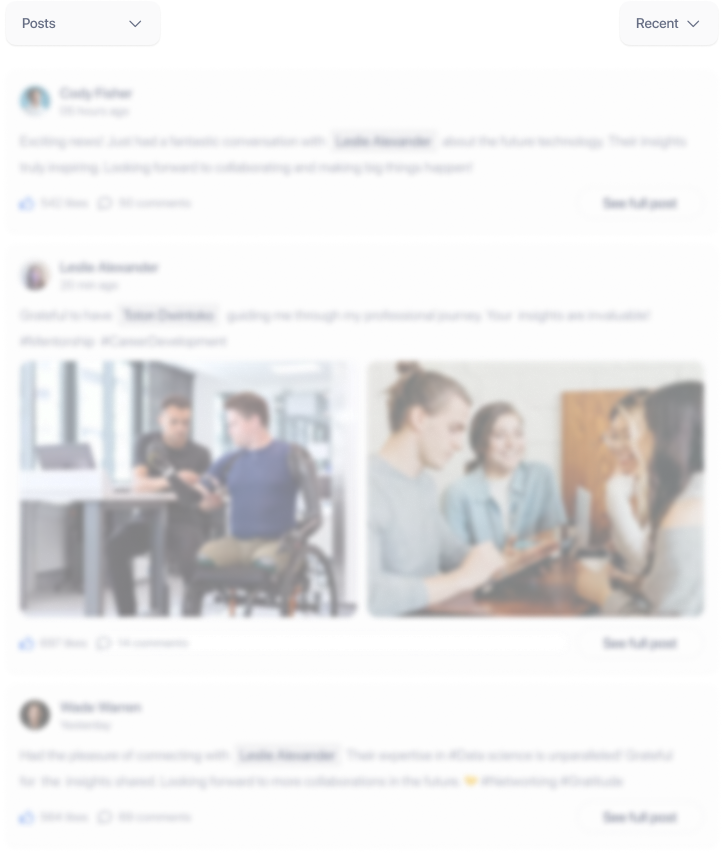