Steve Roberts
Business Development Manager at forteq UK- Claim this Profile
Click to upgrade to our gold package
for the full feature experience.
Topline Score
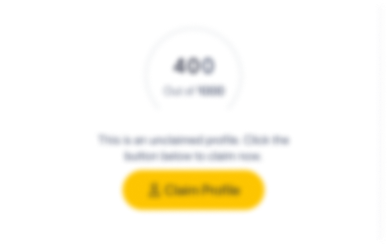
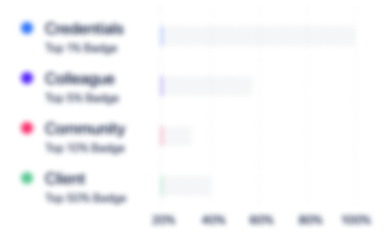
Bio

Gary Beach
If you need an experienced Engineer who knows how to mould and tool-up complex components for injection moulding engineering plastics then Steve is your man. He is also very knowledgeable about high volume production cell units and how to optimise the process to ensure that cost effective solutions are delivered without compromising on quality. He is approachable and always a pleasure to work with.

Alan Bennett
A genuinely good guy with good knowledge of the plastics industry and I hope to work with Steve again in the future.

Gary Beach
If you need an experienced Engineer who knows how to mould and tool-up complex components for injection moulding engineering plastics then Steve is your man. He is also very knowledgeable about high volume production cell units and how to optimise the process to ensure that cost effective solutions are delivered without compromising on quality. He is approachable and always a pleasure to work with.

Alan Bennett
A genuinely good guy with good knowledge of the plastics industry and I hope to work with Steve again in the future.

Gary Beach
If you need an experienced Engineer who knows how to mould and tool-up complex components for injection moulding engineering plastics then Steve is your man. He is also very knowledgeable about high volume production cell units and how to optimise the process to ensure that cost effective solutions are delivered without compromising on quality. He is approachable and always a pleasure to work with.

Alan Bennett
A genuinely good guy with good knowledge of the plastics industry and I hope to work with Steve again in the future.

Gary Beach
If you need an experienced Engineer who knows how to mould and tool-up complex components for injection moulding engineering plastics then Steve is your man. He is also very knowledgeable about high volume production cell units and how to optimise the process to ensure that cost effective solutions are delivered without compromising on quality. He is approachable and always a pleasure to work with.

Alan Bennett
A genuinely good guy with good knowledge of the plastics industry and I hope to work with Steve again in the future.

Experience
-
forteq UK
-
United Kingdom
-
Plastics Manufacturing
-
1 - 100 Employee
-
Business Development Manager
-
Apr 2014 - Present
forteq Group offer world class engineering, manufacturing and assembly services for high volume production of technical automotive plastic components. Headquartered in Switzerland, forteq have PIM manufacturing plants in UK, Central Europe, China and USA totaling 200 mould machines and our own in-house dedicated toolmaking facility in Suzhou China. forteq supply plastic parts globally to the Automotive sector in high volume, functional components and assemblies often unseen on the vehicle, but performing a critical role. Highly focused on technical automotive applications, forteq provide solutions to challenging components often using engineered polymers, forteq's engineering team can lead the development and implementation of plastic components and assemblies delivering high volume supply utilising the latest in robotics technology, twin shot or over-moulding processes. My role is to drive and implement the strategic plan, building greater presence in our market to demonstrate the technical excellence possessed within the group in our "state of the art" facilities. We commit ourselves to maintaining world class quality in all of our components and all that we do. The UK plant holds IATF-16949, ISO9001-2015 & ISO14001-2015 accreditation. Show less
-
-
-
MGS Technical Plastics Ltd
-
United Kingdom
-
Plastics Manufacturing
-
1 - 100 Employee
-
Technical Sales Manager
-
May 2012 - Apr 2014
MGS Technical & MGS Medical Plastics produce plastic injection components for a wide range of industries such as Hygiene, Leisure, Cookware, Electronics, Automotive and Medical. MGS offer in-house tooling as well as UK and far east options, providing technical support for NPD projects including DFM analysis, Moldflow, project plans and PPAP documentation. MGS Technical & MGS Medical Plastics produce plastic injection components for a wide range of industries such as Hygiene, Leisure, Cookware, Electronics, Automotive and Medical. MGS offer in-house tooling as well as UK and far east options, providing technical support for NPD projects including DFM analysis, Moldflow, project plans and PPAP documentation.
-
-
-
Mtool
-
Oldham, United Kingdom
-
Business Development Manager
-
Jun 2011 - May 2012
Grow customer base using industry contacts, trade magazines and exhibitions for prototype and production mould tool projects. Provide technical support, DFM analysis, cost effective tooling strategies and project manage tooling projects through to production approval, and beyond. Increase and develop business opportunities with existing customers and improve customer service to meet quality requirements and timing plans, thus ensure all projects are delivered proficiently. Grow customer base using industry contacts, trade magazines and exhibitions for prototype and production mould tool projects. Provide technical support, DFM analysis, cost effective tooling strategies and project manage tooling projects through to production approval, and beyond. Increase and develop business opportunities with existing customers and improve customer service to meet quality requirements and timing plans, thus ensure all projects are delivered proficiently.
-
-
-
Eaton
-
Ireland
-
Appliances, Electrical, and Electronics Manufacturing
-
700 & Above Employee
-
Category Manager EMEA
-
May 2010 - May 2011
EMEA regional category manager. Supply Chain Position reporting to HQ in Bonn following the Eaton acquisition of Klockner Moeller. Managed Tooling Procurement, Surface Treatment, Wire & Connectors and Stampings supplier categories for Eaton Electric division. This role highly focussed on cost out projects, supplier reduction / consolidation and provide NPI technical support expertise and guidance on supplier selection.
-
-
Supplier Development and Projects Engineer
-
Feb 2007 - Apr 2010
Provide technical support in regard to Quality Processes, PPAP approval, Business Systems, Quality / Process Audits and Lean activities to the Eaton supply base. Assist in European Operations NPD projects in regard to Tooling, PIM supplier selection, raw material selection, cost-out opportunity and resourcing projects.
-
-
Technical Team Leader
-
Feb 2005 - Feb 2007
Responsible for team of tooling and moulding engineers who support production tooling and moulding facilities at outsourced supply partners in Eastern Europe and Asia. High volume product range of MEM switchgear was the platform to make significant savings via better engineered tooling, use of lower cost polymers and elimination of quality and reliability issues.
-
-
Toolmaker - Quality Engineer - Tooling Engineer - Toolroom Supervisor
-
Jun 1989 - Jan 2005
Engineering Apprenticeship specializing in Mould Tools and Stamping Tools 1989 until 1993 then Toolmaker until 1997. I moved into a quality engineer role for 3 years and then became Tooling Engineer in 2000 where I passed Injection Moulding Level 3 at BPTA Telford. In 2003 I became Toolroom Supervisor responsible for 5 toolmakers, 400 mould tools and 250 stamping tools in one of the largest moulding facilities in the UK with 86 Mould machines.
-
-
Education
-
Oldham College of Technology
HNC, Mechanical Engineering
Community
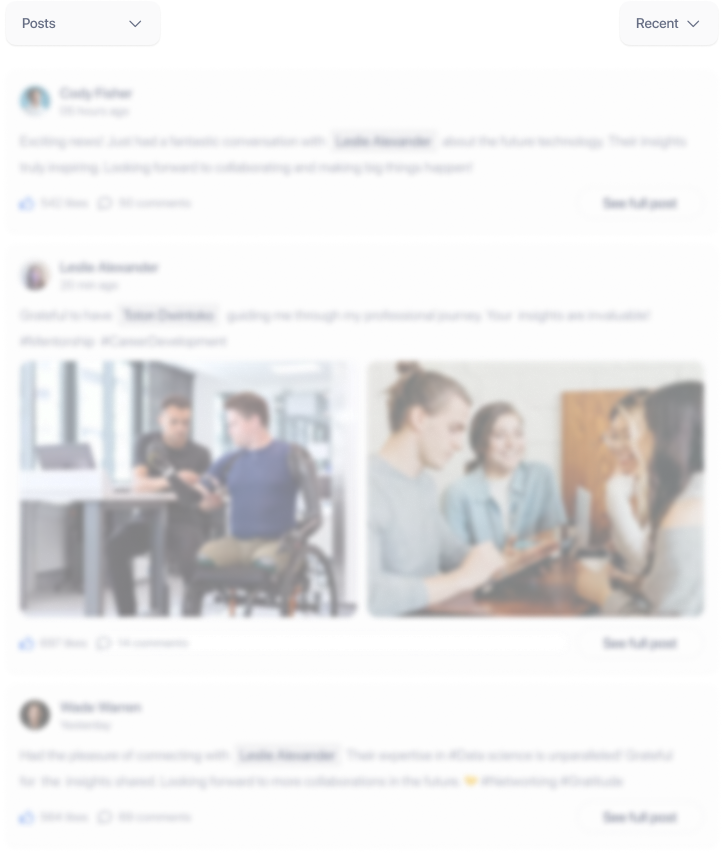