
Steve Jenkins
Sales and Service Manager at ELE International- Claim this Profile
Click to upgrade to our gold package
for the full feature experience.
Topline Score
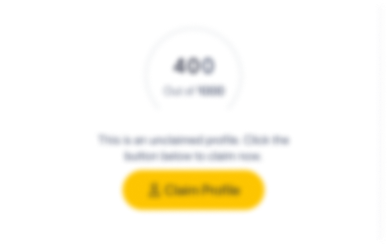
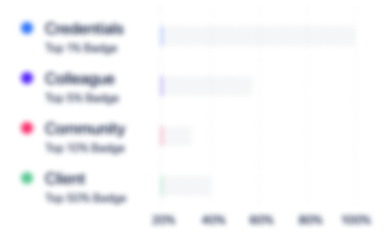
Bio

Martin Barr CEng FIMechE CMgr FCMI
Steve is a very knowledgeable engineer. Highly experienced in his trade and always strives to achieve the best possible outcome in all tasks he carries out. Well respected by his team and he is an effective and contentious manager.

Martin Barr CEng FIMechE CMgr FCMI
Steve is a very knowledgeable engineer. Highly experienced in his trade and always strives to achieve the best possible outcome in all tasks he carries out. Well respected by his team and he is an effective and contentious manager.

Martin Barr CEng FIMechE CMgr FCMI
Steve is a very knowledgeable engineer. Highly experienced in his trade and always strives to achieve the best possible outcome in all tasks he carries out. Well respected by his team and he is an effective and contentious manager.

Martin Barr CEng FIMechE CMgr FCMI
Steve is a very knowledgeable engineer. Highly experienced in his trade and always strives to achieve the best possible outcome in all tasks he carries out. Well respected by his team and he is an effective and contentious manager.

Experience
-
ELE International
-
United Kingdom
-
Machinery Manufacturing
-
1 - 100 Employee
-
Sales and Service Manager
-
Feb 2022 - Present
-
-
-
Pall Water
-
United States
-
Renewable Energy Semiconductor Manufacturing
-
1 - 100 Employee
-
Field Services Engineer
-
Oct 2020 - Feb 2022
Responsible for delivering packaged and bespoke water treatment solutions to industrial and municipal customers in Europe, the Middle East & Africa including:SLA managementSupervision of 3rd party contractorsPlanning of preventive and reactive maintanceConsulting with customers on system improvements and upgrades. Responsible for delivering packaged and bespoke water treatment solutions to industrial and municipal customers in Europe, the Middle East & Africa including:SLA managementSupervision of 3rd party contractorsPlanning of preventive and reactive maintanceConsulting with customers on system improvements and upgrades.
-
-
-
ELE International
-
United Kingdom
-
Machinery Manufacturing
-
1 - 100 Employee
-
Senior Field Service Engineer
-
Mar 2017 - Oct 2020
Employed as Field Service Engineer. Initially responsible for calibration, installation & commissioning of local and international customers equipment. Role expanded rapidly to include providing training solutions both on-site and at ELE bespoke training facility to global customer base.Within first year of employment was engaged in providing remote support to customers worldwide on equipment troubleshooting and technical support identifying correct equipment for customers’ requirements. Further responsibility was granted shortly after to assess and authorise warranty requests against ELE for global customer base. This additional role quickly evolved to include the generation of high-quality sales leads by providing customers with consultative solutions.Under direction from Senior management was engaged to complete Gap Analysis projects and ensure that working practices complied to UKAS procedures and complied with regulatory standards, leading to later appointments as trusted lead and key contributor to multiple departmental and company wide projects:• Designed and Authored Service Manuals for new products with distributors and customers in mind, allowing for limited technical skillsets (Project Lead).• Reduced cost and wastage incurred due to purchase of multiple IEC power leads per equipment sold due to regional requirements (Project Lead).• Worked with potential suppliers to modernise flagship product hydraulic power pack and allow greater functionality. Stretch goal included implementation of Youngs Modulus testing of concrete samples.• Sourced alternative hydraulic components to replace key components in flagship product due to reliability and build quality concerns.
-
-
-
Heavy Parts
-
Australia
-
Truck Transportation
-
Service Engineer
-
Mar 2016 - Mar 2017
Employed as Hydraulic Test & Service Engineer. Responsible for fault analysis, power curve calculations & servicing of hydraulic pumps and motors from a range of manufacturers including Bosch Rexroth, Parker, Samhydraulik, Sauer Danfoss & Kawasaki. Employed as Hydraulic Test & Service Engineer. Responsible for fault analysis, power curve calculations & servicing of hydraulic pumps and motors from a range of manufacturers including Bosch Rexroth, Parker, Samhydraulik, Sauer Danfoss & Kawasaki.
-
-
-
Dana Industrial
-
United States
-
Industrial Machinery Manufacturing
-
300 - 400 Employee
-
Service Engineer
-
Sep 2014 - Mar 2016
Employed as Hydraulic Service Engineer working in partnership with customers on complete range of pumps (closed & open loop), valves (multi slice & CETOP) & motors (Fixed & variable displacement axial pistons). Employed as Hydraulic Service Engineer working in partnership with customers on complete range of pumps (closed & open loop), valves (multi slice & CETOP) & motors (Fixed & variable displacement axial pistons).
-
-
-
-
Field Service Engineer
-
Jan 2014 - Jul 2014
Employed as a Mechanical Field Service Engineer maintaining product range of raw rubber processing equipment. Employed as a Mechanical Field Service Engineer maintaining product range of raw rubber processing equipment.
-
-
-
-
Aircraft Maintenance Supervisor
-
Aug 2001 - Jan 2014
Entered military service as apprentice technician specialising post academic phase in mechanical aircraft systems. Post apprenticeship was employed in section tasked with developing the Apache project from manufacturer delivery to first operational deployment. On promotion to supervisor worked on full range of Army Rotary wing fleet in both front end and depth support in a range of challenging environments.>Managed maintenance tasks and priorities whilst servicing an aircraft.>Provided 100% supervision and technical mentoring to junior technicians during maintenance and in-use testing.>Administered supervision for aircraft fitters during mechanical servicing>Given educational presentations on aircraft systems and adherence to Military Aviation Authority regulations.>Implemented management and maintenance support to the Army Air Corps whilst deployed in locations such as Norway, Afghanistan or Kenya >Assessed and improved upon existing procedures and routines under ISO9001 Quality Assessment routines as head of Technical Communications department.>Experienced in 1st and 2nd line management & maintenance of airframes and systems.>Implemented inspection expertise in techniques such as Vibration analysis, Non-Destructive test level 1>Provided Environmental Conditioning System inspection, servicing and fault diagnosis cover for department.>Involved in trial and development of Apache airframe from initial Release to Service to first operational deployment cycle. Instrumental in correct diagnosis & repair scheme planning of hydraulic/pneumatic system crossover faults.>Assisted 1st line units with their maintenance burden including operational requirements as part of a small external support team.>Controlled Servicing Equipment use, serviceability log books and administrated servicing regime.>Dealt with receipt of urgent technical information and promulgation of signals received.
-
-
Education
-
Yeovil College
Higher National Diploma, Aeronautics/Aviation/Aerospace Science and Technology, General -
ATIL
City & Guilds, Environmental Control Technologies/Technicians -
Joint Arms NDT School
BS.EN.5576, Non Destructive Test Techniques -
Vosper Thornycroft
Modern Apprenticeship, Aeronautical/Aerospace Engineering Technology/Technician -
Vosper Thornycroft
Bachelor of Technology (BTech), Aeronautical/Aerospace Engineering Technology/Technician -
Bideford College
GCSE's, Various
Community
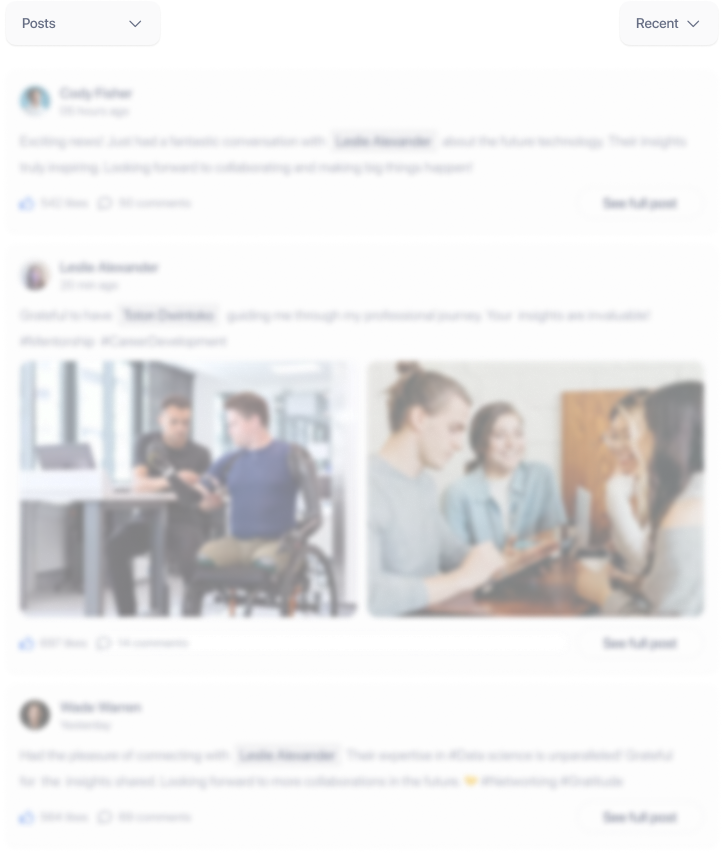