Steve Durham
Vice President of Technical Operations at GW Lisk- Claim this Profile
Click to upgrade to our gold package
for the full feature experience.
Topline Score
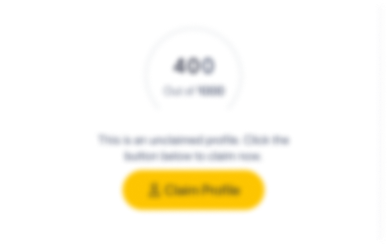
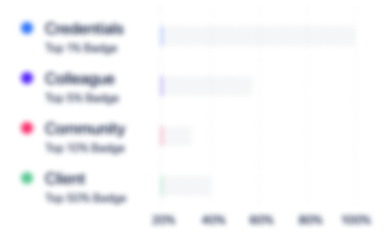
Bio


Experience
-
GW Lisk
-
Costa Rica
-
Appliances, Electrical, and Electronics Manufacturing
-
100 - 200 Employee
-
Vice President of Technical Operations
-
Aug 2021 - Present
Lead and direct the activities of the Quality, Manufacturing Engineering and Continuous Improvement teams to meet KPI improvement targets. Focus on operational excellence and process stability to drive bottom line results. Lead and direct the activities of the Quality, Manufacturing Engineering and Continuous Improvement teams to meet KPI improvement targets. Focus on operational excellence and process stability to drive bottom line results.
-
-
-
ITT Goulds Pumps
-
United States
-
Industrial Machinery Manufacturing
-
400 - 500 Employee
-
Director of Operations, Seneca Falls Foundry & Facilities Maintenance
-
Dec 2019 - Aug 2021
Director of operations for a cast iron foundry producing cast iron components for large centrifugal pumps and Director of Maintenance for all production equipment, buildings and grounds. The site includes approximately 1M square feet of production space and includes an iron foundry, a full CNC machine shop, finishing operations (i.e. sand blast & paint), assembly, test & packaging.
-
-
Director Of Operations, ANSI Focus Factory
-
Jun 2018 - Dec 2019
Director of Operations for ANSI Value Stream. Responsible for all facets of manufacturing operations for a $130M centrifugal pump manufacturer.
-
-
Director OpEx, Mfg. Engineering & Facility Maintenance
-
Jan 2012 - Jun 2018
Director of Operational Excellence, Manufacturing Engineering, and Facilities Maintenance with a professional staff of 25 managers, superintendents, supervisors, engineers and lean facilitators.• 2nd level manager of maintenance team consisting of 35 skilled tradesmen supporting a 1M ft2 production facility with budget oversight of $18-20M. Trades included: electricians, carpenters, plumbers, mechanics, systems repair, security and janitorial (contract).
-
-
-
Daikin Applied Americas
-
United States
-
Industrial Machinery Manufacturing
-
700 & Above Employee
-
Director Of Quality Assurance
-
Jan 2011 - Dec 2011
Director of Quality 2011-2012• Director of Quality for $110M HVAC manufacturing business• Responsible for all facets of quality assurance and warranty• Interfaced with customers to resolve field complaints• Reduced #1 warranty cost by $.5M annually by utilizing DMAIC process to reduce refrigerant leaks
-
-
Manufacturing Engineering, Maintenance & OpEx Manager
-
Feb 2003 - Dec 2010
Manager of manufacturing engineering, operational excellence, facilities and maintenance with a professional staff of 14 direct reports.• Manager of maintenance team of 17 hourly associates supporting a 450,000 ft2 HVAC production facility with an annual operating budget of $2.5M• Responsible for development and implementation of $2-3M annual capital investment plan.• Responsible for annual cost reduction projects of $2-3M.• Responsible for developing and maintaining operational standards for all facets of the manufacturing operation.• Responsible for process and productivity improvements in all manufacturing areas through implementation of lean manufacturing (Toyota Production System) techniques.• Implemented a lean transformation strategy that reduced WIP inventory by 60%, floor space by 25% and improved productivity by 20% Show less
-
-
Senior Lean Manufacturing Engineer
-
Feb 2001 - Feb 2003
•Implement improvement strategies to support divisional goals.•Responsible for process and productivity improvements in assembly, steel and copper manufacturing areas through implementation of lean manufacturing techniques.
-
-
-
Eaton
-
Australia
-
Legal Services
-
1 - 100 Employee
-
Production Supervisor
-
Aug 1999 - Dec 2001
•First-line supervisor over 39 union (IBEW Local 2084) employees involved in machining and assembly of custom electrical control equipment.. •Responsible for production, safety & health, housekeeping, quality, productivity, customer service relations, NC machine maintenance, cross-training, and operating budgets. •First-line supervisor over 39 union (IBEW Local 2084) employees involved in machining and assembly of custom electrical control equipment.. •Responsible for production, safety & health, housekeeping, quality, productivity, customer service relations, NC machine maintenance, cross-training, and operating budgets.
-
-
-
-
Project Specialist, Improvement Operations Office
-
Jul 1994 - Jul 1997
• Responsible for implementation of the Crouse-Hinds Business Process throughout the division. • Team leader on 35 Improvement (Kaizen & SMED) events over an 18 month period. • Improved flow, reduced cost, reduced lead time, reduced inventory and eliminated wastes on a wide variety of products and processes. • Led improvement events at (5) division locations outside of Syracuse. • Responsible for implementation of the Crouse-Hinds Business Process throughout the division. • Team leader on 35 Improvement (Kaizen & SMED) events over an 18 month period. • Improved flow, reduced cost, reduced lead time, reduced inventory and eliminated wastes on a wide variety of products and processes. • Led improvement events at (5) division locations outside of Syracuse.
-
-
Education
-
State University of New York Empire State College
Bachelor's degree, Operations Management and Supervision -
Alfred State College - SUNY College of Technology
Associate of Science - AS
Community
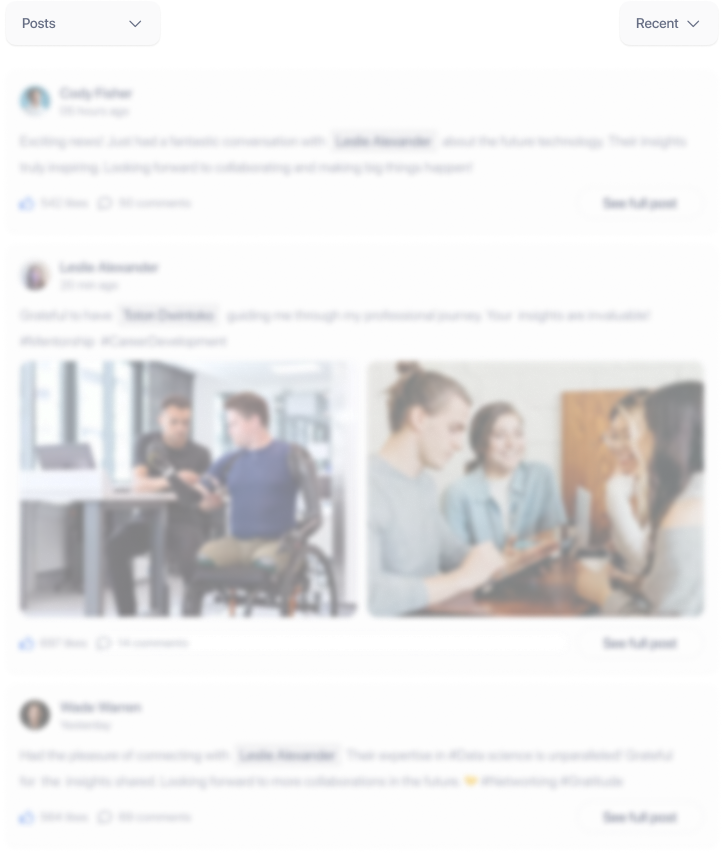