Steve Chinn
Operations Manager at Bischof + Klein- Claim this Profile
Click to upgrade to our gold package
for the full feature experience.
Topline Score
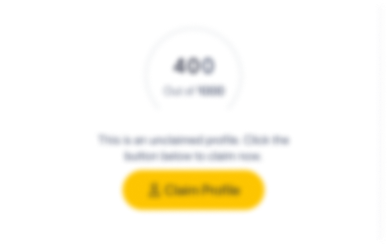
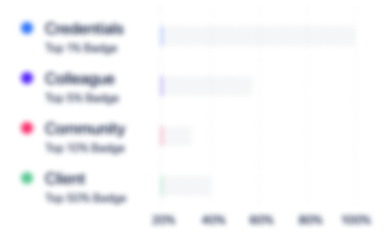
Bio

Bruno Claeys
I've worked together with Steve for more than 5 years and I experienced him as an enthusiastic and positive-minded manager. He is a good listener and takes your feedback fully into account. Steve has brought stability into his organization and achieved year after year, together with his team, to improve the overall performance of the Kettering factory.

LinkedIn User
Steve has been a wonderful colleague for me for 5 years: he is a real believer in the sustainable development philosophy. Under his strong leadership, he managed to realize with his team astonishing reductions in waste, energy, water, waste water ratio’s, making sustainable development much more than just a employer branding or marketing story.

Bruno Claeys
I've worked together with Steve for more than 5 years and I experienced him as an enthusiastic and positive-minded manager. He is a good listener and takes your feedback fully into account. Steve has brought stability into his organization and achieved year after year, together with his team, to improve the overall performance of the Kettering factory.

LinkedIn User
Steve has been a wonderful colleague for me for 5 years: he is a real believer in the sustainable development philosophy. Under his strong leadership, he managed to realize with his team astonishing reductions in waste, energy, water, waste water ratio’s, making sustainable development much more than just a employer branding or marketing story.

Bruno Claeys
I've worked together with Steve for more than 5 years and I experienced him as an enthusiastic and positive-minded manager. He is a good listener and takes your feedback fully into account. Steve has brought stability into his organization and achieved year after year, together with his team, to improve the overall performance of the Kettering factory.

LinkedIn User
Steve has been a wonderful colleague for me for 5 years: he is a real believer in the sustainable development philosophy. Under his strong leadership, he managed to realize with his team astonishing reductions in waste, energy, water, waste water ratio’s, making sustainable development much more than just a employer branding or marketing story.

Bruno Claeys
I've worked together with Steve for more than 5 years and I experienced him as an enthusiastic and positive-minded manager. He is a good listener and takes your feedback fully into account. Steve has brought stability into his organization and achieved year after year, together with his team, to improve the overall performance of the Kettering factory.

LinkedIn User
Steve has been a wonderful colleague for me for 5 years: he is a real believer in the sustainable development philosophy. Under his strong leadership, he managed to realize with his team astonishing reductions in waste, energy, water, waste water ratio’s, making sustainable development much more than just a employer branding or marketing story.

Experience
-
Bischof+Klein
-
Germany
-
Packaging and Containers Manufacturing
-
100 - 200 Employee
-
Operations Manager
-
Oct 2022 - Present
-
-
-
Meridian Foods
-
Food and Beverage Services
-
1 - 100 Employee
-
Site Manager
-
Sep 2021 - Aug 2022
-
-
-
Grainger & Worrall
-
United Kingdom
-
Industrial Machinery Manufacturing
-
100 - 200 Employee
-
Continuous Improvement Manager
-
Dec 2019 - Aug 2021
-
-
-
Coveris UK
-
United Kingdom
-
Packaging & Containers
-
300 - 400 Employee
-
Operational Excellence Manager
-
Jan 2019 - Nov 2019
-
-
-
Wipak
-
Finland
-
Packaging and Containers Manufacturing
-
300 - 400 Employee
-
Continuous Improvement Manager
-
May 2016 - Jan 2019
-
-
-
ABP UK
-
Food Production
-
300 - 400 Employee
-
General Manager
-
May 2015 - Mar 2016
RETAIL GENERAL MANAGER ABP Food Group, Shrewsbury Total P&L responsibility for all Packing Operations on site, achieved substantial customer growth supplying Beef and Lamb mince, burgers, dice and steaks in multiple packaging formats on automated lines. A labour intensive highly complex chilled operation, orders received and product packed and despatched the same day due to short shelf life, a true FMCG operation. Main achievements: Restructured all main meetings to use scorecards and data to drive performance e.g SIC, Daily and Weekly KPI meetings. Implemented monthly departmental ‘deep dive’ reviews to focus on key improvements and establish ‘one’ Team all working in the same direction with clear objectives. KPI’s best in class. Labour cost now lowest in Group. Achieved by detailed standard manning control and driving OEE using Lean Driver and SIC meetings. Developed and implemented a Training system to ensure compliance and drive performance. Piloted Lean projects saving £100k annually and developed a site wide Lean plan to further engage the team and improve problem solving to drive performance. Commissioned two new steak lines; reduced labour costs, improved OEE, improved yield and reduced giveaway saving over £250k per year. Performance improvements have enabled capacity to increase in line with the customers rapid growth. A weekly Packing record was achieved in January 16 , a clear sign of excellent teamwork and Leadership. H&S higher on the agenda by implementing Near Miss reporting.
-
-
-
Mondelēz International
-
United States
-
Food and Beverage Manufacturing
-
700 & Above Employee
-
Site Manager
-
Mar 2014 - May 2015
Total responsibility for all Cadburys hot chocolate and cocoa drinks packing in a highly traditional unionised environment. Seasonal packing demand profile with an annual value of approx. £35M , achieved: Developed robust Management systems to monitor and improve beverage KPI’s. Improved Communication & Team work and through strong Leadership provided focus to develop a culture of continuous improvement. Developed a 3 year Packing roadmap to significantly reduce costs based on capital investment and Operational changes. Increased average Packing line OEE by 10% , utilised short interval control and visual shop floor data to engage the teams, saving over £100k per year. Labour costs reduced by approx. £200k per year by successfully implementing robotic palletisers. Increased focus on waste and control systems to drive down waste costs. End of year stock count had a positive variance – never previously achieved. Developed a complaints reduction trend by using Root cause analysis (5 Why’s, Fishbone..) for Quality issues. H&S higher on the agenda, >50% increase in near miss reporting and risk assessment’s completed with actions to reduce further risk. Absence below 3% by focusing on RTW’s Increased monthly GMP score by over 50%. All NPD launches delivered on time.
-
-
-
Bokomo Foods UK Ltd.
-
United Kingdom
-
Food and Beverage Manufacturing
-
1 - 100 Employee
-
Group Operations Manager
-
Aug 2012 - Mar 2014
Total responsibility for the Peterborough and Wellingborough cereal manufacturing sites having a turnover of £35m per year and achieved the following: Developed robust Management systems to monitor and improve both site KPI’s. Improved Communication & Team work and through strong Leadership provided focus to change a site losing money to become profitable. Engaged the team to understand the importance of good GMP and implemented robust new procedures, training and sign off to achieve an M&S Silver audit , the previous audit rating was red. (Gold not awarded by M&S on first audit after a red) Successful Tesco, M&S, Lidl, Aldi and Dole launches on time in full with very positive customer feedback. Significantly improved the relationships with all key customers to further develop the business resulting in 20% growth in 2013. Negotiated and successfully implemented site wide shift changes to increase production capacity by 20% and save £240k per year in labour costs. Reduced site packing waste by 50% in 12 months. Implemented OEE for the packing lines and Short Interval Control and visual shop floor data to engage the teams and improve efficiencies. H&S higher on the agenda, near miss reporting and risk assessments with follow up and corrective actions to reduce the risks on site.
-
-
-
Gerber Juice Company Ltd
-
Bridgwater
-
Business Unit Manager interim
-
Nov 2011 - Jun 2012
Total responsibility for 15 production lines (UHT and chilled cartons) operating 24/7 with an annual turnover of approx. £400M, achieved the following: Within 2 months increased the 6 week average OEE for 15 lines by 10% , equivalent to a capacity increase of 40M Tons per year. Costs significantly below budget (exceeded business expectations) Developed a waste reduction culture , waste reduced by over £1m per year Developed a reducing complaints trend H&S higher on the agenda , no LTA this year.
-
-
-
Alpro
-
Belgium
-
Food Production
-
500 - 600 Employee
-
Site Manager
-
Apr 2006 - Oct 2011
Proven track record as a General Manager - £75M/year turnover Fresh and UHT drinks manufacturing 24/7 supplying Tesco, Sainsburys, Asda, Morrisons , Coop etc. Developed the Site Management Team to a world class standard. Successfully implemented new management tools via a pilot project and developed a site roadmap to create a culture of continuous improvement e.g. 6 Sigma DMAIC, Ishikowa, 5 Whys, Kaizen, 5S, Training and Standard Operating Procedures (SOP’s). Site KPI results the best in Alpro Full cost centre control , setting the budget and delivering Overheads kept at 2006 level through efficiency improvements Finalist 2010 for Food Manufacturing Excellence award UHT OEE results 'Above World Class' - Tetra Pak
-
-
-
UNIQ
-
Shropshire
-
Business Unit Manager
-
Apr 2005 - Apr 2006
Total operational responsibility for 250 employees producing Yoghurt, Fromage Frais and Cottage Cheese producing 250 T per week (value £0.5m/week). • Successfully changed all M&S yoghurts to probiotic on time to increase sales by 25%. • Improved direct labour utilisation saving £100k per year by implementing shift patterns requiring less paid hours per week without reducing capacity. • Identified >£0.5m per year direct labour savings by automating manual operations. • Achieved a 1% Service improvement to M&S (averaged > 99%) by improving yoghurt process control. • Reduced customer complaints from >20ppm to <10ppm. • Developed and implemented operational KPI’s to measure performance in all key areas. The trends identified improvement actions which improved OEE, quality and reduced waste. • Made continuous GMP improvements (month on month) which were acknowledged and recognised by M&S. • Significantly reduced the H&S risk by focusing on key risk assessments and follow up actions. • Improved Food hygiene and H&S standards which were recognised by internal and external audits.
-
-
-
Allied Bakeries | part of Associated British Foods plc
-
United Kingdom
-
Food and Beverage Manufacturing
-
700 & Above Employee
-
Site Manager at AB's largest flagship site (600 employees)
-
Feb 2003 - Apr 2005
-
-
Education
-
INSEAD - International Business School - Leadership
Pst MBA, Leadership -
University of Derby
MSc, Advanced Manufacturing Management -
The University of Birmingham
BSc, Metallurgy & Materials Science
Community
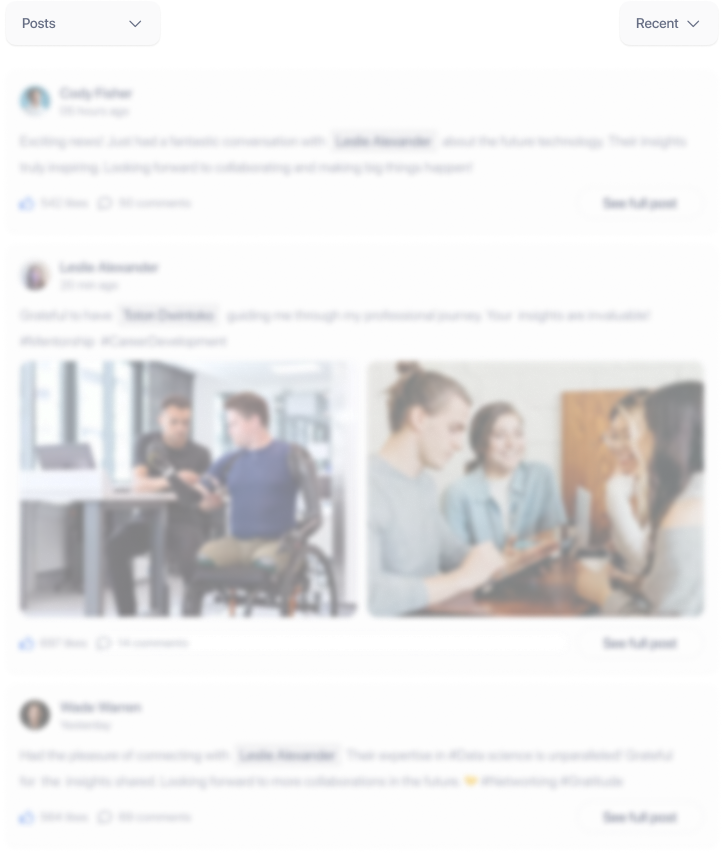