Stephen R.
Director of Fulfillment at The Jay Group- Claim this Profile
Click to upgrade to our gold package
for the full feature experience.
Topline Score
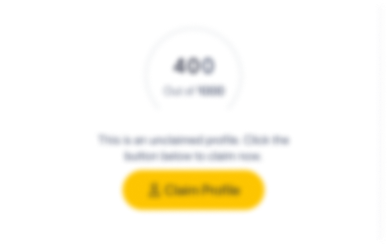
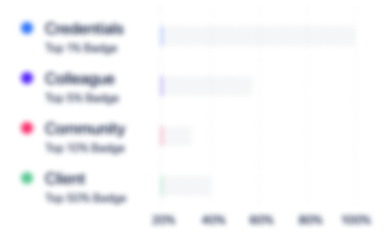
Bio


Experience
-
Jay Group
-
Transportation, Logistics, Supply Chain and Storage
-
100 - 200 Employee
-
Director of Fulfillment
-
Apr 2017 - Present
Oversee daily operations of a 200k Sq. Ft fully automated E-commerce fulfillment center. Champion all Lean projects and Kaizen events which has rendered $400k in fixed overhead and $375k in variable cost reductions . Implemented 5s within the E-commerce fulfillment center. Implemented BI which provides real time information on the floor for productivity, order and line forecast to actual, and time of completion so fulfillment staff are updated as to when work for the day will be completed. Manage labor and strategic planning via customer forecast and historical data. Part of the implementation team for Manhattan WMS 2017. Show less
-
-
-
-
Supply Chain Consultant
-
Feb 2014 - Present
Provide clients in the retail industries of DSD, B2B, B2C, and E-commerce dealing with everyday problems of reducing bottom line cost and top line growth with viable supply chain solutions. Consult with small and medium companies in Central PA and MD on best practices to improve distribution and logistics capabilities. Identified and implemented savings by way of operations layout and design planning, logistics network optimization, facility lease negotiations, carrier negotiations, and capital spend ROI projects. Developed strong relationship with clients by addressing tactical and strategic issues/concerns with sustainable solutions. Improved outbound order accuracy to brick-and-mortar stores by working through client customer complaints via Gemba walks and process mapping of the order process to identify root cause within the operations. Show less
-
-
-
Woodstream Corporation
-
United States
-
Manufacturing
-
200 - 300 Employee
-
Director of Distribution & Logistics
-
Feb 2008 - Jan 2014
Managed a cost center of $30 million in global distribution and $20 million in transportation for a mid-size retail CPG company. Managed 6 salary direct reports and 80 indirect reports out of season and 300 in season for 3 DC’s of 1m Sq.ft of distribution space and 5,000 SKU’s. Managed $1m in annual cost savings initiatives to reduce distribution, and inventory carrying cost by championing CI projects and leading distribution PITs. Re-engineered the North America distribution footprint from 1.5m Sq.ft to 1m Sq.ft while sales increased from $120m annually to $320m and SKU count increased by 150%. Designed, implemented, and managed an automated RF E-Commerce fulfillment center in North America that produced $16m in organic growth with an annual volume of 500k in small parcel packages and 3m in UPS spend. Reduced customers fines related to shipment shortages from $1m to $400k by process mapping, SOP development, employee training to SOP’s, improving WMS capabilities, and working directly with customers. Lead 3 successful acquisitions which increased top line growth of $160 million while maintaining to a 1m Sq.ft footprint. Enhanced customer order accuracy to 99% and reduced customer fines by $500k through CI projects and implementation of a proprietary WMS. Implemented SMART goals for the distribution network by measuring customer service, followed by safety, individual productivity, and financial performance. Show less
-
-
-
FMC Corporation
-
United States
-
Chemical Manufacturing
-
700 & Above Employee
-
Global Distribution Manager
-
Mar 2004 - Feb 2008
Successfully managed a startup of a new 200,000 sq. ft. North America Distribution Center which reduced distribution outsourcing cost by $2.6 million annually. Oversaw a combined cost center budget of $26 million in global distribution for a fortune 500 Pharmaceutical company. Managed 1 North America start up DC and 6 additional DC’s across the globe along with 3PL warehouse sites. Improved the inventory accuracy at the North America DC from 92% in 2004 to 99.99% in 2007, by implementing effective inventory initiatives and cultivating inventory best practices into the culture. Improved fill rate from 94% to 99% with improved inventory accuracy and the rollout of a new SAP WMS. Member of a lean team that identified a cost savings in reducing Finished Goods O/H inventory by $30m by adjusting lead times from domestic and international plants, adjusting safety stock through supply chain modeling, and by establishing ROP's for active SKU's and working with plant production on reducing cycle time. Show less
-
-
-
Schneider
-
United States
-
Transportation, Logistics, Supply Chain and Storage
-
700 & Above Employee
-
Regional Logistics Manager
-
May 2002 - Feb 2004
Oversaw cost center budget of $5.5 million in transportation and $2.5 million in 3PL outsourcing. Managed onsite 3PL provider to include budget and KPI performance. Managed $140 million in finished goods inventory distribution and $114 million in JIT purchase parts management. Accomplished $200k in transportation and logistics hard savings and $500k in soft savings over an eighteen-month period. Managed KPI metrics of OTD and order accuracy for inbound raw material and outbound commercial shipments, cost per mile, cost per case for 3PL coupled with the intensity to drive metrics across the critical functions delivering strong operating margins. Participated in a plant Six Sigma project that resulted in $500k in savings by reducing material handling labor, material handling equipment, plant inventory, and establishing a new plant floor layout. Show less
-
-
-
APL
-
United States
-
Maritime Transportation
-
700 & Above Employee
-
Operations Manager III
-
Jun 1998 - May 2002
Managed 500k Sq. ft fully automated E-Commerce distribution facility and transportation infrastructure that featured more than $12 million in specialized hardware/software, order handling and specialized equipment chosen specifically for speed for customers such as Overstock.com and Gear.com. Managed 3 direct managers and 300 indirect reports over a multi shift DTC operation that shipped 3m small parcel packages to DTC customers. Other responsibilities included: P&L, DSO, capital assets and acquisitions, price negotiations, creating a positive working staff, and exceeding facility key performance indicators. Increased profit margin from 14% to 17% for FY 99 and increased profit margin from 13% to 21% for FY 00. Show less
-
-
-
Marine Corps Recruiting
-
Armed Forces
-
700 & Above Employee
-
Logistican
-
Dec 1991 - May 1998
-
-
Education
-
Penn State University
Master of Business Administration (MBA) -
University of Tennessee, Knoxville
BS, Logistics and Transportation
Community
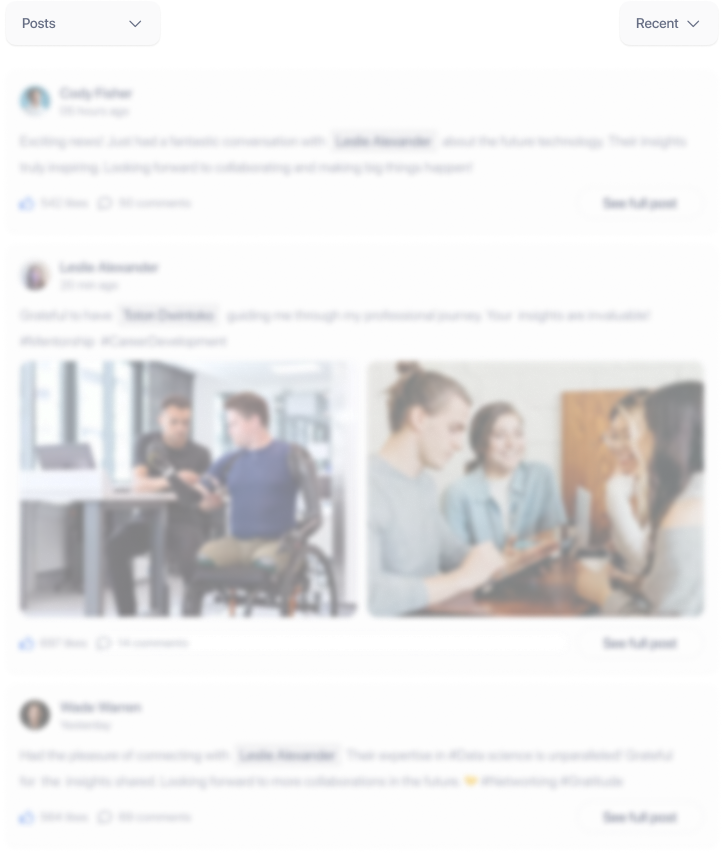