Stephen Jacobs
Operations Manager at Vitrazza- Claim this Profile
Click to upgrade to our gold package
for the full feature experience.
Topline Score
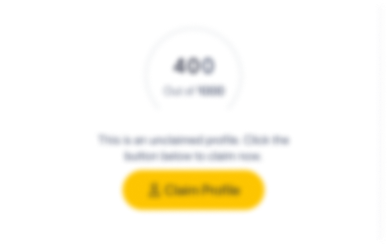
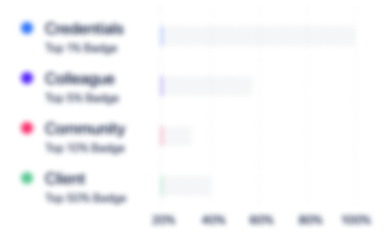
Bio


Experience
-
Vitrazza
-
United States
-
Furniture and Home Furnishings Manufacturing
-
1 - 100 Employee
-
Operations Manager
-
2023 - less than a year
Golden, Colorado, United States
-
-
-
-
Independent Contractor
-
Nov 2019 - May 2021
Golden, Colorado, United States I joined a friend and a fellow Purdue engineer in a new business venture. Together we have worked to grow M&M Contracting LLC from a two-person sideline to a growing business with an emphasis on quality residential construction and customer satisfaction.
-
-
-
ZIP-PAK an ITW Company
-
Packaging and Containers Manufacturing
-
1 - 100 Employee
-
Manufacturing Manager
-
2016 - Sep 2019
Ottawa, Illinois I oversaw 65 staff and 8 direct reports across Production, Shipping, and Receiving in a 24/7 plastic extrusion operation. I direct the operator development program. Ensure ongoing compliance with SQF and Food Safety requirements, as well as plant safety rules and regulations are being followed. • 2019: Leading the Safety Committee • 2018: Exceeded set goal for scrap by 1.69%. • 2018: Managed plant without direct supervision by operations, maintenance, process engineering, … Show more I oversaw 65 staff and 8 direct reports across Production, Shipping, and Receiving in a 24/7 plastic extrusion operation. I direct the operator development program. Ensure ongoing compliance with SQF and Food Safety requirements, as well as plant safety rules and regulations are being followed. • 2019: Leading the Safety Committee • 2018: Exceeded set goal for scrap by 1.69%. • 2018: Managed plant without direct supervision by operations, maintenance, process engineering, and quality managers all the while improving our OEE and reducing scrap. • 2018: Completed an in-lining project for dies and tooling by building a die maintenance room and relocating dies and downstream tooling. • 2018: Established product home lines to help reduce scrap and credits by improving setups, implementing product specific tooling, and product pairing. • 2017-2018: Achieved 12 months without a recordable injury. • 2017: Exceeded annual $150K front-to-back savings with an actual savings of $316K+ savings by improving the hiring process and introducing an efficient product line layout. • 2017: Created short run production crews to reduce the complexity for the long run crews by reducing the number of lines and products for which they were responsible. • 2016: Reduced customer credits from previous year by 50%, saving $327K. • 2016: Reduced production scrap by 37% or 756,000 pounds. • 2016: Reduced recordable safety incidents from 11 to two. • 2016: Achieved an SQF audit score of 99, the highest rating any Zip-Pak plant had ever achieved.
-
-
Manufacturing Manager – Short Run
-
2015 - 2016
Ottawa, IL I managed 20+ staff with 3 direct reports, with responsibility for night shift production teams and a trainer. And I directed the operator development program and developed all training/testing materials. • Hired a Production Tooling Technician to maintain dies and downstream tooling; created position from scratch to support increased manufacturing needs. • Reduced plant scrap by 32% in 2017 YOY savings via better communication and process improvements (spec… Show more I managed 20+ staff with 3 direct reports, with responsibility for night shift production teams and a trainer. And I directed the operator development program and developed all training/testing materials. • Hired a Production Tooling Technician to maintain dies and downstream tooling; created position from scratch to support increased manufacturing needs. • Reduced plant scrap by 32% in 2017 YOY savings via better communication and process improvements (spec documents and working split shifts to improve upon the shift to shift communication and address high scrap opportunities with feedback for improvement directly to crews and individuals.
-
-
-
Morrison Container Handling Solutions
-
United States
-
Automation Machinery Manufacturing
-
1 - 100 Employee
-
Operations Process Engineer / Production Manager
-
2012 - 2015
Glenwood, IL I supervised 25 employees with 18 direct reports in Purchasing, Manufacturing, Assembly, and Stockroom/Shipping departments. This means I prioritized and scheduled projects; identified and implemented process improvements; and hired new team members. • Developed the Process Engineer/Production Manager position to track jobs and aid cross-functional leadership. • Achieved two full weeks of 100% on-time shipments within first six months as the Production … Show more I supervised 25 employees with 18 direct reports in Purchasing, Manufacturing, Assembly, and Stockroom/Shipping departments. This means I prioritized and scheduled projects; identified and implemented process improvements; and hired new team members. • Developed the Process Engineer/Production Manager position to track jobs and aid cross-functional leadership. • Achieved two full weeks of 100% on-time shipments within first six months as the Production Manager. • Introduced tracking metrics to assess team performance and reduce time lost and expenses. • Simplified bill of materials by eliminating unnecessary content and standardizing drawings. • Realized a 14% improvement in on-time delivery in the first year. • Overhauled Kanban system to reduce inventory and long lead parts. • Implemented cross-functional training for Assembly, Manufacturing, and Stockroom employees.
-
-
Operations Process Engineer
-
Jun 2012 - Nov 2012
Glenwood, IL I managed four direct reports and established a Stockroom Manager position. In this role, I focused on improving functions through reorganization of raw materials, products in production, and finished products. • Developed a production calendar to track all job information and present progress to the entire organization. • Improved project management by implementing documented approval at various stages of a project to ensure all parties agreed with project… Show more I managed four direct reports and established a Stockroom Manager position. In this role, I focused on improving functions through reorganization of raw materials, products in production, and finished products. • Developed a production calendar to track all job information and present progress to the entire organization. • Improved project management by implementing documented approval at various stages of a project to ensure all parties agreed with project scope. • Improved customer satisfaction and costs by adjusting quotation terms and conditions to allow for fluctuations in backlog and lead times.
-
-
Education
-
Purdue University
Bachelor of Science - BS, Mechanical Engineering Technology
Community
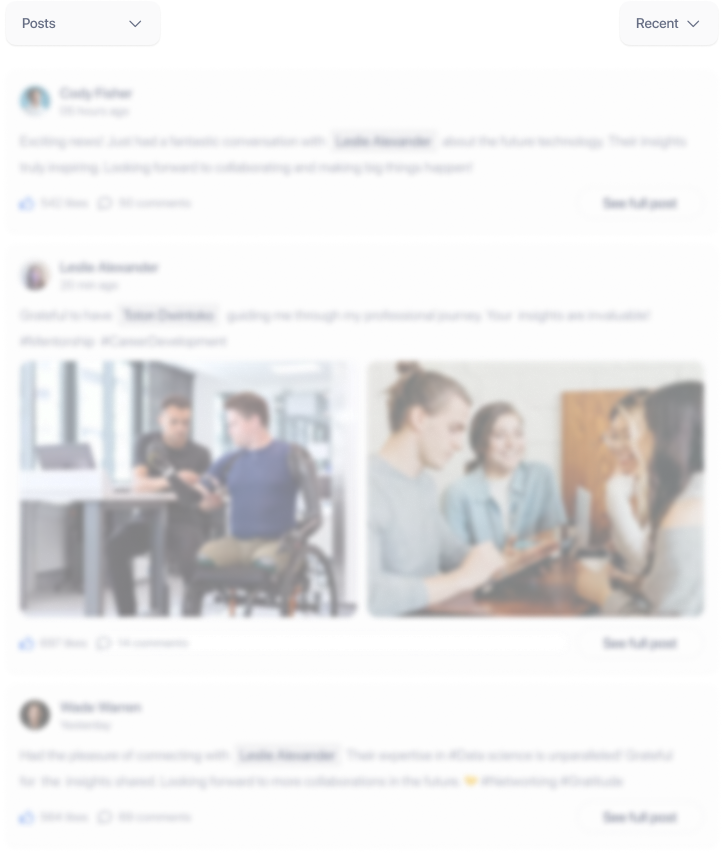