Stephen H.
Senior Continuous Improvement Engineer at CityFibre- Claim this Profile
Click to upgrade to our gold package
for the full feature experience.
Topline Score
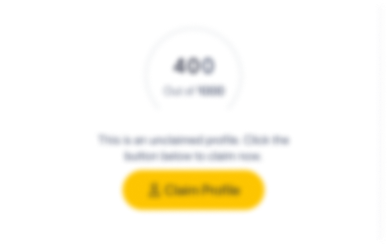
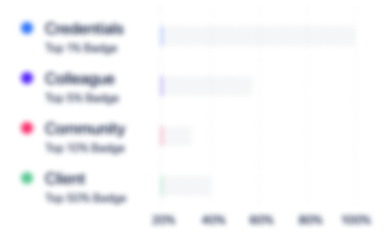
Bio

Steve Cook
I have Known Steve Hoey for 5 years, since joining Tarmac in 2015. Steve carried out extensive training across my packing plant and rail teams in around the CI Fundamentals and also worked on the Radiation Protection systems operating at Dunbar Cement Plant. The work Steve did allowed myself and the teams to prioritise our work flows and C.I. initiatives, and helped us reflect both on where we had come from and where we wanted to be across all elements of our operation. Having used the 5-S methodology previously, Steve was able to add some formal training and structure to the Dunbar packing team. I specifically liked the introduction of T-Maps to help define 12 month strategy and use of Smartsheet as the action planner to help track and achieve the desired goals through regular reviews. I insisted that Steve carried out the reviews as it helped keep us honest as to our progress. Steve introduced the iAuditor for data collection, pictures, analysis, etc (i.e. moving from paper based systems to technological cloud based system). Again, in conjunction with Steve, we expanded and developed this concept and it is now very much the system of choice used across several business functions. Being a fan of process mapping, I used to Steve to build maps of both the packed and bulk process streams, but perhaps the most significant benefit was in the management of radiation sources. The document allowed us to clarify a very complicated and document driven process. I found Steve to be very positive and always willing to help - he was able to step back from the day to day world we become engrossed in and make practical suggestions or observations which challenged or at least gave us food for thought. Steve also has a great taste in music!!!

Tony Green
I first met Steve when I joined Tarmac in August 2016, he was presenting and promoting 5S activities at Tarmac’s Aberthaw site. I was immediately struck by the level of enthusiasm Steve displayed allied to the positive engagement he brought to the training session. All present took part in a fully interactive training session. We within the filling and loading department at Aberthaw began a structured and disciplined journey of continuous improvement under Steve’s guidance. Firstly, setting out criteria to measure where we were and subsequently utilising T-Maps and smartsheets to ensure we kept on track ultimately moving towards our agreed goals. We adopted visual management techniques, creating an information centre at the entrance to our plant so both operators within the section and any visitors can see where we are and what we want to achieve. Within our display centre there’s KPI boards with a rolling twelve weeks of data covering throughput, reliability of the process and waste. This data measurement and display shows not only the progress being made by the team but is also stands as a testament to Steve’s commitment. We’ve fully embraced new technology, utilising camera recognition systems to aid product quality and information, IAuditor to ensure standards and routines are maintained and videos for operator training. We now have our own sharepoint site that incorporates everything within our section, including RA’s and SSoW. Steve has been fully supportive in all of the above, often introducing us to others who could support us in our journey. It is a pleasure working with Steve his commitment is second to none, he is always available to help both in a supportive and practical way never adverse to getting his hands dirty. Almost five years down the line the section has improved beyond compare, something I can state without any fear as we’ve the data history to fully support my claim thanks to the systematic way we monitor our activities. It is a great disappointment to my section and to me personally that Steve’s continuous improvement role was cut because of savings made necessary by Covid-19. I firmly believe that all forward-thinking companies need supporting people like Steve to maintain their position in the marketplace.

Steve Cook
I have Known Steve Hoey for 5 years, since joining Tarmac in 2015. Steve carried out extensive training across my packing plant and rail teams in around the CI Fundamentals and also worked on the Radiation Protection systems operating at Dunbar Cement Plant. The work Steve did allowed myself and the teams to prioritise our work flows and C.I. initiatives, and helped us reflect both on where we had come from and where we wanted to be across all elements of our operation. Having used the 5-S methodology previously, Steve was able to add some formal training and structure to the Dunbar packing team. I specifically liked the introduction of T-Maps to help define 12 month strategy and use of Smartsheet as the action planner to help track and achieve the desired goals through regular reviews. I insisted that Steve carried out the reviews as it helped keep us honest as to our progress. Steve introduced the iAuditor for data collection, pictures, analysis, etc (i.e. moving from paper based systems to technological cloud based system). Again, in conjunction with Steve, we expanded and developed this concept and it is now very much the system of choice used across several business functions. Being a fan of process mapping, I used to Steve to build maps of both the packed and bulk process streams, but perhaps the most significant benefit was in the management of radiation sources. The document allowed us to clarify a very complicated and document driven process. I found Steve to be very positive and always willing to help - he was able to step back from the day to day world we become engrossed in and make practical suggestions or observations which challenged or at least gave us food for thought. Steve also has a great taste in music!!!

Tony Green
I first met Steve when I joined Tarmac in August 2016, he was presenting and promoting 5S activities at Tarmac’s Aberthaw site. I was immediately struck by the level of enthusiasm Steve displayed allied to the positive engagement he brought to the training session. All present took part in a fully interactive training session. We within the filling and loading department at Aberthaw began a structured and disciplined journey of continuous improvement under Steve’s guidance. Firstly, setting out criteria to measure where we were and subsequently utilising T-Maps and smartsheets to ensure we kept on track ultimately moving towards our agreed goals. We adopted visual management techniques, creating an information centre at the entrance to our plant so both operators within the section and any visitors can see where we are and what we want to achieve. Within our display centre there’s KPI boards with a rolling twelve weeks of data covering throughput, reliability of the process and waste. This data measurement and display shows not only the progress being made by the team but is also stands as a testament to Steve’s commitment. We’ve fully embraced new technology, utilising camera recognition systems to aid product quality and information, IAuditor to ensure standards and routines are maintained and videos for operator training. We now have our own sharepoint site that incorporates everything within our section, including RA’s and SSoW. Steve has been fully supportive in all of the above, often introducing us to others who could support us in our journey. It is a pleasure working with Steve his commitment is second to none, he is always available to help both in a supportive and practical way never adverse to getting his hands dirty. Almost five years down the line the section has improved beyond compare, something I can state without any fear as we’ve the data history to fully support my claim thanks to the systematic way we monitor our activities. It is a great disappointment to my section and to me personally that Steve’s continuous improvement role was cut because of savings made necessary by Covid-19. I firmly believe that all forward-thinking companies need supporting people like Steve to maintain their position in the marketplace.

Steve Cook
I have Known Steve Hoey for 5 years, since joining Tarmac in 2015. Steve carried out extensive training across my packing plant and rail teams in around the CI Fundamentals and also worked on the Radiation Protection systems operating at Dunbar Cement Plant. The work Steve did allowed myself and the teams to prioritise our work flows and C.I. initiatives, and helped us reflect both on where we had come from and where we wanted to be across all elements of our operation. Having used the 5-S methodology previously, Steve was able to add some formal training and structure to the Dunbar packing team. I specifically liked the introduction of T-Maps to help define 12 month strategy and use of Smartsheet as the action planner to help track and achieve the desired goals through regular reviews. I insisted that Steve carried out the reviews as it helped keep us honest as to our progress. Steve introduced the iAuditor for data collection, pictures, analysis, etc (i.e. moving from paper based systems to technological cloud based system). Again, in conjunction with Steve, we expanded and developed this concept and it is now very much the system of choice used across several business functions. Being a fan of process mapping, I used to Steve to build maps of both the packed and bulk process streams, but perhaps the most significant benefit was in the management of radiation sources. The document allowed us to clarify a very complicated and document driven process. I found Steve to be very positive and always willing to help - he was able to step back from the day to day world we become engrossed in and make practical suggestions or observations which challenged or at least gave us food for thought. Steve also has a great taste in music!!!

Tony Green
I first met Steve when I joined Tarmac in August 2016, he was presenting and promoting 5S activities at Tarmac’s Aberthaw site. I was immediately struck by the level of enthusiasm Steve displayed allied to the positive engagement he brought to the training session. All present took part in a fully interactive training session. We within the filling and loading department at Aberthaw began a structured and disciplined journey of continuous improvement under Steve’s guidance. Firstly, setting out criteria to measure where we were and subsequently utilising T-Maps and smartsheets to ensure we kept on track ultimately moving towards our agreed goals. We adopted visual management techniques, creating an information centre at the entrance to our plant so both operators within the section and any visitors can see where we are and what we want to achieve. Within our display centre there’s KPI boards with a rolling twelve weeks of data covering throughput, reliability of the process and waste. This data measurement and display shows not only the progress being made by the team but is also stands as a testament to Steve’s commitment. We’ve fully embraced new technology, utilising camera recognition systems to aid product quality and information, IAuditor to ensure standards and routines are maintained and videos for operator training. We now have our own sharepoint site that incorporates everything within our section, including RA’s and SSoW. Steve has been fully supportive in all of the above, often introducing us to others who could support us in our journey. It is a pleasure working with Steve his commitment is second to none, he is always available to help both in a supportive and practical way never adverse to getting his hands dirty. Almost five years down the line the section has improved beyond compare, something I can state without any fear as we’ve the data history to fully support my claim thanks to the systematic way we monitor our activities. It is a great disappointment to my section and to me personally that Steve’s continuous improvement role was cut because of savings made necessary by Covid-19. I firmly believe that all forward-thinking companies need supporting people like Steve to maintain their position in the marketplace.

Steve Cook
I have Known Steve Hoey for 5 years, since joining Tarmac in 2015. Steve carried out extensive training across my packing plant and rail teams in around the CI Fundamentals and also worked on the Radiation Protection systems operating at Dunbar Cement Plant. The work Steve did allowed myself and the teams to prioritise our work flows and C.I. initiatives, and helped us reflect both on where we had come from and where we wanted to be across all elements of our operation. Having used the 5-S methodology previously, Steve was able to add some formal training and structure to the Dunbar packing team. I specifically liked the introduction of T-Maps to help define 12 month strategy and use of Smartsheet as the action planner to help track and achieve the desired goals through regular reviews. I insisted that Steve carried out the reviews as it helped keep us honest as to our progress. Steve introduced the iAuditor for data collection, pictures, analysis, etc (i.e. moving from paper based systems to technological cloud based system). Again, in conjunction with Steve, we expanded and developed this concept and it is now very much the system of choice used across several business functions. Being a fan of process mapping, I used to Steve to build maps of both the packed and bulk process streams, but perhaps the most significant benefit was in the management of radiation sources. The document allowed us to clarify a very complicated and document driven process. I found Steve to be very positive and always willing to help - he was able to step back from the day to day world we become engrossed in and make practical suggestions or observations which challenged or at least gave us food for thought. Steve also has a great taste in music!!!

Tony Green
I first met Steve when I joined Tarmac in August 2016, he was presenting and promoting 5S activities at Tarmac’s Aberthaw site. I was immediately struck by the level of enthusiasm Steve displayed allied to the positive engagement he brought to the training session. All present took part in a fully interactive training session. We within the filling and loading department at Aberthaw began a structured and disciplined journey of continuous improvement under Steve’s guidance. Firstly, setting out criteria to measure where we were and subsequently utilising T-Maps and smartsheets to ensure we kept on track ultimately moving towards our agreed goals. We adopted visual management techniques, creating an information centre at the entrance to our plant so both operators within the section and any visitors can see where we are and what we want to achieve. Within our display centre there’s KPI boards with a rolling twelve weeks of data covering throughput, reliability of the process and waste. This data measurement and display shows not only the progress being made by the team but is also stands as a testament to Steve’s commitment. We’ve fully embraced new technology, utilising camera recognition systems to aid product quality and information, IAuditor to ensure standards and routines are maintained and videos for operator training. We now have our own sharepoint site that incorporates everything within our section, including RA’s and SSoW. Steve has been fully supportive in all of the above, often introducing us to others who could support us in our journey. It is a pleasure working with Steve his commitment is second to none, he is always available to help both in a supportive and practical way never adverse to getting his hands dirty. Almost five years down the line the section has improved beyond compare, something I can state without any fear as we’ve the data history to fully support my claim thanks to the systematic way we monitor our activities. It is a great disappointment to my section and to me personally that Steve’s continuous improvement role was cut because of savings made necessary by Covid-19. I firmly believe that all forward-thinking companies need supporting people like Steve to maintain their position in the marketplace.

Experience
-
CityFibre
-
United Kingdom
-
Telecommunications
-
700 & Above Employee
-
Senior Continuous Improvement Engineer
-
May 2021 - Present
CityFibre is the UK’s third national digital infrastructure platform. With existing networks in more than 60 towns and cities, CityFibre provides wholesale connectivity to multiple business and consumer service providers, local authorities, and mobile operators CityFibre has network rollouts underway with plans to pass up to 8 million homes and businesses with open-access full fibre infrastructure. A growing number of Gigabit City projects have been announced for full-city rollouts and CityFibre continues to prime its existing network assets for expansion. CityFibre build using a unique model so that we try and minimize the times we ever need to dig up a road or pavement and we are Continually Improving our processes and procedures to deliver our network designs in line with our ambition; plan well, dig once, build right first time
-
-
-
Tarmac
-
United Kingdom
-
Construction
-
700 & Above Employee
-
Continuous Improvement Advisor
-
Feb 2008 - Dec 2020
Having worked in the Aggregates, Asphalt, RMX and most recently the Cement & Lime business units, my role as CI Advisor enabled me to work closely with all levels of management and operational teams to effect change in the plant environment through positive engagement and empowerment in order to install a Lean thinking mindset so that ‘Challenging the Norm’ becomes embedded as part of their day-to-day working practice. By focusing my attention on three key drivers - Operating Systems, Management Infrastructure and Mindsets, Behaviours & Capabilities I was able to drive sustainable change resulting in demonstrable improvements both in terms of hard and soft savings.
-
-
-
TDS Logistics
-
United States
-
Transportation, Logistics, Supply Chain and Storage
-
1 - 100 Employee
-
Business Process Improvement (BPI) Manager (UK)
-
Sep 2005 - Feb 2008
As the UK BPI Manager my key job focus was to re-invigorate BPI back into the UK operation and change people’s thinking from the BPI philosophy being something they have to comply with, to making it a process that they want to commit to. Key objectives were; • Determine BPI resource requirement and recruit as necessary • Work with Departmental Managers to generate project pipeline and to deliver sustainable projects to meet business needs and financial targets • Mentor Green Belts to successful completion of 3 projects with a combined value prop of €50k • Develop Cost Benefit Analysis (CBA) to justify project expenditure BPI also supports the Business Development Manager and assists in New Product Introductions (NPI) to ensure we get it right first time.
-
-
-
Johnson Controls
-
Ireland
-
Industrial Machinery Manufacturing
-
700 & Above Employee
-
Six Sigma Black Belt
-
2002 - 2005
-
-
-
LDV
-
Automotive
-
1 - 100 Employee
-
Production Manager (Final Despatch)
-
1995 - 2001
-
-
Education
-
East Birmingham College & University of Central England
Diploma, Quality Assurance
Community
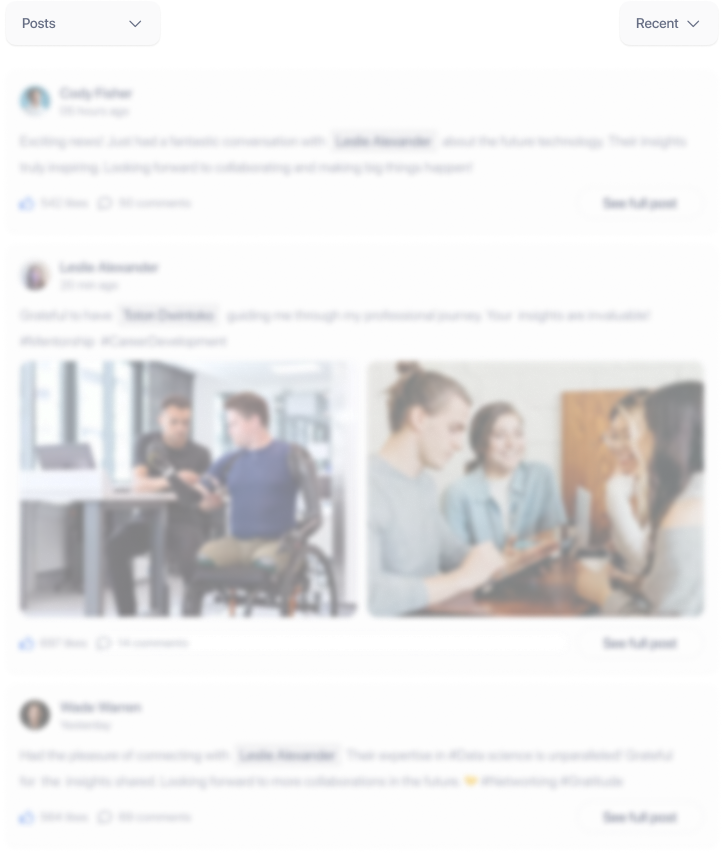