Stephen Fynn
Dispatch Manager at Servworx- Claim this Profile
Click to upgrade to our gold package
for the full feature experience.
-
Afrikaans -
Topline Score
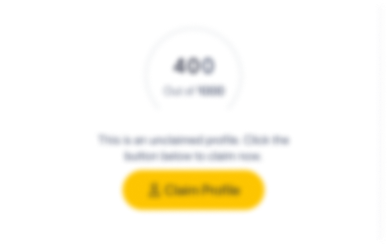
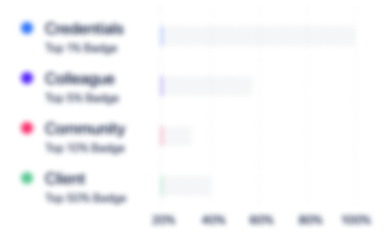
Bio


Credentials
-
Certificate in Storemanship
-Nov, 2001- Nov, 2024
Experience
-
Servworx
-
1 - 100 Employee
-
Dispatch Manager
-
Feb 2016 - Present
-
-
-
Sunshine Bakery
-
25 Willowton Road
-
Dispatch Clerk
-
Jul 2014 - Mar 2015
The despatch clerk that is checking the order from the order sheet and the order pulled for loading must also do the despatch delivery note. All paper work must have the following info: 1. Drivers Name 2. Time 3. Route Name and Chain store Name 4. Amount of crates 5. Pricing – Cash sales 6. Signature of a Despatch Clerk 7. Invoice or Reference Number 8. Amount of bread 9. Totals 10. Credit notes to have driver’s & clerk’s signature 11. A hand over must be done by each shift. Stock to be checked and balanced, after second deliveries and before the start of night shift.(Name & Signature) 12. All the pages of the recon must be signed by the Despatch clerk that balances the stock. (Name & Signature) 13. Next shift to sign for opening stock. 14. When receiving stock from production a despatch clerk must be present to count stock. 15. Production must make one slip per cage and must have an opening and closing time for the cage. 16. Despatch cages must be locked when loading. 17. Clerks will be held responsible for short or over of stock. Dayshift and Nightshift Duties • Count and balance stock • Count Sunshine crate • Do a Production flow for dayshift • Weight checks • Do cash and damage sales • Balance crate sheet • Balance crate file • Do despatch notes for 2nd deliveries • Load bread for 2nd deliveries • Pull bread from production for 2nd deliveries • Enter crates despatched on crate sheet • Count driver’s crates • Do crate return slips • Make claims and credit notes • Check all return bread • Fill distribution control • Enter all information on the computer eg: cash sales – Despatch notes – bread received from production – Opening stock – Returns and claims • Check that all chain store invoices have been returned • Make a list of all outstanding invoices • Balance stock &Cash up • Load one order at a time • Request books for nightshift • Do production flow for nightshift • Pull stock for next shift Show less
-
-
-
Toyota Tsusho Africa
-
Transportation, Logistics, Supply Chain and Storage
-
100 - 200 Employee
-
Dispatch Supervisor
-
Jan 2014 - May 2014
Reporting to the Warehouse Manager. Ø Supervise a staff compliment of 7 employees. Ø Manage all dispatch operations. Ø Liaise with internal and external 3RD party transporters. Ø Cost effectively scheduling of loads and co-ordinating of transport. Ø Ensure loads leave correctly and all paperwork is in place. Ø Ensure that loads leave at the correct time schedule. Ø Overseer the receiving and managing of goods returned. Ø Co-ordinate all transport and load activities. Ø Optimising return loads / “empty loads”. Ø Monitor the supply and availability of pallets. Ø Follow through on any operational queries. Ø Enforce standard operating procedures and policies. Ø Comply with Health and Safety rules and requirements. Show less
-
-
-
Capital Soaps and Rice
-
Pietermaritzburg Area, South Africa
-
Logistics Coordinator
-
Mar 2013 - Mar 2013
Responsible for the following: The Transport Co-coordinator The Receiving Supervisor The Warehouse Supervisor The Packaging Supervisor The Dispatch Supervisor To manage a full staff complement of 48 employees (including the supervisors) To monitor the security company and address issues as they arose and request procedures to be implemented where necessary To process all previous day’s paperwork and address any issues that needed to be attended to To make analyses of data in terms of vehicles out of circulation (routine service schedule), diesel usage and discrepancies with monies drivers returned To meet in the morning with the night shift security for debriefing and address any issues that may have occurred To implement processes where there are loopholes Show less
-
-
-
Makro South Africa
-
South Africa
-
Retail
-
700 & Above Employee
-
Back Returns Supervisor
-
Jun 2008 - Feb 2013
: Delegating duties to staff : Responsible for overseeing the following takes place: i) Receiving customer repairs into storage location for customer repairs ii) Making arrangements for the customer repairs to be collected by the suppliers and their respective agents iii) Handing customer repairs over to the driver where suppliers cannot make the collection iv) Changing the status of the customer repairs on SAP CRM to “received by supplier” (tracking the repair) v) When the customer repairs are ready, to arrange to have the driver make the collection vi) Changing the status of the customer repairs on SAP CRM to “waiting on customer” (tracking the repair) vii) These customer repairs are then handed over to the Front Returns Clerks viii) Receiving stock repairs into storage location for stock repairs ix) Making arrangements for the stock repairs to be collected by the suppliers and their respective agents and generating the “Issue to Stock Repair” documents on SAP Retail x) Generating “Issue to Stock Repair” documents on SAP Retail and handing over stock repairs to the driver where suppliers cannot make the collection xi) Running a weekly Stock Repair Report on SAP Retail to ensure there are no stock repairs nearing 21 working day period (tracking the repair) xii) When the stock repairs are ready, to arrange to have the driver make the collection : At the beginning of each fiscal year I have to have a presentation for the DM’s forum for discussion of shortfalls, achievements and objectives for the new fiscal year : Have meetings with suppliers where problems arise : Continually monitor storage location S002 to ensure that at the end of each week the full value stands at below R 10 000, 00 : Continuous communication with the Front Returns Clerks and various departments to ensure that any damages from the sales floor are sent to the Returns Department timeously Show less
-
-
-
Polycor Chemicals
-
Cape Town Area, South Africa
-
Warehouse Manager
-
Oct 1999 - Feb 2007
Ensuring that ISO 9002 procedures are followed and where improvements can be made, to forward those proposals to the Branch Manager Responsible for the follow up of the e.t.a. of container’s from our overseas suppliers i.e. with clearing agents in South Africa Arranging the delivery of each container at correct intervals to ensure there are no clashes with other deliveries Communicating telephonically with local suppliers to ensure that their deliveries do not impact with each other and that of container deliveries Liaising telephonically with customers to ensure that high service levels are achieved Meeting periodically with customers and suppliers to smooth out concerns Overseeing that the following is carried out correctly: i)Receiving stock into the staging area into the warehouse ii)Identification and checking of stock in the staging area before storing stock in their correct storing area(s) iii)Spot checking the Certificate of Analysis against the batch numbers printed on the product iv)Proper storage of products to ensure that F.I.F.O. principle is achieved v)Picking of orders to be sent to the despatch staging area for checking vi)After checks have been done, loading products onto vehicles and despatching of vehicles vii)Ensuring that the correct Hazchem labels are attached to the vehicles and that all zdocs accompany the driver’s upon departure from the warehouse Ensure all health and safety procedures are adhered to Ensure that codes of conduct are followed Ordering of products at the correct time to ensure there is sufficient: stock available for customers Ensure that the driver’s do the daily vehicle and hyster checks against the check sheets Ensure that all vehicles and equipment are clean and serviced at the correct intervals Carrying out monthly stock take to ensure shrinkage is at a minimum Show less
-
-
-
Master Sports
-
Cape Town Area, South Africa
-
Receiving and Dispatch Manager
-
Jun 1994 - Feb 1999
: Supervise a permanent staff compliment of 8 and a further 8 casuals during peak periods : Communicating with third party for timeous deliveries of correct stock on order : Checking stock delivered against order sheet : Supervising the storage of the said stock into its allocated slot : Supervising the pulling of stock for processing : Supervising the storage of the processed stock into its allocated slot : Supervise the picking of processed stock for checking : Supervise the checking of the said stock for despatching : Supervise the despatching of the checked stock to all Woolworth stores : Assisting the Stock Controller with stock control function : Responsible for the full running of the Reject Storage Facility : Transferring the reject stock when requested to the factory shop : Liaising with all relevant department(s) Show less
-
-
Education
-
Centre for Logistics Excellence
Certificate in Stores Management, Materials Handling, Stores Management, Management Skills, Analysis Techniques, Purchasing and Materi -
Centre for Logistics Excellence
Certificate in Storemanship, Quality, Service Levels, Productivity, The Cube, Unit Loads, Cargo Handling and Containerisation -
Haythorne Senior Secondary High School
No, English, Afrikaans, Accounting, Business Economics, Economics, Mathematics
Community
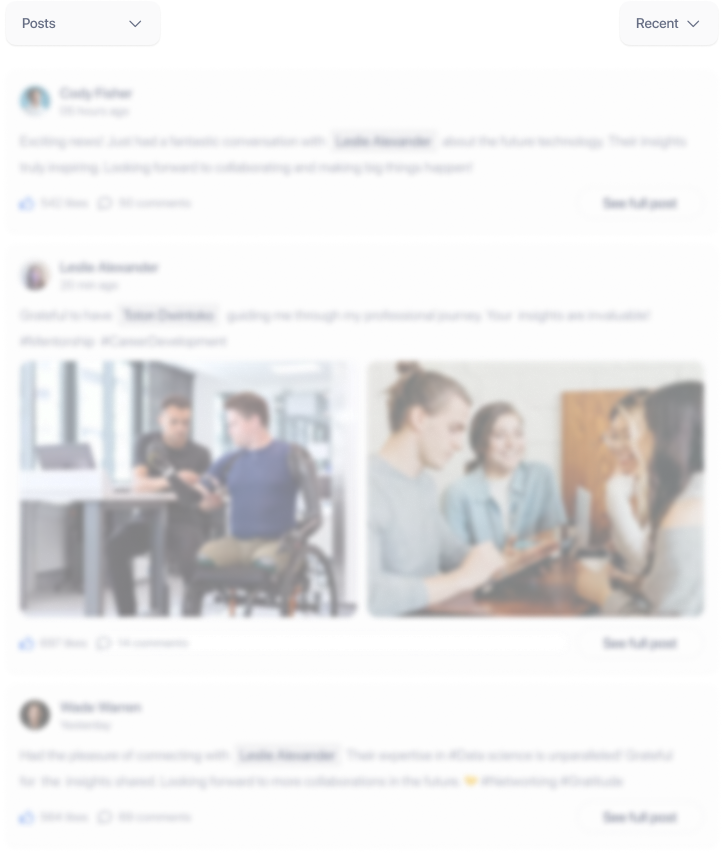