Stephanie Watkins
Senoir Production Planner at Anton Paar QuantaTec- Claim this Profile
Click to upgrade to our gold package
for the full feature experience.
Topline Score
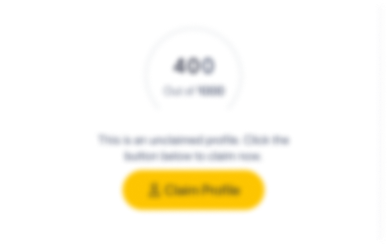
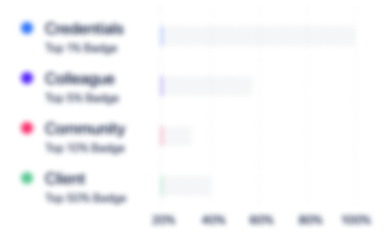
Bio


Experience
-
Anton Paar QuantaTec
-
United States
-
Machinery Manufacturing
-
1 - 100 Employee
-
Senoir Production Planner
-
Dec 2021 - Present
- Manage and oversee team of 25 consisting of line leads and technicians - Develop and maintain production schedules to meet customer demand and achieve on-time delivery targets - Collaborate with engineering and quality control teams to ensure product quality standards are met - Utilize ERP software (SAP) to track work orders, monitor production progress, and generate reports for management - Monitor production processes to identify bottlenecks and implement corrective actions -… Show more - Manage and oversee team of 25 consisting of line leads and technicians - Develop and maintain production schedules to meet customer demand and achieve on-time delivery targets - Collaborate with engineering and quality control teams to ensure product quality standards are met - Utilize ERP software (SAP) to track work orders, monitor production progress, and generate reports for management - Monitor production processes to identify bottlenecks and implement corrective actions - Provide coaching and feedback to team members one-on-one Show less - Manage and oversee team of 25 consisting of line leads and technicians - Develop and maintain production schedules to meet customer demand and achieve on-time delivery targets - Collaborate with engineering and quality control teams to ensure product quality standards are met - Utilize ERP software (SAP) to track work orders, monitor production progress, and generate reports for management - Monitor production processes to identify bottlenecks and implement corrective actions -… Show more - Manage and oversee team of 25 consisting of line leads and technicians - Develop and maintain production schedules to meet customer demand and achieve on-time delivery targets - Collaborate with engineering and quality control teams to ensure product quality standards are met - Utilize ERP software (SAP) to track work orders, monitor production progress, and generate reports for management - Monitor production processes to identify bottlenecks and implement corrective actions - Provide coaching and feedback to team members one-on-one Show less
-
-
-
Anton Paar USA
-
United States
-
Appliances, Electrical, and Electronics Manufacturing
-
100 - 200 Employee
-
Quality Assurance Specialist
-
Mar 2021 - Dec 2021
Inspecting, testing, and approving high level gas sorption porosity, and bulk density instruments to industry and client standards. Inspecting, testing, and approving high level gas sorption porosity, and bulk density instruments to industry and client standards.
-
-
-
SLB
-
United States
-
Technology, Information and Internet
-
700 & Above Employee
-
Field Engineer II
-
May 2018 - May 2020
-
-
-
-
Athletic Tutor
-
Sep 2015 - May 2018
-
-
-
Antero Resources
-
United States
-
Oil and Gas
-
200 - 300 Employee
-
Production Engineer Intern
-
May 2017 - Aug 2017
I worked exclusively with fellow production engineers on daily tasks of monitoring producing wells and updating equipment orders. I worked on two main summer projects involving the potential cost savings for recycling piper brand valves that are used at the GPU inlet during flowback and verifying that foamer use in dry gas wells is beneficial. My results were that recycling the piper brand valves to other sites could save $530,000 if 250 valves were reused at other GPU inlets and $350,000 if… Show more I worked exclusively with fellow production engineers on daily tasks of monitoring producing wells and updating equipment orders. I worked on two main summer projects involving the potential cost savings for recycling piper brand valves that are used at the GPU inlet during flowback and verifying that foamer use in dry gas wells is beneficial. My results were that recycling the piper brand valves to other sites could save $530,000 if 250 valves were reused at other GPU inlets and $350,000 if the valves were re-purposed for reuse at the well head. The foamer proved to increase the flow rate through casing while also preventing slugging in the current 12 wells. The three remaining wells utilized soap through tubing and also had the same results. If the flow rates for the 15 wells remained constant over a year, the foamer created an additional $2.1 million dollars in revenue, which includes the costs of the 15 pumps (installation and tank vault included) and the Q/D of foamer usage in each well for the year. The foamer also created an additional 760 MMCF of gas per year assuming constant flow. I also showed that if the current foamer use in Q/D correlated with the estimated water rate per well that this would create an additional $200,000 per year in savings. Show less I worked exclusively with fellow production engineers on daily tasks of monitoring producing wells and updating equipment orders. I worked on two main summer projects involving the potential cost savings for recycling piper brand valves that are used at the GPU inlet during flowback and verifying that foamer use in dry gas wells is beneficial. My results were that recycling the piper brand valves to other sites could save $530,000 if 250 valves were reused at other GPU inlets and $350,000 if… Show more I worked exclusively with fellow production engineers on daily tasks of monitoring producing wells and updating equipment orders. I worked on two main summer projects involving the potential cost savings for recycling piper brand valves that are used at the GPU inlet during flowback and verifying that foamer use in dry gas wells is beneficial. My results were that recycling the piper brand valves to other sites could save $530,000 if 250 valves were reused at other GPU inlets and $350,000 if the valves were re-purposed for reuse at the well head. The foamer proved to increase the flow rate through casing while also preventing slugging in the current 12 wells. The three remaining wells utilized soap through tubing and also had the same results. If the flow rates for the 15 wells remained constant over a year, the foamer created an additional $2.1 million dollars in revenue, which includes the costs of the 15 pumps (installation and tank vault included) and the Q/D of foamer usage in each well for the year. The foamer also created an additional 760 MMCF of gas per year assuming constant flow. I also showed that if the current foamer use in Q/D correlated with the estimated water rate per well that this would create an additional $200,000 per year in savings. Show less
-
-
-
Range Resources
-
United States
-
Oil and Gas
-
400 - 500 Employee
-
Field Engineer Intern
-
May 2016 - Aug 2016
Production Engineer Intern at RRC. My summer project was heavily field based and looked in depth into fluid separation on wet pads; specifically dealing with the Gas Processing Unit (GPU) and the Coriolis Meter. I determined that the Coriolis Meter could not reliably detect large sand return. I based my findings on the separation data recorded in Cygnet, which was trended before the date of the recorded GPU vessel inspection to determine if the inspection was due to separation or a scheduled… Show more Production Engineer Intern at RRC. My summer project was heavily field based and looked in depth into fluid separation on wet pads; specifically dealing with the Gas Processing Unit (GPU) and the Coriolis Meter. I determined that the Coriolis Meter could not reliably detect large sand return. I based my findings on the separation data recorded in Cygnet, which was trended before the date of the recorded GPU vessel inspection to determine if the inspection was due to separation or a scheduled event. Show less Production Engineer Intern at RRC. My summer project was heavily field based and looked in depth into fluid separation on wet pads; specifically dealing with the Gas Processing Unit (GPU) and the Coriolis Meter. I determined that the Coriolis Meter could not reliably detect large sand return. I based my findings on the separation data recorded in Cygnet, which was trended before the date of the recorded GPU vessel inspection to determine if the inspection was due to separation or a scheduled… Show more Production Engineer Intern at RRC. My summer project was heavily field based and looked in depth into fluid separation on wet pads; specifically dealing with the Gas Processing Unit (GPU) and the Coriolis Meter. I determined that the Coriolis Meter could not reliably detect large sand return. I based my findings on the separation data recorded in Cygnet, which was trended before the date of the recorded GPU vessel inspection to determine if the inspection was due to separation or a scheduled event. Show less
-
-
-
SAMS CLUB
-
United States
-
500 - 600 Employee
-
Cashier
-
Jun 2015 - Nov 2015
Timely and mannerly checkout Collaborating with members/coworkers Maintaining professional relationships Demonstrating punctuality and money management Timely and mannerly checkout Collaborating with members/coworkers Maintaining professional relationships Demonstrating punctuality and money management
-
-
Education
-
Penn State University
Master's degree, Data Analytics -
West Virginia University
Bachelor's degree, Petroleum and Natural Gas Engineering
Community
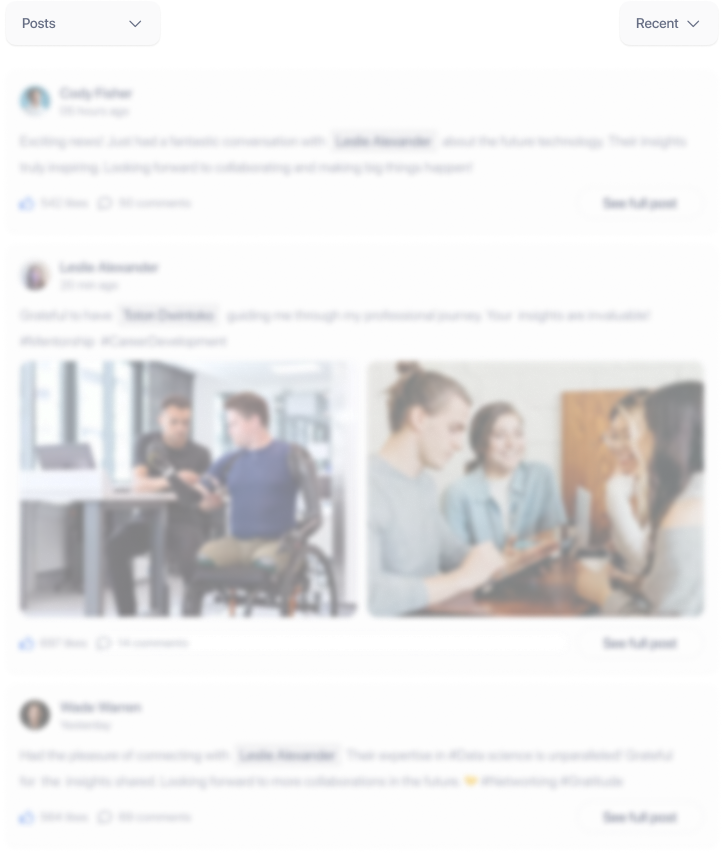