Stephanie Lowe
MRS Workshop Manager at Olympus Medical UKIE- Claim this Profile
Click to upgrade to our gold package
for the full feature experience.
Topline Score
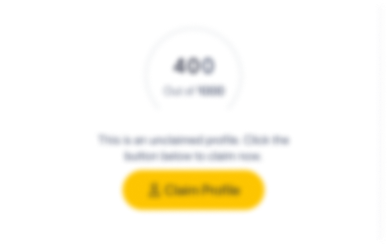
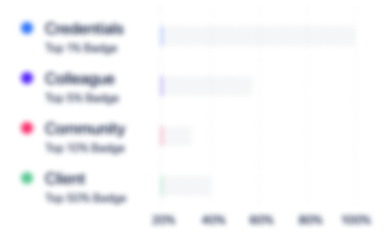
Bio


Credentials
-
Problem Solving
McKinsey & CompanyAug, 2020- Oct, 2024 -
Scrum Master Certified (SMC)
Scrum AllianceSep, 2019- Oct, 2024
Experience
-
Olympus Medical UKIE
-
United Kingdom
-
Medical Devices
-
1 - 100 Employee
-
MRS Workshop Manager
-
Jan 2019 - Present
-
-
Service Manager - Medical
-
Feb 2016 - Dec 2018
-
-
Team Leader - Technical Services (Medical)
-
Jun 2013 - Feb 2016
• In this position I lead a team of 15 repair technicians to ensure the highest level of service is achieved in one section of the medical device service department. I am responsible for the management of medical repairs including safety, quality, technician performance, and day to day cost of repairs of endoscopy equipment, in order to improve turnaround. • Analyse quality and performance data of the department and technicians to identify improvement opportunities. This includes trends that impact the whole department and individual technician performance.• Conduct Personal Development Reviews and other performance related meetings to support technician development.• I liaise with the Quality and Engineering department to understand repair standards and methods, to root cause effectively faults on the equipment.• Deputised for the Service Manager by attending operations meetings. For a four month period, while another team leader vacancy was being filled, I also took responsibility for a further 15 repair technicians. • Training gained: Fundamentals of Employment Law, 8D Problem Solving process.
-
-
-
Procter & Gamble
-
United States
-
Manufacturing
-
700 & Above Employee
-
Line Leader (Production Manager)
-
Sep 2011 - May 2013
• In this position I was responsible for safety, quality, equipment reliability, cost, 10 direct reports, and delivering results on a large carton production line producing branded dry laundry detergent.• I led and developed my team to ensure that they were engaged and energised to follow systems and meet targets. I created personalised work and development plans and used performance management to align expectations and grow the organisation. I also coached Autonomous Maintenance techniques to drive equipment ownership and coach the technical team, operators, and process engineers to use the appropriate work system and standards to solve problems and continuously improve. • Led daily meetings to review all key performance indicators with my team and conducted weekly presentation on line performance to senior management.• Member of a project team to install a new carton size to the correct user requirement specification whilst minimising production impact. I managed a sub-project installing refurbished pallet conveyors, to improve product stability for the new size. This involved writing and executing IQOQPQ protocol.• Organised and prioritised resource availability, maintenance planning and scheduling, and improvement projects, using tools such as Gantt charts. • Responded urgently to supply chain issues, such as customer order changes or material delivery issues, thereby enabling effective collaboration between departments and minimising production disruptions. • Deputised for the Packing Department Leader and Technical Systems Leader being accountable for departmental safety, quality, production, and crewing. Reviewed supply chain issues and determined effects of short term and long term volume forecast.• Occasionally acted as site-wide Manager at weekends to ensure adherence to safety procedures. • Training and Qualifications gained were: GROW Coaching, Corporate Athlete.
-
-
Process Engineer
-
Jul 2010 - Aug 2011
• Daily monitoring of production lines to increase reliability. Provided technical support to production teams to troubleshoot breakdowns and minor stops, differentiating sporadic and chronic failure modes, using the correct root cause analysis tool to fix systemically.• Implemented and improved systems and standards to maintain equipment and throughput results, such as cleaning, preventative maintenance, defect handling, rapid changeover, and centreline.• Validated changes made to production equipment.• Weekly/monthly data analysis identifying trends to determine focus areas for loss elimination. • I led standardisation including representing the department in benchmarking workshops with European plants.• Training and Qualifications gained were: P&G Packing University, Reliability Engineering School.
-
-
-
Patheon
-
United States
-
Pharmaceutical Manufacturing
-
700 & Above Employee
-
Technical Support Engineer
-
Jun 2009 - Sep 2009
• Prioritised actions on the Health and Safety risk register and undertook a number of small projects to resolve the high risk issues. This involved doing risk assessments, writing procedures, and coordinating and supervising contractors.• Working in a large team project I was responsible for managing the contractor works undertaking quality improvements in manufacturing clean rooms under a strict timescale. • Training and Qualifications gained were; 3M fit face trainer, Cryogenic Safety Awareness.
-
-
-
-
Project Engineer
-
Jun 2007 - Sep 2008
• Managed large health and safety project to bring Patheon UK into compliance with the HSE ACOP L8 “Control of Legionella” and organised smaller projects on isolators, waste stores and scaffold structures. This involved planning, prioritising and supervising contractors to action all remedial works and changes with minimal effect on production. For the larger projects, I also followed the company’s stage-gate process. • Developed and implemented systems and standard operating procedures to keep all documentation approved by senior managers and directors which included reports, risk assessments, risk registers, written schemes and a policy up to date. • My communication skills and self confidence enabled me to get the financial support needed to execute a £150,000 project to the correct standard. • I organised all financial requirements for projects including Capital Appropriation Requests, Budgets and Cash Flows.• I was nominated and appointed Employee Safety Representative for Engineering.• Training and Qualifications gained were; Permit to Work, Confined Space Management, Control of Legionella, Asbestos Awareness, Workplace Assessment and other health and safety and pharmaceutical procedures and regulations.
-
-
Education
-
University of Bath
Master of Engineering (MEng), Mechanical Engineering -
Penglais Comprehensive School
Community
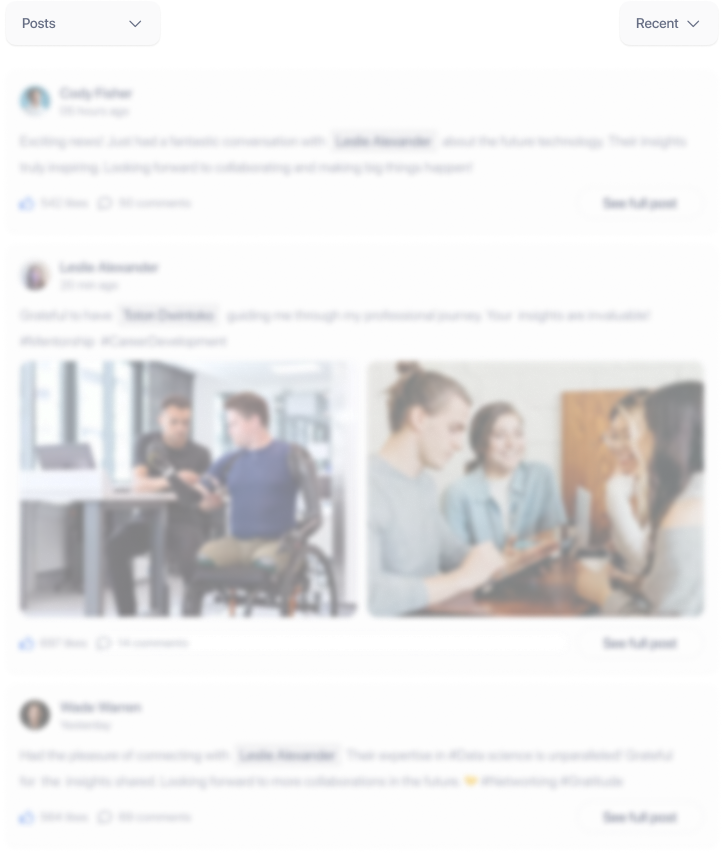