Stephanie Barry
Customer Service Representative at ZAHROOF VALVES INC.- Claim this Profile
Click to upgrade to our gold package
for the full feature experience.
-
Afrikaans -
Topline Score
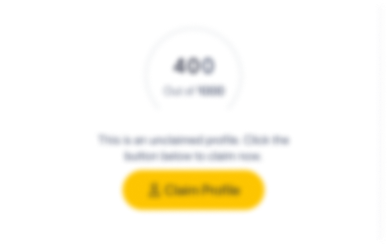
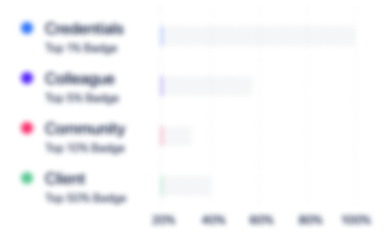
Bio


Experience
-
Zahroof Valves Inc
-
United States
-
Industrial Machinery Manufacturing
-
1 - 100 Employee
-
Customer Service Representative
-
Mar 2018 - Present
-
-
-
American National Carbide
-
Oil and Gas
-
1 - 100 Employee
-
Logistics Manager
-
Jul 2017 - Mar 2018
Responsible for all purchasing for the company including raw material. Establish and maintain order and reorder quantity by part number for finished goods, semi finished, raw materials and supplies. Inventory control of raw material through to finished goods. Create work orders for the shop floor using Global Shop Solutions. Manage pelleted powder in inventory to ensure prompt release of material for manufacturing operation. Handle all freight shipments, national and international. Manage the warehousing and distribution of materials. Compiles and submits monthly reports to the President that details finished goods, WIP, raw materials and supplies inventory by product line and dollar amount. Show less
-
-
-
-
Manufacturing Coordinator
-
May 2013 - Jul 2017
• Entering Sales Orders into MRP system (Avante) and acknowledging acceptance of terms of sale. • Creating work orders based on sales orders entered into the system as well as inventory analysis of raw material and available inventory on hand. • Scheduling orders to meet customers demand on time. • Production Control (work order management / master scheduling / shipping coordination). • Customers’ expedite requests, commit and execution. • Process daily transactions from the floor to provide better traceability of materials and inventory accuracy. • Enter Bills of Material, routings and product structures for new/additional products into Avante MRP system. • Cycle Counts and inventory adjustments. • Scrapping of material at various stages of manufacture. • Reviewing Bills of Material for shortages/expedition of materials. Show less
-
-
-
Foxconn
-
Appliances, Electrical, and Electronics Manufacturing
-
700 & Above Employee
-
Production Control
-
Jun 2009 - May 2013
• Inventory control and management (consignment, turnkey materials) • Coordinated Physical Inventory activities – conducted quarterly PI’s and provided analysis / review • Buyback coordination and implementation • B2B/EDI sales order management – EDI sales data monitoring and implementation • Production Control (work order management / master scheduling / shipping coordination) • Work order fix / BOM revision change / (ECO) change • FGI ROP Trigger management – set up Merge Center ROP trigger model w/ customer • FGI Kanban monitoring and execution • Shipping Coordination (carrier changes / quantity changes / pull-in or push-out) • Customer expedite request commit and execution • Off-line shipment handling (Sales order and Delivery Note generation, Post Goods Issue. • SAP • RMA / Stock rotation and rework handling Key Accomplishments: - Work with IT to set up BOM comparison tool (SAP, Shop Floor Control and Agile) and WPS (Weekly Production Scheduling) improvement. - Set up and implemented FGI ROP trigger process for Merge Center operation. - Implemented FGI Kanban and conducted buyback with customers to maintain “Lean” FG inventory. - Managed inventory and coordinated quarterly Physical Inventory across function (pre-meeting / scheduling / job assignment / reconciliation / analysis / post-mortem review) - Successfully overcame customer’s quarter-ends to fulfill customer’s peak demands by coordinating with PC, Production, Supply Chain Management and Shipping teams. Production coordination, live order management, material review and expedition, capacity review, carrier re-arrangement, update for customers. - Implemented JIT concept into Raw Component Staging and Replenishment process to manage components from Raw Component buffer HUB to Production floor. - Developed and implemented material management process, expedite procedure and commit process between customers and factory. - Streamlined Stock rotation, customer consignment return process w/ customers. Show less
-
-
-
Plastomer Technologies
-
United States
-
Plastics Manufacturing
-
1 - 100 Employee
-
Manufacturing Administrative Assistant
-
Apr 2006 - Jun 2008
Provide high-level administrative support to operations Manager, Quality and Engineering Manager as well as three Production Supervisors of a leading manufacturer of PTFE products. • Inventory control of all raw materials, WIP and final stocked products. • Involved in creating quality work instructions and control plans for ISO 9001: 2000 Quality Management system. • Involved in ISO 9001:2000 management review meetings with presentations and taking down minutes. • Created different databases using MS Access to better track various quality and engineering documentation such as: - Corrective Action Reports. - Internal Audit documentation. - Instrumentation calibration and certificate records. - Process and testing information of all products (billets) • Created database using MS Access to manage daily and monthly reports on productivity. • Analysis and reporting of all customer returns and scrap for Operations Manager and VP. • Process daily transactions from the floor to provide better traceability of materials and inventory accuracy. • Assist with final documentation in terms of shipping, product labels and packing requirements. • Certificates of Analysis and Conformance for Quality Engineer. • Worked on introducing bar code and tracking system for tracing the product flow. • Entered Bills of Material, routings and product structures for new/additional products in Mapics (ERP system) • Cycle Counts. • Daily analysis and processing transaction of “Negative on Hand” report using Mapics. Show less
-
-
Education
-
University of Johannesburg (Rand Afrikaans University)
Logistics, Materials, and Supply Chain Management -
Rand Afrikaans University
Logistics Management, Logistics, Materials, and Supply Chain Management
Community
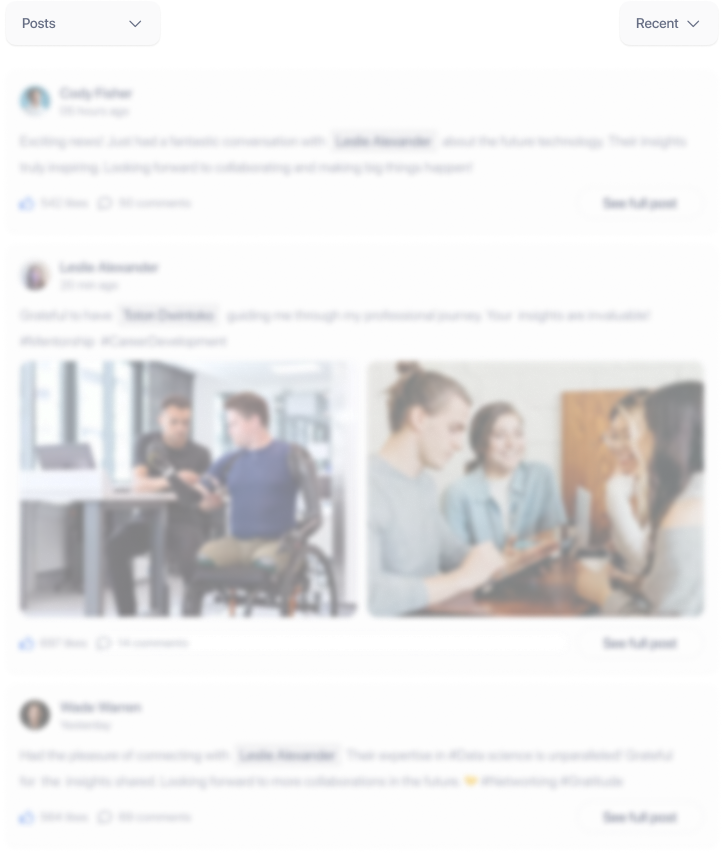