Stella Lee
Principal Consultant at PlantOPS- Claim this Profile
Click to upgrade to our gold package
for the full feature experience.
Topline Score
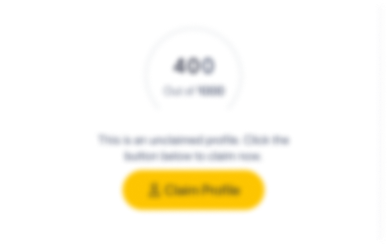
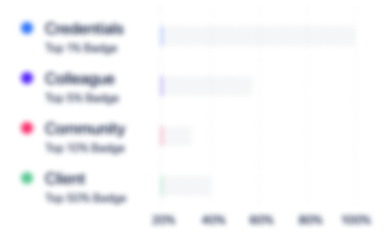
Bio


Experience
-
PlantOPS
-
Manufacturing
-
1 - 100 Employee
-
Principal Consultant
-
Aug 2023 - Present
-
-
-
Olympia Engineering LLC
-
United States
-
Automation Machinery Manufacturing
-
Senior Automation Engineer, Process Lead
-
Jun 2022 - Present
Global MES Consultant: Abbvie MES Engineer o Supported two critical BTS initiatives: PCI enhanced and Aquila o Design lead for PCI enhanced recipe blueprints for ABS Singapore o Training guide and SOP modification for Aquila o Develop and design technical solutions in POMSnet per process requirements and feedback o Supported Hypercare/ Go-live for new MES rollout o Worked with SAP and Manufacturing team to troubleshoot system integration and master… Show more Global MES Consultant: Abbvie MES Engineer o Supported two critical BTS initiatives: PCI enhanced and Aquila o Design lead for PCI enhanced recipe blueprints for ABS Singapore o Training guide and SOP modification for Aquila o Develop and design technical solutions in POMSnet per process requirements and feedback o Supported Hypercare/ Go-live for new MES rollout o Worked with SAP and Manufacturing team to troubleshoot system integration and master data discrepancies Show less
-
-
-
Genentech
-
United States
-
Biotechnology Research
-
700 & Above Employee
-
Sr Automation Engineer
-
Dec 2013 - Jun 2022
Experion R410 SCM (Sequential Control Module) and CM (Control Module) implementation, Total Plant Batch implementation, POMSnet recipe authoring CCP2 Upstream Design lead for various product transfers. Collaborated with cross functional groups to obtain process requirements to design new recipes and modify existing software objects to support operations. Change owner - Initiated change records, defined testing requirements, implemented, tested software changes, and deployed… Show more Experion R410 SCM (Sequential Control Module) and CM (Control Module) implementation, Total Plant Batch implementation, POMSnet recipe authoring CCP2 Upstream Design lead for various product transfers. Collaborated with cross functional groups to obtain process requirements to design new recipes and modify existing software objects to support operations. Change owner - Initiated change records, defined testing requirements, implemented, tested software changes, and deployed software for product transfers and site continuous improvement projects Designed and implemented solutions to simplify recipe execution, reduce costs for Manufacturing by reducing waste and reduced equipment uptime during recipe execution to support faster run rates Automation Qualification testing for POMSnet, TPB, Graphics and Experion software objects. o Generated CQ test packages, execute various tests to support validation of software objects. o Designed custom tests to support testing of several software objects to increase efficiency and reduce redundant testing.
-
-
CCP1 Master Bioprocess Technician and Shift Lead
-
Mar 2010 - Dec 2013
Vacaville, California, United States Helped team members develop goals for their PPR to further develop their skills and technical knowledge of the process Provide support and resources to accomplish their goals Ensured the shift adhered to production schedule and pushed operations in a timely manner Developed training plans with senior members of the shift to train newer members on all operations most efficiently and effectively
-
-
Actemra Tech Transfer- Upstream Fermentation Lead and Senior Bioprocess Technician
-
Mar 2007 - Mar 2010
Vacaville, California, United States Active role in recipe debug for fermentation systems in CCP2 (Cell Culture Plant2) by providing suggestions to changes to automation to ensure automation is aligned with recipe design. Worked closely with Automation team and other support groups to implement changes effectively and timely manner. Lead a team of 18 technicians to debug and troubleshoot the new recipes for Actemra. Fully trained team of technicians to successfully operate the recipes and processes for Engineering and… Show more Active role in recipe debug for fermentation systems in CCP2 (Cell Culture Plant2) by providing suggestions to changes to automation to ensure automation is aligned with recipe design. Worked closely with Automation team and other support groups to implement changes effectively and timely manner. Lead a team of 18 technicians to debug and troubleshoot the new recipes for Actemra. Fully trained team of technicians to successfully operate the recipes and processes for Engineering and Clinical runs Developed process overviews, OJT (On the Job Training), and Training Guides for new processes. Provided hands on training on how to troubleshoot the automation system during debugging process Planned, executed and responded to all debug, validation, and engineering run needs. Learned basic automation code of CCP2 automation system through troubleshooting and recipe debug.
-
-
-
Anheuser-Busch
-
United States
-
Food and Beverage Services
-
700 & Above Employee
-
Process Control Specialist
-
Jun 2006 - Mar 2007
Fairfield, California, United States Production planning to coordinate timely movement and sufficient supply of products to operations. Planned and ordered raw material and supplies according to material usage and inventories. Performed facility audits and inspections of raw material suppliers. Performed inventory audits to track material usage vs production yield to ensure costs are aligned with budget.
-
-
Brewing Group Manager I
-
Jul 2003 - Jul 2006
Fairfield, California, United States Active role in Brewhouse, Grains Unloading and Fermentation Modernization projects. Implemented process improvement suggestions and software redesign and recipe modifications. Identified issues by observing and profiling one production to another to pin point root cause. Decreased unloading time for rice trucks and grain rail cars. Reduced time required to process popular priced brands in the filtration operations, increasing weekly production capability. Active role in… Show more Active role in Brewhouse, Grains Unloading and Fermentation Modernization projects. Implemented process improvement suggestions and software redesign and recipe modifications. Identified issues by observing and profiling one production to another to pin point root cause. Decreased unloading time for rice trucks and grain rail cars. Reduced time required to process popular priced brands in the filtration operations, increasing weekly production capability. Active role in training and development of new Group Managers, Operators and Interns Helped develop training manuals and Standard Operating Procedures for Brewhouse through Fermenting with Training Coordinator to support the increasing responsibilities of the control room operators
-
-
Acting Brewhouse Area Manager
-
Jan 2006 - Jun 2006
Fairfield, California, United States Increased popular priced brand recover rates and adjusted recipes and equipment operating parameters to increase yield for new brand in development. Planned shutdown and manpower during holidays and weekends to achieve cost savings without affecting quality of products or delaying operations. Coordinated with Process Support and contractors for windows to shutdown equipment without impacting production goals. Planned and scheduled average production of 60.000 barrels through… Show more Increased popular priced brand recover rates and adjusted recipes and equipment operating parameters to increase yield for new brand in development. Planned shutdown and manpower during holidays and weekends to achieve cost savings without affecting quality of products or delaying operations. Coordinated with Process Support and contractors for windows to shutdown equipment without impacting production goals. Planned and scheduled average production of 60.000 barrels through the Brewhouse.
-
-
Education
-
University of California, Davis
Minor Japanese, Viticulture and Enology
Community
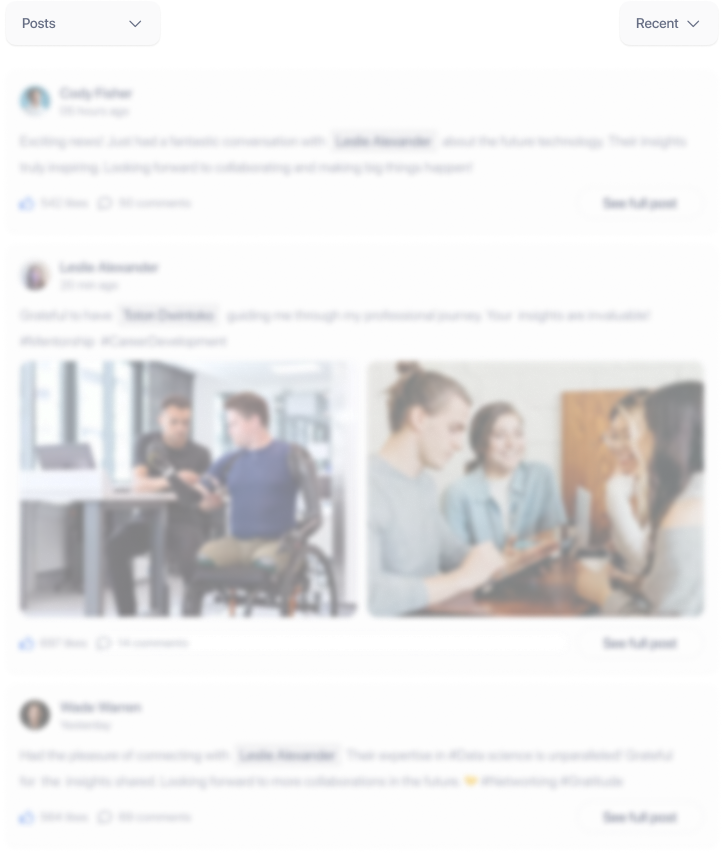