Stefan Calle
Supply Chain Manager - Distribution & Logistics at Sonance- Claim this Profile
Click to upgrade to our gold package
for the full feature experience.
Topline Score
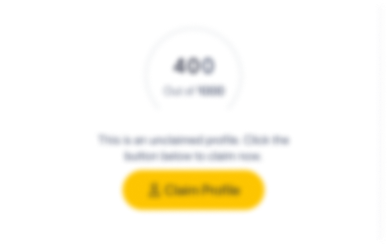
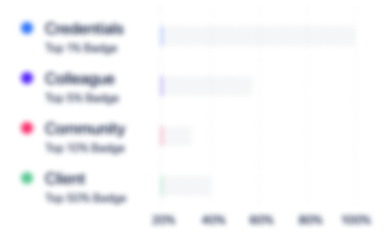
Bio

Robert Jaynes
I had the pleasure of working with Stefan as I oversaw the leadership development program he was in, and found him to be really engaged. He was thoughtful and smart about Supply Chain issues. I then had the opportunity to work with him on a project to improve the commercialization process we used to launch new products. Stefan was passionate about improving that process, and smart about the approach.

Robert Jaynes
I had the pleasure of working with Stefan as I oversaw the leadership development program he was in, and found him to be really engaged. He was thoughtful and smart about Supply Chain issues. I then had the opportunity to work with him on a project to improve the commercialization process we used to launch new products. Stefan was passionate about improving that process, and smart about the approach.

Robert Jaynes
I had the pleasure of working with Stefan as I oversaw the leadership development program he was in, and found him to be really engaged. He was thoughtful and smart about Supply Chain issues. I then had the opportunity to work with him on a project to improve the commercialization process we used to launch new products. Stefan was passionate about improving that process, and smart about the approach.

Robert Jaynes
I had the pleasure of working with Stefan as I oversaw the leadership development program he was in, and found him to be really engaged. He was thoughtful and smart about Supply Chain issues. I then had the opportunity to work with him on a project to improve the commercialization process we used to launch new products. Stefan was passionate about improving that process, and smart about the approach.

Experience
-
Sonance
-
United States
-
Consumer Electronics
-
100 - 200 Employee
-
Supply Chain Manager - Distribution & Logistics
-
Aug 2023 - Present
-
-
-
Speedo
-
Retail Apparel and Fashion
-
200 - 300 Employee
-
Senior Supply Chain Analyst
-
Sep 2022 - Jun 2023
- Develop reporting using internal and external data sources such as SAP, Nexus, and Smartsheet. - Perform statistical analysis on data sets containing millions of individual data points in order extract information relevant to KPI’s, vendor performance, and PO/Material/Style accuracy. - Help to develop structure around weekly activities and tasks that help to address issues that may arise systematically and with counterparts working at on-site locations. - Creation of the Transit Time Analysis utilizing reporting from K&N in order to determine actual Lead times from overseas origin to Distribution Center. - Develop tool for analyzing containers in order to determine the correct DC destination based on Material/Style/SMU within the container. - Assist in Project Breeze execution by working cross functionally with Planning, Finance, Sales and Operations in order to streamline information flow in order to ensure visibility to inventory during DC transition to allow for customer orders to be supported. - Monitor external reporting in order to prevent additional costs associated with demurrage and detention. - Support and maintain Maersk Inbound tracker to provide external partners with visibility to incoming material good shipments through communication of relevant information such as PO and delivery numbers, quantities, styles, packing details and ETA to facility. Show less
-
-
-
Ryder Supply Chain Solutions
-
United States
-
Transportation, Logistics, Supply Chain and Storage
-
700 & Above Employee
-
Operations Manager
-
Feb 2021 - Dec 2021
3PL Operations Manager: - Responsible for managing Inbound, Outbound, Inventory, and Maintenance Departments within 750,000 sq. ft. facility. - Direct reports include hourly, salary, and department managers. - Managing relationship with 3PL Customer. - Completing Weekly, Monthly, and Quarterly Business Reviews. - Developing KPI's to drive productivity and performance efficiencies. - Implementing Lean and Safety initiatives to help drive standardization, accountability and safety improvements. - Collaborating cross-functionally to develop new operational processes to improve facility throughput by 55%. - Developing Leader Standard Work (LSW) for Leads, Supervisors, and Managers as part of standardization and training program. - Revamping Quality Audits and procedures to reduce customer chargebacks and drive improved compliance. - Creation of a Safety Committee to facilitate continuous safety improvements across the site and to bring awareness to OSHA rules and standards. - Streamlining of Outbound loading processes to reduce driver wait time by 60% - Development of Drop Trailer program to enable 24/7 pick-ups and reduce facility carrier failure rate by 20% - Certified Forklift Trainer Show less
-
-
-
Amway
-
United States
-
Manufacturing
-
700 & Above Employee
-
Distribution Manager
-
May 2020 - Feb 2021
1st Shift Distribution Manager at Amway California Regional Service Center Responsibilities include: - Supporting and managing a team of 15 full time employees and 20-50 temporary staff employees. - Coaching and training employees within fulfillment, replenishment, inbound, and outbound operations. - Ensuring customer and ABO orders are fulfilled in full and on-time (OTIF). - Auditing facility to ensure we are meeting regulatory, safety, and company standards. - Development and execution of projects focused on improving customer experience, inventory accuracy, order fulfillment speed, and safety. - Collaboration across functions to establish and implement pandemic safety initiatives in order to improve employee safety and reduce outbreak risks. - Show less
-
-
-
Self Employed
-
United States
-
700 & Above Employee
-
Business Performance Consultant
-
Jun 2019 - May 2020
Business Performance Consultant responsibilities include: - Assessing client operations to determine impact of project work. - Advising management on pros and cons of different technical and management consulting approaches. - Leveraging statistical models in order to validate data inputs and allow for distribution and network modeling. - Provide recommendations to clients with financial implications to both top and bottom line. - Develop metrics, processes and training for implementation of new programs and initiatives. - Business analytics verification leveraging statistical models. - Partner with numerous consulting firms in order to be able to provide comprehensive business solutions regardless of industry. Show less
-
-
-
DB&A - DeWolff, Boberg & Associates, Inc
-
United States
-
Business Consulting and Services
-
100 - 200 Employee
-
Management Consultant
-
Mar 2019 - Jun 2019
- Professionally service client organizations to solve business issues, create value, maximize growth and improve overall performance for sustainability. - Quickly become familiar with client business challenges and technologies to understand the environment for behavioral changes. - Gather, organize and analyze data regarding key business drivers to present information in a manner that is meaningful to clients by using metrics and analytics to guide organizational decision making. - Thoroughly understand client resource utilization to identify operational and performance improvement opportunities. - Openly, respectfully and professionally discuss business and organizational shortcomings with clients to provide valuable feedback and influence solutions for long-term sustainability. - Empower front-line accountability of actions, roles and responsibilities by guiding clients through self-explorations of their business segments and staff utilization. - Collaborate with front-line leaders on a daily basis to improve leadership and management behaviors. - Strong facilitation skills and ability to build relationships and interface with clients at all levels of the organization. - Effectively coach clients to approach their business issues as forward thinkers to exude confidence for improving behaviors and process efficiencies. - Ability to juggle many responsibilities at one time to effectively partner with clients throughout the project life-cycle. - Foster a spirit of teamwork and unity among project team members that allows for healthy disagreements – expeditiously resolve conflicts by approaching with positive cohesiveness, supportiveness and working effectively together to enable the overall team to succeed. Show less
-
-
-
General Mills
-
United States
-
Manufacturing
-
700 & Above Employee
-
End-to-End Logistics Planner
-
Feb 2017 - Feb 2019
Logistics Planner roles help to enable optimized performance for Business Units by consolidating multiple Supply Chain functions into a single role.As a Logistics Planner responsibilities include, but are not limited to: - Developing and executing inventory and manufacturing strategies set with the broader Supply Chain and Business Operating Units. - Creation of Capacity Models in monthly cadence to review manufacturing capabilities and utilization at manufacturing locations across the network.- Development of Master Schedule to support Finite Level execution at manufacturing locations.- Planning and execution with broader cross-functional business team to support new product launches, innovation, and Lean/Six Sigma initiatives.- Supporting new product commercialization through cross-functional collaboration with Sales, Marketing, R&D, Finance, and numerous other stakeholders. Show less
-
-
Brand Planner
-
Jun 2016 - Jan 2017
Brand Planner supporting Baking Operating Unit at General Mills Headquarters in Golden Valley, MN. Responsible for planning and facilitating Supply Chain execution on Marketing projects to support new product launches across multiple household name brands.
-
-
Logistics Team Leader
-
Dec 2015 - Jun 2016
Floor Supervisor assisting with coordination and execution of daily and long term Logistics oriented tasks at the manufacturing level to support Convenience and Food Service (C&F) business.Team Lead responsibilities include: - Top priorities of ensuring Food Safety of products and Human Safety of all employees. - Removing barriers for team members to streamline Logistics operations and workflow including regular troubleshooting of Red Prairie Warehouse Management System. - Auditing of Logistics owned areas, including receiving and shipping warehouses, to ensure compliance with OSHA, FSSC, and upcoming Food Safety Modernization Act (FSMA) standards. - Implementation of facility safety improvements through cross functional cooperation with Operations, Maintenance, and Logistics Technician team. - Execution of Work Measurement project to benchmark Logistics department workload. - Creation of Work Measurement tool to quantify total pallet movement within department for the purpose of balancing staffing levels and development of KPI's. - Assisting HR with screening of potential candidates for open positions within Logistics department. - Assisting team members with development of standardized training materials for new employee on-boarding programs. - Annual Performance Appraisals for department employees. - Leading Business Development Training for Logistics team members. Show less
-
-
Finished Product Inventory Management
-
Jan 2015 - Dec 2015
Finished product inventory planning and scheduling. Coordinating movement of 100+ SKU's across National and International network of Central Storage Facilities through collaboration with Brand specific Deployment teams and 10+ Transportation Carrier Partners.Continuous Improvement Project to design optimal loads in order to maximize trailer utilization through analysis of loading procedures. Project increased average pallets per truck from 46 pallets/truck to 54 pallets/truck. Load optimization also increased throughput in Cubes per Labor Hour by approximately 20% from Fiscal 2015 through current Fiscal 2016. Direct interaction with Customers to support Direct Product Shipment program (DPS) from Manufacturing facility. Coordination of on time pick-up and delivery through carrier partners.Product Age Review process improvement helped to avoid over $70,000 of finished product destroy write-offs.Facilitation and creation of donation orders for Second Harvest/Food Bank to support local community.Analysis of production and inventory levels to develop shipping volume forecast for plant decommission and closure using excel and SAP reporting tools.Active monitoring and management of CHEP ordering process to minimize over-ordering practices. Show less
-
-
Production Scheduling and Raw Material Inventory Management
-
Jun 2014 - Dec 2015
Raw Material and Production Schedule Planning for United States Retail Organization within General Mills.Interfacing with SAP and WMS interfaces and using Lean/Six Sigma strategies in order to develop ordering and production plans that will minimize plant costs. Using Bill of Materials in order to develop safety stock based on material lead time.Development of ordering strategy that resulted in 0 plant shutdowns due to raw material inventory maintenance and tracking during Fiscal 2015. Ordering strategy also resulted in $0 of write-offs due to raw materials expiration.Facilitating and development of cultural attitude to sustain and improve High Performance Work System used within the facility.Development and execution of Continuous Improvement projects based on business needs. Focus of projects is to increase operating efficiency and allow for more flexible production capabilities. Project resulted in reduction of needed changeovers by 30% while still supporting fluctuating product demand. Show less
-
-
-
University of Central Florida
-
United States
-
Higher Education
-
700 & Above Employee
-
Teaching Assistant
-
Aug 2013 - May 2014
-
-
-
ScreenWorks USA
-
United States
-
Retail Apparel and Fashion
-
1 - 100 Employee
-
Industrial Engineer/ Process Optimization Intern
-
Sep 2012 - Dec 2013
-
-
Education
-
University of Central Florida
Bachelor of Science (B.S.), Industrial Engineering
Community
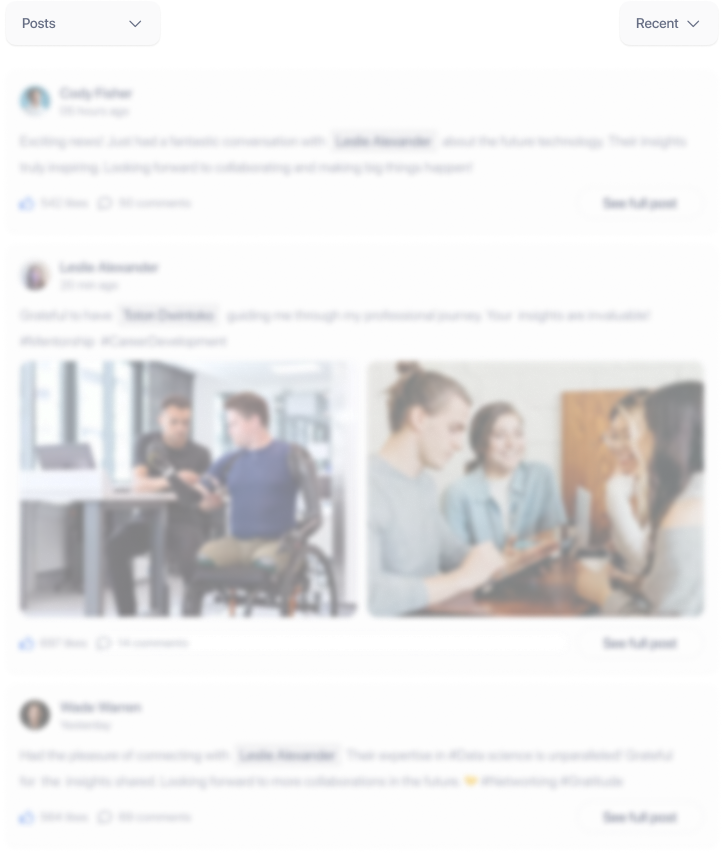