shankara raman
Director Technical at Pushkar Techno Private Limited- Claim this Profile
Click to upgrade to our gold package
for the full feature experience.
-
English Full professional proficiency
-
Hindi Professional working proficiency
-
Tamil Professional working proficiency
-
Bengali Limited working proficiency
Topline Score
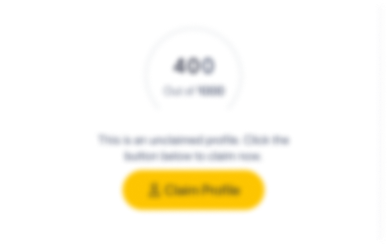
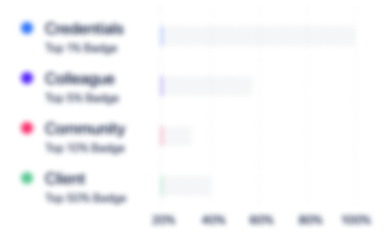
Bio


Experience
-
Pushkar Techno Private Limited
-
India
-
Mechanical Or Industrial Engineering
-
1 - 100 Employee
-
Director Technical
-
Oct 2015 - Present
-
-
-
Quality Austria Central Asia Pvt. Ltd.
-
India
-
Business Consulting and Services
-
500 - 600 Employee
-
Empaneled IATF 16949 Lead Auditor
-
Sep 2018 - Present
-
-
-
-
AGM , Lead Quality Engineering
-
Apr 2014 - Oct 2015
Responsible for Strategic Quality of Jamshedpur Plant encompassing a) Developing and Deploying Balanced Score Card for Quality Function b) Reduction of Plant Warranty c) Quality Budgeting d) IT Development and Deployment for MIS e) Development and Deployment of Tata Motors Production System for Quality Engg. Function f) Implementing World Class Quality initiative, Plant Lead for Built in Quality. Responsible for Conformance Quality w.r.t a) Material conformance for incoming parts ( Metallurgy, Oil, Polymer & Paint Labs) b) Conformance of Surface Protection on Incoming Parts c) Metrology Labs
-
-
-
-
AGM , Forward Model Quality
-
Jan 2012 - Mar 2013
• Proficiently established FMQ a new vertical created to ensure design quality in the NPI Process• Approve Design modifications through DFMEA review (CFT Approach)• Played a vital role in streamlining CFT participation in DFMEA review prior to design release through training of relevant officers on DFMEA, Aggregates, Getting Buy in of Senior Management and Regular Reviews• Proficiently launched Prima LX through FMQ route of validation & Productionisation• Worked on Advance Product Quality Plan (APQP) & Production Part Approval Process (PPAP) for new products introduction at vehicle level
-
-
Asst General Manager, Supplier Quality Improvement Group
-
Jul 2007 - Mar 2013
• New Vendor Enlistment and Vendor development for Sheet metal/ Casting/ Forging/ & Machining.• Establishing Vendor Rating, Vendor Evaluation and Vendor Base Rationalisation.• Developed, headed & supervised a team of 24 officers in SQIG for addressing bought out parts quality issues• As Head Supplier Quality Improvement Group started the initiative of Process Mapping, Monitoring and control of KPIVs and KPOVs, PDI Station, First & Last PC inspection for quality control at supplier end, thereby enhancing their performance in incoming at Tata Motor’s and their response to in house Quality issues.• Steered efforts in introducing Systematic Capability building of Tier 1 suppliers through ACMA/ CII Cluster Programme:o 2010-2012- Mentor for ACMA ACT 24 month Cluster programme, 8 Suppliers had participated with Mr. KPS Raghuvanshi as Counselloro 2010-2011- Mentor for ACMA Preparatory Cluster Programme, 16 Suppliers had participated with Mr. KPS Raghuvanshi as Counsellor Major Achievements were PPM Reduction, Improvement in Vendor Quality Rating, CEO involvement in plant, 5S improvement, Implementation of Quality Tools & Mistake Proofing, Waste Elimination, TPM Step1 & 2, SMED, and Reduction of inventory in RM/WIP / FG.o 2012-13- Mentor for NPC 12 month Cluster programme (3 nos), 25 Suppliers had participated Major Achievement was introduction to Lean Management.• Successfully executed a project of developing pallets for skin panels o Root Cause Analysis through 8D methodology & initiation of POKA YOKE solutions o Process Audits at supplier works for capability improvements o System Audit for effective implementation of the quality standard (TS16949/OHSAS/EnMS/EMS)• Key person in evolving Logistics & Packaging Manual for TML, Jamshedpur, thereby adopted across the other locations in the organization• Distinction in reducing PPM 76% of bought out parts from local ancillaries from approx. 800 to below 190 in 2yrs
-
-
-
Tata Motors, Jamshedpur
-
India
-
Appliances, Electrical, and Electronics Manufacturing
-
1 - 100 Employee
-
Asst. General Manager, Vendor developmet
-
Nov 1997 - Jun 2007
• As Head Sheet metal Development ensured timely Development of:o Approximately 1000 parts during change over from TATA engine to Cummins Engine in 2002-03 involving approximately 100 Suppliers.o Approximately 600 parts during change over from BSI to BSIIo First time OK development of 16 Parts for SD Fatroll in a record time of 4 days which otherwise would take 3 months and helped Tata Motors in overcoming crisis situationo Revived M/s Jayshree Enterprises and ran the company for two months during their bankruptcy phase and ensured smooth availability of material at Tata Motors and also converted their Loss making situation to profit making.• Essayed a stellar role in enhancing capacity of EDAG line from 60 cab/shift to 140/shift through improvement in supply chain (Procurement in higher assembly, Part correction, Green room at vendors end)• Identified & implemented benchmark process for fabrication parts & new suppliers for existing range of part families• Efficiently involved in supplier development and resolved their issues with Tata Motors• New Vendor Enlistment and Vendor development for Sheet metal/ Casting/ Forging/ & Machining.• Establishing Vendor Rating, Vendor Evaluation and Vendor Base Rationalisation.
-
-
Manager Production & Maintenance
-
Jun 1989 - Oct 1997
• Monitoring production operations with respect to cost, resource deployment, time over-runs, quality compliance and manpower planning to ensure timely execution of activities for Kurimoto and Nissie Line manufacturing Fornt Axle Beam and Crank Shaft respectively• Handling the planning, scheduling and management of production; ensuring completion of assignments within time and budgetary parameters• Planning & effectuating predictive & preventive maintenance schedules for various equipment / lines to increase machine uptime & equipment reliability• Implementing maintenance schedules and carrying out periodic checks to ensure performance of various equipment and maintaining requisite documents for the same• Taking stringent quality measures including preparation of necessary documents for ensuring compliance with standards & customer requirements• Executing various techniques for cycle time / cost reduction, entailing identification of opportunities, analysis of data, conducting tests, cost benefit analysis and implementation• Imparting continuous on job training to the workforce for accomplishing greater operational effectiveness / efficiency• Significantly contributed in augmenting production of FAB from 200/day to 180/shift through Line balancing, reducing cycle time & die setup time, improving plant up time and increasing die life & employee involvement
-
-
Education
-
Bihar Institute of Technology
Bachelor’s Degree, Production Enggineering -
DBMS HIGH SCHOOL
High School, Science -
Loyola High School
ICSE, 1st Division
Community
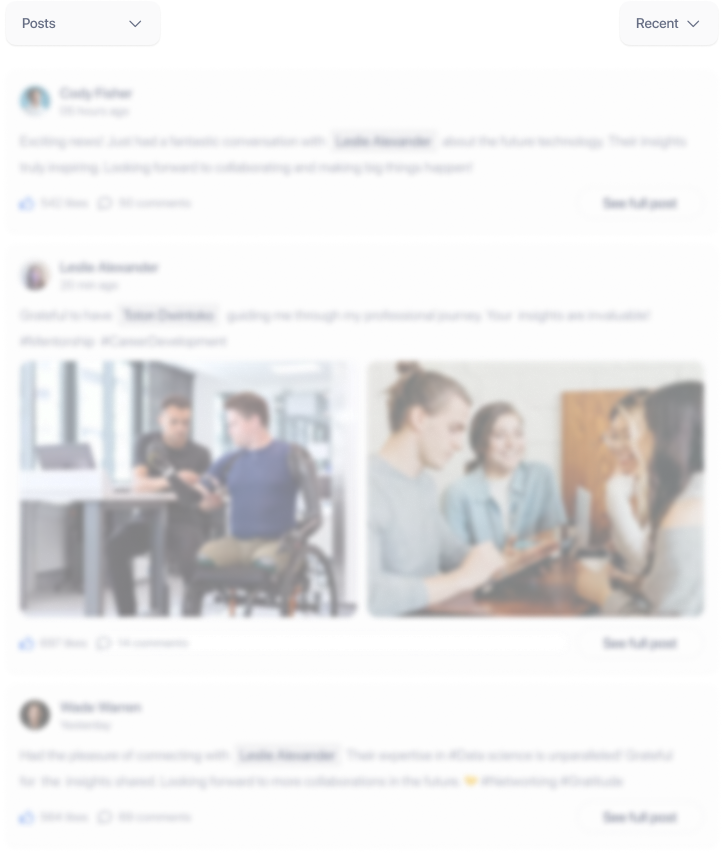