Spurgeon Baker,MBA
Group Controller at Nucor Warehouse Systems- Claim this Profile
Click to upgrade to our gold package
for the full feature experience.
Topline Score
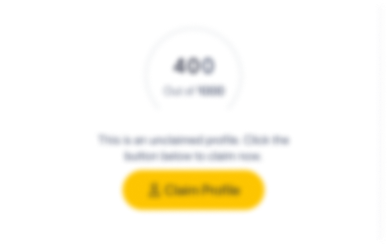
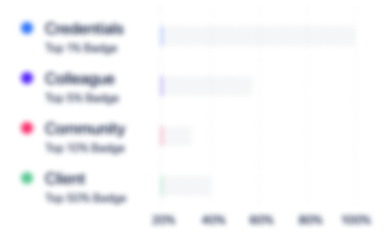
Bio

J David Green
I have know Spurgeon Baker for the last 10 years, from his time at SRG Global as Plant Controller for the Covington, Georgia Plant. As Corporate Executive Master Black Belt, I have watched him grow as a leader, a professional and a problem solver. He has always impressed me with his ability to deal with complex and critical circumstances in a calm, confident manner that draws colleagues to him to form effective teams. My role as Executive Master Black Belt, for SRG Global, World Wide, brought us together often to prioritize projects and create value. The key was not just supporting each team, but developing leadership from within for promotability. Spurgeon not only identified the best candidates and helped focused project objectives, but mentored many individuals thru the learning curve of applied lean six sigma methodology. The results included sustainable solutions that improved efficiencies, reduced cost of quality and developed management talent. Time ran out before I could recognize Mr. Baker as a Master Black Belt. He was and is a worthy candidate for the title. His enthusiasm is contagious. J David Green, Executive Master Black Belt,

Tom Schneider
I had the pleasure of working with Spurgeon for more than 10 years. During that time, I knew him to be a very capable Finance Manager and an asset to the business. He was able to relate manufacturing issues and accounting metrics so that the business could be managed effectively. Spurgeon has a very good personality and interacts well with all levels in an organization. I knew him to be a good manager. His reports grew in skill and were always positive because of Spurgeon's leadership. I would recommend Spurgeon for any position in manufacturing or finance.

J David Green
I have know Spurgeon Baker for the last 10 years, from his time at SRG Global as Plant Controller for the Covington, Georgia Plant. As Corporate Executive Master Black Belt, I have watched him grow as a leader, a professional and a problem solver. He has always impressed me with his ability to deal with complex and critical circumstances in a calm, confident manner that draws colleagues to him to form effective teams. My role as Executive Master Black Belt, for SRG Global, World Wide, brought us together often to prioritize projects and create value. The key was not just supporting each team, but developing leadership from within for promotability. Spurgeon not only identified the best candidates and helped focused project objectives, but mentored many individuals thru the learning curve of applied lean six sigma methodology. The results included sustainable solutions that improved efficiencies, reduced cost of quality and developed management talent. Time ran out before I could recognize Mr. Baker as a Master Black Belt. He was and is a worthy candidate for the title. His enthusiasm is contagious. J David Green, Executive Master Black Belt,

Tom Schneider
I had the pleasure of working with Spurgeon for more than 10 years. During that time, I knew him to be a very capable Finance Manager and an asset to the business. He was able to relate manufacturing issues and accounting metrics so that the business could be managed effectively. Spurgeon has a very good personality and interacts well with all levels in an organization. I knew him to be a good manager. His reports grew in skill and were always positive because of Spurgeon's leadership. I would recommend Spurgeon for any position in manufacturing or finance.

J David Green
I have know Spurgeon Baker for the last 10 years, from his time at SRG Global as Plant Controller for the Covington, Georgia Plant. As Corporate Executive Master Black Belt, I have watched him grow as a leader, a professional and a problem solver. He has always impressed me with his ability to deal with complex and critical circumstances in a calm, confident manner that draws colleagues to him to form effective teams. My role as Executive Master Black Belt, for SRG Global, World Wide, brought us together often to prioritize projects and create value. The key was not just supporting each team, but developing leadership from within for promotability. Spurgeon not only identified the best candidates and helped focused project objectives, but mentored many individuals thru the learning curve of applied lean six sigma methodology. The results included sustainable solutions that improved efficiencies, reduced cost of quality and developed management talent. Time ran out before I could recognize Mr. Baker as a Master Black Belt. He was and is a worthy candidate for the title. His enthusiasm is contagious. J David Green, Executive Master Black Belt,

Tom Schneider
I had the pleasure of working with Spurgeon for more than 10 years. During that time, I knew him to be a very capable Finance Manager and an asset to the business. He was able to relate manufacturing issues and accounting metrics so that the business could be managed effectively. Spurgeon has a very good personality and interacts well with all levels in an organization. I knew him to be a good manager. His reports grew in skill and were always positive because of Spurgeon's leadership. I would recommend Spurgeon for any position in manufacturing or finance.

J David Green
I have know Spurgeon Baker for the last 10 years, from his time at SRG Global as Plant Controller for the Covington, Georgia Plant. As Corporate Executive Master Black Belt, I have watched him grow as a leader, a professional and a problem solver. He has always impressed me with his ability to deal with complex and critical circumstances in a calm, confident manner that draws colleagues to him to form effective teams. My role as Executive Master Black Belt, for SRG Global, World Wide, brought us together often to prioritize projects and create value. The key was not just supporting each team, but developing leadership from within for promotability. Spurgeon not only identified the best candidates and helped focused project objectives, but mentored many individuals thru the learning curve of applied lean six sigma methodology. The results included sustainable solutions that improved efficiencies, reduced cost of quality and developed management talent. Time ran out before I could recognize Mr. Baker as a Master Black Belt. He was and is a worthy candidate for the title. His enthusiasm is contagious. J David Green, Executive Master Black Belt,

Tom Schneider
I had the pleasure of working with Spurgeon for more than 10 years. During that time, I knew him to be a very capable Finance Manager and an asset to the business. He was able to relate manufacturing issues and accounting metrics so that the business could be managed effectively. Spurgeon has a very good personality and interacts well with all levels in an organization. I knew him to be a good manager. His reports grew in skill and were always positive because of Spurgeon's leadership. I would recommend Spurgeon for any position in manufacturing or finance.

Experience
-
Hannibal
-
United States
-
Warehousing and Storage
-
100 - 200 Employee
-
Group Controller
-
May 2022 - Present
-
-
-
Elite Storage Solutions
-
United States
-
Warehousing and Storage
-
1 - 100 Employee
-
Chief Financial Officer - Finance and Administraton
-
May 2021 - Jul 2022
Transformed Finance and Accounting structure, functions, improved controls and reporting Treasury and cash management responsibilities and forecasting Experienced with financial statement preparation, consolidation and analysis Manufacturing variance analysis and reviews Short-term and long-term business planning Business systems process improvement Internal Control/Compliance/Risk Costing; activity based and standard cost Strong Leadership, team building and… Show more Transformed Finance and Accounting structure, functions, improved controls and reporting Treasury and cash management responsibilities and forecasting Experienced with financial statement preparation, consolidation and analysis Manufacturing variance analysis and reviews Short-term and long-term business planning Business systems process improvement Internal Control/Compliance/Risk Costing; activity based and standard cost Strong Leadership, team building and Visionary Database SQL Query and data mining Inventory variance review and reporting Conducts balance reviews Versatile in ERP deployment to meet various business functional needs Supervises Project Accounting and Fixed Asset Accounting Manages HR, Payroll, IT, Inventory Control and EHS
-
-
Corporate Controller
-
Nov 2017 - May 2021
The primary purpose of this position is to manage and direct the daily accounting activities within the organization; provide cash management and cash flow analysis; create annual budgets and monitor trends; manage the short and long-term strategic goals; consolidation of multiple manufacturing location’s financial statements; coordinate the preparation of annual tax returns and financial audits with external CPA partners; provide debt management analysis; prepares and provide ad-hoc… Show more The primary purpose of this position is to manage and direct the daily accounting activities within the organization; provide cash management and cash flow analysis; create annual budgets and monitor trends; manage the short and long-term strategic goals; consolidation of multiple manufacturing location’s financial statements; coordinate the preparation of annual tax returns and financial audits with external CPA partners; provide debt management analysis; prepares and provide ad-hoc financial analysis, sales analysis reporting, commissions analysis; prepare presentations for owners and executive staff •Managed and completed a 100% accounting staff turnover within 6 months •Reduced AR past dues by initiating frequent reviews with the sales team, our valued customers and shipping personnel; resulted in a collection of $345K of a $368K aged balance in less than 30 days •Improved weekly cash flow forecasting from 70% to 95% by utilizing a structured team accountability approach •Continual improvement in quality, timeliness, and reliability of financial analysis and key performance metrics available to executive management. including forecasting, budgeting, and resource allocation in all areas •Drive performance management tied to key metrics/KPIs/business drivers that provide a forward-looking view into trends requiring management decisions and actions •Manage all aspects of project accounting reporting and analysis; 30+ jobs worth $25M •Cost Accounting analysis of bills of material; labor review of headcounts; review overhead rate construction; identify material usage variances; identify causes of over/under absorptions of labor and overhead •Eliminated account reconciliation variances and improved timing from 4 days to 2 by utilizing custom excel queries, VLOOKUP’s and pivot tables •Create annual capital expenditure plan and prepares variance analyses to budget •Ensures all internal policies and procedures are in place and are adhered to protect company assets
-
-
-
SRG Global
-
United States
-
Motor Vehicle Manufacturing
-
700 & Above Employee
-
Plant Controller
-
Feb 2007 - Nov 2017
Global supplier of Tier 1 automotive parts (Domestic and Import OEM $80M in sales) The primary purpose of this position is to manage and direct the daily accounting and finance activities; provided financial statement preparation and analysis; promoted continuous improvement practices with all accounting function; complied with all corporate reporting requirements; ensured internal control protocols were adhered to; participated in all cross functional team initiatives designed for cost… Show more Global supplier of Tier 1 automotive parts (Domestic and Import OEM $80M in sales) The primary purpose of this position is to manage and direct the daily accounting and finance activities; provided financial statement preparation and analysis; promoted continuous improvement practices with all accounting function; complied with all corporate reporting requirements; ensured internal control protocols were adhered to; participated in all cross functional team initiatives designed for cost reductions; worked closely with various manufacturing teams to ensure accurate and timely reporting of all production data; and provided analysis of production variance •Implemented a fixed asset bar coding program that uncovered $400K worth of assets still were being depreciated at a cost of $56K; assets were moved to another location but were not transferred in the fixed asset system •Prepared and presented annual and long-range business plans to executive staff along with a short-term strategic review •Revamped monthly financial projections process to seek a higher level of accuracy by facilitating a cross-functional approach to forecasting resulting in 10% reduction in input errors •Implemented a preventative maintenance system to be used in by the maintenance and spare parts crib; supported the use of predictive data streaming from the production machines to leverage the timely purchase of critical spare parts and supplies; saved $15K in five months by having enough time to shop for better pricing •Oversaw the migration of AP and AR to a shared services center; exceeded estimated completion date by 2 weeks •Involved the Accounting team in plant related audits, process reviews and customer quality reviews; part of the development and training of the team to increase their value
-
-
Production Control Manager
-
Jul 2005 - Jan 2007
Production Control Manager July 2005 – January 2007 The primary purpose of this position is to manage the daily activities within a 200,000 sq. ft. finished goods and raw materials warehouse; managed customer relationships with 7 automotive manufacturing facilities; coordinated the on-time delivery of raw materials and returnable packaging to ensure on-time delivery of manufactured products •Increased customer delivery scores by 15% by utilizing process flow mappings and increased… Show more Production Control Manager July 2005 – January 2007 The primary purpose of this position is to manage the daily activities within a 200,000 sq. ft. finished goods and raw materials warehouse; managed customer relationships with 7 automotive manufacturing facilities; coordinated the on-time delivery of raw materials and returnable packaging to ensure on-time delivery of manufactured products •Increased customer delivery scores by 15% by utilizing process flow mappings and increased communications to production staff; process reduced finished product stock outs by 22%; reduced expedited shipping costs by $60k in the first year of implementation •Simplified warehousing processes with the introduction of RF units; eliminated operational inefficiencies caused from manual batch processing; reduced searches for missing stock by 60% within first 3 weeks of implementation •Instituted a weekly container management review process with our customers to minimize the container shortages on the production floor; our customers were not consistent in returning containers
-
-
Operations Manager
-
Jan 2005 - Jun 2005
The primary purpose of this position is to provide customers with on-time delivery of defect free products; provided operational updates and recommendations to strategic plans; prepared and completed action plans supporting any deviations from financial metrics; initiated production planning to support established finished good levels; reported on daily quality targets and supported the necessary actions required to meet and exceed customers’ standards and expectations; analyzed work cell… Show more The primary purpose of this position is to provide customers with on-time delivery of defect free products; provided operational updates and recommendations to strategic plans; prepared and completed action plans supporting any deviations from financial metrics; initiated production planning to support established finished good levels; reported on daily quality targets and supported the necessary actions required to meet and exceed customers’ standards and expectations; analyzed work cell process flows and layouts designed to increase maximize throughput and reduce fatigue •Reduced daily startup costs by 15% and implemented new production procedures that maintained an 85% schedule accuracy •Created weekly cross functional team meetings that identified waste opportunities, addressed quality issues and customer’s concerns; process drastically improved working relationships and encourage working together to resolve issues in timely manner •Performed product quality reviews on FG products stored in the warehouse; review process initially reported 13% quality defects on 500 part numbers; number was reduced in 6 months to 3%; those are parts that would have reached customers and would have been rejected •Managed the day-to-day operations of the injection molding, painting, extrusion and assembly processes within a 100,000 sq. ft. manufacturing facility; 120 employees on 3 shifts •Initiated lean manufacturing activities to drive labor costs down by 20% and increased productivity by 15% •Assisted in the development of internal systems designed to ensure compliance of Total Quality Management (TQM) and ISO 9000 systems; trained in ISO 9001 and TS-16949 standards •Reduced manufacturing variances by 16% and identify inventory shrinkage issues by mapping the process flow; process flow added key quality check points throughout the production cycle
-
-
Plant Controller
-
Aug 2001 - Dec 2004
The primary purpose of this position is to manage and direct the daily accounting and finance activities; provided financial statement preparation and analysis; promoted continuous improvement practices with all accounting function; complied with all corporate reporting requirements; ensured internal control protocols were adhered to; participated in all cross functional team initiatives designed for cost reductions; worked closely with various manufacturing teams to ensure accurate and timely… Show more The primary purpose of this position is to manage and direct the daily accounting and finance activities; provided financial statement preparation and analysis; promoted continuous improvement practices with all accounting function; complied with all corporate reporting requirements; ensured internal control protocols were adhered to; participated in all cross functional team initiatives designed for cost reductions; worked closely with various manufacturing teams to ensure accurate and timely reporting of all production data; and provided analysis of production variance •Managed and coached a staff of 5 in the areas of Accounting, Payroll, A/P, A/R and I/T departments •Designed ad-hoc reporting formulated to target opportunities, improvements to overall plant profitability, improves cash flow, elimination of material variances and other financial metrics •Analyzed key performance metrics to ensure continued profitability at the manufacturing site •Initiated lean manufacturing objectives designed to reduce labor costs, inventory shrinkage and increase productivity •Developed and strengthened the Accounting and Operational relationships to ensure the achievement of common strategic goal
-
-
Education
-
Lindenwood University
Master's degree, Business Administration and Management, General -
Heidelberg University
Bachelor of Business Administration - BBA, Business Administration and Management, General
Community
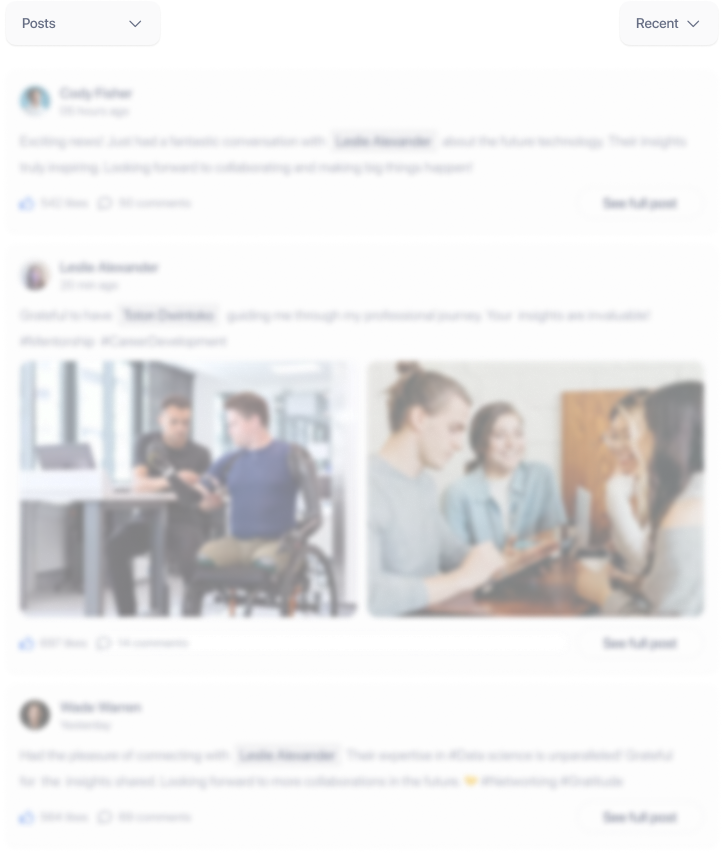