Spencer L Young
Quality Inspector at SSI Manufacturing Technologies- Claim this Profile
Click to upgrade to our gold package
for the full feature experience.
Topline Score
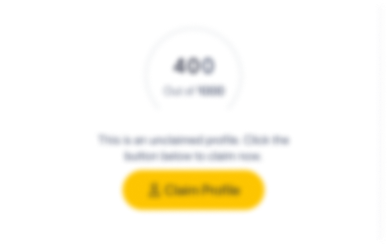
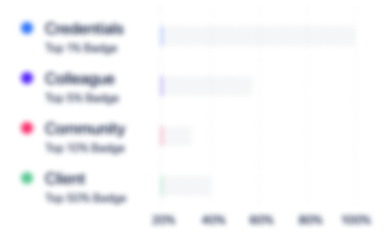
Bio

Doug Robertson
I worked with Spencer on a number of new product introductions and product line expansions. Spencer is a very detail oriented and thorough manufacturing engineer. During the course of those projects he both lead and participated as a team member in process risk assessments and process validations. He was effective in the identification of process requirements and material specifications that would need to be addressed to ensure product safety and effectiveness for new products and new manufacturing technologies. His work on the investigations of non-conformance issues demonstrated the use of appropriate root cause determination tools. He is knowledgeable in process risk assessments and the designation of the applicable hazards to be controlled to mitigate product risk.

Nigel Smith - Biomedical Consultancy Ltd
Spencer is a dedicated, thorough and competent Process Engineer that I have worked with on a range of technically challenging and advanced processes whilst at Synthes Inc. He is an excellent team member who is diligent, knowledgeable and able to bring both creative and pragmatic solutions to bear on issues.

Doug Robertson
I worked with Spencer on a number of new product introductions and product line expansions. Spencer is a very detail oriented and thorough manufacturing engineer. During the course of those projects he both lead and participated as a team member in process risk assessments and process validations. He was effective in the identification of process requirements and material specifications that would need to be addressed to ensure product safety and effectiveness for new products and new manufacturing technologies. His work on the investigations of non-conformance issues demonstrated the use of appropriate root cause determination tools. He is knowledgeable in process risk assessments and the designation of the applicable hazards to be controlled to mitigate product risk.

Nigel Smith - Biomedical Consultancy Ltd
Spencer is a dedicated, thorough and competent Process Engineer that I have worked with on a range of technically challenging and advanced processes whilst at Synthes Inc. He is an excellent team member who is diligent, knowledgeable and able to bring both creative and pragmatic solutions to bear on issues.

Doug Robertson
I worked with Spencer on a number of new product introductions and product line expansions. Spencer is a very detail oriented and thorough manufacturing engineer. During the course of those projects he both lead and participated as a team member in process risk assessments and process validations. He was effective in the identification of process requirements and material specifications that would need to be addressed to ensure product safety and effectiveness for new products and new manufacturing technologies. His work on the investigations of non-conformance issues demonstrated the use of appropriate root cause determination tools. He is knowledgeable in process risk assessments and the designation of the applicable hazards to be controlled to mitigate product risk.

Nigel Smith - Biomedical Consultancy Ltd
Spencer is a dedicated, thorough and competent Process Engineer that I have worked with on a range of technically challenging and advanced processes whilst at Synthes Inc. He is an excellent team member who is diligent, knowledgeable and able to bring both creative and pragmatic solutions to bear on issues.

Doug Robertson
I worked with Spencer on a number of new product introductions and product line expansions. Spencer is a very detail oriented and thorough manufacturing engineer. During the course of those projects he both lead and participated as a team member in process risk assessments and process validations. He was effective in the identification of process requirements and material specifications that would need to be addressed to ensure product safety and effectiveness for new products and new manufacturing technologies. His work on the investigations of non-conformance issues demonstrated the use of appropriate root cause determination tools. He is knowledgeable in process risk assessments and the designation of the applicable hazards to be controlled to mitigate product risk.

Nigel Smith - Biomedical Consultancy Ltd
Spencer is a dedicated, thorough and competent Process Engineer that I have worked with on a range of technically challenging and advanced processes whilst at Synthes Inc. He is an excellent team member who is diligent, knowledgeable and able to bring both creative and pragmatic solutions to bear on issues.

Experience
-
SSI Manufacturing Technologies
-
United States
-
Industrial Machinery Manufacturing
-
1 - 100 Employee
-
Quality Inspector
-
Nov 2021 - Present
-
-
-
Emerson Automation Solutions
-
Automation Machinery Manufacturing
-
700 & Above Employee
-
Manufacturing Engineer - Quality Supervisor
-
Apr 2021 - Oct 2021
Lead and train the team in lean manufacturing, assembly, and quality control with emphasis on manufacturing engineering. Provide preeminent support, leadership, and training to the machine shop, assembly, and inspection areas through process analysis, problem resolution, and continuous improvement while ensuring compliance to ISO 9001 Quality Management System (QMS). • Measure and minimize cost of poor quality through root cause identification and implementation of proper corrective and preventative actions and design for manufacturing. • Slashed calibration spending by reviewing and consolidating inventory of Measuring and Test Equipment (MTE) while demonstrating how to better utilize existing assets. • Implemented regular verification of key converters for both internal and external manufacturing and presented a business case for the idle converter cell equipment and experienced personnel.
-
-
-
Materion Corporation
-
United States
-
Manufacturing
-
700 & Above Employee
-
Process Engineer III
-
Jan 2020 - Sep 2020
Hands-on support of product and processes, troubleshooting, cost (yield and labor efficiency) and quality improvement, and cycle time reduction. Develop procedures for manufacturing processes and equipment and facilitate 8D failure analyses. Drive process capability and continuous improvement through change control and real time SPC . • Advocated employee safety by identifying and communicating potential risks and mitigation strategies. • Promoted the improvement of receiving inspection, documentation, and handling of customer owned backing plates to mitigate complaints and improve customer confidence. • Introduced technical drawing standards and implemented the quality system for their change control.
-
-
-
Lannett Company
-
United States
-
Pharmaceutical Manufacturing
-
200 - 300 Employee
-
Technical Services Scientist II & Senior Validation Engineer
-
Oct 2017 - Oct 2019
TECHNICAL SERVICES SCIENTIST II: Provided operations, regulatory affairs, and project management timely, qualitative, and science-based support of products (liquids, suspensions, lotions, and creams) manufacturing and contract manufacturing organizations (CMOs) in technology transfer, product/process development, submission, scaling, product/process improvement, and validation. Worked directly with product development to transfer and scale up processes for clinical studies, regulatory submissions, and new product launches. • Advocated employee safety by identifying and communicating potential risks and mitigation strategies. • Proactively identified and addressed issues and gaps while supplying technical process documentation to facilitate timely abbreviated new drug application submissions to the FDA. • Applied a fresh perspective to create clear and concise batch record templates to ensure quality system and regulatory compliance while promoting greater consistency within process documentation. • Provided product and process troubleshooting, technical expertise, and assistance with product transfers to contract manufacturing organization (CMO). SENIOR VALIDATION ENGINEER: Collaborated, planned, coordinated, implemented, executed, reviewed, and approved utility, equipment, and computer systems commissioning, installation, operational, and performance qualifications, process and cleaning validations and verifications, and technology transfers for the manufacture, filling, and packaging of bulk intermediates, active pharmaceutical ingredients (API), and finished dosage form (FDF) oral and topical solutions. • Challenged the status quo by regularly asking why to eliminate waste and improve efficiency and cost. • Identified training and compliance gaps while providing direction and instruction to contractors and reviewing and approving their implementation of a new process control network.
-
-
-
-
Manufacturing Engineer
-
Apr 2009 - May 2017
Supported production operations (turning, milling, drilling, EDM, finishing, etc.) in the areas of process development, tool design, CNC programming, equipment acquisition, and layout. • Teamed with drafting, document control, environmental health and safety, facilities, machine operators, maintenance, operations, planning, product development and management, production supervisors and operators, QA inspectors, quality engineers, regulatory, sourcing, and training to assure safety, quality, delivery, cost, and inventory (SQDCI) met the key performance indicators (KPI) and ensured compliance with all applicable regulations and voice of the customer (VOC). • Improved quality and compliance to specifications by negotiating document change orders (DCO) to revise product drawings and product quality plans (PQP) by clarifying and correcting critical to quality (CTQ) features and dimensioning and tolerancing. • Redesigned gauges and fixturing to simplify and standardize manufacturing and remove redundancies. • Acted as a liaison to vendors regarding contracted products, tools & fixtures, and their manufacture. • Doubled machining capacity by testing and validating additional production equipment. • Reduced waste and cost by making the same product out of less raw material. • Served as a technical reference and completed special projects.
-
-
-
Roche Diagnostics
-
United Kingdom
-
Hospitals and Health Care
-
200 - 300 Employee
-
Project Engineering Consultant
-
Jun 2007 - Dec 2008
Responsible for equipment qualification, production support, implementation of process improvements, and promotion of regulatory compliance within quality system. • Headed the specification, acquisition, installation, testing, and qualification of over 60 pieces of equipment. • Significantly reduced hazardous incidences by properly training personnel on equipment’s intended use. • Halved the time required to modify PM tasks by eliminating duplication and unnecessary redundancies. • Supported production by troubleshooting process/equipment issues to reduce downtime and back orders.
-
-
-
Zimmer
-
Austria
-
Retail Furniture and Home Furnishings
-
1 - 100 Employee
-
Process Validation Engineer & Process Engineer
-
Apr 2005 - Jun 2007
PROCESS VALIDATION ENGINEER: Tasked with a strategic initiative to validate processes in a consistent, clear, and concise manner and in compliance with FDA Title 21 CFR Parts 11 and 820 and ISO 13485. • Developed master validation program and plan. • Facilitated changing company culture while adopting current Good Manufacturing Practices (cGMP). PROCESS ENGINEER: Manufacturing project leader and core team member responsible for process development, validation, documentation, management, and support to ensure timely new product release. • Completed new product and line extension release and manufacturing transfer to production. • Removed redundant penetrant inspection by proving mass finishing does not mask surface indications. • Improved Safety Data Sheet (SDS) accessibility by initiating change to electronic filing by EHS department. • Reduced manual processing by machining parts closer to finished dimensions. • Tripled tool life resulting in a reduction of tool changes, scrap, and cost. • Cut mass finishing time in half by optimizing process variables.
-
-
Education
-
Brigham Young University
Bachelor of Science (BS), Manufacturing Engineering Technology
Community
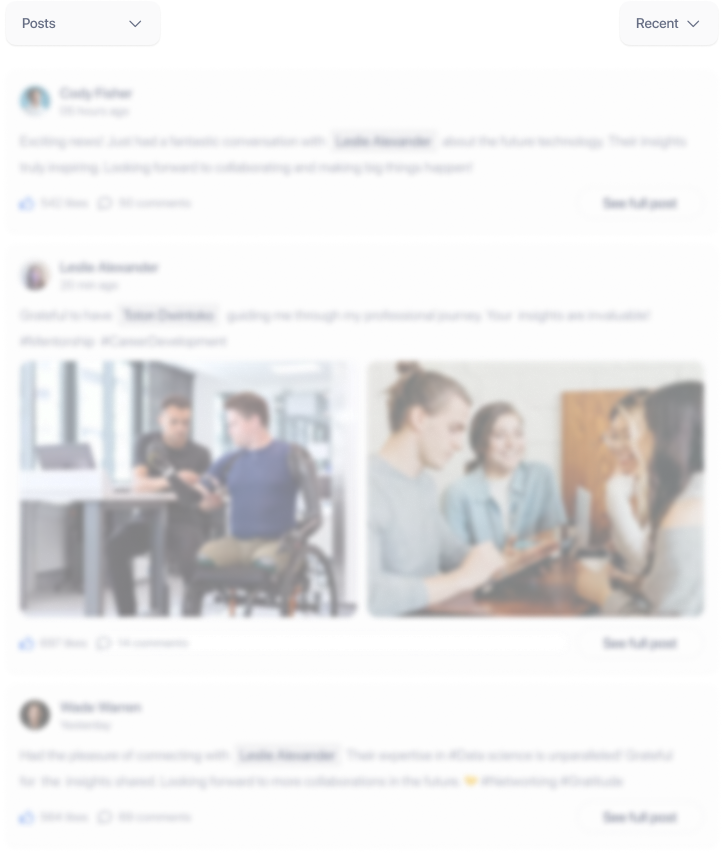