Sandi Muska
Quality Manager at Pure Power Technologies, Inc.- Claim this Profile
Click to upgrade to our gold package
for the full feature experience.
Topline Score
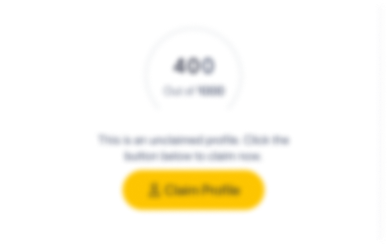
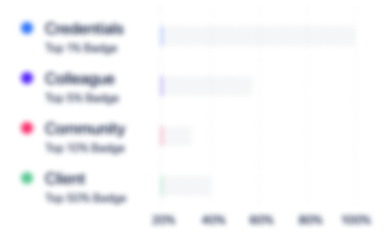
Bio


Experience
-
Pure Power Technologies, LLC A Stanadyne Company
-
United States
-
Motor Vehicle Manufacturing
-
100 - 200 Employee
-
Quality Manager
-
Apr 2022 - Present
-
-
-
Apex Tool Group, LLC
-
United States
-
Manufacturing
-
700 & Above Employee
-
Quality Manager
-
Jul 2020 - Apr 2021
•Rebuild QMS by conducting full system internal audit and gap analysis to the quality manual and ISO standard, modifying/create procedures to comply with QMS requirements, and by conducting training to complete the PDCA cycle of the rebuild. •Establish CAPA management system and lead focused issue management process for root cause/corrective action of both internal and external concerns to drive fast response of root cause counter measures. •Design and implement robust MRB process to manage control on nonconforming material for in-process materials, received goods, and customer warranty returns. •Conduct training on problem solving methodologies with cross functional work force to increase number of participants to improve quality level of root cause activities and overall time to close customer concerns. •Develop KPI data with measurable targets for quality related processes, determine top detractors affecting product/process quality, and establish a Quality Transformation plan for the organization. Show less
-
-
-
Nikola Corporation
-
United States
-
Motor Vehicle Manufacturing
-
700 & Above Employee
-
Corporate Quality Manager
-
Apr 2019 - Jul 2020
• Develop Integrated Management System (IMS) from the greenfield status for startup company to achieve Quality Management System certification to ISO9001:2015, Environmental Management System certification to ISO14001:2015, and Occupational Health & Safety System certification to ISO45001:2019. • Train process owners on roles, responsibilities, and requirements of the ISO standards related to their functions within the Integrated Management System. • Develop Key Product/Process Indicators to measure quality and manufacturing operating system effectiveness for immediate corrective action opportunities and process improvement planning. • Manage implementation of new technical standards and regulatory requirements – including integration into the Integrated Management System manual and processes. • Establish IMS internal audit process and train personnel as internal auditors to perform gap audits and ISO system audits using the process approach required by ISO 9001. • Launch Quality Management System modules as part of PLM system to support control of inputs/outputs for Corrective & Preventative Actions, Control of Nonconforming, Document & Record Control, Audit Management, Measurement Analysis, and Risk Management. • Develop APQP process for the company as a new OEM – company wide roll out with responsibilities and authorities. • Develop Advanced Quality team for new product / new process launches – support APQP process through validation and into manufacturing for continuous improvement. Show less
-
-
-
Mayco International
-
United States
-
Automotive
-
300 - 400 Employee
-
Corporate Quality Director
-
Jan 2012 - Sep 2018
Core Competencies: Management Systems: ISO 9001:2015, IATF 16949:2016, ISO 14001:2015, ISO 45001:2018, ISO 31000:2018, AS9100D:2016 QMS, EMS, OH&S TrainingRequirements Management: OEM, Statutory, and Regulatory Customer Quality Assurance Effective Problem Solving - CAPAInternal Audit Development & Execution – including Layered Process Audits & Product AuditsProduct & Process Design: AIAG Core Tools – APQP, PPAP, FMEA, Control Plan, MSANew Program Launch – Traditional, Greenfield Manufacturing Launches, and Constrained Supplier TakeoversProgram Management – Quality Attributes & RASIC DevelopmentDimensional Management - GD&T - SPCWorld Class Manufacturing – Quality Pillar / Quality Toolkit / PDCA Plan-Do-Check-ActRisk Management - Risk Analysis & Mitigation Lean Six Sigma Principles - DFSS and DMAIC Automotive Warranty Management Sup-Tier Supplier Management Processes - Supplier Development – Scorecard ManagementCost of Poor Quality, Cost Savings, Cost Avoidance CCC China Compulsory CertificationMMOG Materials Management OperationsSustainabilityIMDS / Conflict of MineralsKPI DevelopmentMRB / Return Material AuthorizationsDOEs & Test planningConflict Management / Cohesive Team Building / Individual and Team Confidence Building Visionary Leadership / Dynamic LeadershipColor Acuity – Craftsmanship High Dollar Debit Reconciliation – Exceeding 1 million USDManufacturing Processes:Injection moldingBlow moldingPaint – manual & automatedCarbon fiber lay upSub-assembliesOEM sequence assembly linesThermoformingAirbag scoringFoam in placePlatingHeat treatingAutomotive Interior / Exterior / Functional Commodities:Hard TrimSeatingInstrument PanelsDoor PanelsAir OutletsDecorative AppliquesAirbagsUnderbody / Underhood Functional Plastics Integrated Center StacksArmrest / Consoles Glove Box LightingFasciasCladdingsGround EffectsAerodynamic EffectsLight bars MirrorsGrillsAerospace Commodities:Tubing Show less
-
-
Quality Manager
-
Nov 2006 - Jan 2012
• Achieved implementation of Quality Management Systems for four North American plants by obtaining ISO/TS16949 & ISO14001 certifications with less than 3 minor nonconformances during any audit. • Manufacturing Operating System Quality Pillar Lead achieving 500-800K/yr cost savings/avoidance through planned kaizen activities.• Led cross-functional teams in root cause analysis - utilizing various Quality Toolkit Practices for corrective and preventative actions.• Mentored all departments in various methods and implementation practices for corrective/preventative action & continuous improvement activities. • Track/Analyze Internal & External Performance Indicators (KPIs) for quality improvement planning & verification of corrective / preventative actions taken.• Manage Internal Audit system in support of QMS requirements - including training for new auditors.• Conduct Management Reviews of KPIs and process outputs for process improvement planning.• Established APQP planning and tracking process - utilized program RASIC and timing charts to achieve 100% on-time PPAP approval from customers for new and refreshed programs.• Managed all aspects of APQP with program management, product engineering, manufacturing and quality for new and existing programs.• Analyzed part dimensional data on a monthly basis to ensure process and product capability continued to meet customer expectations.• Mentor Plant Quality Engineers and Quality Techs to ensure process & product verification was performed as required by the customer to ensure satisfactory output of products. Show less
-
-
-
Venture Industries
-
Grand Blanc, Michigan, United States
-
Advanced Quality Engineer Supervisor
-
Apr 1998 - Nov 2006
• Maintained Quality Management Systems as required by ISO/TS16949 and customer specific requirements as ISO/TS16949 internal auditor. • Conducted root cause analysis and preparation of corrective actions to OEM customers. • Track & analyze KPIs to develop corrective and preventative actions. • Implemented engineering specifications to ensure product and process conformance to requirements. • Analyzed product capability of functional part dimensional characteristics to ensure conformance to customer expectations. • Developed production part demonstration runs to achieve process/product approval by customers. • Quality lead for launch readiness: Gage design reviews, error & mistake proofing validation, secondary equipment qualifications in manufacturing setting, process DOEs, key characteristic analysis, development of APQP documents, and process sign off. • Mentor / train quality technicians on process verification of key characteristics. • Manage product & process audits to ensure 100% conformance to customer expectations prior to shipment of prototype and production parts. Show less
-
-
Education
-
Baker College Business and Corporate Services
Associate of Science - AS -
Spring Arbor University
Bachelors, Management of Organizational Development
Community
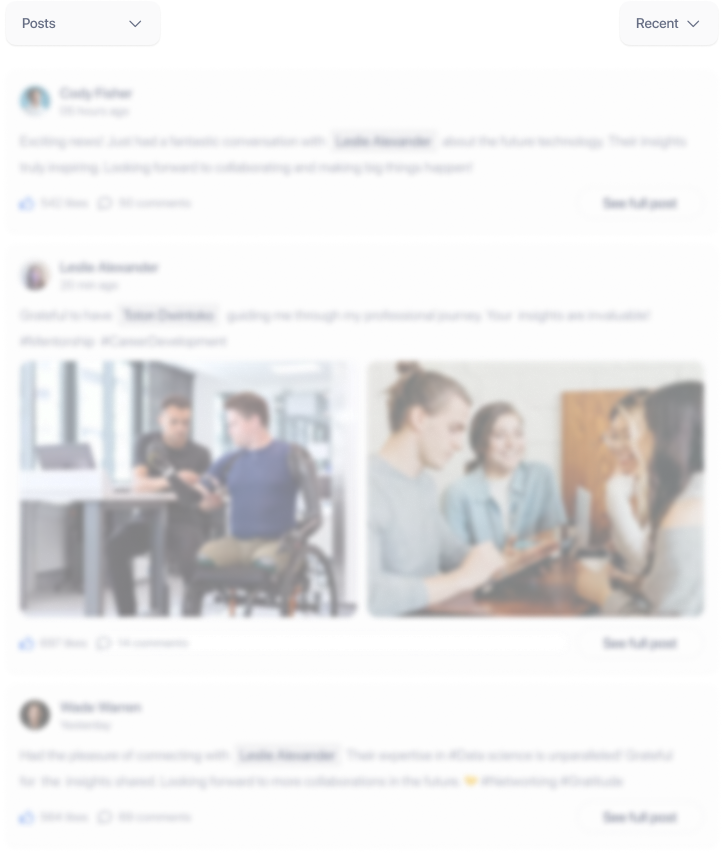