Simon Sharkey
Quality Coordinator at Ellex- Claim this Profile
Click to upgrade to our gold package
for the full feature experience.
Topline Score
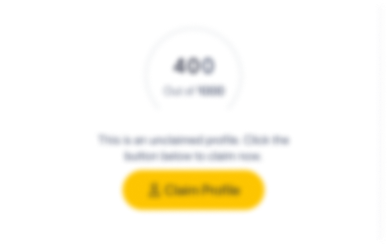
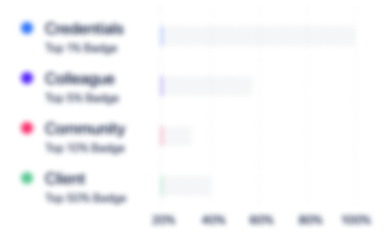
Bio


Experience
-
Ellex
-
Australia
-
Medical Equipment Manufacturing
-
1 - 100 Employee
-
Quality Coordinator
-
Jan 2009 - Present
•Over-see Product final quality inspection processes •Provide regular reports, feedback, analysis and quality data •Ensure all administration activities are effectively managed and performed •Ensure inspection staff are achieving objectives, meeting performance goals, are trained effectively, and are being managed according to company requirements •Development of departmental policies, processes and procedures to improve quality, efficiency and cost •Recommend changes to product or process that will improve design and manufacturing process reliability, process efficiency, or cost improvement •Ensure maintenance and calibration of inspection equipment •Provide feedback to vendors on quality issues and in conjunction with other departments, work with vendors to improve their quality, performance and processes •Coordinate inspection activities with other teams •Assist in training of company personnel in use of products, quality assurance and inspection activities and any other areas as required •Participates in design review process as representative of Quality department •Perform validation of new and changed designs to ensure they meet requirements •Member of ECB to ensure quality and inspection related issues are being addressed and to provide a quality perspective for proposed changes •Review of ECR contents for completeness and accuracy. •Management of CAR process, including investigations, recommendations, problem solving and documentation •Root cause analysis and implementation of corrective and preventative actions •Continuous improvement of QMS and product quality. •Ensure internal audit program is implemented and maintained to schedule and to include the QMS, production processes and product audits • Active participation in company wide process improvement and general adherence to defined processes. •Direct supervision, direction and management of inspection department personnel. •Acting Quality Manager in case of absence of VP Quality Show less
-
-
-
-
Quality Coordinator
-
2009 - Present
-
-
-
Futuris Automotive
-
United States
-
Motor Vehicle Manufacturing
-
100 - 200 Employee
-
Quality Technician
-
Dec 2003 - Nov 2006
Assist and support production line operators and engineers with productivity improvements on manufacturing current and new Product lines; Participate in the preparation and maintenance of quality documentation such as PCP (Process Control Plans), SOP (Standard Operating Procedures), PFMEA (Process Failure Mode Effects Analysis), GI (Gauge Instructions), SPL (Single Point Lessons), PPAP (Production Part Approval Process), G8D (Global 8 Discipline, corrective action process) and Data collection; Assist with trials and samples relating to new processes, products and problem solving activities, in particular performing capability studies using Minitab; Responsible for tooling and gauge calibration; Conduct manufacturing process audits (MPA’s) to TS16949 / QS9000 standards; Support and liaise with external suppliers in relation to quality development; Implement and communicate breakpoint notices, notifying customers (Holden, Ford, Mitsubishi) of change/modification on parts or processes that apply; Interpret design drawings and instigate required customer and internal deviation notices in the event of departure from the norm in part assembly (but still within functional tolerances); Product testing and reporting to senior management and engineers. Show less
-
-
Education
-
University of South Australia
Bachelor of Visual Communication -
Gleeson College
Community
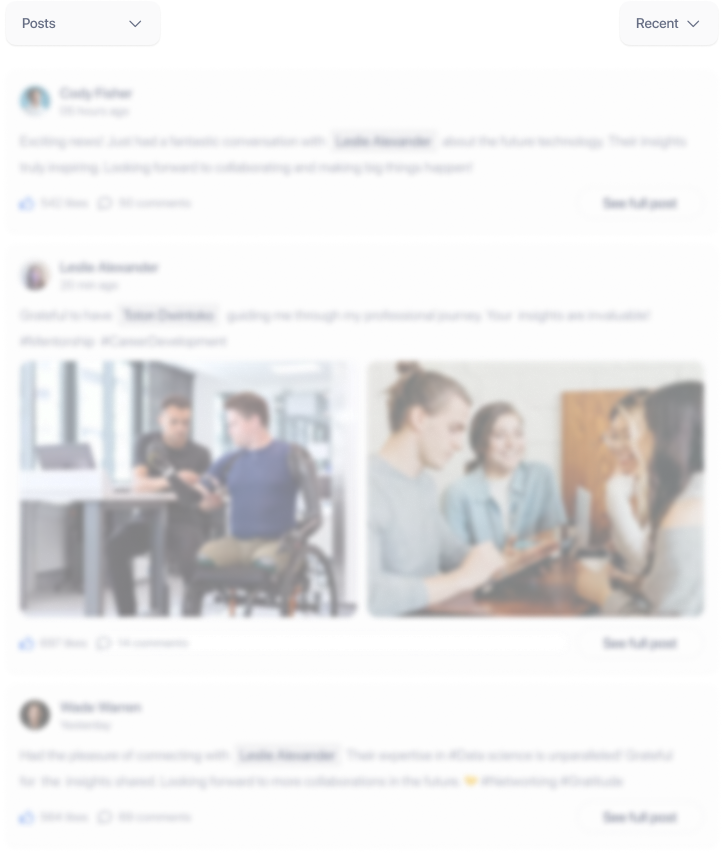