Simon Parsons
Senior Principal Process Safety Consultant at Advisian- Claim this Profile
Click to upgrade to our gold package
for the full feature experience.
Topline Score
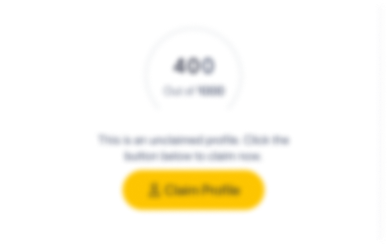
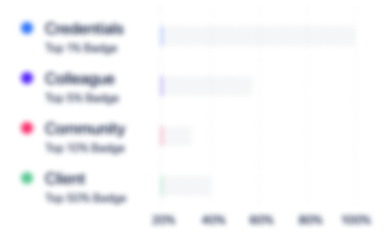
Bio


Experience
-
Advisian
-
Australia
-
Business Consulting and Services
-
700 & Above Employee
-
Senior Principal Process Safety Consultant
-
Sep 2022 - Present
-
-
-
Worley
-
Australia
-
Professional Services
-
700 & Above Employee
-
Principal Process & Process Safety Consultant
-
May 2015 - Jan 2022
Facilitation and management of Qualitative, Quantitative Risk Assessments, Safety and Loss Management studies. Process Safety Reviews, Bow Tie, HAZOP (using PHA Works), HAZID, LOPA/SIL, ALARP, SIMOPS, MOPO, Alarm Management, Value Engineering/Improvement, Lessons Learnt, Project Risk Reviews, etc. • Principal Technical Auditor for an independent Tier 2 oil company. Dozens of Audits (over a three year period) • Functional Safety Audit (4 months duration) of the SIS system of an Aluminium Refinery in Saudi Arabia against the Functional Safety requirements of IEC 61511. • Site and office based; Pre-Start-up Safety Review (PSSR) of a mixed hydrocarbon tank farm and road loading facility, onsite in mainland China. • Responsible for co-ordinating the Hydrocarbons business stream for Advisian in Malaysia. • Development of conceptual business opportunities. • Determination of H2S management requirements for a CPP in Malaysian waters. • Greenhouse Gas Emissions evaluations for wellhead platforms a Greenfield CPP. • Technical review of potential consequences and risk assessment of a high pressure (dense phase) CO2 system for the Chevron Gorgon LNG Plant. • Process Technical Authority. • Provide in-house training for HAZOP facilitators. • Personnel Mentor and Mentor for the RICE University Project Management on-line training course. Process Engineering Head of Department & Project Engineering Manager (Ranhill WorleyParsons) Responsible for the technical and departmental management of 60 Process Engineering personnel in various work locations around Malaysia which are part of a total company workforce of nearly 500 personnel. • Process Design of onshore and offshore, greenfield and brownfield facilities. • Flow Assurance, • Dynamic Analysis, • Operating and Start-up procedures. • Facilitated Process Safety Design Reviews (PSDR’s) Project Engineering Manager for the Qatar Petroleum NFA Platform Detailed Design (960 MMscfd high H2S greenfield wellhead platform). Show less
-
-
-
Chevron Australia Holdings Pty. Ltd.
-
Perth, Western Australia, Australia
-
Upstream Technical Advisor to the Commissioning & Start-Up Team (Gorgon Project)
-
Apr 2014 - Apr 2015
Provider of expert process and process safety advice to the CSU (Commissioning and Start-up) personnel and the Upstream Commissioning Manager. Reviewer of CPT’s (commissioning test plans), ISUP’s (Initial Start-up Procedures) and inlet facilities plant design. Attended many of the Project’s revalidation HAZOP’s and various HAZID’s. As part of a personal initiative I authored a weekly Process Safety newsletter for the CSU team. Attended various Chevron and JV Partner PEER reviews concerning plant design and commissioning readiness. The Gorgon facility is built on Barrow Island (a Class A nature reserve) 60 km off the coast of Western Australia. It includes a three train 15.6 Million tonne per annum LNG plant with LNG and condensate storage, 300 teraJoules per day domestic gas plant, two subsea gathering systems (Gorgon and Jansz-lo fields) both with MEG injection, 4.3 Million tonnes per year CO2 injection facilities. Show less
-
-
-
Origin Energy
-
Australia
-
Utilities
-
700 & Above Employee
-
Client Process Safety Engineer (Pre-Start-Up Team Leader) Australia Pacific LNG Project (APLNG)
-
Jul 2012 - May 2013
Client Process Safety Engineer (Pre-Start-Up Team Leader) and commissioning gatekeeper for process safety, reporting to Commissioning Manager (deputised for Commissioning Manager during his absence) – activities included: chairmanship of Commissioning Readiness Risk Reviews and Pre-Start-up Safety Reviews for all project facilities, review of all Project deliverables to ensure compliance with Process Safety Requirements and support in the development of bow-ties as part of safety case. Process Safety Champion for the Commissioning Team. Project included: 34 HV electrical driven centrifugal compressors, 15 TEG drying and regeneration packages 1200 wellheads and wellhead separators, gathering piping and HV electrical network, 14 air compressors and drier packages, 14 nitrogen generation packages, 2 water treatment plants and associated large bore high pressure pipelines. Multiple control rooms and integrated operating centres. Total project value $22 Billion AUD. Show less
-
-
-
Ranhill WorleyParsons
-
Kuala Lumpur, Federal Territory of Kuala Lumpur, Malaysia
-
Principal Process Engineer
-
Apr 2011 - Jul 2012
Principal Engineer responsible for managing Process Design and Process Safety in Design, quality assurance of process deliverables, personnel management/leadership, assisting head of department with team management and the development of engineering procedures, philosophy documents, “OneWay” (process safety) moments and job proposals. PTTEPI Block M3 Pre-Conceptual Study/supporting Field Development Plan. Process Study Leader for the kick-off of an early field development study for PTTEPI in Myanmar. Study includes 6 wellhead platforms, CPP, FSO, export gas and condensate pipelines, condensate storage on-shore, LPG plant on-shore and Power Station. JDA Block B-17 Platform – Field Development Project – MDPP Production Debottlenecking Study. Project Process Lead, responsible for platform troubleshooting and development of conceptual debottlenecking options for the CPOC MDPP Platform in the Joint Development Area between offshore Malaysia and Thailand. The facilities include 5 wellhead platforms, a CPP that is connected to an export pipeline, flare platform and Living Quarter Platform with Floating Storage and Offloading of condensates. Feed gas is high in CO2 which is removed using membrane technology. Platform maximum design export flowrate before debottlenecking is 372 MMscfd of gas and 18,307 bpd of condensates. Debottlenecking options included multiple platform throughputs and feed compositions. Laila Field Development – conceptual/FEED design. Project Process Leader, responsible for managing all Process deliverables for a free-flowing gas and condensate wellhead platform and tie-back design for Sarawak Shell Berhad. Barzan Offshore Project – Facilitation of Process Design Review. Facilitation of a Detailed Design review of the Process Documentation for the RasGas Barzan Offshore Project. Show less
-
-
-
BIEN DONG PETROLEUM OPERATING COMPANY (PetroVietnam)
-
Kuala Lumpur, Federal Territory of Kuala Lumpur, Malaysia
-
Client Process Engineering Lead
-
May 2010 - Apr 2011
Client Process Engineering Lead, responsible for the successful completion of all Process Engineering and Process Safety activities for the detailed design phase of the greenfield Bien Dong 1 ($1.5 Billion USD) for the East Sea of Vietnam. Reporting to the Project Engineering Manager. Responsibilities included: • Client approval of all process documentation. Including: P&ID’s, PFD’s, Heat and Material Balances, Flare & Blowdown Study, line list, vessel calculations, pump calculations, SAFE Charts, Process & fire and gas cause & effect charts, rotating equipment and package calculations, firewater dynamic surge analysis, pipeline chemical injection and flow assurance analysis. • Supporting the Technical Safety Engineer with the review of project related technical safety documentation. • Client attendee at HAZOP and LOPA review meetings and responsible for coordination of action closure. • Supplied data for specialist RAM, RBI and FIV (Flow Induced Vibration) assessments. • Answering Process Engineering Technical Queries, and generating Process Design Instructions to the contractor. • Issued weekly process safety news letter to project team. Project scope included: Two wellhead platforms, Processing and Quarters Platform (design capacity 360MMscfd gas and 20 Kbpd condensate), two export pipelines and interface with FSO. Show less
-
-
-
CHEVRON THAILAND EXPLORATION & PRODUCTION LTD.
-
Singapore, Singapore
-
Client Process Engineering Lead (Platong Gas II Project)
-
Jul 2008 - Apr 2010
Client Process Engineering Lead, responsible for the successful delivery of all Process Engineering and Process Safety activities for the detailed design phase of the greenfield platform and brownfield tie-ins of the Platong Gas II Project ($1Billion USD) for the Gulf of Thailand. Reporting to the Project Engineering Coordinator. Responsibilities included: • Client approval of all process documentation. Including P&ID’s, PFD’s, Heat and Material Balances, Flare & Blowdown Study, SAFE Charts, Cause and Effects, line list, vessel calculations, hydraulic calculations, technical review of firewater and compressor surge dynamic analysis and vendor package sizing calculations. • Client attendee at all HAZOP and LOPA review meetings and responsible accepting action closure on behalf of the Client organisation. • Assistance with Technical Safety – QRA and ship collision, Fire and Explosion Analysis, Firewater deluge modelling, Fire and gas detector mapping and cause and effect charts, Emergency Escape Route Analysis, ALARP study, Venting and flare radiation analysis, etc. • Responding to Process Engineering Technical Queries and generating Process Technical Instructions to the contractor. • Assisted integrity team with RBI assessment. • Process Safety Champion – sharing weekly process safety bulletin. • Package Manager for the Condensate Stabiliser Package, Potable Water Maker Packages, Survival Craft, Electric Heaters, Fuel & Seal Gas Packages, heat exchangers, firefighting and safety equipment. Also responsible for the mentoring of junior Thai Chemical Engineers. Project scope included: Bridge linked Living Quarters platform (200 personnel), Gas Processing Platform producing 420MMscfd dried and dewpointed gas plus 22 Kbpd of condensate. Show less
-
-
-
BP AZEBAIJAN (Azerbaijan International Operating Company)
-
Baku, Baki, Azerbaijan
-
Client Senior Process (Offshore Modifications Team)
-
Apr 2004 - Jul 2008
Client Engineer responsible for Process and Project Engineering of capital modifications for the Chirag-1 platform (165Mbd oil and 170MMscfd associated gas) and deputy to the Strategic Performance Unit Process Technical Authority. Responsible for Conceptual Evaluation, Field Development options, FEED, Detailed Design, offshore Implementation. Projects executed: • Project engineering of topsides modifications associated with a new gas export system to an adjacent platform ($5.5M). Also managed the design and testing of a specific Low Dose Hydrate Inhibitor (LDHI) chemical, injection facility and pipeline hydrate formation monitoring algorithm. • Project Engineering of extension of water injection turbine exhausts in order to remove their interaction with the helideck. • Project Management of the production and subsequent updates of the Chirag –1 Platform QRA and a detailed Explosion Risk Assessment for the main and cellar deck areas. • Project Management for the Chirag-1 2006 Shutdown (10 day outage) and 2007 development works (circa $70M). Included: o Total replacement and upgrade of fire and gas system o Total replacement and upgrade of the glycol dehydration system o Flare and gas system debottlenecking and installation of a new flare tip o Deck drainage and firefighting enhancements o Upgrade of the accommodation and life safety facilities o General infrastructure enhancements o Process safety integrity reviews, and platform LOPA o Replacement of the Water Injection Booster Pump system o Replacement of one of the platform cranes • General process support, troubleshooting, optimisation and plant modifications for the platform • Company representative at dozens of HAZOPs, Safety Reviews, Constructability Reviews & Go/No-Go meetings for brownfield modifications. • Supported Azeri Field Production shutdown team (14 day outage) as process engineer. Also responsible for mentoring junior Azerbaijan national Chemical Engineers. Show less
-
-
-
Atkins
-
United Kingdom
-
Engineering Services
-
700 & Above Employee
-
Principal Process/Technical Safety Engineer
-
Jan 2001 - Mar 2004
Responsible for Technical Leadership and Project Management of studies covering a variety of process and Technical Safety issues within the Oil & Gas sector including: • Chairmanship of process business risk review & HAZOP study for the BP CATS Train 1 Conditioning & Separation Plant • Chairmanship of two HAZOP studies for the Baku-Tbilisi-Ceyhan pipeline (Turkish section). • HAZOP Chairmanship of six (6) HAZOP’s and one (1) safety engineering review for various clients. • Conceptual design of a green field gas reception facility at Centrica, Easington (approx. capital value £60M) – now constructed – Langeled Project. • Authorship of Control of Major Accident Hazard (COMAH) report for BP Dalmeny Crude Oil Tankfarm & Marine Vapour Recovery Plant. • Chairmanship of a capacity and operability review for the BP CATS Gas Terminal. • Integrity Level (IEC 61508/61511) assessment for a gasoline blending system. • Business and safety risk review for an onshore oil & gas field. • Conceptual design of a green field gas reception facility at BP Bacton Gas Terminal & BP Dimlington Gas Terminal. (Approx. capital value £40M). • Technical Expert within incident review team following a loss of containment at a Gas Separation Plant. • Front End Design of capacity and availability improvements to the 8 Ground Flares at BP Grangemouth, Kinneil Gas Separation Plant. (Approx. Capital value £3M) • Conceptual & Front End Design for the BP Dalmeny Crude Oil Tankfarm (eight crude tanks, 79m diameter containing 70,000 tonnes each). (Approx. Capital value £4.5M) Show less
-
-
-
ELECTROWATT CONSULTANTS LIMITED
-
United Kingdom
-
Mechanical Or Industrial Engineering
-
1 - 100 Employee
-
Conceptual Design Engineer
-
Aug 2000 - Dec 2000
Full time seconded to Petroleum Development Oman (PDO) as Bahja Production Area, Conceptual Design/ Process Engineer, responsible for Operational Process Support and Business development of the oil filed area and gathering stations. Responsibilities involved regular liaison with Operations Personnel, Petroleum Engineers, Geologists and Geophysicists in order to optimise field development plans. Reported to Senior Conceptual Process Engineer. Full time seconded to Petroleum Development Oman (PDO) as Bahja Production Area, Conceptual Design/ Process Engineer, responsible for Operational Process Support and Business development of the oil filed area and gathering stations. Responsibilities involved regular liaison with Operations Personnel, Petroleum Engineers, Geologists and Geophysicists in order to optimise field development plans. Reported to Senior Conceptual Process Engineer.
-
-
-
WS Atkins Oil & Gas
-
Glasgow, Scotland, United Kingdom
-
Principal Process/Technical Safety Engineer
-
Feb 1998 - Aug 2000
Responsible for Technical Leadership and Project Management of studies covering a variety of process and Technical Safety issues within the Oil & Gas sector including: • HAZOP Chairman of twelve (12) HAZOP’s and seven (7) safety Engineering Reviews for various clients. • Production of Refinery Emergency Operating Procedures for a small bitumen refinery in Scotland. • Review of mechanisms causing sand deposition and de-sanding facilities for a number of offshore oil/gas separators in Saudi Arabia. • Operation & Maintenance Audit of Castrol Technology Centre Pangbourne. • Production of COMAH (Control of Major Accident Hazards) installation reports for a number of refinery process units. • QRA, for the onshore section of the BP Exploration, Forties Pipeline System, including fault tree analysis of the booster station instrument trip systems. • A review of foaming mechanisms within an Oil/Gas separator at BP Exploration, Kinneil Gas Separation Plant, offering proposed modifications to plant and operating procedures in order to optimise foaming potential. • A Vulnerability/Contingency Review for the BP Exploration, Forties Pipeline System from landfall through pipeline transfer, separation plant, tankage and ship loading processes. • Two technical assessments of the design of the relief valve and flare systems; One for BP, Sullom Voe Terminal & the other for BP, Wytch Farm Gathering Station, offering guidance concerning application of national and company standards. • Member of BP PHSER (Project Health Safety & Environmental Reviews) team at BP Exploration, Wytch Farm Gathering Station & for BP Vietnam. • Project Management of a team of engineers carrying out an environmental audit of a UK onshore oil production facility. • Production of a Safety Climate Survey for a number of offshore drilling platforms in the Far East. Show less
-
-
-
EWBANK INTERNATIONAL CONSULTANTS
-
Muscat, Masqaţ, Oman
-
Process Department Manager (Conceptual/Field Development Engineer)
-
Aug 1996 - Feb 1998
Process Department Manager - (leading 10 Process Engineers). Latterly, fulltime seconded to PDO (Petroleum Development Oman) as Rima Production Area Conceptual Design/ Field Development Engineer, responsible for Operational Process Support and Business Development of 1/6th of PDO’s production (90,000 bbls/day crude oil production from 200 wells, two production stations and a booster station). Constant liaison with Operations Personnel, Petroleum Engineers, Geologists and Geophysicists in order to optimise field development plans. Reported directly to Asset Team Leader and was responsible for developing projects totalling US$15M per annum. Show less
-
-
-
BP GRANGEMOUTH CHEMICAL & REFINERY COMPLEX, SCOTLAND.
-
Grangemouth, Scotland, United Kingdom
-
Senior Process Engineer
-
Oct 1987 - Aug 1996
Client Engineer, responsible for: • Developing business options and presenting justification for capital projects within the BP Exploration assets at Kinneil Gas Separation Plant (1,150 Mbd). • Project Implementation of a number of corrective engineering jobs related to the newly commissioned Train III Gas/Oil Separation Plant (550 Mbd) at BP, Kinneil Gas Separation Plant. • Selection and leadership of a multi-disciplined team of Engineers (6 Process Engineers, plus others), who were charged with the implementation of the “Pressure Systems & Transportable Gas Containers Regulations 1989” at BP Grangemouth Refinery. • Production of a detailed statement of requirements for a relief system study, encompassing approximately 50% of the Refinery (300 relief valves and several kilometres of flare headers) - Total capital value £10M. • leadership of a team of Engineers and operations personnel responsible for the safe and timely commissioning of the KG Ethylene Cracker Offsites. Senior Process Engineer (BP Chemicals – Offsite & Utilities Area) • Operations Process Support to the Offsites & Utilities Operations Personnel. • Client Senior Process Engineer reporting to the Engineering Manager on all Process and Design Safety matters. Responsible for coordinating the process design of the rehabilitated Hydrocracker Unit. Show less
-
-
-
MATTHEW HALL NORCAIN LTD.
-
Southampton, England, United Kingdom
-
Process Design Engineer
-
Sep 1985 - Sep 1987
Member of the “Front End” & “Detailed” design team that was responsible for the development of an innovative design for a new coffee manufacturing facility (£5M). Member of the “Front End” & “Detailed” design team that was responsible for the development of an innovative design for a new coffee manufacturing facility (£5M).
-
-
-
Ralph M Parsons Co. Ltd.
-
London, England, United Kingdom
-
Process Systems Engineer
-
Oct 1982 - Sep 1985
Member of the Process Design Department, responsible for hydraulic design, equipment and instrumentation sizing and selection of a NGL plant. Part of home office design team and latterly seconded to site as the process department representative on-site. Member of the Process Design Department, responsible for hydraulic design, equipment and instrumentation sizing and selection of a NGL plant. Part of home office design team and latterly seconded to site as the process department representative on-site.
-
-
Education
-
University of Bath
Bachelor of Science - BS, Chemical Engineering
Community
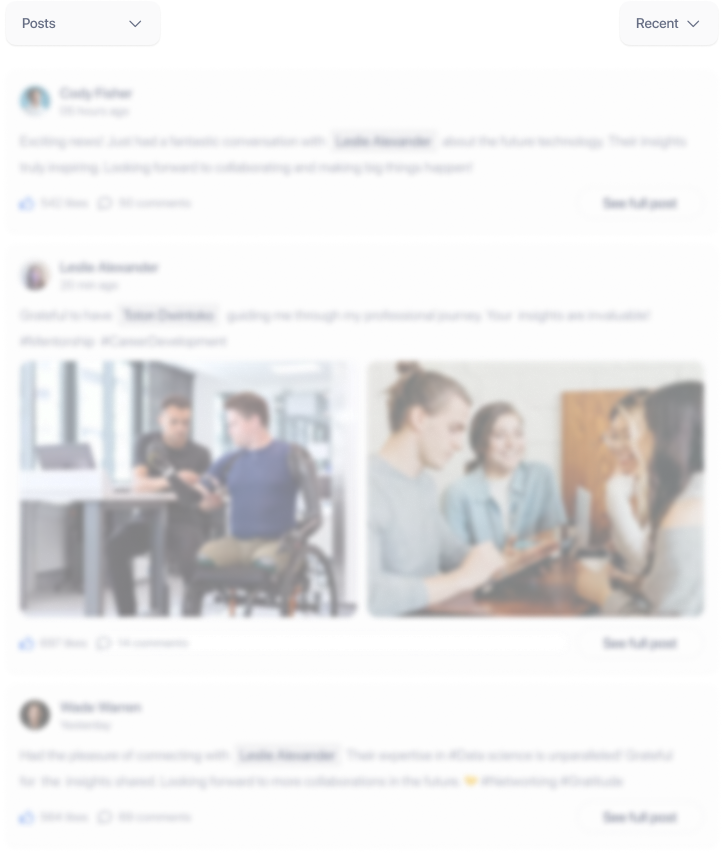