Simeon Sagabaen
Quality Assurance Specialist at Calyxo, Inc.- Claim this Profile
Click to upgrade to our gold package
for the full feature experience.
Topline Score
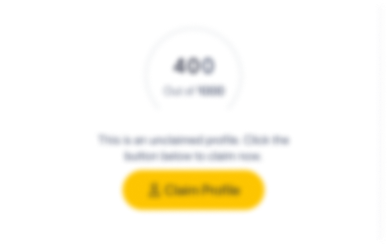
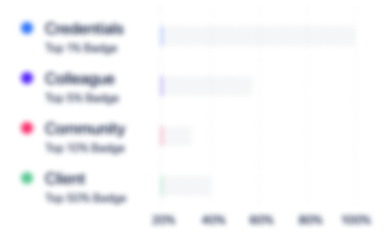
Bio

Donna Samson
Simeon is a very detail oriented employee. He always complete every job on time and accurately. He is very knowledgeable and hardworking. Simeon has outstanding work ethics and can be relied upon at all times.

Alice Nguyen
Simeon is a responsible, hard worker. He also is a helpful team player who would do anything to meet the group goals. It was a pleasure working with him.

Donna Samson
Simeon is a very detail oriented employee. He always complete every job on time and accurately. He is very knowledgeable and hardworking. Simeon has outstanding work ethics and can be relied upon at all times.

Alice Nguyen
Simeon is a responsible, hard worker. He also is a helpful team player who would do anything to meet the group goals. It was a pleasure working with him.

Donna Samson
Simeon is a very detail oriented employee. He always complete every job on time and accurately. He is very knowledgeable and hardworking. Simeon has outstanding work ethics and can be relied upon at all times.

Alice Nguyen
Simeon is a responsible, hard worker. He also is a helpful team player who would do anything to meet the group goals. It was a pleasure working with him.

Donna Samson
Simeon is a very detail oriented employee. He always complete every job on time and accurately. He is very knowledgeable and hardworking. Simeon has outstanding work ethics and can be relied upon at all times.

Alice Nguyen
Simeon is a responsible, hard worker. He also is a helpful team player who would do anything to meet the group goals. It was a pleasure working with him.

Experience
-
Calyxo, Inc.
-
United States
-
Medical Equipment Manufacturing
-
1 - 100 Employee
-
Quality Assurance Specialist
-
Aug 2022 - Present
-
-
-
Stellartech Research Corporation
-
United States
-
Medical Equipment Manufacturing
-
1 - 100 Employee
-
Quality Control Supervisor
-
Sep 2021 - Aug 2022
• Understands customer needs and requirements to develop effective quality control processes. • Reviews and approves Device Master Record documentation for device design changes as appropriate (impact on past, current and future product(s)). • Reviews and approves Device History Records for finished device and perform QA release of finished devices. • Performs internal quality audits and external quality audits of contractors and suppliers where/when appropriate. • Oversees all product development procedures to identify deviations from quality standards. • Participate as quality representative for MRB and review of NCMRs. • Manage calibration program for manufacturing and development test equipment. • Manage maintenance program for manufacturing assembly and test fixtures. • Perform statistical analysis/report on service and complaint data for Management • Review, Customer Business Review, External/Internal Audits, etc., • Manage corrective actions generated from customer and field returns. • Reviews and approves Service and Complaint Records as appropriate. • Supervise QC technicians and provide guidance and feedback. • Ensure adherence to health and safety guidelines as well as legal obligations. Show less
-
-
-
Accellix
-
United States
-
Biotechnology
-
1 - 100 Employee
-
Quality Assurance Specialist
-
Apr 2021 - Sep 2021
• Perform inspections according to internal policies, procedures, specification(s), drawing(s), and work instructions, ECO’s, Deviations, and other applicable controlled Quality System documents. • Receive fixture parts and raw materials such as solutions, chemicals, reagents from receiving. • Perform functional testing. • Initiate and investigate non-conformances. • Performed 2nd signature review of QC Inspectors recorded data ensuring GMP and GDP have observed as well as the correct sampling plan per AQL/ANSI/ASQZ1.4, specification, and WI is used. • Review of completed batch record and LHRs from all departments. • Performed inspections of product labeling and packaging. • Perform and monitor training for all Accellix employees • Assist on equipment control program ensuring critical equipment are calibrated/maintained as scheduled. • Interpret and comply with quality assurance standards • Make sure that quality assurance standards are adequate • Elaborate the procedures of sampling and guidelines for collection and reporting quality data • Oversee the implementation and ensure efficiency of inspection and quality systems • Plan, perform and oversee inspection and testing of products to ensure the quality deliverable • Document quality assurance activities, such as internal audits • Assist on analyze customer complaints and other non-compliance issues. • Inspect data to detect areas for improvement Show less
-
-
-
Zipline Medical, now part of Stryker
-
Campbell, California
-
Quality Assurance Specialist
-
Jul 2017 - Apr 2021
• Perform all Document Control duties for managing all aspects of company controlled documents and training records. This includes processing document change orders, and maintenance of all company documents and records. • Interface with Contract Manufacturers and other suppliers for document changes, requests for Certifications, device history records, and other quality documentation • Prepare and maintain Employee Training Sets and training curriculum, including notification of training requirements and monitoring of training status • Perform incoming inspection of components used in manufacturing and inspection of finished device for final acceptance and generate nonconforming material reports, as needed • Coordinate calibration activities for measuring and test equipment with the calibration supplier, including review of calibration results and initiating and tracking of out of tolerance equipment • Assist with trend analysis, filing, audits, and perform administrative tasks as needed. Show less
-
-
-
Creganna Medical
-
Ireland
-
Medical Equipment Manufacturing
-
700 & Above Employee
-
QC Supervisor
-
Dec 2014 - Jun 2017
Manage the Inspection Functions, consisting of Receiving, In-process and Final Inspections, including Dock to Stock Strategy.Work closely with Operations/Supply Chain for scheduling and prioritization of inspection.People management aspects of the Inspection team, including ensuring adequate coverage and an effective cross-training program.Lead and manage the Material Review Board to ensure products are appropriately dispositioned within a timely manner, while ensuring appropriate corrective and preventive actions and trending are initiated while meeting all regulatory requirements.Responsible for the Non-Conforming Product process, including trending and analyzing data to determine improvement opportunities.Work with New Product Development teams to determine appropriate testing and inspection of raw materials, in-process and final release of product based on Critical To Quality specifications and FMEAs.Assist in issues related to Metrology, Inspection, Testing, and Product Stability.Work with suppliers of both raw materials and components, to improve product quality and/or resolve quality issues. Develop quarterly supplier acceptance trending reports and supplier report card system.Utilize data to identify opportunities to improve productivity with regard to inspection through-put and/or sampling plans.Qualification and Validation: knowledge to develop plans to evaluate quality and process impacting activities to ensure compliance of FDA’s 21 CFR Part 820 and ISO13485 through equipment qualification and process validation or ISO14644 for cleanroom design, operation and performance monitoring. Show less
-
-
QA Specialist II Product Release
-
Mar 2014 - Jun 2017
Support quality systems, including complaints, returned material, failure investigations, corrective and preventive action (CAPA), rework, deviations and non-conforming materials. Review current documents, correct typos and formatting errors. Create Engineering Change Orders and route for approval. Interface with Manufacturing and Operations to support product release to specifications. Review and disposition LHRs for incoming components, in-process assemblies and finished goods; verify product inventory. Assist in the management of supplier evaluations and records; track supplier audits and quality improvements. Support quality inspectors by assisting in hands on inspection Identify and initiate quality improvements in systems and procedures. Assist in the management of equipment and tooling calibration; interface with calibration provider; maintain associated records. Show less
-
-
-
Miramar Labs
-
United States
-
Medical Equipment Manufacturing
-
1 - 100 Employee
-
Senior QA/QC Specialist
-
Jul 2011 - Apr 2014
Lead QA/QC in inspection and release of incoming raw materials, in-process/subassembly and finished devices. Initiate, investigate and review non-conforming reports. Execute MRB lot dispositions. Coordinate calibration and preventive maintenance program. Lead QA/QC in inspection and release of incoming raw materials, in-process/subassembly and finished devices. Initiate, investigate and review non-conforming reports. Execute MRB lot dispositions. Coordinate calibration and preventive maintenance program.
-
-
-
AngioScore
-
United States
-
Medical Equipment Manufacturing
-
1 - 100 Employee
-
Senior QA Specialist
-
Jul 2008 - Jul 2012
-
-
-
Novo Nordisk
-
Denmark
-
Pharmaceutical Manufacturing
-
700 & Above Employee
-
QA Specialist II
-
Apr 2003 - Mar 2008
-
-
-
-
QA Technician
-
Oct 1999 - Aug 2001
-
-
-
Cardiogenesis Corporation
-
United States
-
Medical Equipment Manufacturing
-
1 - 100 Employee
-
Operator
-
Oct 1997 - Sep 1999
-
-
Education
-
Saint Louis College - Philippines
Associate of Arts and Sciences - AAS, AB Economics
Community
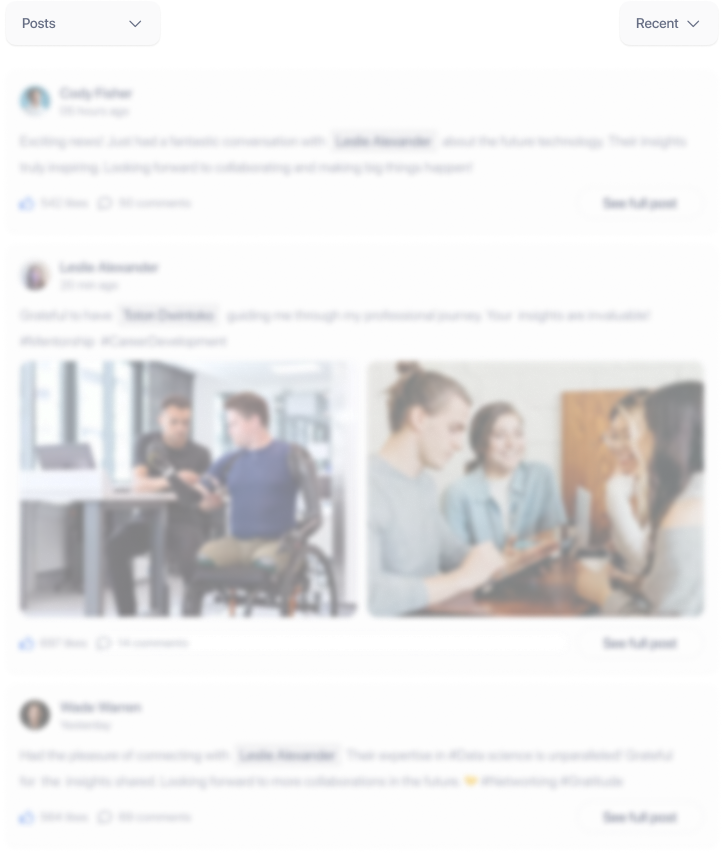