
Sherwin Yarisantos
Shift Manager at Alaska Milk Corporation- Claim this Profile
Click to upgrade to our gold package
for the full feature experience.
-
Arabic -
-
English -
-
Tagalog -
Topline Score
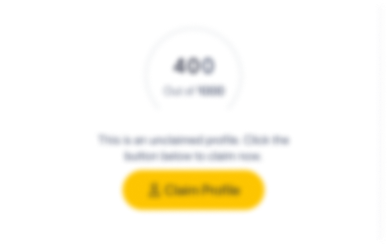
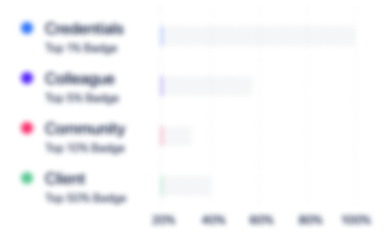
Bio


Credentials
-
Basic Occupation Safety and Health
Philippine Department of Labor and EmploymentJun, 2021- Oct, 2024 -
Basic Occupation Safety and Health
CONSAFEMay, 2018- Oct, 2024 -
DMAIC white belter certified
Nestle Philippines Inc.Dec, 2013- Oct, 2024
Experience
-
Alaska Milk Corporation
-
Food and Beverage Manufacturing
-
300 - 400 Employee
-
Shift Manager
-
Jul 2022 - Present
-
-
-
Eau de Coco Inc.
-
Philippines
-
Food and Beverage Services
-
1 - 100 Employee
-
Production Supervisor / Safety Officer
-
Feb 2021 - Jul 2022
-
-
-
-
Service Engineer
-
Jul 2020 - Sep 2021
-
-
-
-
Senior Shift In Charge (Senior Supervisor)
-
Jan 2020 - Jul 2020
I was responsible on supervision of production and maintenance of tetra production Ensure compliance to production plan as per PPIC scheduled. Ensure compliance to Safety and GMP of plant. Taking lead in coordinating and implementing / monitoring all relevant task and activities for projects involving capability build up for the company’s manufacturing and technical facilities, ensuring that this is optimally done in cost-effective and timely manner. Supporting initiatives on continuous improvement.As Senior Shift In Charge(Senior Supervisor) here in Tolman Manufacturing Inc., I was ask to handle both maintenance and operation of Tetra Production Line. I have to review process flow as well as the HACCP plan to ensure that the plant was compliant. I also have to plan production as per schedule of PPIC in aligned with preventive maintenance activity to ensure a smooth flow of production runs. I also introduced spare parts monitoring files/program that can easily track and monitor all the available parts of the machine and can request immediately if needed or if in critical stocks/inventory. I also have to ensure that our operator was highly motivated to get their 100% engagement.Currently, I was working with Del Monte Philippines (our customer) for their DMAIC Project which aim to reduce line losses on our manufacturing plant.
-
-
-
Franklin Bakery Inc
-
United States
-
Food and Beverage Manufacturing
-
1 - 100 Employee
-
Tetra Pak Supervisor
-
Nov 2018 - Jan 2020
I was responsible on planning and manage operation and maintenance activities of the aseptic lines to meet scheduled target. As supervisor, I have to monitor my staff on duty and ensure that they comply to standards such as GMP, ISO, Sanitations, Housekeeping and Safety Procedures. I also have to review maintenance checklist as well as the implementation of a weekly care and daily care on Alfa Laval pasteurizer and Sterilizer, Alfa Laval Oil Separator, Aseptic Bulk Filler, AL CIP, AL Safe (30000 Liters of Aseptic Tank), Tetra Pak Filling Machines (A3 CompactFlex) and Distribution Equipment (Helix, LC30 and Cap30).Being a Tetra Pak Supervisor on Franklin Baker was a very challenging task since Tetra Pak Technology was newly introduced to the company. Operators and Engineering Department was not fully knowledgeable on the machine operations and principle. As I join the company, I stablished and aligned a lot of documents together with my co-supervisor in the line such as production logsheets, CIP and SIP logsheets, packaging integrity monitoring logsheets, HACCP Certificate, and different preventive maintenance checklist. I even engage my self on creating our HACCP on Aseptic Processing Line. Since our Engineering Department has limited knowledge on the machine, during machine breakdown, I was more involve on trouble shooting to lessen the machine downtime. We arrange different trainings from Tetra Pak such as Machine Operation and Maintenance on A3 Compact Flex, Cap30 and Helix. We also arrange PLMS training and Machine Electrical wirings and controls. In this way, we can fast track the learnings of our Engineering team as well as our Operators.I also sent to our toll packing company at Canlubang Laguna to assist our San Pablo Plant on their first commercial run on one of our customer of Coconut water 1 Liters since our machine here at Davao Del Sur was only 330ml.
-
-
-
-
Technical Service Executive
-
Jan 2018 - Sep 2018
I was responsible in all issues regarding Markem - Imaje printers such as Laser printer, Thermal printer, CIJ Printer, TIJ printer and Print and Apply printer. I was also responsible on preparing all the safety documents and permits needed prior to our job requirements on our client’s location.As Technical Service Executive / Safety Officer, I conduct plant visit before conduction a machine demo for our client. I also done an machine installations and conduct training for our client’s personnel. I also conduct preventive maintenance and servicing when we have a job order from our client. I also conduct a phone support when our client has an urgent issue if we cannot be able to send a technician immediately.In my current position, I was able deal with different persons with different personalities. I was also able to see different machines with different technologies from our different client such as Nestle Philippines Inc., Coca Cola Philippines Inc., Procter and Gamble Philippines, Universal Robina Corporation, Phelp Dodge Philippines, Wyeth Nutrition Philippines, Epson Philippines, Japan Tobacco Inc., Philip Morris Fortune Tobacco Corporation Inc and many other big and small scale companies.
-
-
-
-
Packaging Technician
-
Nov 2013 - Nov 2017
I was responsible for all packaging materials in the plant (receiving, analysis, trial, commissioning and rejection). I also do supplier communication and supplier plant visit.First their hire me as Process Operator and once they see my potential, they hire me as Packaging Quality Technician. I used to deal with the suppliers especially if we have material issues in the plant. My daily routine was to go in the line for checking all the material issues then attend the meeting together supervisor and manager of our production and maintenance team to discuss all the issues that they faced from the previews day. I also suggest some improvements on the line that save a lot of money and increase the line efficiency. I also did a material improvement that also makes savings for the company. If there was new material or new machine, I was there to see how does the material going to run in the machine and suggest some inputs for the success of the trials.As Packaging Technician, I should know how machine works that’s why I frequently stay on the machine to know also how to operate and troubleshoot the different machine like Tetra Pak, Ermi, Arcil, and Serac filling machine and even the date printing machine ( Markem - Imaje and Video Jet). By having training on those machines, I can make my job easy because I can see where the problem came from (if there’s a problem occur) during the trials or even the normal production.
-
-
-
-
Operator I (Operator/Technician)
-
Sep 2009 - Nov 2013
In my 4 year on working with Nestle Philippines, I was task to handle different projects and also chose to be a part of a commissioning team. My first big project was to handle the compound die that cut and form the foil of Bear Brand and Chamito probiotic drink. It was a very old die that’s why it causes us a lot of problem if we don’t know how to handle it. First I was pulled out from the production just to focus on this project for 2 months. I disassemble the die, take measurement of all parts, and make a list for all the parts, since it doesn’t have a manual. I make 2D and 3D drawings (AutoCAD) for all the part and sectioned drawing of die assembly. After that project, I finished a manual for that compound die and my manager asked me to conduct training for all operators and maintenance who handle that machine and they give me recognition for that. They give also some projects on cost saving for reducing waste materials on the machine that we commissioned which is FFS (Formed Fill Seal) Machine. I have done a lot of innovation and improvement on the line that wins a “BEST INNOVATION” award. One those innovation was converting the manual adjustment of air conveyor to automatic adjustment during change over. Before the modification I made, it took 30minutes to do the changeover on the air conveyor but after the modification, it took 1 second to switch the changeover. I was also awarded as having a “MOST NUMBER OF INNOVATION” for submitting more than 100 innovations. During my stay in Nestle, they also asked me to crate the CDM schedule (Consequence Driven Maintenance) also known as their preventive maintenance schedule of several machines (FOGG Filler 1 & 2, Benison Wrapping Machine, Fuji Wrapping Machine, REMI Filler and FFS Machine. I was also certified as a White Belter for DMAIC (problem solving tools) for leading a two waste reduction projects on FFS Machine.
-
-
-
-
Maintenance Engineer
-
Jun 2007 - Sep 2009
Conduct PM and trouble shoot assembly die, press stamping die and molding die.Install electrical wiring.Conduct PM on HVAC and molding machine.Operate chiller and compressor.Operate milling, lathe, band saw, surface grinder, profile grinder, optical profile grinder, MIG and TIG welding. Conduct PM and trouble shoot assembly die, press stamping die and molding die.Install electrical wiring.Conduct PM on HVAC and molding machine.Operate chiller and compressor.Operate milling, lathe, band saw, surface grinder, profile grinder, optical profile grinder, MIG and TIG welding.
-
-
Education
-
MFI Technological Institute
Mechanical, Tool and Die Technology/Technician
Community
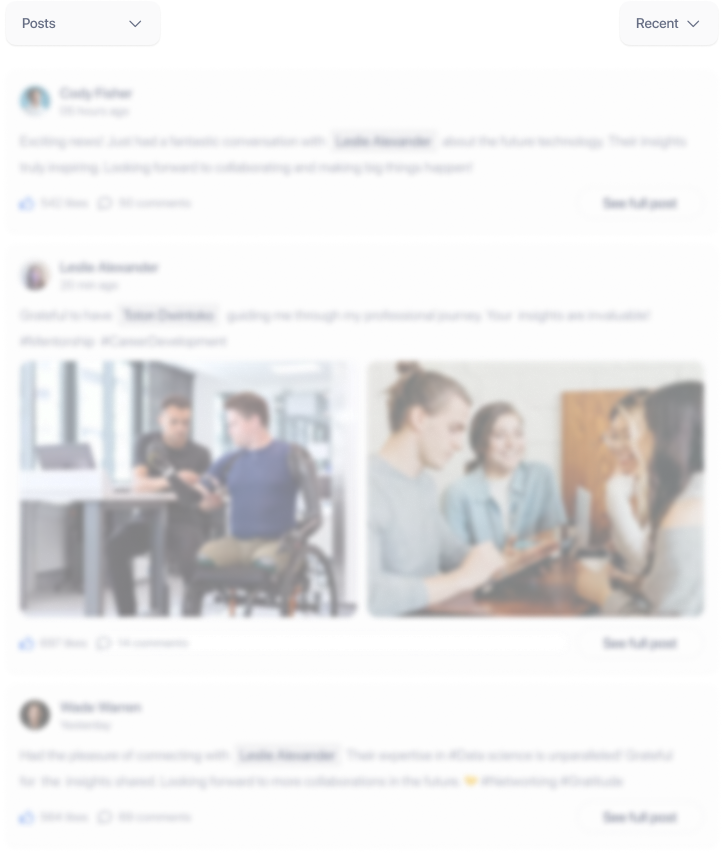